A WAY TO FORMALLY DESIGN THE STRUCTURE OF TECHNOLOGICAL PROCESSES
A WAY TO FORMALLY DESIGN THE STRUCTURE OF TECHNOLOGICAL PROCESSES
Abstract
The problem of automating the design of parts machining processes on metal-cutting machines requires formal tools for technological development. The most important design task is to form a set and sequence that determine the structure of the technological process. The article reviews a formal method for modelling the part of machining process. The basis of the method is an approach based on generating technological bases (sets of bases) and determining the sequence of surface machining. The information basis is a set of dimensional relationships set by the blueprint and technical requirements. The given examples of two variants of modelling the machining process indicate the real possibility of formal design of the technology.
1. Введение
Назначение технологического процесса – получить в результате изготовления заданные функциональные характеристики деталей машин, определяемые двумя факторами: физико-механическими свойствами материала (прочность, твёрдость, износостойкость коррозионная стойкость и др.); геометрическими характеристиками (точность размера, точность формы, точность относительного расположения поверхностей, шероховатость поверхностного слоя) .
В статье рассматриваются вопросы формализации проектирования технологических процессов обработки деталей на металлорежущем оборудовании. Для достижения заданных геометрических свойств решаются две взаимосвязанные задачи. Одна заключается в разработке набора методов формообразования для всего множества поверхностей. Вторая касается вопроса формирования структуры технологического процесса, обеспечивающего заданные пространственные отношения, а именно, взаимное расположение рассматриваемых поверхностей , , .
2. Постановка задачи
Формализация процесса проектирования технологии является одним из важнейших направлений теоретических и практических разработок, в рамках которых большую значимость представляет теория базирования, так как именно базирование влияет на погрешность взаимного расположения поверхностей при обработке в процессе изготовления детали. В нашей стране исследования в области базирования при обработке и сборке были начаты в первой половине ХХ столетия. Основные понятия, определения и положения теории базирования сформулированы в работах А. П. Соколовского, А.А. Маталина, А. И. Каширина, В.М. Кована, Б.С. Балакшина, А.Б. Яхина. Значительный вклад в развитие теории базирования, размерных цепей, способов проектирования и оптимизации проектных решений внесли отечественные ученые В.И. Аверченков, А.М. Дальский, И.М. Колесов, Б.С. Матвеев, В.В. Мордвинов, В.Г. Старостин, А. Г. Суслов, В.Д. Цветков, Ю.М. Соломенцев, Б.М. Базров и др.
Как известно, технологический процесс дискретного производства включает в себя ряд разноплановых технологических процедур, т.е. элементов, которые выполняются в определенном порядке , , . В качестве базового элемента технологического процесса в работе рассматривается регламентируемая ГОСТ 3.1109-82 часть технологической операции, выполняемая при неизменном закреплении обрабатываемых заготовок или собираемой сборочной единицы, называемая установом . Следовательно, структура технологического процесса есть набор и последовательность выполнения этих установов .
Целью статьи является реализация формального подхода проектирования структуры технологического процесса, поиск всех возможных вариантов установов непротиворечащих условиям существования конкретной геометрической конфигурации детали. Для исследования в качестве базы использована схема моделирования процесса обработки деталей на станках, описанная в работах , .
Теоретическим базисом рассматриваемого метода проектирования технологии обработки деталей является геометрия неидеальных объектов, использующая шестимерное пространство с тремя линейными и тремя угловыми координатами
Исходным постулатом в ходе моделирования процесса обработки является прямое выдерживание заданных на чертеже размерных связей, определяющих их взаимное расположение. При этом в качестве баз для получения рассматриваемой поверхности могут быть использованы реальные поверхности детали, позволяющие однозначно ориентировать формообразующие движения для её обработки. Процесс проектирования комплектов баз и последовательности их смены построен на использовании алгоритма направленного поиска реально существующих сторон детали, которые можно применить в качестве баз для ориентации детали при обработке поверхностей , , , . Структура технологического процесса образовывается на основе: определения баз и комплектов баз; установления последовательности смены баз.
