ТЕРМОДИФФУЗИОННЫЕ ПОКРЫТИЯ ДЕТАЛЕЙ, РАБОТАЮЩИХ В УСЛОВИЯХ ГИДРООБРАЗИВНОГО ИЗНАШИВАНИЯ
ТЕРМОДИФФУЗИОННЫЕ ПОКРЫТИЯ ДЕТАЛЕЙ, РАБОТАЮЩИХ В УСЛОВИЯХ ГИДРООБРАЗИВНОГО ИЗНАШИВАНИЯ
Научная статья
Александров В.А.1, *, Кудряшов Б.А.2
1 ORCID: 0000-0002-8105-1111,
1, 2 Московский автомобильно-дорожный государственный технический университет
* Корреспондирующий автор (met.madi[at]mail.ru)
Аннотация
Приведены результаты стендовых испытаний, рабочих колёс и статоров центробежных насосов, обработанных химико-термическим методом (ХТО), в условиях гидроабразивного изнашивания. Покрытие значительно повышает стойкость поверхности к гидроабразивному изнашиванию. В ходе эксперимента было установлено снижение износа (определенного массовым методом) в 1,7—2,3 раз.
Ключевые слова: азотирование, трение, гидроабразивное изнашивание, коррозионная стойкость.
THERMAL DIFFUSION COATINGS OF DETAILS WORKING UNDER CONDITIONS OF HYDROABRASIVE WEAR
Research article
Aleksandrov V.A.1, *, Kudryashov B.A.2
1, ORCID: 0000-0002-8105-1111,
1, 2 Moscow automobile-road state technical university (MADI)
* Corresponding author (met.madi[at]mail.ru)
Abstract
The results of bench tests, impellers, and stators of centrifugal pumps, processed by chemical-thermal method (HTO), under conditions of hydroabrasive wear are presented in this work. The coating significantly increases the resistance of the surface to hydroabrasive wear. In the course of the experiment, a decrease in wear (determined by a mass method) of 1.7–2.3 times was established.
Keywords: nitriding, friction, hydroabrasive wear, corrosion resistance.
Введение
Среди деталей гидромашин наибольшему эрозионному износу подвергаются детали насосов (рис. 1.) для транспортировки взвешенных веществ. Они применяются в гидротехническом и транспортном строительстве, в сельском хозяйстве, в металлургической, горнорудной, угольной, химической, пищевой, бумажной, деревообрабатывающей промышленности и в ряде других отраслей.
Несмотря на широкое применение этих гидромашин, стоимость транспортировки единицы объема гидроабразивных веществ еще довольно высока. Это объясняется, главным образом, тем, что рабочие органы насосов изготовляются из материалов, имеющих низкую эрозионную прочность, вследствие чего они быстро разрушаются и выходят из строя. Ремонт и замена их вызывают простой оборудования и требуют больших затрат на материалы, монтаж и обслуживание.
Рис. 1 – Внешний вид статора насоса (а) и рабочее колесо насоса (б)
Гидроэрозии подвергается проточная часть колеса и отвода, наружные поверхности дисков колес, примыкающие к ним поверхности крышек или корпуса и щелевые уплотнения, расположенные на всасывающей стороне насоса.
Детали насосов, перекачивающих абразивные жидкости, в результате эрозионного износа выходят из строя после нескольких месяцев эксплуатации. Применение некоторых нержавеющих сталей для изготовления деталей проточной части насосов несколько увеличивает срок их службы, однако эрозионный износ деталей все еще остается значительным.
В настоящее время ведется изыскание эрозионно-стойких материалов и таких форм проточной части колеса и отвода, при которых износ был бы наименьшим. Практика эксплуатации гидромашин показала, что конструктивные методы борьбы с эрозионным износом не всегда дают положительные результаты и являются только одним из путей, увеличения срока службы деталей этих машин. В данном случае больший эффект получается от рационального выбора конструкционного материала или применения эффективного способа упрочнения рабочей поверхности детали. Поэтому разработка технологий нанесения эрозионных покрытий является наиболее актуальной.
