Finite Element Modelling of Stiffness Parameters of Stressed State of Small-Size Steel Plates from Long Products for Small-Size CNC Machine Tools with Reinforcing Elements
Finite Element Modelling of Stiffness Parameters of Stressed State of Small-Size Steel Plates from Long Products for Small-Size CNC Machine Tools with Reinforcing Elements
Abstract
The aim of this article is to theoretically substantiate, from the point of view of stiffness, the possibility of manufacturing one of the load-bearing parts of a previously developed syntagranic frame with loaded reinforcing elements from long steel bars. In particular, the steel end plates of the bed and their lateral prismatic columns are examined. In the present work, a comparison of the stiffness of the machine frame end plates has been carried out when monolithic columns are used in their construction and when rolled columns are applied. The stiffness comparison is carried out by means of modelling in the computer-aided design system "CATIA", the conditions of bonding in which are substantiated by the frame manufacturing technology. It is shown that even the case of using welded columns, consisting of rolled steel with minuscule side square in the end plates of the bed, leads to a non-critical reduction in the stiffness of the design of the ends, due to their special geometry and the direction of the vector of the applied force. Thus, the scientific novelty of the work follows from the new method of manufacturing and consists in the study and numerical evaluation of a new variant for manufacturing of end elements of the previously developed frame structure, in particular from rolled steel, and justification of its applicability from the position of stiffness.
1. Введение
Вопросы жесткости различных базовых узлов станков с ЧПУ, в особенности наиболее податливых – настольных станков, остаются актуальными ввиду их прямого влияния на достигаемую точность работы оборудования , . При этом, на итоговую жесткость конструкции влияет не только её материал и геометрия, но так же и способ по которому данная конструкция была изготовлена. Так, например, резьбовые соединения зачастую уступают по жесткости и прочности сварным, а сварные конструкции, в свою очередь, менее жесткие, чем цельные и литые . В этой связи для решения вопросов применения настольных станков ЧПУ облегченной, и достаточно жесткой конструкции актуальны исследования параметров жесткости напряженного состояния их сборных станин, изготовленных с применением различных, например, аддитивных, и (или) традиционных технологий.
В данной работе выполнен анализ варианта изготовления торцевых плит сборной станины из сортового проката посредством его резания и приваривания призматических элементов (цельных), для снижения себестоимости, причем для проведения численной оценки был принят наиболее неблагоприятный, предельный вариант конструкции призмы, когда она изготовлена сварной из нескольких отрезков проката.
Настоящая работа является логическим продолжением и углублением ранее опубликованной статьи, где представлена конструкция станины с нагруженными армирующими элементами, схема армирования и общая технология её изготовления . Таким образом, цель работы заключается в описании и анализе нового способа изготовления предложенных в предыдущей работе торцовых плит станины, а также в сравнительной оценке его применимости, в первую очередь на предмет обеспечиваемой жесткости. Теоретическая значимость работы состоит в углублении тематики поиска, разработки и анализа различных подходов по изготовлению предложенной конструкции станины с напряженными армирующими элементами для настольных станков, что актуально ввиду крайней дороговизны и сложности изготовления монолитного торца станины с призмами – . Кроме того, оценка применимости такой конструкции станин, позволит перейти к разработке аддитивной технологии их изготовления, как инновационной технологии. Данные решения в настоящее время находятся на этапе патентования.
Метод конечно-элементного моделирования параметров жесткости широко используется при исследовании различных металлических конструкций , , . В этой работе данный метод является предпочтительным ввиду сложности геометрии конструкции и её неоднородности в случае сварных колонн.
2. Описание способа изготовления торцов станины с применением проката, обоснование условий нагружения и моделирование предельной сварной конструкции на жесткость
Перед переходом к непосредственному объекту исследования, обратимся к конструкции станины (см. рис. 1), в которой используются рассматриваемые торцы. Конструкция станины состоит из двух стальных торцов 1, стянутых армирующими элементами 2 круглого сечения диаметром от 15 до 35 мм. Армирующие элементы упруго растянуты, закреплены контргайками 3 и, поэтому, обеспечивают жесткость стальной конструкции. Все прочее пространство заполнено полимербетоном. Более подробно конструкция, её обоснование, значимость и технология изготовления изложена в работе – .
