Improvement of technology of obtaining extruded mixed fodders and feed additives
Improvement of technology of obtaining extruded mixed fodders and feed additives
Abstract
When making mixed fodders, producers try to replace grain raw materials with various wastes of food and agro-industrial complex. Such aspiration is especially clear in the countries of Western Europe. This is due to the high cost of grain resources, which directly affects the final cost of agricultural products. Feeding costs in some cases can be up to 80% of the final selling price of products. Therefore, improvement of technologies of production of mixed fodders and diets for farm animals is an urgent task. As substitutes for grain, raw materials can be such industrial wastes as: beet pulp, stems of legumes, husks of various grain crops and others. Usually substitutes for grain raw materials contain a large proportion of fibre and lignin, which are difficult to digest during digestion in farm animals. For more complete assimilation of these substances it is necessary to carry out technological operations aimed at destruction of high biopolymer structures in order to obtain simpler easily digestible substances. The article examines the improvement of the technology of extruded mixed fodders and feed additives through the use of two-stage grinding operation with chemical treatment and freezing of raw materials.
1. Введение
Доля замещения зернового сырья может доходить до 85 % от общей массы производимых комбикормов, что достаточно существенно сказывается на результирующих затратах сельскохозяйственного производства . В качестве технологической операции при приготовлении комбикормов для увеличения переваримости рационально применять экструзию. При экструдировании кормовой смеси создаётся давление около 5 МПа и температура от 160 °С до 180 °С вследствие чего происходит разрыв высокобиополимерных цепей что обуславливает дальнейшее более полное и легкое усвоение комбикормового продукта под действием микрофлоры пищеварительного тракта животного . Характер механического воздействия в совокупности с высоким давлением и температурой обуславливает степень биохимических изменений клетчатки и лигнина в сырье. Для более глубокого преобразования высокобиополимерных структур необходимо перед экструдированием производить двухстадийное измельчение с химической обработкой и заморозкой сырья. При этом производительность пресс-экструдера и удельные затраты энергии на процесс сильно зависят от влажности экструдируемого сырья и от его гранулометрического состава. Чем больше влажность и меньше размер частиц экструдируемого сырья – тем легче и менее энегрозатратно проходит сам процесс экструдирования .
Экспериментально установлено, что при такой последовательности технологических операций удается максимально полно перевести высокомолекулярные соединения углеводов в низкомолекулярные углеводы. Количество сырой и кислоторастворимой клетчатки и лигнина в таких комбикормах уменьшается на 50% .
Немаловажным в процессе экструзии являются конструктивные особенности и механизм прессования. Заметное влияние на количество сырой клетчатки оказывает диаметр отверстий в матрице. При уменьшении диаметра отверстий матрицы содержание клетчатки и лигнина снижается что, объясняется более жестким механическим воздействием на продукт, а количество содержания низкомолекулярных углеводов повышается.
Предложенная последовательность проведения технологических операций показывает особенно большую эффективность при обработке комбикормового сырья с большим содержанием клетчатки. В этом случае «освобождение» и распад целлюлозы, гемицеллюлоз и лигнина наиболее значительны .
Применение химической обработки сырья в предлагаемой технологии, позволяет эффективно использовать в качестве заменителей зернового сырья лузги крупяных культур и подсолнечника, содержащие в своём составе высокий процент целлюлозы и лигнина.
Клеточные оболочки отходов растительного сырья обладают ультраструктурой схожей по строению со структурой железобетона. Микрофибриллы целлюлозы выполняют армирующую роль, а пространство между ними заполняет лигнин, который обладает высокой прочностью на сжатие . Вследствие воздействия химических реагентов на такую структуру сырья показатель деструкции лигнина и целлюлозы значительно увеличивается.
