Increasing the Accuracy of CNC Table-top Working Benches by Using Load-Bearing Reinforcements in Their Frame
Increasing the Accuracy of CNC Table-top Working Benches by Using Load-Bearing Reinforcements in Their Frame
Abstract
The aim of this article is to theoretically substantiate the rationality of application of polymer-granite frames with reinforcing elements in table-top working benches. The article presents all structural solutions used in the developed frame and demonstrates the results of analysis of table-top working bench design on the basis of the developed frame by means of a mathematical model. It is demonstrated that by introduction of stretched reinforcing elements of special form into the cast-in-synthetic frame, increased rigidity and vibration resistance of the table machine tool as a whole is achieved. The proposed solution makes it possible to create table-top working benches of various types having multiply increased stiffness and vibration resistance without any multiplication of manufacturing costs. The application area is metal machining on table-top working benches. It is in the description of this new method, which makes it possible to provide increased accuracy of table-top working benches, that the scientific novelty of the work lies. The specific application of the developed frame in a horizontal milling machine is considered separately.
1. Введение
На данный момент настольные станки наиболее востребованы в условия малых и средних предприятий различной направленности, а также среди частных предпринимателей . Причиной тому служит их неоспоримое преимущество в стоимости, массе и габаритах перед крупными промышленными станками. Однако, имея кратно (или даже на порядок) меньшие массово-габаритные показатели, настольные станки менее жёсткие, намного более уязвимы к вибрациям, неизбежно возникающим в их рабочей зоне при обработке материала.
Таким образом, сами исходные параметры настольных станков предопределяют их относительно низкую точность обработки и, как следствие, значительно сужают спектр их возможного применения. Одна из сфер применения настольных станков с ЧПУ – фрезерная обработка. Для того чтобы повысить жёсткость динамической системы станок-приспособление-инструмент-заготовка, необходимо в первую очередь увеличить жёсткость несущих элементов конструкции станка . Несущими элементами, в частности, являются вертикальные стойки и станина.
В настоящее время в станкостроении известен и широко используется целый ряд композитных материалов на основе полимерных смол, в связи с чем в современной научной литературе по данной теме выделяется несколько наиболее многообещающих новых подходов. Один из таких подходов – использование предварительно созданного напряжённого состояния в полимербетонах для базовых частей станков . Этот подход позволяет не только эффективнее гасить вибрации, но и кратно повысить жёсткость системы. Именно вопросу повышения жёсткости таким путём, в частном случае горизонтально-фрезерного настольного станка, и посвящено исследование.
Так, основываясь на вышесказанном и анализируя источники , , можно сделать вывод, что решение вопросов обеспечения жёсткости и точности является актуальной задачей при создании станков с ЧПУ. В качестве решения этой задачи в источниках , рассмотрены методы обеспечения точности путём применения синтеграна и армирования станины направляющими. Совокупное применение методов минерального литья (синтегран) и армирования станины и является целью выполненного в данной работе исследования.
2. Конструкция разрабатываемой станины, технология её изготовления и теоретическое обоснование технической значимости
Итак, предложен способ достижения жёсткости настольного станка, который состоит во внедрении в его синтеграновую станину закладных элементов особой формы в состоянии предварительного натяга. Конечно, применение в различных конструкциях элементов с предварительным натягом не является инновационным методом повышения жёсткости. Но в нашем случае определяющим для новизны исследования фактором является сочетание состояния и формы армирующих элементов с самим материалом станины.
Форма, размеры закладных элементов станины и материал из которого они изготавливаются, определяются исходя из задач, стоящих перед станком и сил резания, возникающих при его работе. То же самое справедливо и для геометрических параметров самой станины. Так, переходя к частному случаю горизонтально-фрезерного станка, необходимо отметить как общую топологию и геометрию станины и её элементов, так и их конкретные размеры. На рисунке (см. рисунок 1) изображена модель разрабатываемой синтеграновой станины.
