PRODUCTION TECHNOLOGY COMPOSITE PIPES BY WINDING FOR OIL AND GAS INDUSTRY
Николаев A.К. 1, Лутов В.А. 2
1Доктор технических наук, 2Магистр, Санкт- Петербургский Национальный минерально-сырьевой университет «Горный»
ТЕХНОЛОГИЯ ПРОИЗВОДСТВА КОМПОЗИЦИОННЫХ ТРУБ МЕТОДОМ НАМОТКИ ДЛЯ НЕФТЕГАЗОВОЙ ОТРАСЛИ
Аннотация
Рассмотрены возможные технологии производства композитных труб используемых при строительстве и эксплуатации промысловых трубопроводов. Предложена усовершенствованная технология изготовления композитных труб методом непрерывной намотки.
Ключевые слова: промысловый трубопровод, коррозия, композитный материал, намотка, изготовление, композитная труба.
Nikolaev A.K. 1, Lutov V.A. 2
1Doctor of Technical Sciences, 2Master student. Saint Petersburg National Mineral Resources University (Mining University)
PRODUCTION TECHNOLOGY COMPOSITE PIPES BY WINDING FOR OIL AND GAS INDUSTRY
Abstract Possible manufacturing techniques of composite pipes used in the construction and operation of the flowlines. An improved technology for manufacturing composite pipes by continuous winding. Keywords: flowline, corrosion, composite, winding, manufacturing, composite tube.В практике эксплуатации промысловых трубопроводов важной проблемой является выход их из строя в результате коррозии. Средний срок службы промысловых трубопроводов изменяется от нескольких месяцев до 15 лет. Коррозионные процессы приводят к снижению механической прочности труб, и как следствие - к отказам трубопроводов. В результате отказов происходит загрязнение окружающей среды, снижение добычи нефти, повышение затрат на капитальный ремонт трубопроводов и на природоохранные мероприятия. Промысловые трубопроводы, построенные из углеродистой и низколегированной стали, подвержены, в основном, коррозии по нижней образующей труб. При этом происходит локальное утонение стенки трубы, и в некоторых местах появляются коррозионные отверстия - свищи. В то же время толщина стенки труб по остальному периметру практически не уменьшается[1]. Данные трубопроводы имеют еще следующие недостатки. Высокая стоимость монтажных работ и значительные тепловые потери, что приводит к неумеренным энергозатратам. Также большой вес стальных труб не позволяет доставлять в труднодоступные места. В России энергодобывающие предприятия располагаются в основном на севере.
В последние десятилетия широкое распространение получили изделия из волокнистых полимерных композиционных материалов, состоящих из отдельных волокон и связывающей их термопластичной или термореактивной матрицы. В зависимости от целей и задач, волокно может быть стеклянным, базальтовым, углеродным; смолы – эпоксидными, полиэфирными, фенольными. Эти изделия получили широкое применение в нефтяной и газовой индустрии. Достаточно эффективно использовать достоинства эти материалов могут быть использованы при создании тонкостенных оболочечных конструкций и, в частности, труб, полученных способом непрерывной намотки. В настоящие время в мире производиться более 200 тысяч тонн труб из волокнистых ПКТ, в основном из стеклопластика.
Композитные материалы в первую очередь заменяют традиционные стальные трубы, благодаря скорости и легкости установки изделий из них, более легкому весу, стойкости к коррозии, стойкости к криогенным температурам, разломам и разрывам. Стоимость их также конкурентоспособна по сравнению со сталью.
В процессе роста объемов производства изделий из композитных материалов все более важными становиться прогнозирования их несущей способности. Решение этих задач тесно связано с разработкой математических моделей, позволяющих учесть и оценить влияние наиболее значимых конструктивных и технологических факторов на напряженно-деформированное состояние и прочность конструкций. Теоретические сложности нахождению оптимальной траектории и закона движения раскладывающего механизма намотки привлекают к ним многих известных ученых [1 - 6].
Одним из недостатков композиционных материалов является до сих пор их высокая стоимость. При моделировании процесса изготовления конструкций из композитных материалов методом намотки лент, которые укладываются на поверхность технологической оправки, необходимо обеспечить высокую точность соответствующих моделей оболочек не только для достижения желаемых эксплуатационных свойств конструкций, но и для экономии материалов.