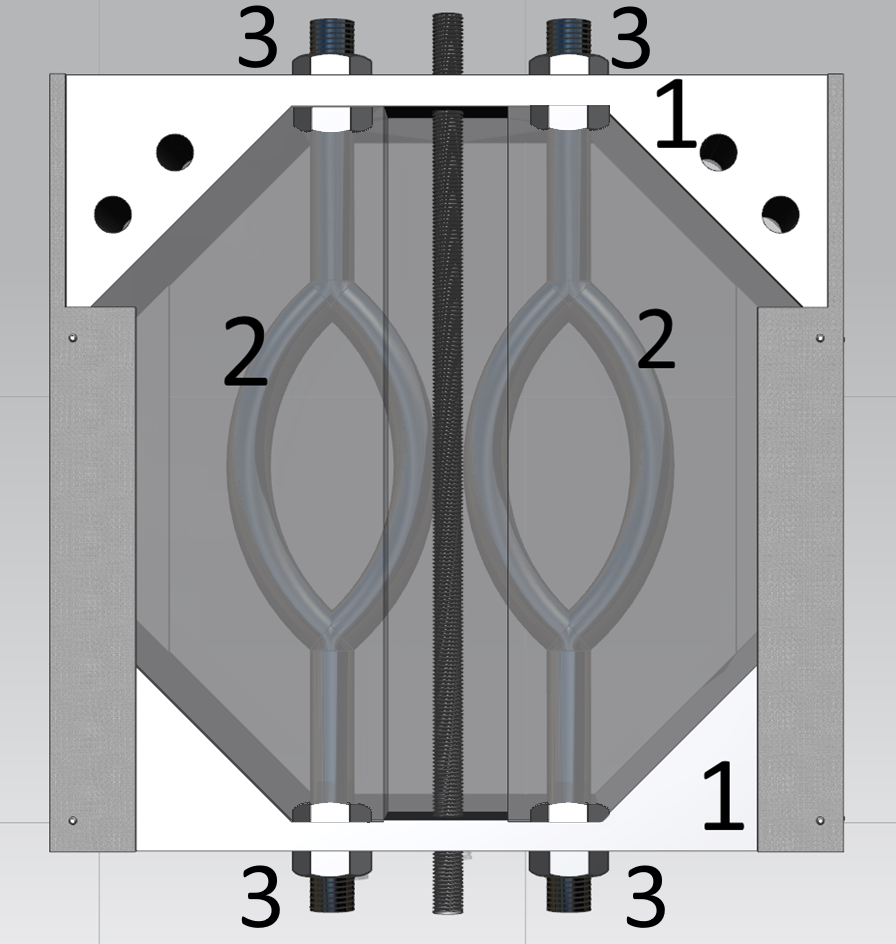
Рисунок 1 - Общая конструкция станины:
1 – торцевые плиты станины; 2 – армирующие элементы (нагруженные); 3 – системы контргаек
Примечание: вид сверху
Для изготовления торцевых плит согласно предложенному методу предполагается использовать сортовой квадратный прокат по ГОСТ 2591-2006. Наиболее технологичным решением для реализации на практике, разумеется, будет применение проката с наибольшей стороной квадрата, а именно 120 – 150 мм, что соответствует габаритному размеру рассматриваемой призмы – .
Однако, поскольку в теоретических расчетах необходимо учитывать предельный вариант, (т.е. вариант, приводящий к наименьшей жесткости), то в рамках данного исследования рассмотрим один из самых неблагоприятных, нетехнологичных вариантов и примем для моделирования сварную призму из проката, сторона которого равна лишь 10 мм. Площадь его сечения составляет 1 см2. Площадь же поперечного сечения одной треугольной призмы станины может варьироваться от 72 см2 до 112,5 см2. Важно отметить, что использование на практике данного размера проката не подразумевается и рассмотрено лишь в качестве наихудшего по жесткости случая для нашего моделирования. В практической реализации, как отмечено выше, рационально использовать цельную призму, получаемую из проката с бОльшим поперечным сечением.