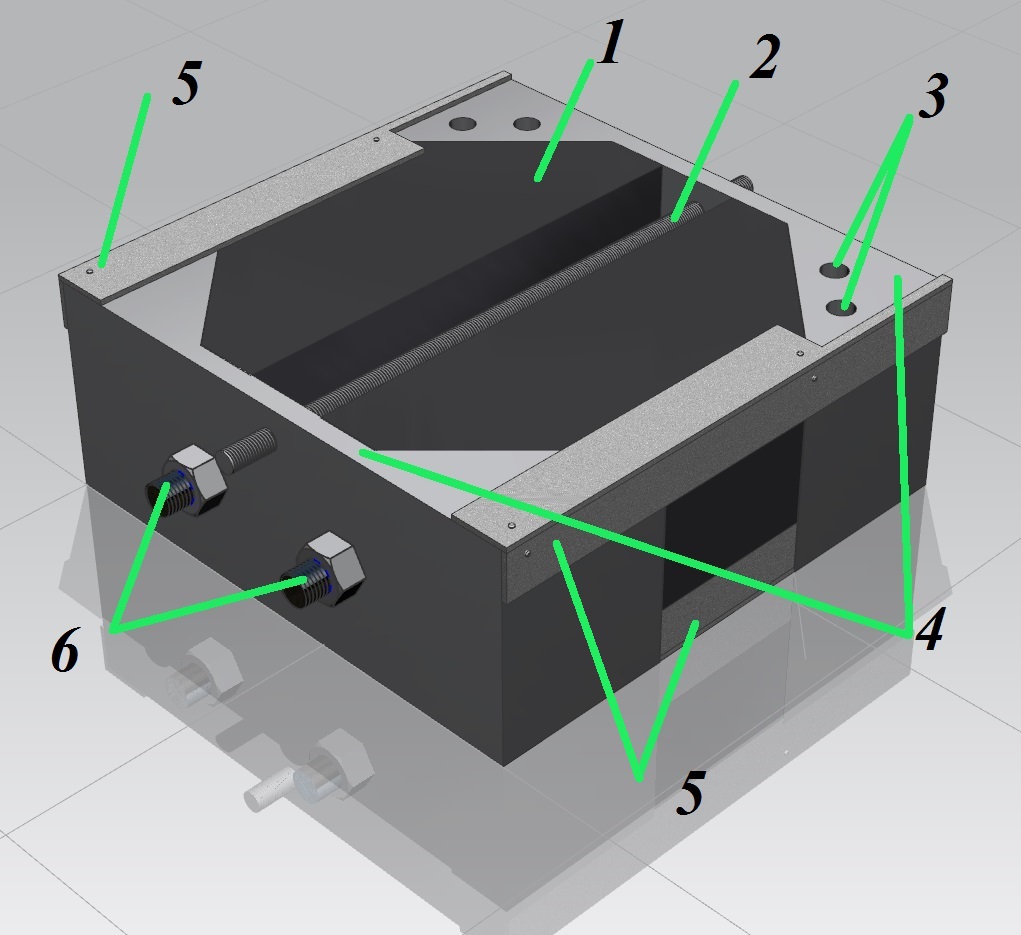
Рисунок 1 - Трёхмерная модель разрабатываемой синтеграновой станины с армирующими элементами:
1 – синтеграновая литая плита; 2 – винт шарико-винтовой пары; 3 – отверстия для крепления стоек к станине; 4 – торцевые стальные пластины; 5 –стальные уголки; 6 – наружная часть армирующих элементов станины
Портальную конструкцию стоек, представляющую собой две литые колонны со стальной пластиной в основании, предполагается соединять со станиной при помощи сквозных отверстий в её заднем торце, которые отмечены цифрой 3 на рисунке 1. Данные отверстия в количестве четырёх штук обладают расширенным диаметром (50мм) в нижней части станины. Это необходимо для обеспечения возможности физического доступа инструменту в отверстия. Доступ инструмента в отверстие нужен для осуществления фиксации стержней с резьбой, являющихся частью стоечной конструкции, в задней торцевой пластине станины при помощи систем контргаек. Гайки в отверстии упираются в ступень сужения диаметра отверстия, обеспечивая жёсткое крепление стоек к станине.