Результаты исследований и их обсуждение
Упрочнению подвергали изделия (рис.1) проточных частей погружных насосов выполненных из серого чугуна марки СЧ-28-48.
Разрушение деталей проточных частей погружных насосов (рис.2) наблюдается и при незначительной загрязненности воды. Следовательно, в рабочих органах насосных ступеней погружных центробежных насосов эрозия металла вызывается, как абразивным фактором, так и явлением кавитации. В загрязненном потоке кавитирующее действие воды может усиливаться за счет способности твердых частиц (при большом их удельном весе) разрывать жидкость.
Рис. 2 – Наличие питинговой коррозии на поверхности не обработанных изделий в процессе испытаний
Исследования показывают, что в результате различного удельного веса воды и твердых частиц имеется различие в скоростях их движения. Это приводит к тому, что перед каждой частицей, движущейся в потоке, возникают вихри. Образование таких вихрей обусловлено обтеканием взвешенных частиц потоком воды. Отставание частиц от жидкости будет тем больше, чем они крупнее и тяжелее. Разная скорость движения частиц приводит к непрерывному хаотическому их соударению, что способствует увеличению нестационарности потока и образованию кавитационных пузырьков. Откачиваемая жидкость всегда содержит во взвешенном состоянии некоторое количество твердых частиц. Поэтому ударное воздействие потока одновременно сопровождается ударами и трением твердых частиц о поверхность детали, создавая условия для выламывания кусочков металла.
Для деталей насосов и других подобного типа гидромашин наибольшее распространение имеет разрушение металла вследствие абразивного действия движущихся в потоке частиц. Однако при больших скоростях сама жидкость оказывает на металл сильное разрушающее действие вследствие развития в потоке кавитации.
Серый чугун (СЧ 28-48) при эрозионных испытаниях не проявляет явно выраженного хрупкого разрушения. Его металлическая основа разрушается при эрозионном воздействии, так же как и углеродная сталь. Однако серый чугун, имеет графитовые включения, разрушается быстрее, чем углеродная сталь. Очевидно, графитовые включения действуют как очаги разрушения (надрезы), вокруг которых концентрируются напряжения, вследствие чего процесс разрушения усиливается.
Кафедра ТКМ МАДИ занимается разработкой покрытий с заданными свойствами, наносимых на поверхности деталей, выполненных из сталей и чугунов.
Во многих практически важных случаях оказывается достаточным надежно защитить лишь внешнюю поверхность деталей, поэтому в промышленности широко применяется защита поверхностного слоя деталей износостойкими и коррозионно-устойчивыми покрытиями. За последние годы все большее внимание привлекают диффузионные защитные покрытия, наносимые на сталь и другие материалы с целью предотвращения коррозии.
Рис. 3 – Изделия после нанесения диффузионных покрытий
Диффузионные покрытия обладают существенным преимуществом по сравнению с другими видами покрытий, прежде всего потому, что прочность связи их с основным металлом в результате проникновения наносимого вещества в кристаллическую решетку защищаемого материала, значительно превышает прочность связи других видов покрытий. Кроме того, постепенное падение концентрации наносимого вещества по глубине покрытия создает менее резкое изменение свойств, при переходе от покрываемого металла к внешней поверхности диффузионного слоя. На рисунке 3 показаны изделия с нанесённым диффузионным покрытием.
При образовании диффузионных слоев наблюдается проникновение наносимого вещества в глубину покрываемого металла и тем большее, чем выше температура и длительность процесса диффузии. В поверхностных слоях покрываемого металла наблюдается при этом образование новых фаз — химических соединений или твердых растворов.
В случае образования в поверхностных слоях металла химических соединений атомы металла растворителя и наносимого вещества сочетаются в строго определенных количественных соотношениях, и состав возникшей новой фазы может быть выражен той или иной химической формулой. Наиболее часто, однако, при нанесении диффузионных покрытий в поверхностном слое наблюдается образование твердых растворов.
Для проверки стойкости поверхностей, имеющих покрытия, к гидроабразивному изнашиванию была создана экспериментальная установка, в которой поверхности испытываемых деталей подвергаются гидроабразивному воздействию потока воды с включениями твердых абразивных частиц песка.