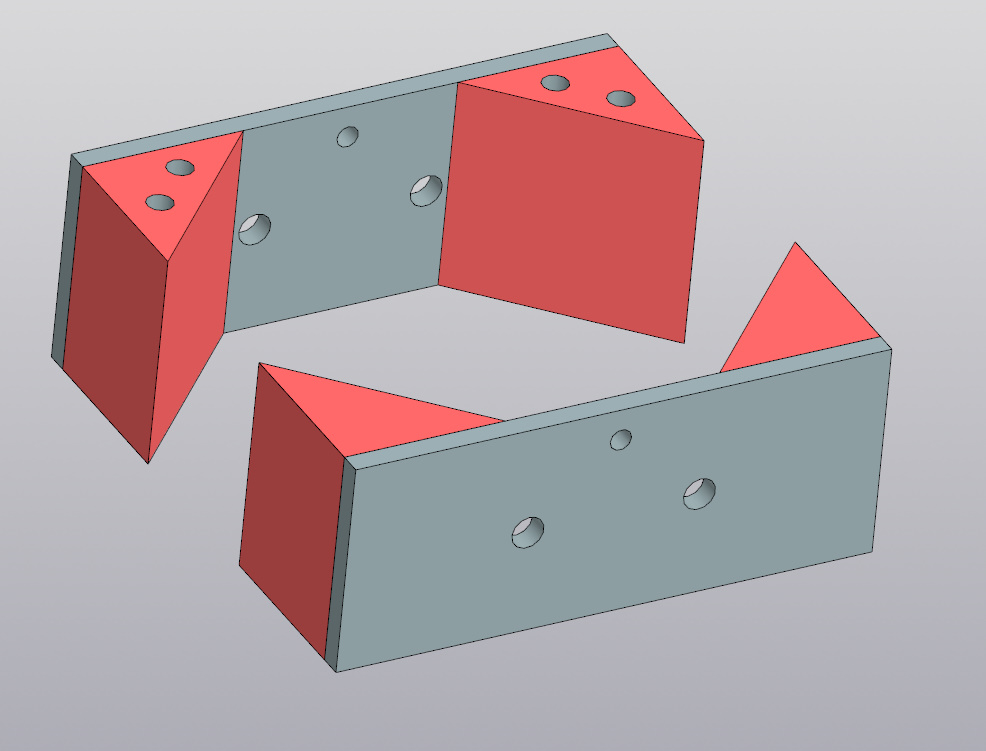
Рисунок 2 - Торцы станины
Примечание: красным отмечены рассматриваемые цельные треугольно-призматические колонны
Итак, при рассмотрении наихудшего предельного случая использования проката, принимаем случай сварной призмы. Неизбежно требуются некоторые упрощения для моделирования, с рядом введённых допущений. В настоящем исследовании для представления в расчетной модели сварных швов между отрезками малого проката 3, нами были использованы цилиндрические тела 1, а сформированные при этом пустоты 2 призваны учесть не только пористости, сторонние включения в сварном шве и прочие внутренние дефекты, но так же и имитировать призму, полученную аддитивно (для дальнейших исследований) (см. рис. 3). На рисунке 3 изображена расчетная модель сварной призмы, содержащей высокую концентрацию сварных швов на единицу площади.
