SIMULATION AND AUTOMATION OF COPPER-NICKEL SULFIDE RAW MATERIAL SMELTING PROCESS
SIMULATION AND AUTOMATION OF COPPER-NICKEL SULFIDE RAW MATERIAL SMELTING PROCESS
Abstract
The work is dedicated to improving the technical and economic performance of the smelting process of copper-nickel sulfide raw materials in the Vanyukov furnace. The melting temperature providing the best course of physical and chemical reactions of the process is chosen as the target parameter. A model of the Vanyukov process based on heat balance equations is developed. The heat input and output items are described. Adequacy of the mathematical model is evaluated by the value of deviation of the calculated melting temperature from the nominal value. The options of melting temperature control on the basis of PI and PID regulators are examined. Quality indicators of the system are assessed. SCADA-system that collects information and controls the regime of melting of copper-nickel materials in Vanyukov furnace has been developed.
1. Введение
Востребованность высококачественных цветных металлов растет с каждым годом. В связи с этим требования к производству цветных металлов в современных условиях ужесточаются с точки зрения культуры труда, экономических и экологических аспектов [1], [2].
Печь Ванюкова – особая технологическая установка отечественного производства, которая является важнейшим звеном получения меди. Характерной особенностью установки служит ее высокая удельная производительность и непрерывная работа. При этом должен поддерживаться заданный тепловой режим при непрерывном контроле объемов загруженной шихты и подаваемого дутья. Даже кратковременные неисправности печи могут привести к повторному окислению расплава, увеличению его вязкости и выбросу из печи [3], [4], [5].
Целью работы является стабилизация температуры плавки на требуемом уровне, при котором обеспечивается наилучшее протекание физико-химических реакций процесса.
2. Моделирование процесса плавки
Технологический расчет плавки медно-никелевого сырья в печи Ванюкова включает в себя расчет материального и теплового баланса [1], [2], [6]. В соответствии с законом сохранения энергии основное уравнение теплового баланса имеет вид:
Статьями прихода являются: теплота вносимая шихтой с флюсом, теплота химических реакций, теплота технического кислорода и воздуха, статьями расхода являются: количество теплоты уносимой со шлаком, штейном, отходящими газами, тепло, затрачиваемое на испарение влаги и прочие потери [1], [5]. Таким образом, уравнение теплового баланса принимает вид:
В упрощенной форме уравнение можно записать в виде статического теплового баланса, учитывая, что М – масса шлако-штейновой ванны, с – теплоемкость штейна при температуре 1250°С, Т – контролируемая температура:
Формулы для расчетов статей баланса представлены в таблице 1.
Таблица 1 - Формулы для расчета статей баланса
Наименование величины | Формулы |
М – масса шлако-штейновой ваннны | М=148 т |
с – теплопроводность штейна | с=64,86 кДж/т*К |
Статьи прихода тепла | |
|
|
|
|
| q=11879,79 кДж/кг*К усредненный тепловой эффект реакций n=0,97 степень усвоения кислородом дутья Gdyt =37150 м3/ч расход дутья O2vd =57,59*0,01 содержание кислорода в дутье по объему |
|
|
Статьи расхода тепла | |
| i, j – этантальпии шлака и штейна соответственно i = 960 кДж/кг, j = 1460 кДж/кг
|
| |
|
Т – контролируемая температура, К |
|
|
По указанным формулам в Simulink Matlab была собрана балансовая модель процесса Ванюкова. Целевым параметром выбрана температура плавки, так как именно при поддержании температуры в заданных пределах обеспечивается требуемое технологией протекание физико-химических процессов в печи.
Для оценки адекватности модели был проведен численный эксперимент: входные потоки задавались с учетом рандомизации в пределах регламентных значений, при этом оценивалось значение температуры плавки. Рассчитанное по модели значение температуры сравнивалось с номинальным. Гистограмма отклонений расчетного значения температуры от номинального приведена на рисунке 1 (высота столбца – количество ситуаций, всего проведено 100 экспериментов).