Рис. 4 – Структурная схема установки для испытания при гидроабразивном износе
Схема установки показана на рисунке 4. Установка представляет собой замкнутый трубопровод, по которому помпой (1) перекачивается пульпа (вода с включениями частиц песка и мелкого гравия). Бак (2) служит для хранения пульпы. Мерный бачёк (3) служит для определения скорости движения пульпы по трубопроводу. Манометром (5) контролируется давление в трубопроводе перед испытательным участком.
Рис. 5 – Обработанные детали с вырезанными из них образцами после испытаний
В трубу врезан испытательный участок 4, в котором устанавливаются детали-образцы из испытываемых материалов. Образцы (рис. 5.) при работе установки испытывают в условия гидроабразивного нагружения, близкие к тем, что испытывают рабочие колеса насосов при перекачке жидкости с включениями твердых частиц.
Детали-образцы представляют собой вырезанные части рабочие колеса и статора насоса. Изготовленные из серого чугуна марки СЧ 28-48, ротор и статор насоса (рис. 1), подвергали диффузионной металлизации по следующим режимам, представленным в таблице 1.
Таблица 1 – Технологические режимы металлизации деталей насоса
Вид обработки | Температура Насыщения, Co | Время, часы | Глубина Покрытия, мм | Твёрдость, HV | Группа хрупкости |
Алитирование | 650…850 | 12 | 0,9…1,0 | 350…380 | 1 |
Титанирование | 1050 | 10 | 0,6…0,7 | 250…280 | 1 |
Силицирование | 1080 | 11 | 0,5…0,6 | 300 | 3 |
Хромирование | 1100 | 8 | 0,25…0,3 | 180…230 | 1 |
После металлизации детали обезжиривали и подвергали нитроцементации либо азотированию с применением каталитических плёнок.
В результате такой обработки твёрдость диффузионных слоёв резко возросла (Таблица 2).
Таблица 2 – Механические характеристики модифицированных деталей
Вид обработки | Глубина Покрытия, мм | Твёрдость, HV | Группа хрупкости |
Алитирование + азотирование | 0,65 | 1200 | 2 |
Титанирование + азотирование | 0,58 | 1650 | 1 |
Силицирование + азотирование | 0,63 | 950 | 2 |
Хромирование + азотирование | 0,6 | 950…1000 | 1 |
Хромирование + нитроцементация | 0,35 | 1000…1050 | 1 |
Рис. 6 – Свойства поверхностных слоёв после металлизации
Зависимости изменения твёрдости поверхности, толщины покрытия и хрупкости от типа общей термической обработки представлены на рисунке 7.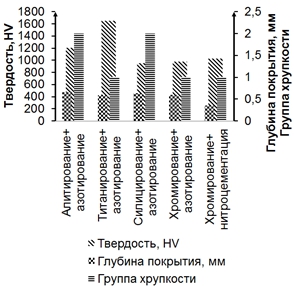
Рис. 7 – Свойства поверхностных слоёв от типа общей термической обработки
Одно из обработанных рабочих колес, поверхность которого была модифицирована алюминием, изготовили шлиф. На рис. 5 показана структура этого покрытия. Поверхностный слой имеет однородную структуру на всю глубину.
Рис. 8 – Структура алитированного покрытия на сером чугуне СЧ-28-48
На первом этапе было произведено испытание вырезанных частей рабочих колёс. Колёса испытывали в пульпе, состоящей из, крупных частиц (3…17 мм) горной породы (аргиллит) при их концентрации 16,6 г/л. Скорость потока пульпы 5 м/сек. Время испытания 4 часа. Одновременно испытывали два колеса с диффузионными покрытиями и один эталонный. Износ определяли взвешиванием деталей до и после испытания с точностью до 0,001г. Результаты испытаний приведены на рисунке 9.