Одной из особенностей предложенной конструкции являются треугольно-призматические колонны на боках торцевых пластин станины. Их наличие придаёт торцам более сложную, нестандартную геометрию, что оправдывается их значительной практической значимостью. Во-первых, благодаря наличию этих треугольных призм проще осуществлять параллельную ориентацию торцевых пластин, что является необходимым этапом при изготовлении предложенной станины. Во-вторых, поскольку в горизонтальной плоскости данные призмы являются равнобедренными прямоугольными треугольниками, то они обеспечивают отсутствие острых и прямых углов в полости литья, а как следствие и устранение концентраторов напряжений синтеграна в местах его контакта с краями станины. Иными словами, любой угол в полости литья – тупой. В-третьих, благодаря призмам, повышается суммарная масса торцов и самой станины, что позитивно влияет на жёсткость всей конструкции, а также увеличивается площадь поверхности контакта торцевых пластин с полом, повышая их устойчивость. В-четвёртых, призмы позволяют осуществлять повышенную величину растяжения армирующих элементов станины при меньшей деформации торцевых пластин. Обеспечивается это за счёт того, что, фактически, призмы являются рёбрами жёсткости для пластин в направлении действия силы сжатия стержней. И наконец, как уже было упомянуто выше, треугольные призмы, находящиеся на заднем торце станины являются установочной базой для портальной конструкции стоек на станину. В связи описания предложенных треугольных призм на торцах станины, важно упомянуть, что такие призмы могут быть изготовлены без потери их технической значимости отдельно от торцевых пластин при помощи комбинации операций отрезания и сваривания прутков квадратного проката ГОСТ.