В ходе проектирования технологии задано следующее условие порождения поверхности – окончательную обработку каждой из поверхностей детали достаточно выполнить только за один технологический переход. Выбор черновых баз производится исходя из следующих положений:
· количество их может быть не более трёх;
· базы должны быть непосредственно связаны размерной связью с обрабатываемыми поверхностями;
· любую черновую базу можно использовать только один раз;
· совокупности степеней свободы, фиксируемые базами, не могут повторяться.
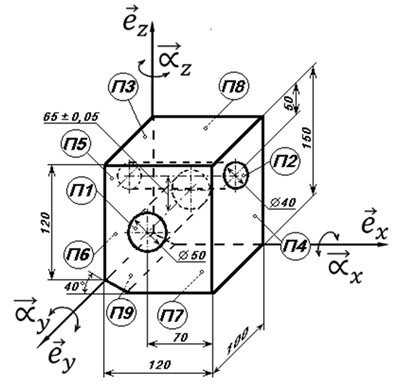
Рисунок 1 - Деталь
Примечание: параллельность отверстия П1 относительно плоскости П4 не более 0,01 мм; параллельность поверхности П4 относительно поверхности П6 не более 0,01 мм; перпендикулярность поверхности П6 относительно поверхности П8 не более 0,01 мм; перпендикулярность поверхности П3 относительно поверхности П5 не более 0,01 мм; перпендикулярность поверхности П3 относительно поверхности П4 не более 0,01 мм; перпендикулярность поверхности П4 относительно поверхности П5 не более 0,01 мм
В рассматриваемом случае в качестве исходной заготовки используется тело в форме прямоугольного параллелепипеда, ограниченного шестью необработанными (черновыми) поверхностями. Для обеспечения связи чистового комплекса с черновым используются три черновые поверхности: Ч6, Ч7 и Ч8. Каждая из них связана размерами с поверхностями П4, П3 и П5 соответственно.
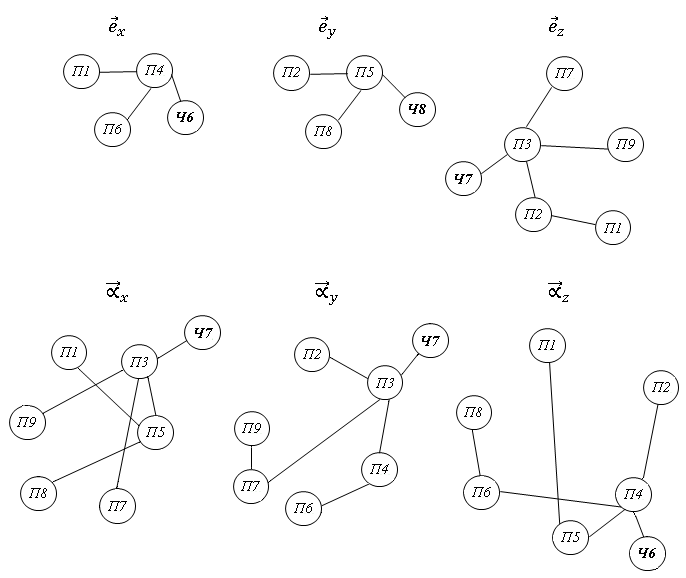
Рисунок 2 - Графы размерных связей для координат e→x,e→y,e→z,∝→x,∝→y,∝→z
Далее представлены два варианта моделирования технологий обработки: первый с последовательным получением поверхностей, второй с параллельным.