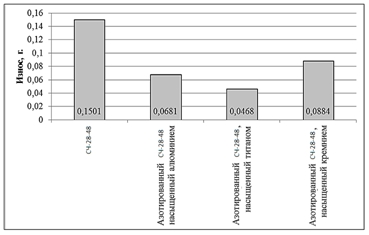
Рис. 9 – Зависимость стойкости рабочего колеса от типа химико-термической обработки
На втором этапе испытаний испытательный участок 4 (рис. 4) был заменен устройством, показанным на рис. 10.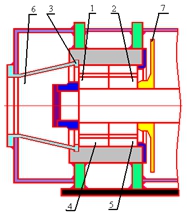
Рис. 10 – Стенд для испытаний деталей центробежного насоса
Устройство представляет собой участок водопроточного тракта установки, в котором установлены втулки (1 и 2), внутренние поверхности которых при испытании на установке подвергаются гидроабразивному изнашиванию. Втулки-образцы при работе установки испытывают условия гидроабразивного нагружения, близкие к тем, что испытывают элементы гидравлических линий, а также корпусные детали насосов при перекачке жидкости с включениями твердых частиц.
Втулки испытывали пульпой, в состав которой входили частицы песка (72%) и породы (28%) одинаковой дисперсности (0,25…1,0 мм). Концентрация твёрдых частиц в пульпе 83 г/литр. Время испытаний 8 часов. Скорость потока пульпы 12,5 м/сек. Результаты испытаний образцов-втулок приведены на рисунке 11.
Рис. 11 – Зависимость стойкости втулок статора от типа химико-термической обработки
По результатам испытаний установлено, что металлизированные термодиффузионные покрытия значительно повышают стойкость материалов к гидроабразивному изнашиванию. Также данные покрытия обеспечивают высокую коррозионную стойкость и значительное снижение образующихся отложений. Повышение коррозионной стойкости и снижение отложений может быть объяснено тем, что комбинированные термодиффузионные покрытия снижают свободную поверхностную энергию. Последующее азотирование проникало на глубину до 0,5 мм, создавая слой, поверхность которого обладала нормальным, присущим азотированной стали внешним видом и твердостью в пределах 1000…1150HV. Хрупкость поверхности соответствовала I, а в худшем случае— III группе распространенной шкалы хрупкости.
Спектральное исследование покрытия (рис. 8), показало структуру, свойственную азотированным слоям, и состояло из смеси ε и -γ'-фаз у поверхности, далее — браунит, а затем отдельные иглы нитридов, переходящие в сердцевину образцов. При этом отчетливо отмечался слой, насыщенный алюминием.
В алитированном. слое обнаруживаются наиболее благоприятные результаты. В процессе азотирования диффузия алюминия медленно продолжается вглубь и перераспределяет его концентрацию в слое, несколько уменьшая перенасыщенность периферийной зоны и обеспечивая легирование почти на всю глубину азотирования.
Подкорковый слой, обнаруживающий иглы нитридов, отличается также повышенной твердостью порядка 255…260HV, вдвое больше твердости сердцевины. Этот слой служит опорой для корки модифицированного покрытия и обеспечивает постепенный переход к сердцевине.
Результаты проведенных исследований позволяют сделать вывод о возможности азотировании обыкновенных серых чугунов при условии их предварительного поверхностного легирования (алитирования, титанирования с последующим азотированием). Получаемая при этом твердость поверхности не уступает азотированным нитраллоям и в худшем случае все же, превышает твердость стального цементированного закаленного слоя. Некоторое усложнение процесса не умаляет, его экономического эффекта, так как при этом отпадает надобность в применении дорого стоящих сплавов, для изготовления деталей насосов.
Выводы
- Комбинированные термодиффузионные покрытия обеспечивают повышение твердости обработанной поверхности до 1000—1700 HV при приемлемой хрупкости образовавшегося покрытия.
- Покрытие значительно повышает стойкость поверхности к гидроабразивному изнашиванию. В ходе эксперимента было установлено снижение износа (определенного массовым методом) в 1,7—2,3 раз.
- Покрытия обеспечивают значительное повышение коррозионной стойкости поверхности.
Конфликт интересов Не указан. | Conflict of Interest None declared. |
Список литературы / References
- Александров В.А.Изучение влияния кавитационной эрозии на деформацию и разрушение изделий из стали / В. А. Александров, Д. С. Фатюхин// Деформация и разрушение материалов 2012. №10. С. 38-40.