Следующей ключевой конструктивной особенностью разрабатываемой станины являются её армирующие элементы. Предложенные нами армирующие элементы представляют собой два стальных стержня, которые имеют центральный участок в форме эллипса (см. рисунок 2.). Стержни обладают круглым поперечным сечением, диаметр которого зависит от габаритов станины и сил резания. Стержни выполняются из стали 45, а на их цилиндрических краевых участках нарезана метрическая резьба. Резьба на стержнях используется для их фиксации на торцах станины с последующим затягом. Габаритная длинна каждого армирующего элемента должна превышать габаритный размер самой станины, на величину около ста миллиметров, что необходимо для обеспечения достаточной наружной длинны армирующего элемента, используемой для его фиксации системой контргаек. Техническая значимость такой формы армирующего элемента будет рассмотрена и показана далее.
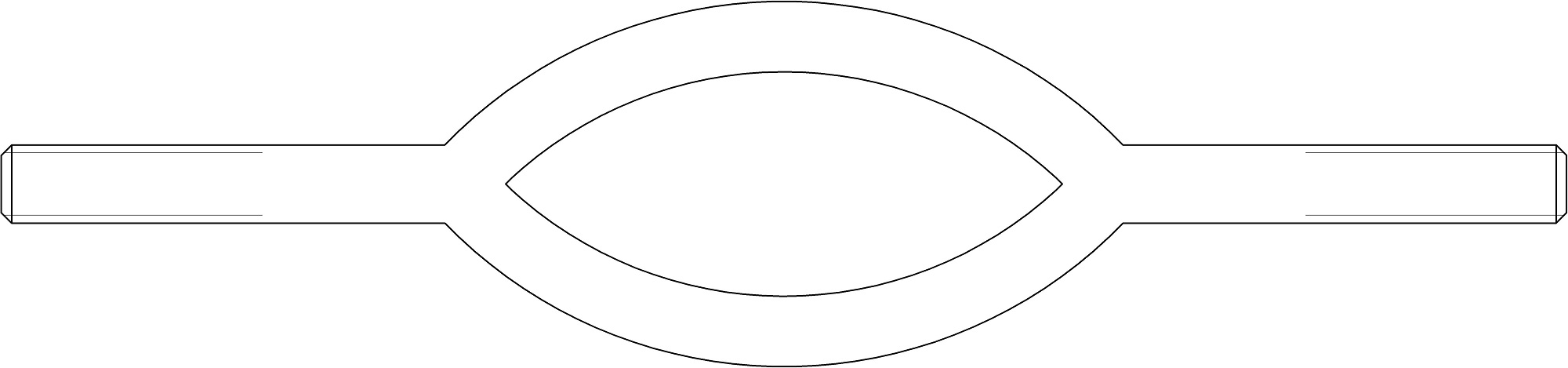
Рисунок 2 - Форма армирующего элемента станины
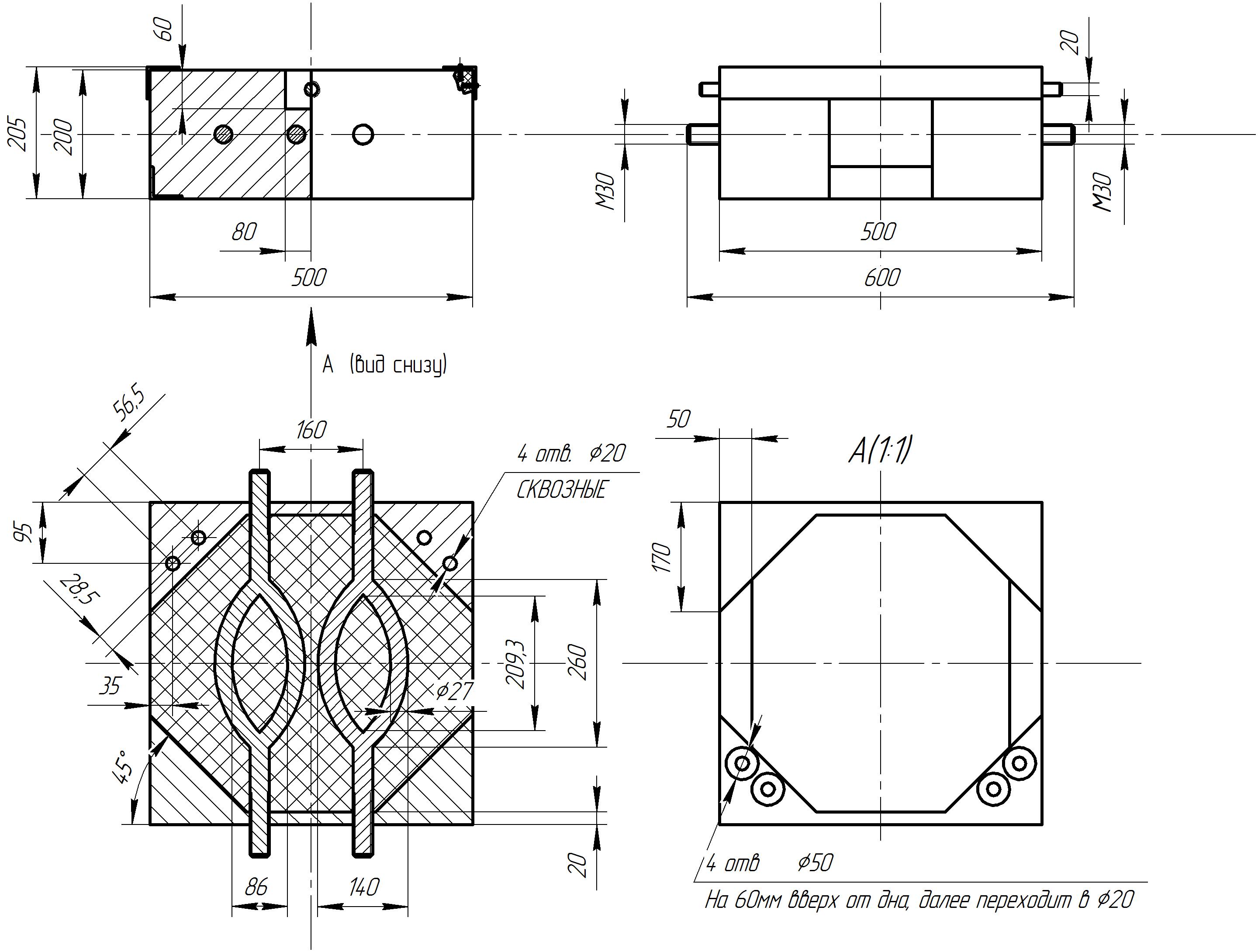
Рисунок 3 - Чертёж разработанной синтеграновой станины с армирующими элементами
Технология создания предложенной станины включает в себя ряд подготовительных действий. Сначала необходимо произвести подготовку тех поверхностей торцевых пластин, которые находятся в контакте с полом, стоечной конструкцией станка, а так же контргайками. Подготовка перечисленных поверхностей пластин заключается в фрезеровании поверхностей контакта и участков близ отверстий. Данный этап играет значительную роль для последующего обеспечения взаимной параллельности двух пластин и надёжности фиксации на них армирующих элементов.