На кафедре машин и аппаратов химических и пищевых производств Оренбургского государственного университета проводятся исследования по разработке технологии получения экструдированных комбикормов с частичной заменой зернового сырья на отходы растительного происхождения (лузга крупяных культур и подсолнечника), содержащие в своём составе большой процент лигнина и клетчатки. В процессе проведения исследований в качестве основного оборудования использовали шкаф шоковой заморозки, молотковую дробилку, роторную дробилку, кормовой одношнековый пресс-экструдер .
Цель работы заключалась в совершенствовании технологии получения экструдированных комбикормов с применением в качестве заменителей зерна отходов растительного происхождения различных отраслей. Технологический результат достигается за счет внедрения в производство двух стадийного измельчения растительного сырья, с обработкой его различными химическими реагентами и охлаждением до отрицательной температуры.
2. Основная часть
Объектом исследования является совершенствование технологии получения экструдированных комбикормов. Для проведения экспериментальных исследований и апробации предлагаемой технологии использовали: шкаф шоковой заморозки, молотковую дробилку (ОАО «Долина»), роторную дробилку («Фермер», конструкция ООО «Уралспецмаш»), одношнековый пресс-экструдер ПЭШ-30/1.
Для эксперимента готовили три состава смесей растительных отходов с высоким содержанием целлюлозы и лигнина: первый состав смеси содержал 80% гречишной лузги и 20 % пшеничных отрубей; второй состав смеси содержал 80% подсолнечной лузги и 20% пшеничных отрубей; третий состав смеси содержал 20% гречишной лузги, 20% подсолнечной лузги и 60% пшеничных отрубей. Все три состава смесей на первой стадии подвергали измельчению на молотковой и роторной дробилке. Далее измельчённое сырьё обрабатывали 3, 4 и 5% .раствором NaOH и замораживали до температуры минус 20 0С. После этого измельчённые и замороженные смеси подвергали второй стадии измельчения на молотковой и роторной дробилке.
Анализ экспериментальных данных показал, что сопротивляемость растительного сырья измельчению с понижением температур снижается. Такой подход к реализации предложенной технологии позволяет снизить энергозатраты на измельчение. При замерзании вода, содержащаяся внутри растительных клеток, превращается в лед и разрывает их структуру, что снижает сопротивляемость к измельчению и увеличивает хрупкость , .
После второй стадии измельчения смеси подвергали экструдированию на кормовом одношнековом пресс-экструдере при этом частоту вращения шнека пресс-экструдера варьировали в диапазоне от 30 до 120 об/мин , , .
Производительность пресс-экструдера определяли по отобранной навеске за определенный временной промежуток с одновременным регистрированием затраченной мощности за тот же промежуток времени.
По результатам проведённых экспериментальных исследований для всех девяти образцов были построены следующие зависимости: производительности пресс-экструдера Q (кг/час) от частоты вращения шнека n (об/мин); удельной энергоемкости процесса экструзии Э (кВт/час кг) от частоты вращения шнека n (об/мин) , , , .