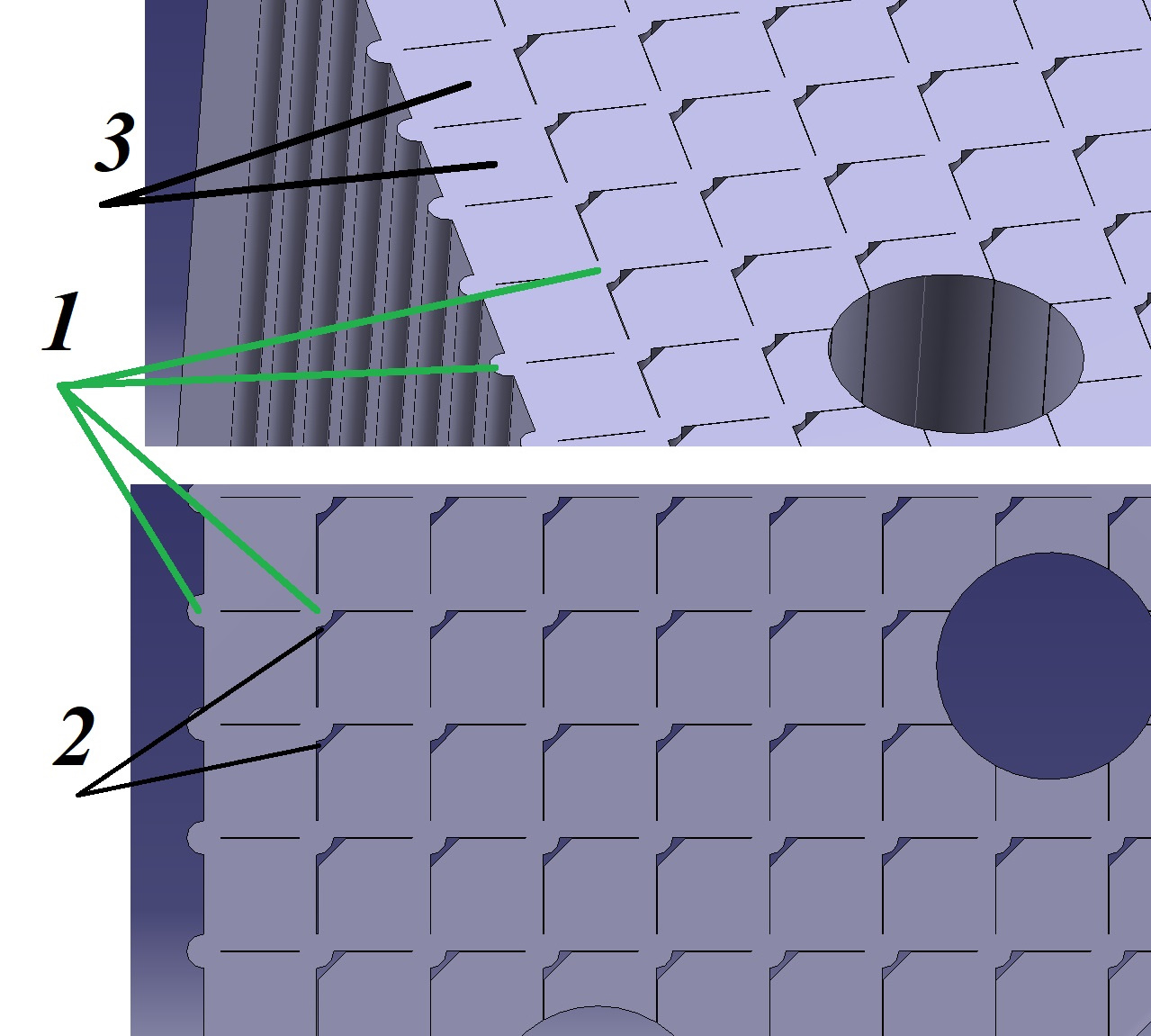
Рисунок 3 - Структура тела, моделирующего предельную сварную призму:
1 – сварные швы; 2 – пустоты; 3 – отрезки квадратного проката малого сечения
Итак, для наглядного отображения и обоснования как направления, места приложения возмущающих сил (см. рис. 4(б, в)), так и места установки заделки (см. рис. 4(а)), ниже представлена иллюстрация закрепления торцов станины при установке в них нагруженных армирующих элементов. Стрелками обозначены векторы действия сил сжатия в армирующих элементах.