Далее подготовленные торцевые пластины необходимо зафиксировать для реализации последующих операций. Фиксация осуществляется путём закрепления каждой пластины по контуру в заделке. После чего, между зафиксированными пластинами устанавливаются специальные распорки, имеющие Х-образную форму. Её концы упираются перпендикулярно во внутренние грани торцевых треугольных призм (см. рисунок 5(а)), обеспечивая, таким образом, требуемую взаимную параллельность пластин, а как следствие и геометрических параметров самой станины. Затем в отверстия на торцевых пластинах устанавливаются будущие армирующие элементы станины. На данном этапе они представляют собой прямые стальные стержни с утолщённым центральным участком, который имеет длинный сквозной разрез вдоль оси стержня (см. рисунок 4). Эти центральные участки как раз и становятся криволинейными на конечных армирующих элементах, форма эллипса им придаётся посредством термо-силового воздействия. Реализуется это воздействие следующим образом: после установки стержней, их центральные участки нагреваются докрасна, приблизительно до 500º-450ºС и с помощью захвата термо-силовой установки производится растяжение правой и левой половин центрального участка в направлении, перпендикулярном оси стержня. Деформация происходит до момента формирования требуемой формы центрального участка. После придания стержням требуемой формы, на них производится ещё одно воздействие, а именно растяжение вдоль продольной оси с захватом за края, но при меньшей температуре (около 300 ºС). Величина данного растяжения рассчитывается предварительно, исходя из предполагаемых сил резания, возникающих при работе станка. Данное воздействие является ключевым, поскольку позволяет получить продольное растяжение, находящееся в области упругой деформации стержня, и поэтому в полученных армирующих элементах имеет место постоянно действующая сила сжатия. Следующим шагом в технологии изготовления станины является фиксация готовых армирующих элементов на торцевых пластинах при помощи систем контргаек. Крепление контргайками предусмотрено не только с внешней, но и с внутренней стороны стальных пластин, суммарно в восьми местах (см. рисунок 5(г)).
После закрепления армирующих элементов на торцах, следует удалить распорки и фиксаторы пластин. Полученная конструкция не является замкнутой полостью для литья, а потому необходимо закрыть пустое пространство между призмами передней и задней пластин по бокам станины. Для этого предполагается использовать две деревянных дощечки, прижатых с наружной стороны массивным упором. Кроме этого, в верхней части сформированной конструкции нужно установить стержневой знак в форме прямоугольного параллелепипеда, который призван обеспечить полость при литье, используемую в дальнейшем для установки ШВП продольного хода в станину. Итак, в результате вышеописанных действий, получена конструкция станины из стальных элементов и готовая к литью синтеграна замкнутая форма.
Далее, в готовую форму производится заливка синтеграновой смеси, изготавливаемой по известной технологии . При этом, важно отметить, что подготавливается две смеси на одинаковом связующем компоненте, но с различной фракцией гранитной крошки. Фракция гранитной крошки в синтегране, который льётся в соприкосновении и в непосредственной близости от армирующих элементов станины и её торцевых пластин существенно меньше, чем фракция гранита в синтегране, льющегося во весь остальной объём. В процессе литья смесей синтеграна необходимо соблюдать одновременность заливки обоих смесей. Соблюдение этого условия в сочетании с одинаковостью связующего компонента двух смесей обеспечит их взаимное схватывание и отсутствие фрагментарности застывшего литого блока. Смысл решения относительно применения двух смесей с различными фракциями гранитной крошки состоит в предотвращении появления трещин внутри синтегранового блока при достаточно больших значениях сил сжатия в армирующих элементах. Риск растрескивания синтеграна изнутри определяется его физико-механическими свойствами, а именно сравнительно малым пределом работы на сжатие . Именно ввиду уменьшения фракции гранита в синетгране, данный риск частично или полностью ликвидируется в зависимости от величины сил сжатия. Объясняется это тем, что при уменьшении фракции гранитной крошки возрастает плотность упаковки гранита в смеси, а вместе с этим и ряд физико-механических свойств затвердевшего синтеграна, в том числе и предел его работы на сжатие . В остальных аспектах процесс литья синтеграна не имеет отличительных особенностей или тонкостей, прост, не требует повышенных температур, прочих особых условий среды и дорогостоящего специализированного оборудования. Подводя итог, можно обобщённо представить описанную технологию изготовления станины в виде нескольких основных этапов, представленных схематично на рисунке 5. Таким образом, получена конструкция станины, где застывший синтегран является твёрдым, монолитным композитным блоком с массивными стальными торцами, а армирующие элементы жёстко зафиксированы внутри него и находятся под действием сил сжатия, равных или кратно превышающих предельные силы резания при работе станка.