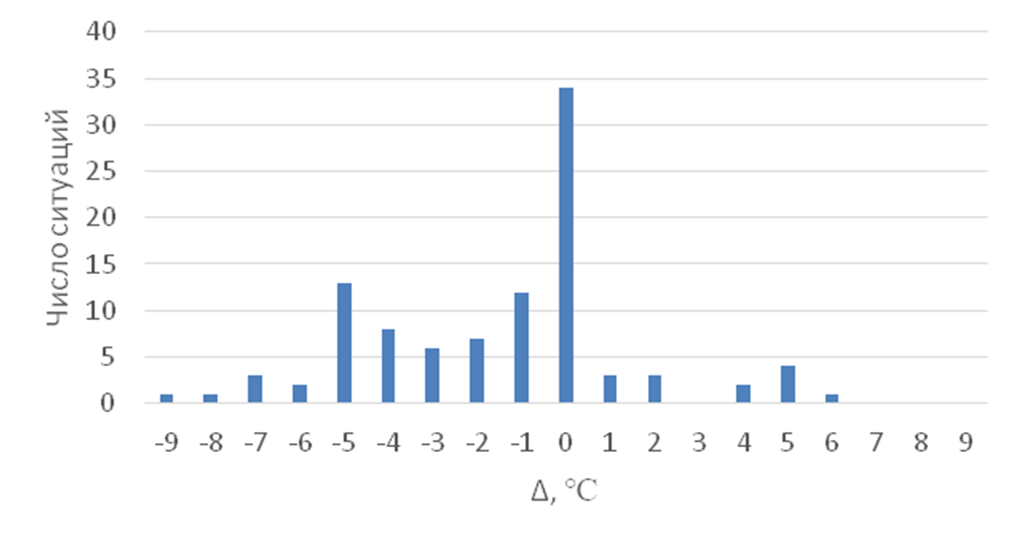
Рисунок 1 - Проверка адекватности модели
Согласно рисунку 1, ошибка моделирования не превосходит ±10°С при номинальном значении температуры 1250°С. Таким образом, модель признается адекватной.
3. Управление температурой плавки
Для управления температурой плавки медно-никелевого сырья в печи Ванюкова были рассмотрены ПИ и ПИД регуляторы.
Графики переходных процессов при различных возмущениях, поданных на систему, показаны на рисунке 2.
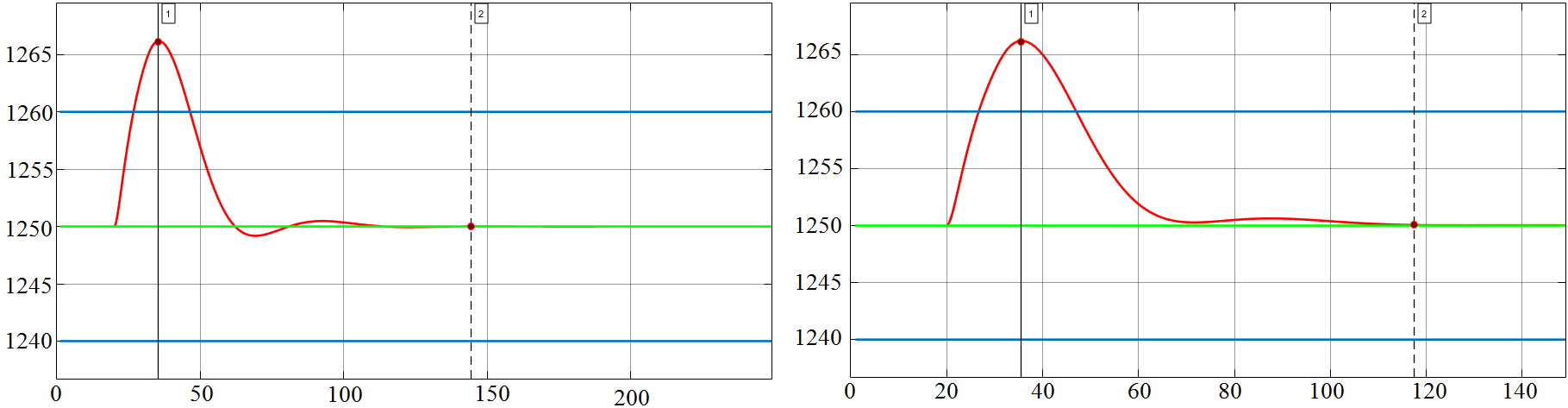
Рисунок 2 - Реакция системы на возмущение по управляющему параметру
Примечание: зеленый – номинальное значение температуры; синий – диапазон регламентных значений температуры; красный – реакция системы на возмущающие воздействия; слева – работа ПИ-регулятора; справа – работа ПИД-регулятора
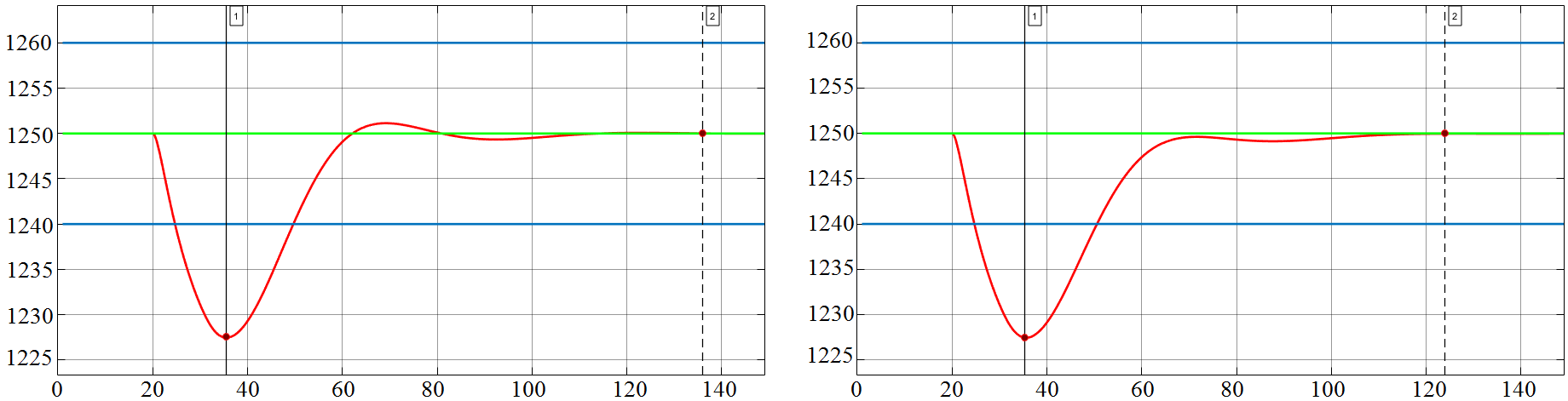
Рисунок 3 - Реакция системы на возмущение по возмущающему параметру
Примечание: зеленый – номинальное значение температуры; синий – диапазон регламентных значений температуры; красный – реакция системы на возмущающие воздействия; слева – работа ПИ-регулятора; справа – работа ПИД-регулятора
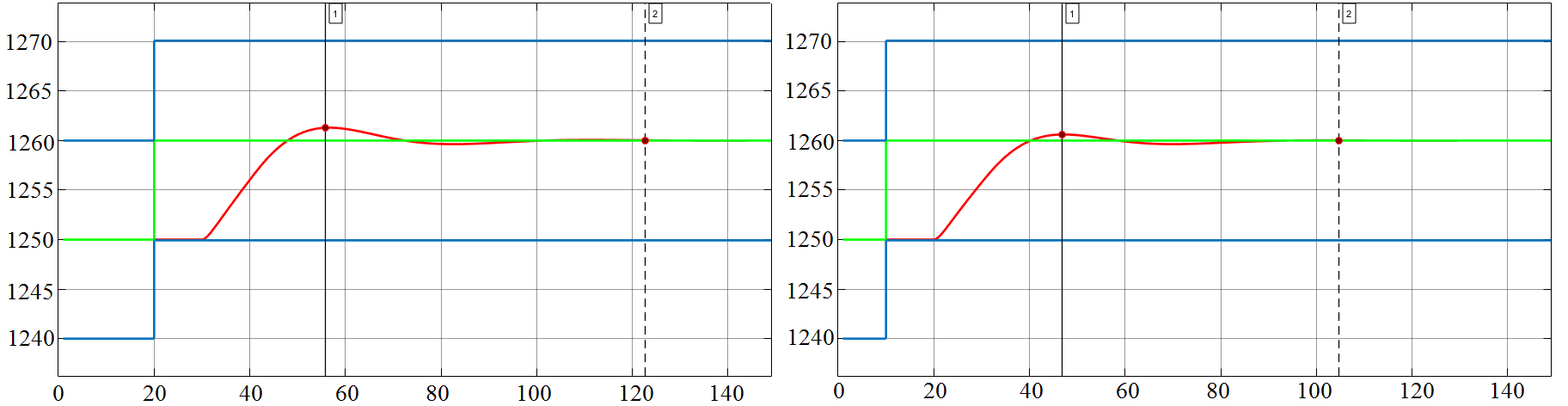
Рисунок 4 - Реакция системы на изменение уставки
Примечание: зеленый – номинальное значение температуры; синий – диапазон регламентных значений температуры; красный – реакция системы на возмущающие воздействия; слева – работа ПИ-регулятора; справа – работа ПИД-регулятора