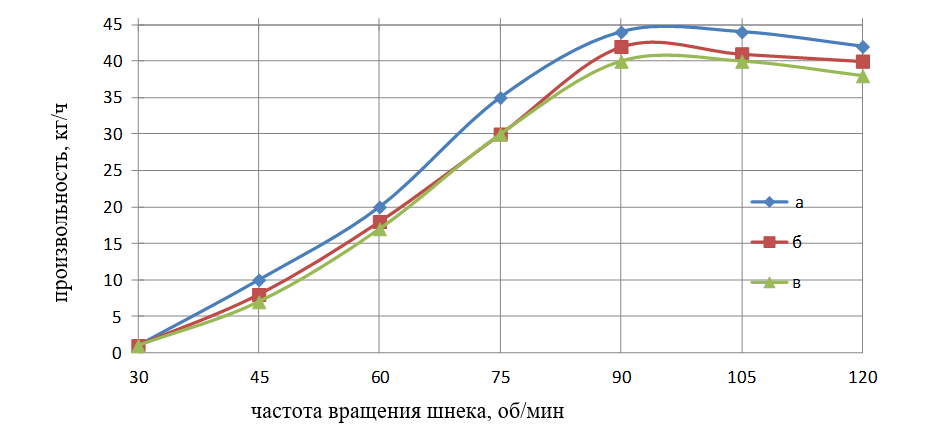
Рисунок 1 - Зависимость производительности пресс-экструдера от частоты вращения его шнека для кормосмесей различного состава при её обработке 3 % раствором NaOH:
а – первый состав смеси; б - второй состав смеси; в - третий состав смеси
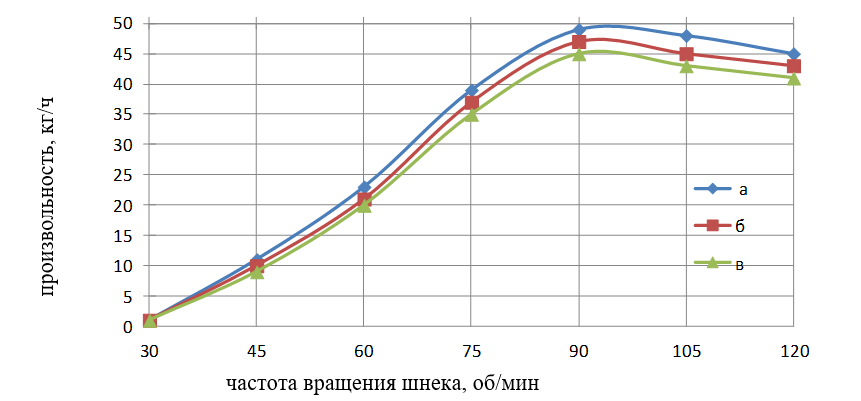
Рисунок 2 - Зависимость производительности пресс-экструдера от частоты вращения его шнека для кормосмесей различного состава при её обработке 4 % раствором NaOH:
а – первый состав смеси; б - второй состав смеси; в - третий состав смеси
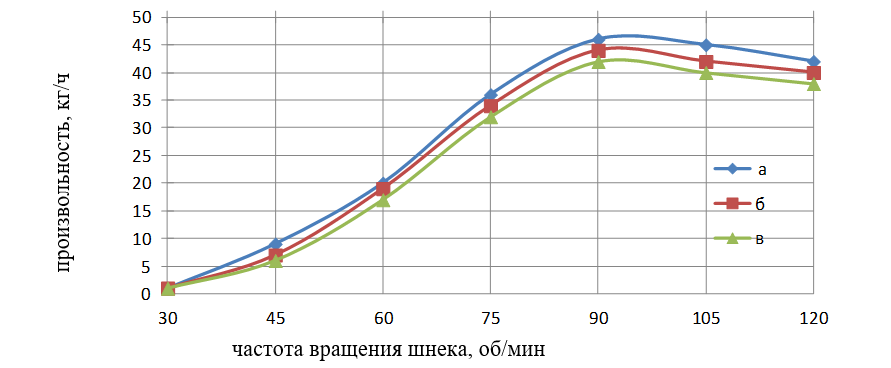
Рисунок 3 - Зависимость производительности пресс-экструдера от частоты вращения его шнека для кормосмесей различного состава при её обработке 5 % раствором NaOH:
а – первый состав смеси; б - второй состав смеси; в - третий состав смеси
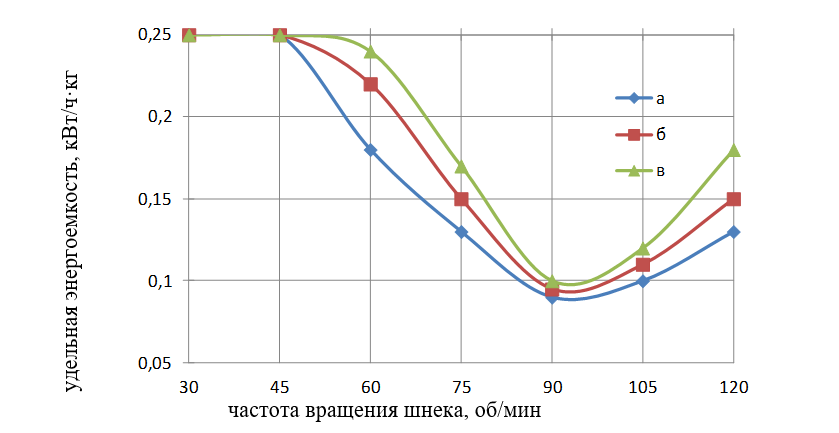
Рисунок 4 - Зависимости удельной энергоемкости процесса экструзии от частоты вращения шнека для кормосмесей различного состава при её обработке 3 % раствором NaOH:
