Экономическое обоснование технологии производства кормов и кормовых добавок с использованием замораживания зернового сырья и продуктов его переработки
Экономическое обоснование технологии производства кормов и кормовых добавок с использованием замораживания зернового сырья и продуктов его переработки
Аннотация
Существование РФ в условиях санкционных ограничений ставит задачи по снижению себестоимости продукции во всех отраслях народного хозяйства и промышленности, что можно реализовать путем внедрения инновационных технологий и нестандартных методов решения возникающих проблем.
Необходимо отметить, что это касается и сферы кормопроизводства, так как удешевление технологии выработки комбикормов позволит их сделать более доступными для сферы животноводства и птицеводства, а следовательно увеличить производство мясной и молочной продукции. В результате литературно-патентного обзора и проведения собственных исследований нами было установлено, что одним из перспективных направлений совершенствования технологий кормопроизводства является использование для измельчения зернового сырья, предварительно замороженного до отрицательных температур. В этом состоянии влага, содержащаяся в порах зерна, превращается в лёд, расширяясь и разрушая структуру материала, что способствует облегчению процесса измельчения.
С этой целью длительное время на кафедре МАХПП проводятся исследования по влиянию отрицательных температур на качественные и количественные показатели проведения процесса измельчения зерна и продуктов его переработки, в частности различных видов лузги и для производства комбикормов, добавок к ним в рассыпном и виде экструдатов.
Исследование показали, что шоковая заморозка зернового сырья и продуктов его переработки, в частности лузги подсолнечника и гречихи, позволяет снизить энергозатраты на его измельчение и повысить питательные свойства получаемого корма. Таким образом, на основании полученных результатов исследований нами была предложена технологическая линия производства кормов и кормовых добавок с использованием замороженного зернового сырья и продуктов его переработки, проведено её экономическое обоснование.
1. Введение
На основе результатов исследований была разработана технология изготовления экструдированных комбикормов с добавками, включающая заморозку перед измельчением исходного сырья (рисунок 1). Общая схема технологии включает следующие этапы: в бункере 1 загружаются лузга (подсолнечника, гречихи) и мучные отруби, далее сырье подается на установку шоковой заморозки 4, работающую в различных режимах для лузги и мучного сырья. Лузга направляется на молотковую дробилку 5, а мучные отруби на роторную дробилку 6. Воздействие охлаждения замороженным воздухом на оболочку и мелкую часть зерна делает их хрупкими, что позволяет эффективно измельчать оболочку до потери её режущих свойств в молотковой дробилке 5, а также эффективно измельчать мелкую часть зерна до размера частиц менее 100 микрометров в роторной дробилке 6.
Это позволяет безопасно вводить оболочку в корм животных, не беспокоясь о её острой кромке, а также добавлять измельченное мучное сырье (отруби) размером менее 100 микрометров в экструдируемые комбикорма, что улучшает усвояемость , .
2. Методы и принципы исследования
Исходные сыпучие компоненты, хранящиеся в бункерах 1, роторными дозаторами, которые установлены в нижней части бункеров подаются в строго определенной порции на установку шоковой заморозки 4.