По полученным графикам (рис. 2) были определены показатели качества системы управления объектом. Сравнение показателей работы системы с ПИ и ПИД-регулятором приведено в таблице 2.
Таблица 2 - Сравнение показателей переходного процесса системы с ПИ и ПИД-регулятором
Характеристика | ПИ-регулятор | ПИД-регулятор |
Возмущение по управляющему параметру | ||
Время выхода системы на установившее значение (время регулирования) | 124 | 97 |
Статическая ошибка | 0 | 0 |
Перерегулирование, % | 1,28 | 1,28 |
Возмущение по возмущающему параметру | ||
Время выхода системы на установившее значение (время регулирования) | 115 | 103 |
Статическая ошибка | 0 | 0 |
Перерегулирование, % | 1,76 | 1,84 |
Изменение уставки | ||
Время выхода системы на установившее значение (время регулирования) | 103 | 84 |
Статическая ошибка | 0 | 0 |
Перерегулирование, % | 0,07 | 0,07 |
Основной показатель, характеризующий работу системы – это время регулирования, то есть, то время, за которое система, вышедшая из равновесия, вернется в устойчивое состояние. Меньшее время регулирования показывает ПИД-регулятор, поэтому для дальнейшей работы выбран он.
4. Настройка клиент-серверной архитектуры
На производстве для измерения параметров используется большое количество датчиков, генерирующих различные сигналы. Все сигналы поступают на один или несколько контроллеров, которые в свою очередь передают данные в SCADA-систему [7], [8].
