Economic substantiation of the technology of production of fodders and feed supplements with the use of freezing of grain raw materials and products of its processing
Economic substantiation of the technology of production of fodders and feed supplements with the use of freezing of grain raw materials and products of its processing
Abstract
The existence of the Russian Federation under the sanctions restrictions sets the task of reducing production costs in all sectors of the economy and industry, which can be implemented through the introduction of innovative technologies and non-standard methods of solving emerging problems.
It should be noted that this also applies to the sphere of fodder production, as the cheapening of feed production technology will make them more affordable for livestock and poultry farming, and consequently increase the production of meat and dairy products. As a result of literature-patent review and carrying out of own researches it has been established by us that one of perspective directions of perfection of technologies of fodder production is use for grinding of grain raw materials preliminary frozen to negative temperatures. In this state, the moisture contained in the pores of the grain turns into ice, expanding and destroying the structure of the material, which contributes to facilitating the grinding process.
For this objective the researches on influence of negative temperatures on qualitative and quantitative indicators of carrying out of process of grinding of grain and products of its processing, in particular various kinds of hull and for manufacture of mixed fodders, additives to them in loose and as extrudates are carried out for a long time at the faculty of MACFI.
The study showed that blast freezing of grain raw materials and its products, in particular sunflower husk and buckwheat, allows to reduce energy consumption for its grinding and increase the nutritional properties of the resulting feed. Thus, on the basis of the obtained research results we proposed a technological line of production of fodder and feed additives with the use of frozen grain raw materials and products of its processing, its economic substantiation was carried out.
1. Введение
На основе результатов исследований была разработана технология изготовления экструдированных комбикормов с добавками, включающая заморозку перед измельчением исходного сырья (рисунок 1). Общая схема технологии включает следующие этапы: в бункере 1 загружаются лузга (подсолнечника, гречихи) и мучные отруби, далее сырье подается на установку шоковой заморозки 4, работающую в различных режимах для лузги и мучного сырья. Лузга направляется на молотковую дробилку 5, а мучные отруби на роторную дробилку 6. Воздействие охлаждения замороженным воздухом на оболочку и мелкую часть зерна делает их хрупкими, что позволяет эффективно измельчать оболочку до потери её режущих свойств в молотковой дробилке 5, а также эффективно измельчать мелкую часть зерна до размера частиц менее 100 микрометров в роторной дробилке 6.