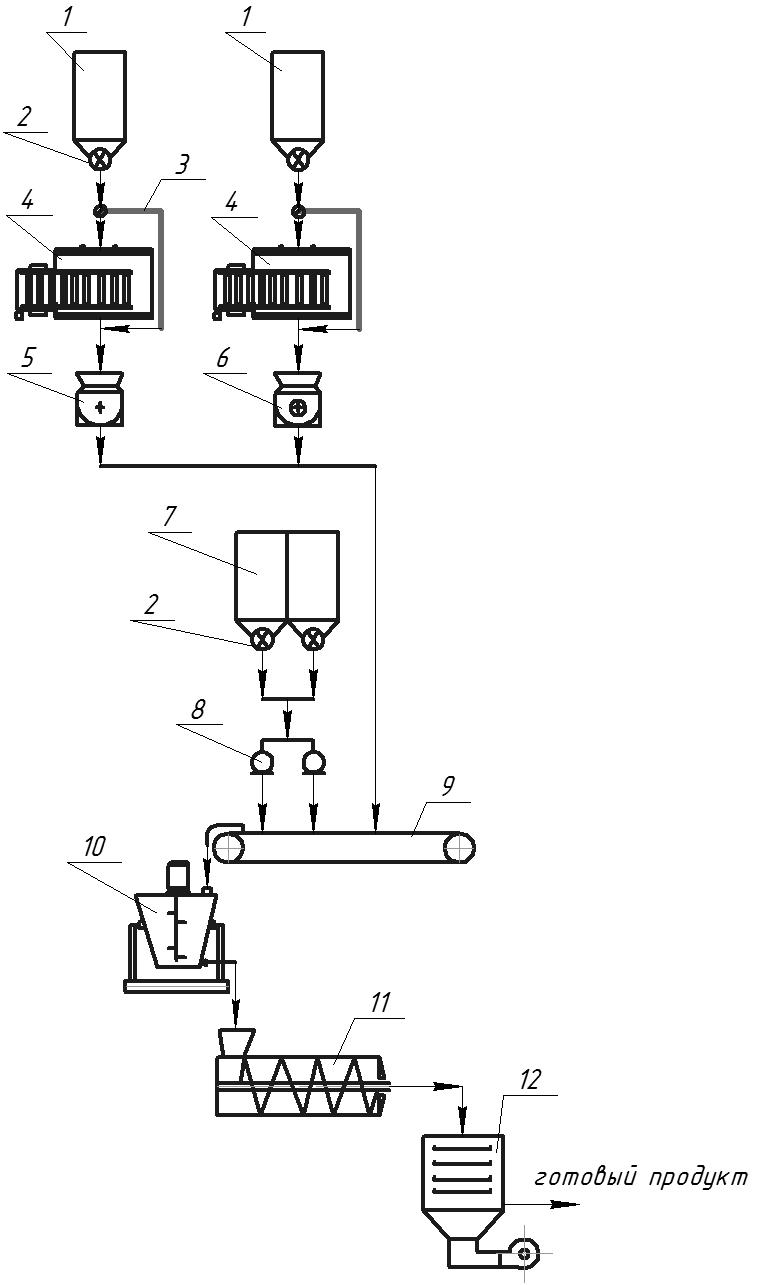
Рисунок 1 - Технологическая схема производства экструдированных комбикормов и добавок с заморозкой исходного сырья:
1 - бункера для хранения сыпучих компонентов; 2 - дозаторы; 3 - резервные трубопроводы для возможного прохождения продукта без шоковой заморозки; 4 - установки шоковой заморозки для обработки отходов исходного сырья (лузга подсолнечника, гречихи и отрубей); 5 и 6 – роторные дробилки; 7 - бункера для хранения жидких компонентов; 8 - форсунки для распыления жидких компонентов; 9 - ленточный транспортер; 10 - смеситель; 11 - экструдер; 12 - сушилка
Давление расплава экструдата в зоне дозирования достигает нужного уровня, что приводит к окончательному расплавлению мелких включений и образованию однородного по структуре и температуре расплава. Это необходимо для обеспечения заданной однородной по сечению температуры расплава продукта. Затем продукт попадает в предматричную зону. После выхода из матрицы происходит мгновенное испарение влаги из-за резкого перепада температуры и давления, что приводит к образованию пористой структуры и увеличению объема экструдата. После этого экструдат направляется в ленточную сушилку 12, где теплоноситель проникает через слой продукта по ленте, высушивая его, а затем удаляется из сушилки 12.
В технологическую схему можно добавить смеситель для более равномерного распределения жидких компонентов между частицами смеси лузги и мучнистого сырья, что способствует получению более однородного по влажности и содержанию сухих веществ экструдированного комбикорма и, следовательно, повышению его качества , , , .
Нами были проведены опыты по изучению эффективности полученной экструдированной кормосмеси.
Производство осуществлялось двумя технологиями: традиционной и авторской. Сырье подготавливалось путем увлажнения до рекомендуемой влажности, измельчения в молотковой дробилке и экструзии , , , . При использовании авторской технологии зерно замораживали методом шоковой заморозки до -10 °С, перед измельчением. Готовую продукцию упаковывали в мешки с использованием упаковочного полуавтомата. После перехода на стационарный режим для каждой технологии измеряли параметры, представленные в таблице 2.