Суть последовательной обработки в формировании структуры проектируемого технологического процесса, отражающего последовательное (друг за другом) выявление баз или комплектов баз, используемых для обработки одной (конкретной) поверхности в соответствии с требованиями чертежа
, . При параллельной обработке выявляются комплекты баз, используемые для обработки нескольких поверхностей детали. Работа алгоритма проектирования процесса обработки по обоим вариантам основана на преобразования матрицы смежности.3. Первый вариант моделирования
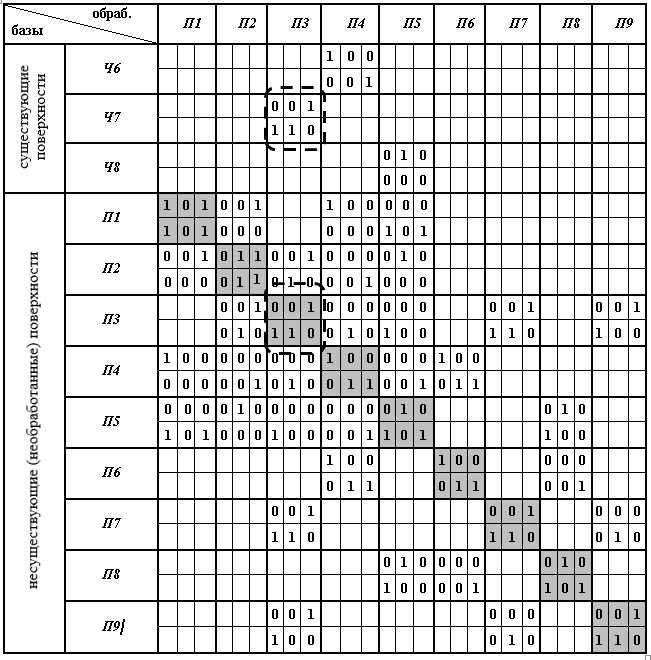
Рисунок 3 - Первый шаг обработки матрицы смежности
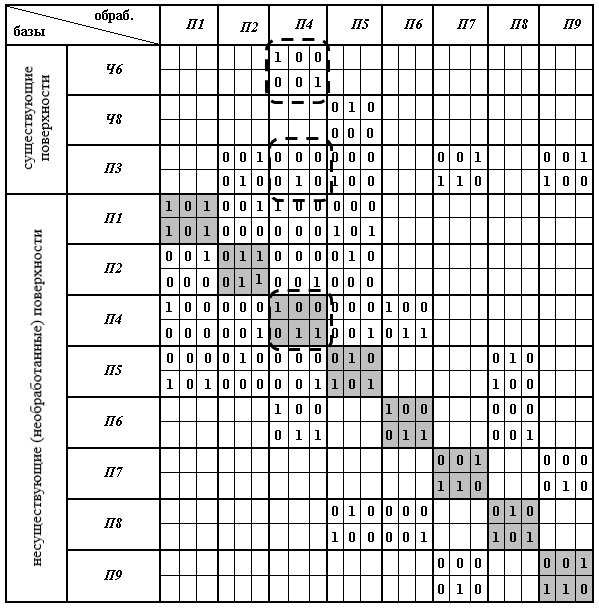
Рисунок 4 - Второй шаг обработки матрицы смежности
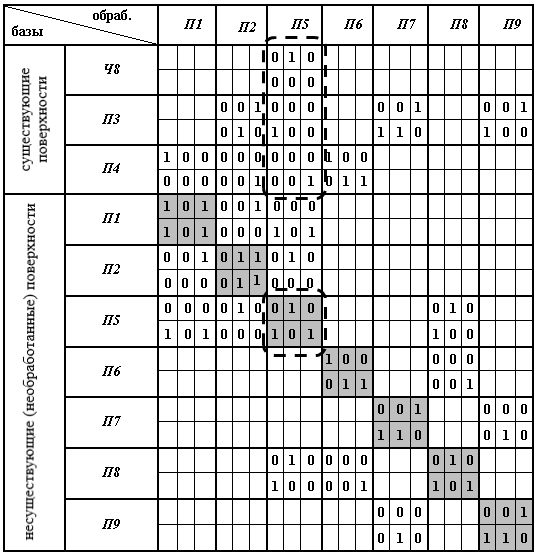
Рисунок 5 - Третий шаг обработки матрицы смежности
Трансформация приводит матрицу в вид, представленный на рисунке 6.