Это позволяет безопасно вводить оболочку в корм животных, не беспокоясь о её острой кромке, а также добавлять измельченное мучное сырье (отруби) размером менее 100 микрометров в экструдируемые комбикорма, что улучшает усвояемость , .
2. Методы и принципы исследования
Исходные сыпучие компоненты, хранящиеся в бункерах 1, роторными дозаторами, которые установлены в нижней части бункеров подаются в строго определенной порции на установку шоковой заморозки 4.
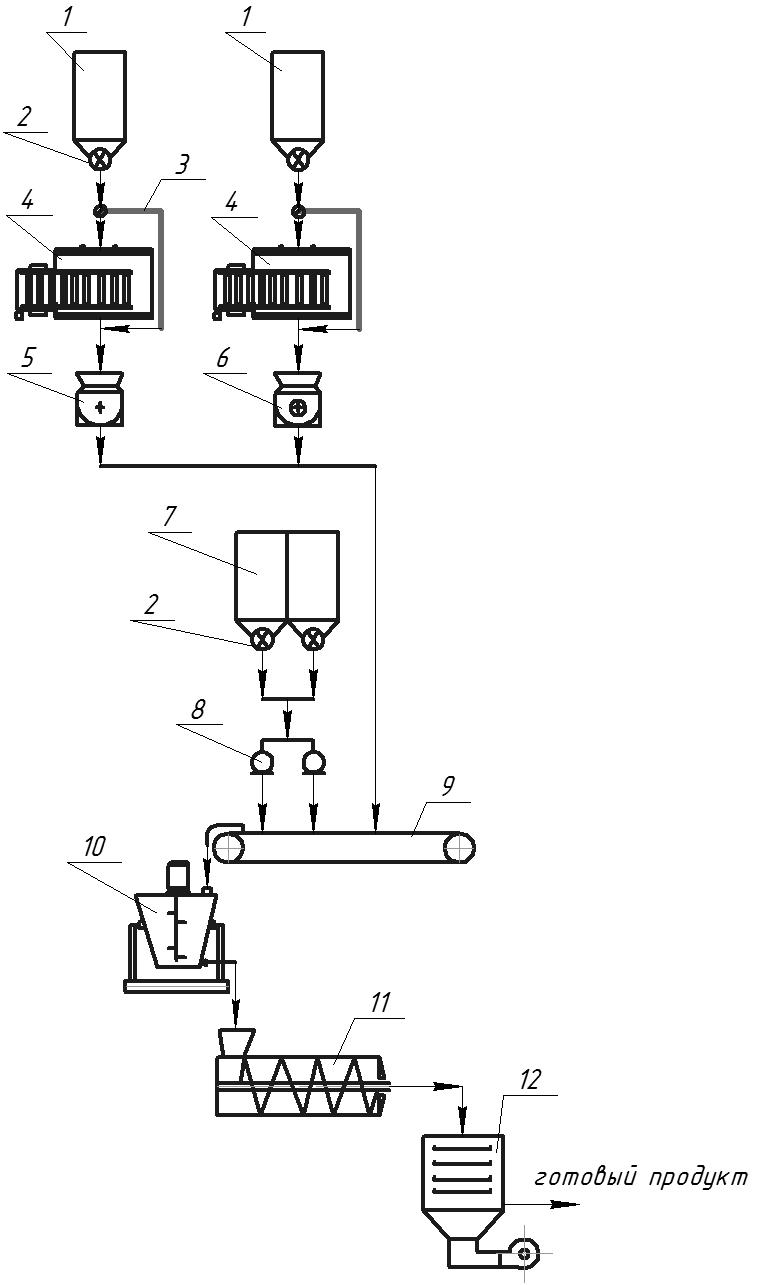
Рисунок 1 - Технологическая схема производства экструдированных комбикормов и добавок с заморозкой исходного сырья:
1 - бункера для хранения сыпучих компонентов; 2 - дозаторы; 3 - резервные трубопроводы для возможного прохождения продукта без шоковой заморозки; 4 - установки шоковой заморозки для обработки отходов исходного сырья (лузга подсолнечника, гречихи и отрубей); 5 и 6 – роторные дробилки; 7 - бункера для хранения жидких компонентов; 8 - форсунки для распыления жидких компонентов; 9 - ленточный транспортер; 10 - смеситель; 11 - экструдер; 12 - сушилка
Давление расплава экструдата в зоне дозирования достигает нужного уровня, что приводит к окончательному расплавлению мелких включений и образованию однородного по структуре и температуре расплава. Это необходимо для обеспечения заданной однородной по сечению температуры расплава продукта. Затем продукт попадает в предматричную зону. После выхода из матрицы происходит мгновенное испарение влаги из-за резкого перепада температуры и давления, что приводит к образованию пористой структуры и увеличению объема экструдата. После этого экструдат направляется в ленточную сушилку 12, где теплоноситель проникает через слой продукта по ленте, высушивая его, а затем удаляется из сушилки 12.
В технологическую схему можно добавить смеситель для более равномерного распределения жидких компонентов между частицами смеси лузги и мучнистого сырья, что способствует получению более однородного по влажности и содержанию сухих веществ экструдированного комбикорма и, следовательно, повышению его качества , , , .
Нами были проведены опыты по изучению эффективности полученной экструдированной кормосмеси.
Производство осуществлялось двумя технологиями: традиционной и авторской. Сырье подготавливалось путем увлажнения до рекомендуемой влажности, измельчения в молотковой дробилке и экструзии , , , . При использовании авторской технологии зерно замораживали методом шоковой заморозки до -10 °С, перед измельчением. Готовую продукцию упаковывали в мешки с использованием упаковочного полуавтомата. После перехода на стационарный режим для каждой технологии измеряли параметры, представленные в таблице 2.