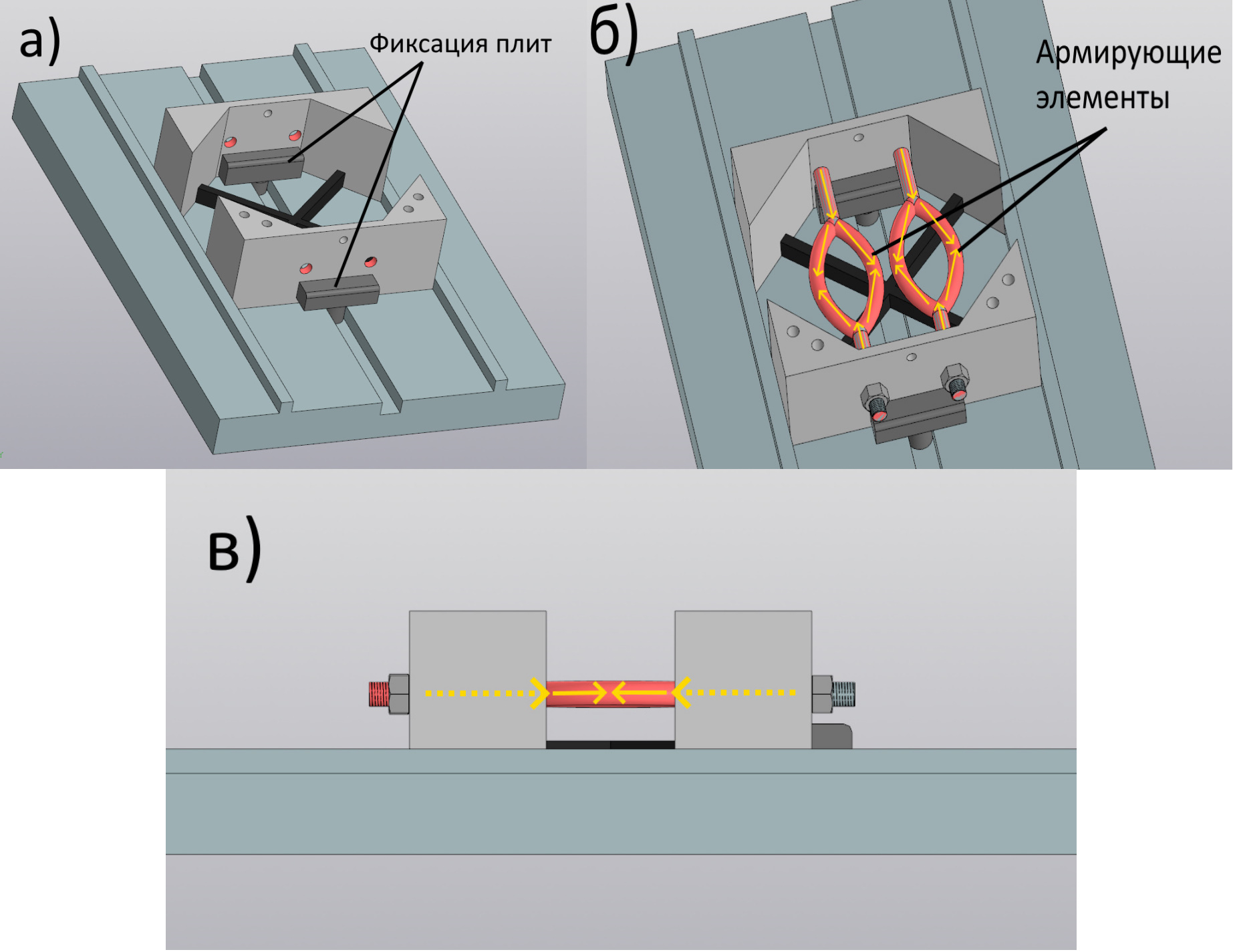
Рисунок 4 - Обоснование мест установки заделки и приложения сил:
а - расположение фиксирующих элементов относительно торцевых плит станины; б, в - места приложения и направление возмущающих сил F
При расчете значений жесткостей конструкций, введём в формулу (3) поправочный коэффициент заполнения сварной призмы. Выведем общую методику определения коэффициента k, исходя из параметров, обозначенных на рисунке 5. Для этого, определим площадь поперечного сечения отрезка проката с учетом полости SСЕЧ двумя способами – через длину стороны полости и через длину стороны проката, но с введением дополнительного множителя k0, показывающего, во сколько раз длина a1 отличается от длины a. Тогда, имеем:
отсюда,
отсюда, искомый коэффициент k:
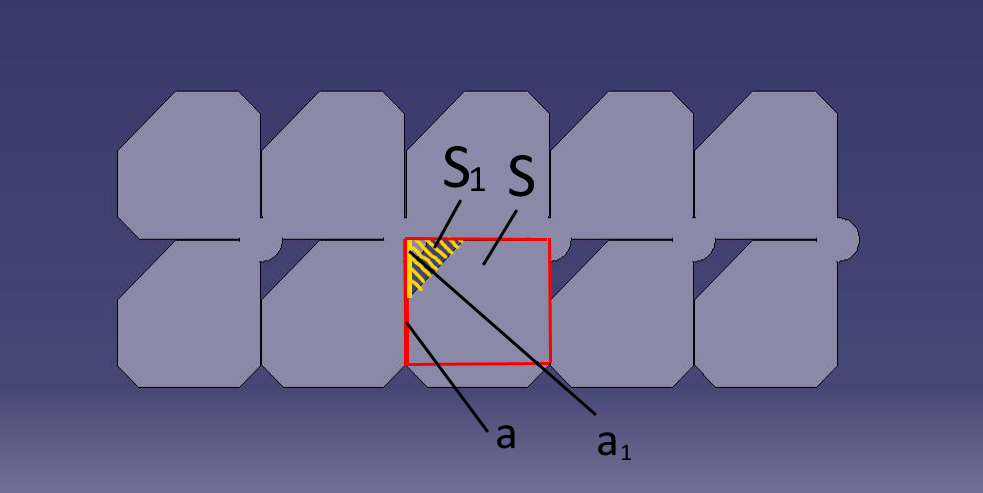
Рисунок 5 - Фрагмент предельной сварной призмы из малого проката:
a – длина стороны отрезка; a1 – длина стороны полости S и S1 – Площади отрезка и полости соответственно
3. Основные результаты
По результатам моделирования получим величины перемещений в различных точках тела в обоих случаях. Поскольку предметом данного исследования является жесткость конструкций, то примем во внимание лишь максимальные значения полученных перемещений и, зная величину приложенных сил, рассчитаем значения жесткости для их оценки. Результаты проведённых расчётов, на основе описанных выше вводных условий, представлены ниже (см. рис. 6, 7).
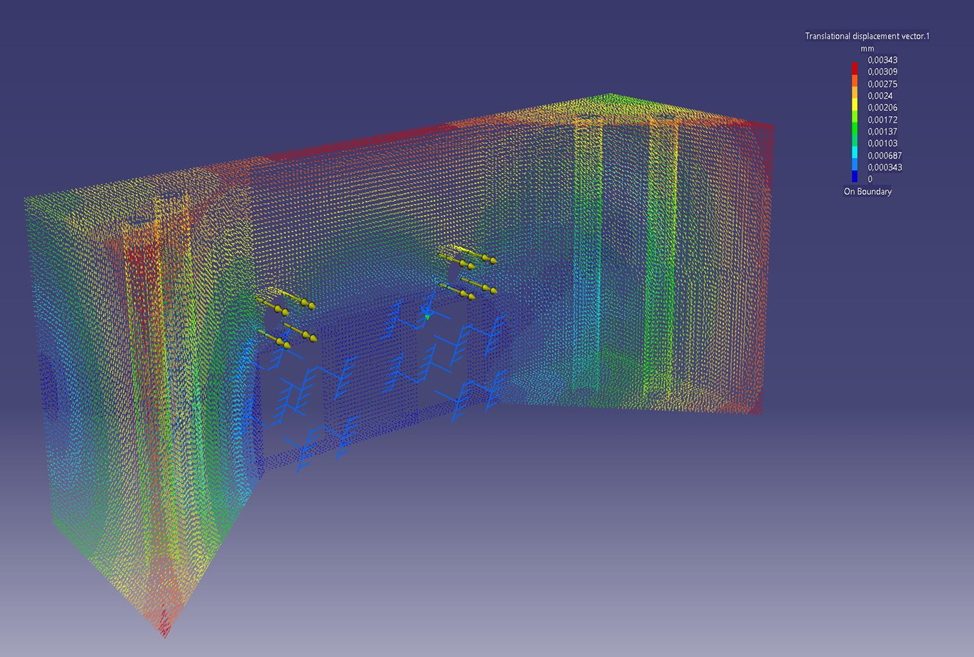
Рисунок 6 - Результат расчёта на жесткость методом конечных элементов монолитной конструкции торца станины
где, F – величина прикладываемой к конструкции внешней силы
x1 – величина перемещений, полученных в результате расчета

Рисунок 7 - Результат расчёта на жесткость методом конечных элементов конструкции торца станины со сварными призмами из малого проката
Примечание: предельные призмы