Также была проведена оценка эффективности технологического процесса с использованием интегральных критериев с помощью программного обеспечения, основанная на методике интегральной оценки эффективности авторской технологии .
3. Основные результаты
Для подтверждения разработанной технологии были проведены полупромышленные испытания на ОАО «Оренбургский комбикормовый завод» (г. Оренбург).
Рабочий период предприятия составляет 236 рабочих дней в году; предприятие в состоянии реализовать всю производимую продукцию.
Суточная мощность производства экструдирования зерносмеси при 8 часовой работе цеха составит 2480 кг для традиционной технологии или 3600 кг экструдированной зерносмеси произведенной по предлагаемой технологии. Плановая численность работающих составляет 4 человека, из которых рабочих – 3 человек, ИТР – 1 человек.
При перепрофилировании цеха было необходимо изготовление измельчителя для проведения измельчения замороженного зернового сырья (ориентировочные затраты 900 тыс. руб. в ценах на 1.09.2020 г.).
Все остальное оборудование имелось в наличии (балансовая стоимость на 1.09.2020 г. – 2000 тыс.руб ). Расчет произведен в ценах на 01.09.2023 г.
Таблица 1 - Параметры процесса производства зерносмеси
№ п/п | Наименование параметров технологического процесса | Вид производства | |
традиционное | замораживание | ||
1 | Производительность, кг/ч | 310 | 450 |
2 | Расход электроэнергии, кВт/ч | 10,5 | 10 |
3 | Влажность пшеницы, % | 14 | 14 |
4 | Влажность ячменя, % | 14,5 | 14,5 |
5 | Влажность проса, % | 13,5 | 13,5 |
6 | Закладка соли на 100 кг зернового сырья, кг | 1 | 1 |
7 | Влажность соли, % | 3,5 | 3,5 |
8 | Потери при заморажевание зерносмеси, % | 0 | 0,01 |
9 | Потери при измельчении зерносмеси, % | 0,1 | 0,05 |
10 | Потери при экструдировании зерносмеси, % | 0,2 | 0,1 |
11 | Потери солевого раствора, % | 0,5 | 0,5 |
12 | Влажность материала подвергаемого измельчению и экструдированию, % | 16 | 20 |
13 | Влажность готового продукта, % | 10 | 10 |
14 | Потери при упаковке, % | 1 | 1 |
15 | Расход мешков на 100 кг готовой продукции, шт. | 0,5 | 0,5 |
Таблица 2 - Показатели эффективности технологии производства зерносмеси
№ п/п | Наименование показателя | Вид производства | |
без заморозки | с заморозкой | ||
1 | Критерий безотходности | 0,8274 | 0,8304 |
2 | Критерий глубины переработки сырья | 0,9352 | 0,9463 |
3 | Критерий экологичности | 0,9880 | 0,9930 |
4 | Интегральный критерий | 0,7644 | 0,7803 |
5 | Удельные затраты энергии на проведение процесса, кВт/кг | 0,955 | 0,563 |
6 | Выход готовой продукции из 100 кг крупяного сырья, кг | 95,0 | 95,3 |
Данные таблицы 2 свидетельствуют о повышении эффективности технологии выработки зерносмеси с применением замораживания зернового сырья. Интегральный критерий увеличился с 0,7644 до 0,7803. Причем удельные затраты энергии на проведение процесса значительно сокращаются с 0,034 кВт/кг. до 0,022 кВт/кг.
4. Заключение
Использование разработанной технологии, вместо традиционной на предприятии позволит:
Увеличить прибыль на 2297,38 тыс. руб.;
Увеличить рентабельность продукции на 7,2 %;
Снизить срок окупаемости на 0,05 года.
Снизить затраты на один руб. товарной продукции на 0,18 руб.
Таким образом, использование предложенной технологической схемы с применением шоковой заморозки позволит, по сравнению с применяемой технологией:
1) расширить ассортимент выпускаемых многокомпонентных комбикормов заданной пищевой ценности, адаптированных для различных видов животных;
2) повысить перевариваемость крупнорогатого скота и других с/х животных.