Также была проведена оценка эффективности технологического процесса с использованием интегральных критериев с помощью программного обеспечения, основанная на методике интегральной оценки эффективности авторской технологии .
3. Основные результаты
Для подтверждения разработанной технологии были проведены полупромышленные испытания на ОАО «Оренбургский комбикормовый завод» (г. Оренбург).
Рабочий период предприятия составляет 236 рабочих дней в году; предприятие в состоянии реализовать всю производимую продукцию.
Суточная мощность производства экструдирования зерносмеси при 8 часовой работе цеха составит 2480 кг для традиционной технологии или 3600 кг экструдированной зерносмеси произведенной по предлагаемой технологии. Плановая численность работающих составляет 4 человека, из которых рабочих – 3 человек, ИТР – 1 человек.
При перепрофилировании цеха было необходимо изготовление измельчителя для проведения измельчения замороженного зернового сырья (ориентировочные затраты 900 тыс. руб. в ценах на 1.09.2020 г.).
Все остальное оборудование имелось в наличии (балансовая стоимость на 1.09.2020 г. – 2000 тыс.руб ). Расчет произведен в ценах на 01.09.2023 г.
Таблица 1 - Параметры процесса производства зерносмеси
№ п/п | Наименование параметров технологического процесса | Вид производства | |
традиционное | замораживание | ||
1 | Производительность, кг/ч | 310 | 450 |
2 | Расход электроэнергии, кВт/ч | 10,5 | 10 |
3 | Влажность пшеницы, % | 14 | 14 |
4 | Влажность ячменя, % | 14,5 | 14,5 |
5 | Влажность проса, % | 13,5 | 13,5 |
6 | Закладка соли на 100 кг зернового сырья, кг | 1 | 1 |
7 | Влажность соли, % | 3,5 | 3,5 |
8 | Потери при заморажевание зерносмеси, % | 0 | 0,01 |
9 | Потери при измельчении зерносмеси, % | 0,1 | 0,05 |
10 | Потери при экструдировании зерносмеси, % | 0,2 | 0,1 |
11 | Потери солевого раствора, % | 0,5 | 0,5 |
12 | Влажность материала подвергаемого измельчению и экструдированию, % | 16 | 20 |
13 | Влажность готового продукта, % | 10 | 10 |
14 | Потери при упаковке, % | 1 | 1 |
15 | Расход мешков на 100 кг готовой продукции, шт. | 0,5 | 0,5 |
Таблица 2 - Показатели эффективности технологии производства зерносмеси
№ п/п | Наименование показателя | Вид производства | |
без заморозки | с заморозкой | ||
1 | Критерий безотходности | 0,8274 | 0,8304 |
2 | Критерий глубины переработки сырья | 0,9352 | 0,9463 |
3 | Критерий экологичности | 0,9880 | 0,9930 |
4 | Интегральный критерий | 0,7644 | 0,7803 |
5 | Удельные затраты энергии на проведение процесса, кВт/кг | 0,955 | 0,563 |
6 | Выход готовой продукции из 100 кг крупяного сырья, кг | 95,0 | 95,3 |
Данные таблицы 2 свидетельствуют о повышении эффективности технологии выработки зерносмеси с применением замораживания зернового сырья. Интегральный критерий увеличился с 0,7644 до 0,7803. Причем удельные затраты энергии на проведение процесса значительно сокращаются с 0,034 кВт/кг. до 0,022 кВт/кг.
4. Заключение
Использование разработанной технологии, вместо традиционной на предприятии позволит:
Увеличить прибыль на 2297,38 тыс. руб.;
Увеличить рентабельность продукции на 7,2 %;
Снизить срок окупаемости на 0,05 года.
Снизить затраты на один руб. товарной продукции на 0,18 руб.
Таким образом, использование предложенной технологической схемы с применением шоковой заморозки позволит, по сравнению с применяемой технологией:
1) расширить ассортимент выпускаемых многокомпонентных комбикормов заданной пищевой ценности, адаптированных для различных видов животных;
2) повысить перевариваемость крупнорогатого скота и других с/х животных.