- Петрова Л. Г. Интенсификация процесса азотирования конструкционной низкоуглеродистой стали путём формирования каталитической плёнки оксида меди / Л. Г. Петрова, В. А. Александров, А. Ю. Малахов и др. // Упрочняющие технологии и покрытия, №3 (123), 2015, С. 37-44.
- Александров В. А. Способ упрочнения поверхностного слоя стальных деталей / В. А. Александров, В. Ф. Казанцев, Р. И. Никметзянов //Патент на изобретение RUS №2558020 C1, зарегистрирован 27.07.2015.
- Александров В. А. Азотирование деталей гибридного автомобиля через наноплёнки окислов металлов, обладающих полупроводниковыми свойствами / В. А. Александров, А. Ю. Иванов, А. В. Степанов // Наукоемкие технологии в машиностроении. №10(52), 2015, с. 6-10.
- Приходько В. М. Влияние ультразвуковой кавитации, на состояние поверхностного слоя азотированной стали / В. М. Приходько, В. А. Александров, Д. С. Фатюхин и др. // Металловедение и термическая обработка металлов. № 5(719). 2015г. С. 55-59.
- Петрова Л.Г. Регулирование строения диффузионного слоя в углеродистых сталях при азотировании с предварительным нанесением каталитических плёнок оксида меди / Л. Г. Петрова, В. А. Александров, А. Ю. Малахов //Металловедение и термическая обработка металлов. 2017. № 3 (741). С. 48-53.
- Александров В. А. Комбинированный технологический способ ХТО для поверхностного упрочнения сталей / В. А. Александров // Металловедение и термическая обработка металлов. 2010. №5. С. 27-31.
- Александров В. А. Перспективы развития химико-термической обработки сталей: теория – эксперимент – технологии / В. А. Александров, С. И. Барабанов // М.: МАДИ, 2011. С.
- Александров В. А. Получение многослойных комбинированных покрытий на поверхности стальных изделий для повышения эксплуатационных характеристик / В. А. Александров // Упрочняющие технологии и покрытия 2014. №12, С. 13-19.
- Петрова Л. Г. Повышение коррозионной стойкости стальных заглушек на двигателях способами комбинированной металлизации алюминием и титаном / Л. Г. Петрова, В. А. Александров, П. Е. Демин // Упрочняющие технологии и покрытия 2013. №9 (105). С. 26-23.
- Petrova L.G. Improvement of operation lifetime of machine parts with composite coatings in wear conditions / L. G. Petrova, V.A. Aleksandrov, A.Yu. Malakhov and others // Journal of Mechanical Engineering and Technology (IJMET) Vol 8, Issue 10, October 2017, pp. 855-861, Article ID: IJMET_08_10_092
- Petrova L.G. Control of the Structure of Diffusion Layer in Carbon Steels Under Nitriding with Preliminary Deposition of Copper Oxide Catalytic Films / L. G. Petrova, V. A. Aleksandrov, A. Y. Malakhov // Metal Science and Heat Treatment, 2017
Список литературы на английском языке / References in English
- Aleksandrov V.A. Izuchenie vliyaniya kavitacionnoj ehrozii na deformaciyu i razrushenie izdelij iz stali [The study of the effect of cavitation erosion on the deformation and destruction of steel] / V. A. Aleksandrov, D. S. Fatyuhin// Deformaciya i razrushenie materialov [Deformation and destruction of materials] 2012. №10. S. 38-40. [in Russian]
- Petrova L. G. Intensifikaciya processa azotirovaniya konstrukcionnoj nizkouglerodistoj stali putyom formirovaniya kataliticheskoj plyonki oksida medi [Intensification of the nitriding process of structural low-carbon steel by forming a catalytic film of copper oxide ] / L. G. Petrova, V. A. Aleksandrov, A. YU. Malahov i dr. // Uprochnyayushchie tekhnologii i pokrytiya [Strengthening technologies and coatings], №3 (123), 2015, S. 37-44. [in Russian]