где, F – величина прикладываемой к конструкции внешней силы
x2 – величина перемещений, полученных в результате расчета
k – коэффициент, учитывающий контактную площадь
В соответствии со сделанными предположениями и логикой, сварная конструкция обладает меньшей жесткостью, чем монолитная, однако перемещения в обоих случаях достаточно малы. Для наглядной сравнительной оценки жесткостей двух конструкций рассчитаем относительную потерю жесткости (в процентах) при замене литой конструкции на сварную по формуле (4):
4. Обсуждение
Итак, соответственно проведенному исследованию, при рассмотрении предельного случая предложенного способа изготовления призм для торцов станины из сортового проката, жесткость торцевой плиты снижается приблизительно на 38%. Такое снижение жесткости не является критическим для конструкции ввиду малых абсолютных перемещений. Более того, принимая во внимание тот факт, что был намеренно промоделирован предельный случай составной (сварной) призмы, содержащий высокую концентрацию сварных швов в её объеме, можно утверждать, что предлагаемая практическая реализация конструкции с цельным прокатом большего сечения (без сварных швов в объеме), с запасом обеспечит необходимую жесткость конструкции.
Столь низкий процент снижения жесткости, полученный по результатам моделирования, объясняется сразу несколькими факторами. Во-первых, это не совершенство математических моделей как таковых, в том числе и построенная нами для расчёта модель не учитывает всех дефектов сварных швов и отрезков проката. Во-вторых, сама геометрия конструкции торцов станины изначально предусматривала возможность изготовления методом сварки. В-третьих, модель не учитывала наличие внутренних напряжений в конструкции, векторы направления которых могли бы совпасть с вектором перемещений.