Технология формирования изделий методом намотки из композиционных материалов, имеет возможность обеспечение высокой степени автоматизации технологического процесса производства композитных труб.
Для достижения задаваемой ориентации волокнистого наполнителя в стенке изделия является одной из сложнейших задач. В этом плане метод намотки открывает широкие возможности. Выбор оптимальных углов намотки в сочетании с требуемым технологическим натяжением армирующего материала позволяет придать материалу изделий свойства, наиболее полно отвечающие характеру внешних нагрузок.
Наиболее широкое применение армирующего материала получил стеклоровинг [7]. Специальные механизмы, которые перемещаются со скоростью, синхронизированной с вращением оправки, контролируют угол намотки и расположение армирующего материала. Угол намотки может изменяться от 15º до 90º, относительно оси. Отношение радиальной и осевой прочности изделия зависят от скорости вращения оправки и перемещения лентораскладчика. Оптимальное соотношение радиальной и осевой прочности достигается при величине угла намотки α = 54,75° [8].
При изготовления труб периодическим способом формирование поверхности осуществляется с прерывистым перемещением ее по оправке и возвратно-поступательным перемещением лентораскладчика, что во многих случаях приводит к неравномерности структуры получаемой трубы, деформации готовой трубы при ее съеме с оправки и длительности изготовления трубы. При создании композиционных труб путем наматывания на оправку одной ленты в трубах возникают изгибающие моменты, которые вызывают деформации текстильных армирующих структур нижележащих слоев. Многослойная композитная труба характеризуется неравномерностью ее структуры по длине.
На рисунке 1 предлагаемый в работе способ изготовления трубы на который получен патент РФ [№ RU 2425753 С2], состоит в непрерывном наматывании образующих трубу армирующих лент 1 с лентораскладчика 2 на движущуюся оправку 3, представляющую собой систему ременных передач, отводящую изготовленную часть композитной трубы 4 через зону сушки 5. Клей подается в зону формирования трубы через узел нанесения клея на внешнюю и внутреннюю сторону армирующей ленты через перфорированные трубки, которые распыляют клей на ролики. Ролики имеют пористую структуру, что обеспечивает равномерное нанесение клея на поверхность ленты и исключает его разбрызгивание.
Рис.1 - Принципиальная схема изготовления трубы
Задаваемое соотношение скоростей перемещения оправки 3 и лентораскладчика 2 позволяет обеспечить равномерную спиральную намотку лент 1 при непрерывном перемещении трубы 4, а также возможность изменять количество слоев готовой трубы.
На рисунке 2 представленная принципиальная схема изготовление труб. На этой схеме указана создаваемая труба 1 радиуса R, которая перемещается вдоль этой оси со скоростью V. На трубу наматывается армирующая лента 2 с углом подъема φ, с питающей паковки 3, которая вращается с угловой скоростью ω вокруг подвижной оси радиус r. Ось на которой размещена паковка вращается вокруг неподвижной оси x с угловой скоростью Ω.
Предполагая, что образующая питающей паковки перпендикулярна к нитям основы, так как только при этом условии лента будет сматываться с паковки без скольжения по ее поверхности в направлении ее образующих. Указанная схема наматывания ленты приводит к неравенству натяжений нитей ее основы. Это неравенство связано с различием длин свободных участков этих нитей, которые располагаются между поверхностями паковки и трубы. Обозначая длину свободной части нижней нити основы через L(h). Длина свободного участка нити основы, которая расположена на расстоянии h от нижней нити, оказывается больше, чем L0 на величину ΔL=hctgφ, определяется по зависимости


Рис. 2 - Наматывание ленты на трубу кругового сечения
Частицы ленты при навивке на трубу приобретают скорость U, складывающуюся из окружной скорости поверхности трубы, равной RΩ, и из скорости поступательного движения трубы V. Так как эти составляющие скорости U взаимно перпендикулярны, получаем.