Рисунок 6 - Четвёртый шаг обработки матрицы смежности
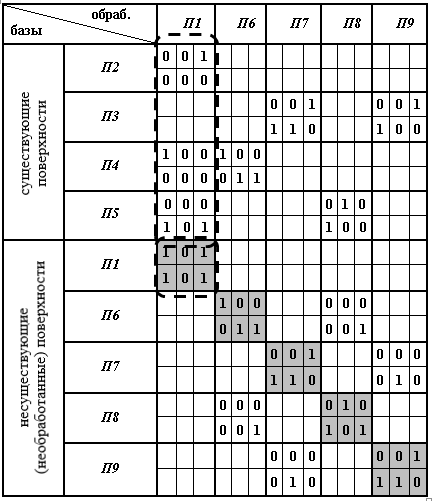
Рисунок 7 - Пятый шаг обработки матрицы смежности
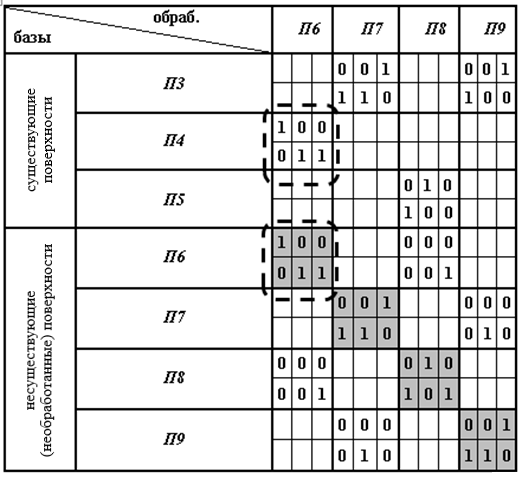
Рисунок 8 - Шестой шаг обработки матрицы смежности
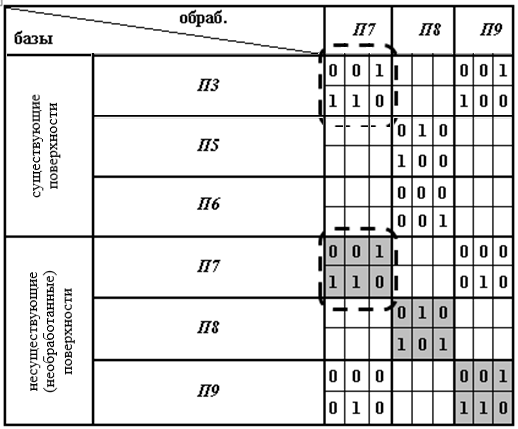
Рисунок 9 - Седьмой шаг обработки матрицы смежности
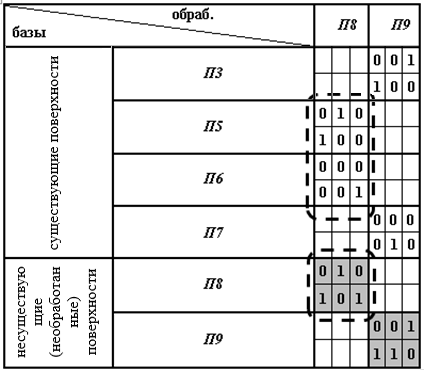
Рисунок 10 - Восьмой шаг обработки матрицы смежности
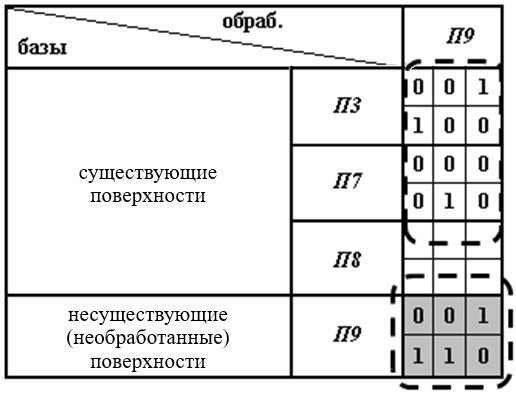
Рисунок 11 - Девятый шаг обработки матрицы смежности
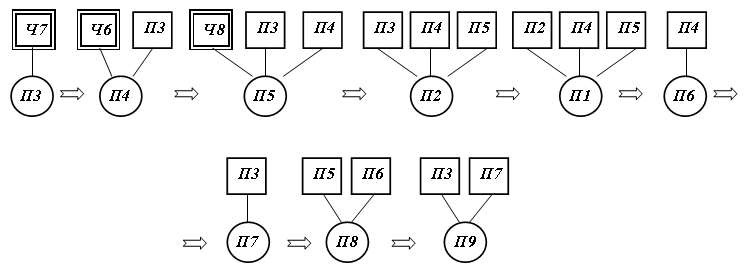
Рисунок 12 - Последовательность обработки поверхностей детали
4. Второй вариант моделирования
При реализации второго способа моделирования технологии обработки используются комплекты баз для получения нескольких поверхностей детали. При анализе матрицы смежности выделенная база или комплект баз проверяются на возможность их использования для ориентации всех возможных поверхностей детали на данном шаге.