Рисунок 4 - Исходный стержень до деформационного воздействия

Рисунок 5 - Схематичное изображение основных этапов технологии до литья:
а, б, в, г — последовательность этапов
Итак, с целью оценки технической значимости, нами была построена математическая модель системы СПИЗ, где в качестве станка рассматривается настольный горизонтально-фрезерный станок. Используемая нами для анализа математическая модель была построена на базе существующих верифицированных математических моделей настольных станков, а в частности на базе – . Разработанная математическая модель для нашего случая представляет собой дискретную упруго-массовую систему, описываемую системой нелинейных дифференциальных уравнений, приведённой ниже (cм. рисунок 6):
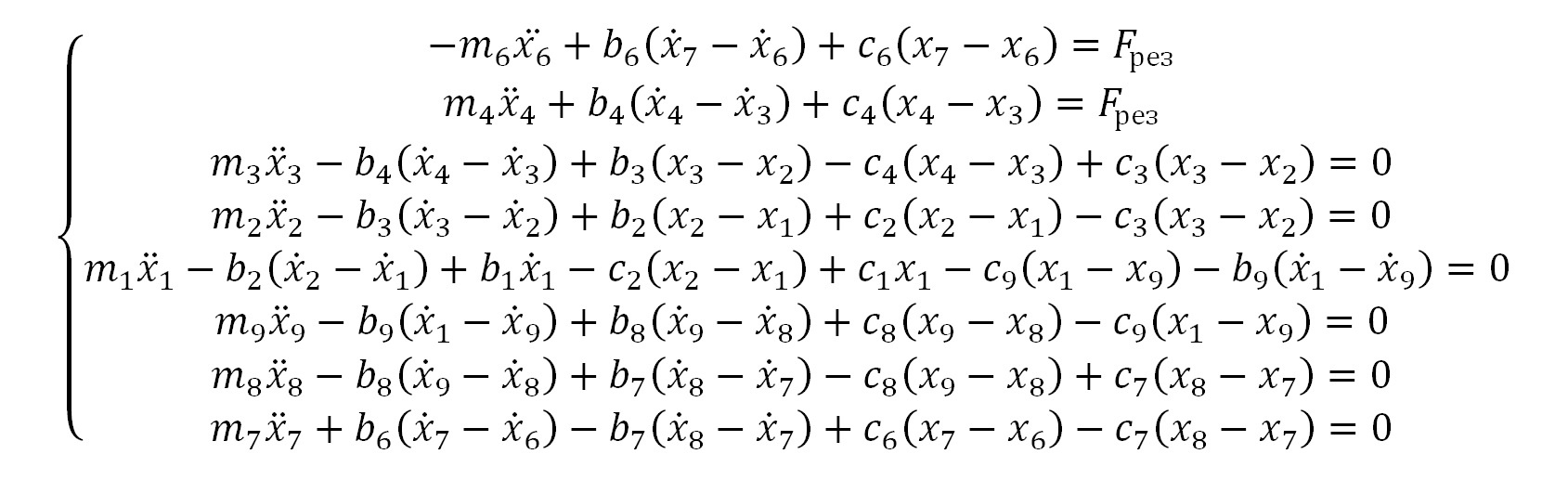
Рисунок 6 - Система уравнений, описывающая математическую модель
Расчётная схема математической модели состоит из отдельных узлов станка и компонентов системы СПИЗ, которые представлены в виде комбинации блоков определённой массы, пружин с конкретным значением жёсткости и демпферов, обладающих некоторым коэффициентом демпфирования. Расчётная схема показана в двух проекциях (см. рисунок 7).