К плюсам рассмотренного метода изготовления, помимо обеспечения высокой жесткости, можно отнести применение стандартного квадратного проката ГОСТ, его относительную дешевизну, вариативность размеров и доступность. Так же, поскольку метод заключается лишь в диагональной резке и приваривании этого проката к торцевой пластине, то номенклатура инструмента для изготовления конструкции ограничивается сварочным аппаратом и отрезной пилой (либо отрезной станок).
Важно отметить, что рассмотренный в данной работе способ обладает и рядом минусов. Во-первых, при приваривании призмы к торцевой пластине невозможно обеспечить высокую точность итоговой детали, что может оказаться критично для такого ответственного узла станка как станина. Более того, в случае обеспечения точности при сварке, после окончания процесса в конструкции будут иметь место остаточные напряжения, что потенциально может привести к изменению её геометрии или разрушению в случае релаксации напряжений , .
Причиной же, ввиду которой в тексте статьи предлагается реализовывать на практике именно цельные, а не сварные призмы, является наличие нижнего предела величины сечения проката, при достижении которого изготовление призмы становится не только трудоемким, но и невозможным ввиду появления при сварке трещин в шве и прилегающей к нему зоне. Полученные при этом остаточные напряжения приведут к разрушению конструкции. Соответственно, можно сделать однозначный вывод о нецелесообразности использования сварных призм (т.е. проката, сторона которого меньше, чем габаритная ширина призмы).
5. Заключение
Таким образом, предложенный вариант изготовления торцов синтеграновой станины с нагруженными армирующими элементами, является применимым, требует относительно низких затрат на материалы (сортовой прокат) и применяемый инструмент, а так же обеспечивает высокую жесткость для конструкции, но является ситуативным ввиду ряда обозначенных выше недостатков.