Рис. 3 – Макет для производства труб
Данная конструкция предусмотрена возможность изменения внешнего диаметра самоподающейся оправки, который определяет формирующую поверхность, дает возможность изготавливать композитные трубы различных диаметров, что позволяет сокращать затраты на дополнительную оснастку оборудования. Используя одну установку, можно в кратчайшее время перенастроить геометрические параметры формируемой трубы и тем самым расширить ассортимент изготавливаемой продукции.Рис.4 Принципиальная схема конструкции для создания трубы заданной формы
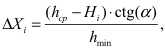
Рис.5 – Схема ременной передачи
Для вычисления изменения длины ленты самоподающейся оправки применяем следующие выражение
Литература
- Айдуганов В.М. Опыт строительства и эксплуатации трубопроводов из металлопластиковых труб / Айдуганов В.М., Волкова Л.И.// Нефтегазовое дело, 2006
- Ефремов, Е. Д. Основы теории наматывания нити на паковку / Е.Д. Ефремов, Б. Д. Ефремов // Легпищепром, 1982. – 144 с.
- Ефремов, Е. Д. О возможности проектирования мотальных механизмов по параметрам намотки / Е. Д. Ефремов // Изв. вузов. Технология текстильной промышленности, № 6, 1962. – С. 78 – 82.
- Матюшев, И. И. Высокоскоростные приемно-намоточные механизмы для химических нитей / И. И. Матюшев, В. А. Климов, Л. С. Мазин // Легпромбытиздат, 1991. –С. 256.
- Башин Г.Б. Расчет деформаций волокон композитных оболочек в процессеих изготовления и эксплотачии// Вестник пермского университета. – 2007.-№7(12)– С.95-100.
- Битюков Ю.И. Численный анализ схемы укладки ленты переменной ширины на технологическую оправку в процессе намотки конструкций из композиционных материалов / Битюков Ю.И., Калинин В.А. //Механика композиционных материалов и конструкций.–2010.–Т.16.-№2.-С. 276-290.
- Интернет-сайт научно-производственной фирмы “ АЛЬТАИР РУСПОЛ ” http://ruspol.spb.ru;
- Интернет-сайт аналитический портал химической промышленности «Новые химические технологии» http://newchemistry.ru/
- Патент на изобретение № RU 2425753 С2 от 10.08.2011. Авторы: Полякова Е.В, Лутов В.А, Майоров А.М, Дятлова П.А, Чайкин В.А. Патентообладатель: Санкт-Петербургский государственный университет технологий и дизайна.
- ГОСТ Р 50443-92. Препреги и премиксы. Термины и определения
References
- V.M. Ayduganov Experience in the construction and operation of pipelines of plastic pipes / Ayduganov V.M. Volkova L.I. .// Oil and Gas Business, 2006
- Efremov 1, E.D. Basic theory of winding yarn into a package / E.D. Efremov, B.D. // Legpischeprom Efremov, 1982. - 144 p.
- Efremov, E.D. differential equation of motion in terms of winding into a package / E.D. Efremov // Math. universities. The technology of the textile industry, № 2, 1960. - S. 86 - 90.
- Efremov, E.D. On the possibility of designing mechanisms for winding the winding / E.D. Efremov // Math. universities. The technology of the textile industry, № 6, 1962. - S. 78 - 82.
- Matyushev, II High-receiving mechanisms for winding filaments / II Matyushev, V.A. Klimov, L.S Mazin // Legprombytizdat, 1991. -C. 256.
- G.B.Bashin Calculation of deformations in the fiber composite shells protsesseih manufacturing and eksplotachi // Bulletin of Perm State University. - 2007.-№7 (12) - S.95-100.
- Bityukov Y.I. Numerical analysis of the scheme laying tape of variable width on technological mandrel during winding composite structures / Bityukov Y.I. Kalinin, V.A. // Mechanics of Composite Materials and konstruktsiy.-2010-T.16.-№2.-C. 276-290. Website of scientific and production company "ALTAIR Ruspoli" http://ruspol.spb.ru;
- Website Analysis Portal of the chemical industry "New chemical technology» http://newchemistry.ru/
- The patent for the invention № RU 2425753 C2 on 10.08.2011. Authors: E.V. Polyakov, V.A. Lutov, Mayorov, A.M., Dyatlov P.A., V.A. Chaykin Patentee: Saint Petersburg State University of Technology and Design.
- GOST 50443-92. Prepregs and premixes. Terms and Definitions