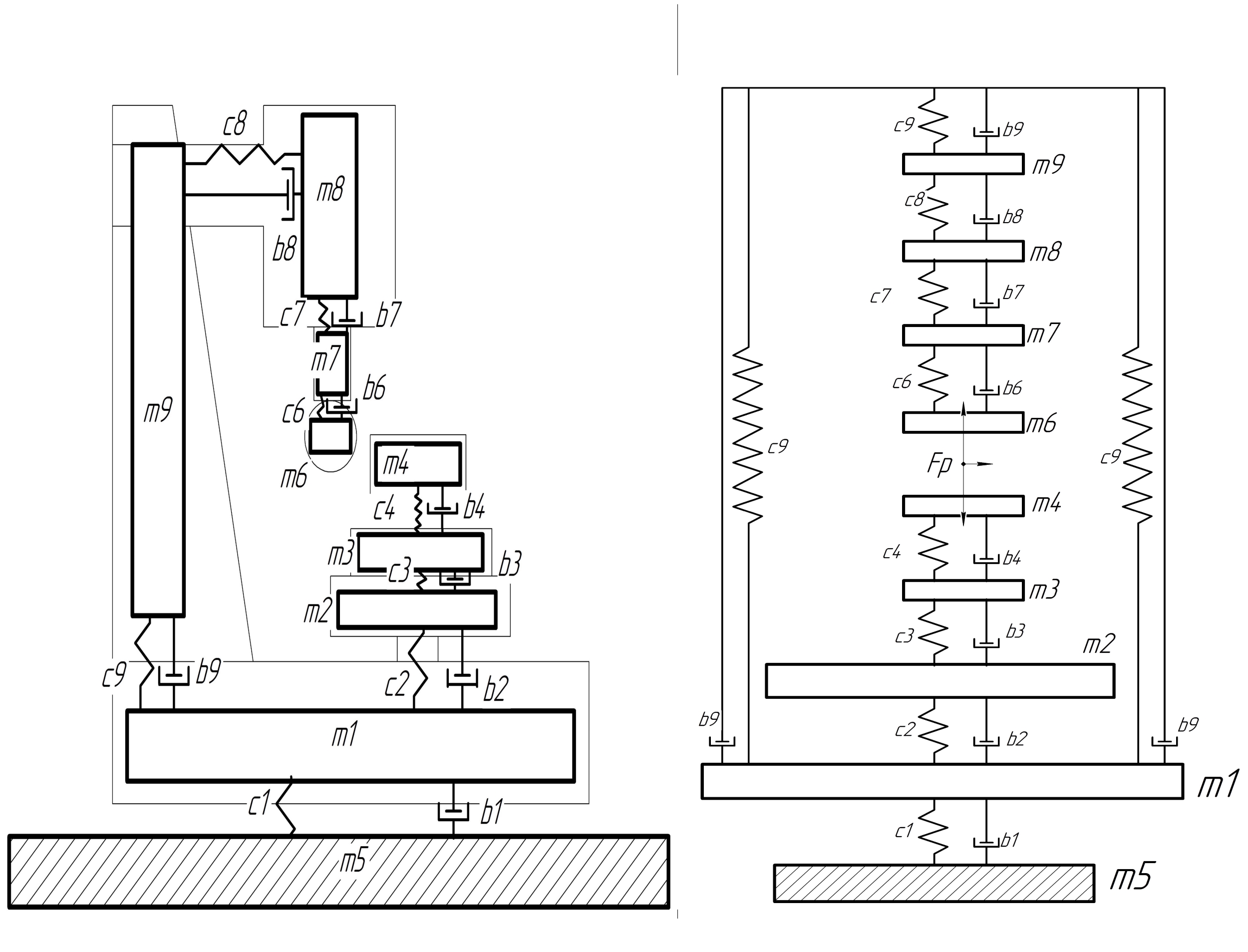
Рисунок 7 - Расчётная схема математической модели настольного горизонтально-фрезерного станка:
1 - станина; 2 - столик; 3 - приспособление; 4 - заготовка; 5 - основание; 6 - инструмент; 7 - шпиндель; 8 - фрезерная бабка; 9 - стойки
Для оценки жёсткости использовалось мгновенное разовое приложение возмущающей силы на систему СПИЗ, в результате чего в системе возбуждались затухающие колебания. Конечно, при реальной работе станка сила действует не разово, однако для нас важен лишь общий характер реакции системы на возмущающую силу и величина входной амплитуды, а потому данный подход принимается допустимым. Прикладывая последовательно силу резания величиной, например, 700 ньютон к системе в случае использования в ней обычной литой синтеграновой станины без натянутых армирующих элементов и в случае использования предложенной нами станины, были получены графики перемещений в виде колебаний, значительно отличающихся друг от друга (см. рисунок 8).