а – первый состав смеси; б - второй состав смеси; в - третий состав смеси
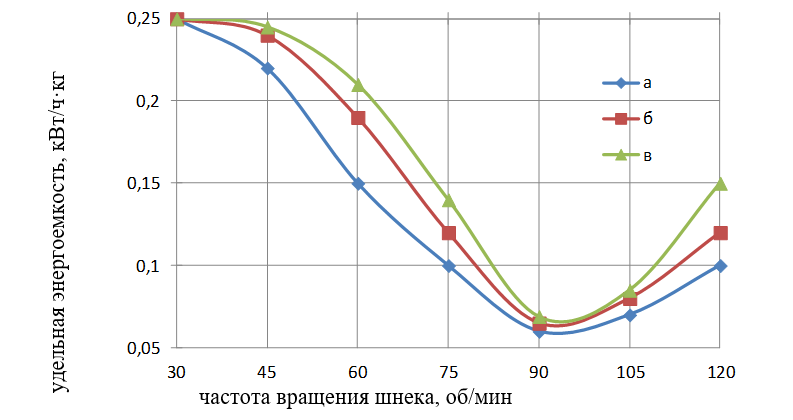
Рисунок 5 - Зависимости удельной энергоемкости процесса экструзии от частоты вращения шнека для кормосмесей различного состава при её обработке 4 % раствором NaOH:
а – первый состав смеси; б - второй состав смеси; в - третий состав смеси
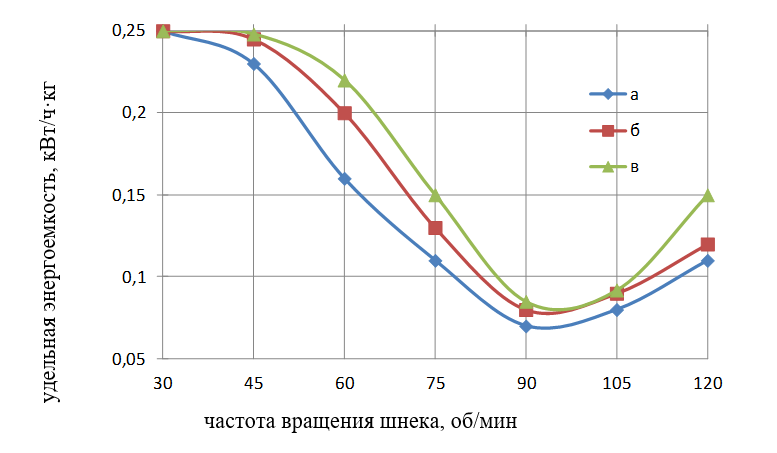
Рисунок 6 - Зависимости удельной энергоемкости процесса экструзии от частоты вращения шнека для кормосмесей различного состава при её обработке 5 % раствором NaOH:
а – первый состав смеси; б - второй состав смеси; в - третий состав смеси
3. Заключение
Таким образом, можно констатировать, что для совершенствования предложенной технологии производства экструдированных комбикормов с применением двух стадийной операции измельчения, обработкой химическими реагентами и заморозкой сырья является рациональным использование в качестве химических реагентов 4% раствор NaOH.