Основными функциями SCADA-системы является сбор информации и управление технологическим процессом путем выработки управленческих сигналов. Также SCADA-системы предоставляют графическое описание хода технологического процесса в форме, удобной для оператора (операторский экран), регистрируют события, которые произошли за все время работы, архивируют их и формируют отчеты на основе архивных данных [9], [10].
Для связи датчиков со SCADA-системой используются различные технологии. Так, наиболее часто используется OPC-технология, которая определяет единый интерфейс передачи данных между объектами. Данная технология использует клиент-серверную архитектуру, то есть в сети есть OPC-клиент, который передает данные, и OPC-сервер, обрабатывающий полученные данные и хранящий их. Главным преимуществом такой архитектуры является то, что при замене сервера, клиент продолжает работать в штатном режиме и не требует перенастройки либо замены, так как интерфейс передачи данных между ними подходит для большинства производителей аппаратуры.
Операторский экран или мнемосхема – наглядное изображение технологической цепочки агрегатов, несущее в себе достаточную информацию для наблюдения за процессом. На экране могут быть изображены агрегаты, сигналы с датчиков, графики, журнал тревог и так далее.
В статье рассматривается разработка экрана в SCADA-пакете IFIX. Был нарисован экран оператора, настроена база данных (созданы локальные теги (переменные) и связанных с имеющимися сигналами с датчиков). IFIX имеет множество встроенных библиотек с готовыми фигурами, есть анимированные изображения. Анимация привязывается к тегам, которые были ранее созданы в базе данных.