- Aleksandrov V. A. Sposob uprochneniya poverhnostnogo sloya stal'nyh detalej [Method for hardening of the surface layer of steel parts] / V. A. Aleksandrov, V. F. Kazancev, R. I. Nikmetzyanov //Patent na izobretenie [Patent for invention] RUS №2558020 C1, registered on 27.07.2015. [in Russian]
- Aleksandrov V. A. Azotirovanie detalej gibridnogo avtomobilya cherez nanoplyonki okislov metallov, obladayushchih poluprovodnikovymi svojstvami [Nitriding of parts of a hybrid car through nanofilms of metal oxides possessing semiconductor properties ] / V. A. Aleksandrov, A. YU. Ivanov, A. V. Stepanov // Naukoemkie tekhnologii v mashinostroenii [High technology in engineering]. №10(52), 2015, s. 6-10. [in Russian]
- Prihod'ko V. M. Vliyanie ul'trazvukovoj kavitacii, na sostoyanie poverhnostnogo sloya azotirovannoj stali [Influence of ultrasonic cavitation on the state of the surface layer of nitrided steel ] / V. M. Prihod'ko, V. A. Aleksandrov, D. S. Fatyuhin i dr. // Metallovedenie i termicheskaya obrabotka metallov [Metallurgy and thermal treatment of metals]. № 5(719). 2015g. S. 55-59. [in Russian]
- Petrova L.G. Regulirovanie stroeniya diffuzionnogo sloya v uglerodistyh stalyah pri azotirovanii s predvaritel'nym naneseniem kataliticheskih plyonok oksida medi [Regulation of the structure of the diffusion layer in carbon steels during nitriding with preliminary deposition of catalytic films of copper oxide ] / L. G. Petrova, V. A. Aleksandrov, A. YU. Malahov //Metallovedenie i termicheskaya obrabotka metallov [Metal Science and Heat Treatment of Metals]. 2017. № 3 (741). S. 48-53. [in Russian]
- Aleksandrov V. A. Kombinirovannyj tekhnologicheskij sposob HTO dlya poverhnostnogo uprochneniya stalej [Combined technological method HTO for surface hardening of steels ] / V. A. Aleksandrov // Metallovedenie i termicheskaya obrabotka metallov [Metallurgy and heat treatment of metals]. 2010. №5. S. 27-31. [in Russian]
- Aleksandrov V. A. Perspektivy razvitiya himiko-termicheskoj obrabotki stalej: teoriya – ehksperiment – tekhnologii [Perspective Prospects for the development of chemical heat treatment of steels: theory - experiment - technology] / V. A. Aleksandrov, S. I. Barabanov // M.: MADI, 2011. S. [in Russian]
- Aleksandrov V. A. Poluchenie mnogoslojnyh kombinirovannyh pokrytij na poverhnosti stal'nyh izdelij dlya povysheniya ehkspluatacionnyh harakteristik [multilayered composite coatings on the surface of steel products to improve performance] / V. A. Aleksandrov // Uprochnyayushchie tekhnologii i pokrytiya [Strengthening technologies and coatings ]. 2014. №12, S. 13-19. [in Russian]
- Petrova L. G. Povyshenie korrozionnoj stojkosti stal'nyh zaglushek na dvigatelyah sposobami kombinirovannoj metallizacii alyuminiem i titanom [Increase of corrosion resistance of steel plugs on engines by means of combined metallization with aluminum and titanium ] / L. G. Petrova, V. A. Aleksandrov, P. E. Demin // Uprochnyayushchie tekhnologii i pokrytiya [Strengthening technologies and coatings]. 2013. №9 (105). S. 26-23.
- G. Petrova, V.A. Aleksandrov, A.Yu. Malakhov, V.M. Zinchenko, V.I. Karagodin /Improvement of operation lifetime of machine parts with composite coatings in wear conditions// Journal of Mechanical Engineering and Technology (IJMET) Volume 8, Issue 10, October 2017, pp. 855-861, Article ID: IJMET_08_10_092
- Petrova, L.G. Control of the Structure of Diffusion Layer in Carbon Steels Under Nitriding with Preliminary Deposition of Copper Oxide Catalytic Films / L.G. Petrova, V.A. Aleksandrov, A.Y. Malakhov // Metal Science and Heat Treatment, 2017