Первый шаг анализа матрицы показывает, что база Ч7 может использоваться только для обработки поверхности П3, так как больше не выявлено столбцов, в которых логическая сумма шестиклеточных таблиц базовых поверхностей, полностью «покрывает» соответствующие диагональные шестиклеточные таблицы необработанных поверхностей. Поэтому первый шаг преобразования матрицы полностью соответствует виду, показанному на рисунке 3.
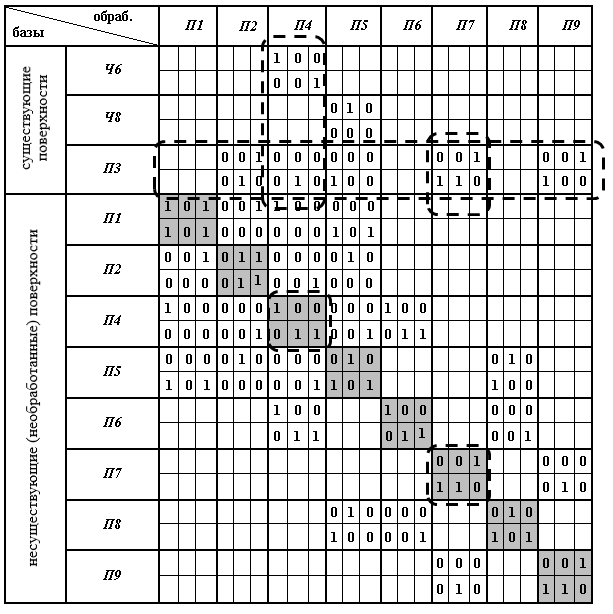
Рисунок 13 - Второй шаг обработки матрицы смежности

Рисунок 14 - Третий шаг обработки матрицы смежности
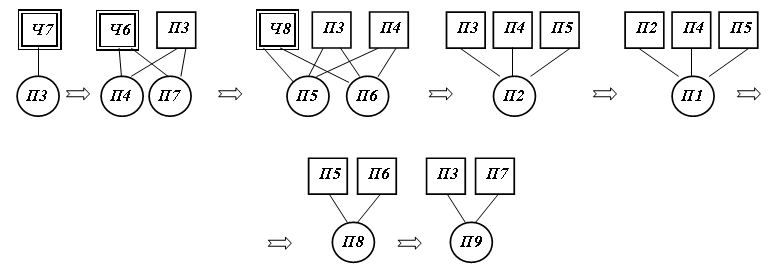
Рисунок 15 - Последовательность обработки поверхностей детали
5. Заключение
В статье наглядно продемонстрирован способ формального проектирования структуры технологического процесса обработки детали резанием. Показана возможность моделирования разного состава технологий для получения геометрической конфигурации. Хотя в дальнейшем, в зависимости от условий производства можно получить и другие варианты структур технологических процессов.
Таким образом, первый и второй подход формального проектирования технологии позволяет сформировать комплекты баз для обработки поверхностей, спланировать последовательность смены баз при обработке, построить последовательность обработки. Используемая методика моделирования даёт возможность представить состав и структуру установов технологического процесса обработки детали.