Вид разработанного экрана оператора представлен на рисунке 3.
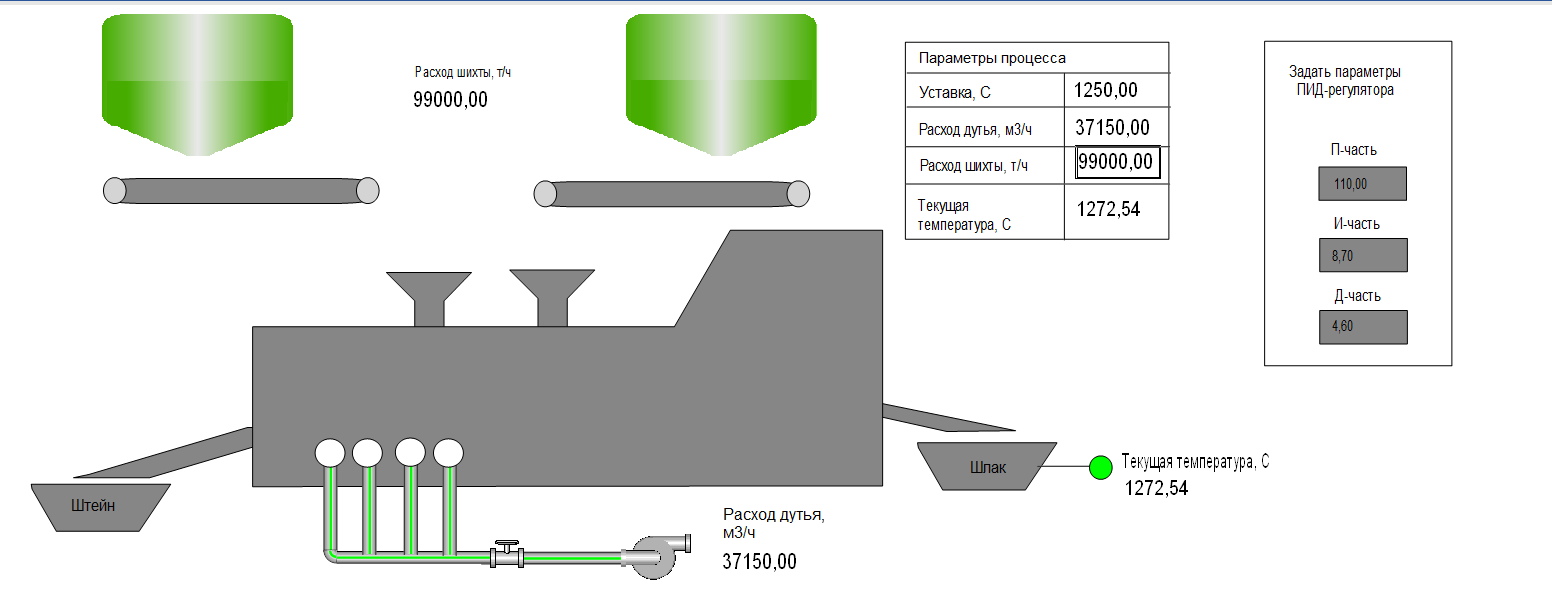
Рисунок 5 - Экран оператора
На рисунке 3 представлены конвейеры и бункеры, которые отвечают за подачу шихтового материала, трубы подачи кислородно-воздушной смеси, контролируемые параметры. Также настроена анимация – при изменении параметра мигает объект, который за него «отвечает». Например, при увеличении количества подачи шихты в печь, бункеры меняют цвет с серого на зеленый, а при увеличении подачи дутья – трубы.
5. Заключение
Таким образом, была разработана математическая модель процесса плавки медно-никелевого сырья в печи Ванюкова. На основе уравнений теплового баланса найдена зависимость температуры плавки от параметров процесса. Показана адекватность математической модели.
Проанализирована работа ПИ и ПИД регуляторов для управления температурой плавки. Показано, что работа ПИД регулятора позволяет более качественно управлять температурой плавки.
Разработана SCADA-система, осуществляющая сбор информации и управление режимом плавки медно-никелевых материалов в печи Ванюкова.