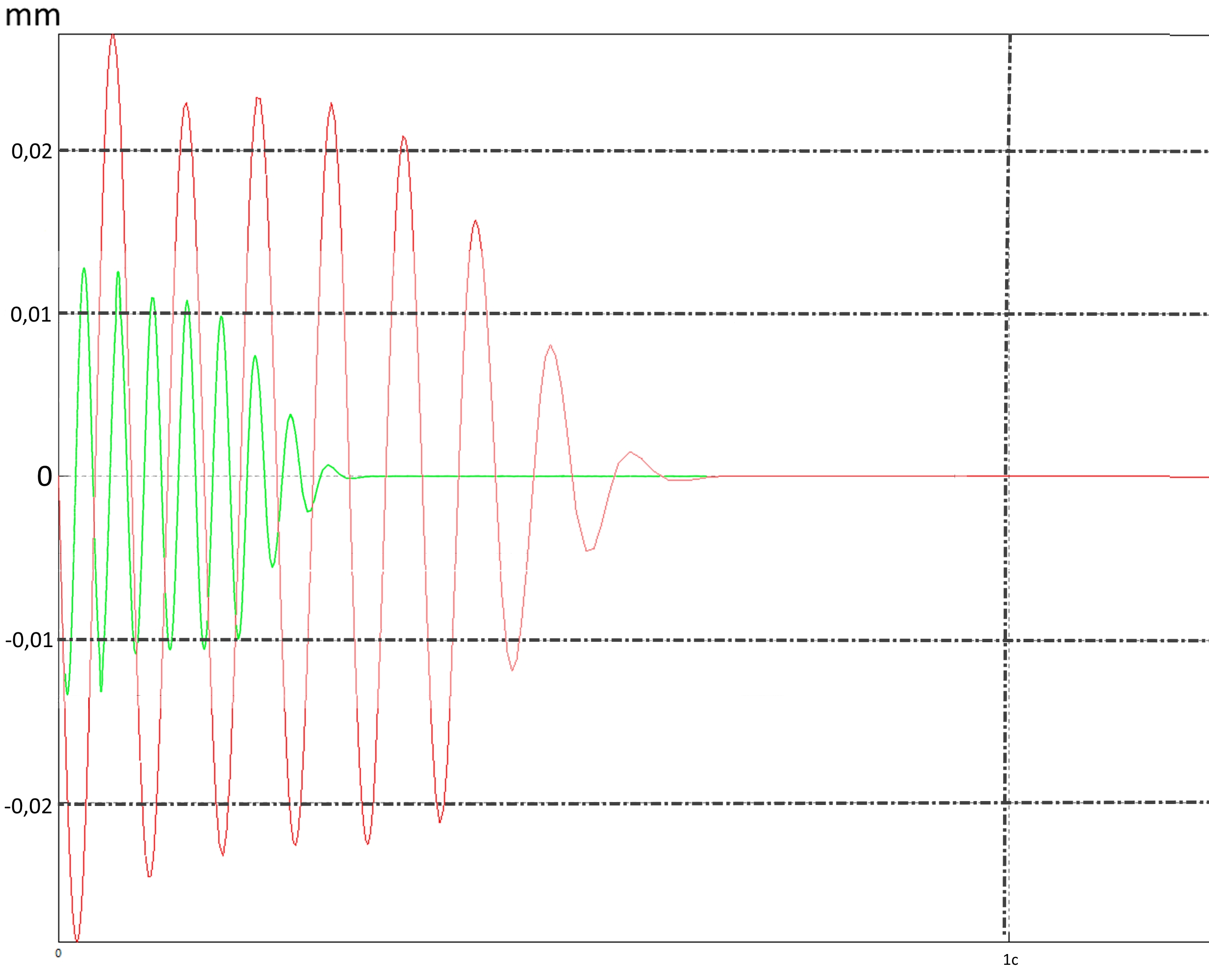
Рисунок 8 - Графики зависимости перемещений от времени в системе СПИЗ:
зелёный график – используется предложенная нами станина; красный – обыкновенная литая синтеграновая станина
В связи разъяснения технической значимости натянутых армирующих элементов, важно упомянуть и о технической значимости криволинейных участков на них. Наличие эллипс-образного участка позволяет получить вторую составляющую силы сжатия в стержне, а как следствие и частично компенсировать сонаправленную с ней составляющую силы резания (см. рисунок 9). Таким образом, появляется возможность гасить колебания как в продольном, так и в поперечном направлениях станины. Очевидно, что величина этой поперечной составляющей силы сжатия кратно меньше, чем у продольной, но в то же время и соответствующая ей составляющая силы резания при фрезеровании, гораздо меньше .
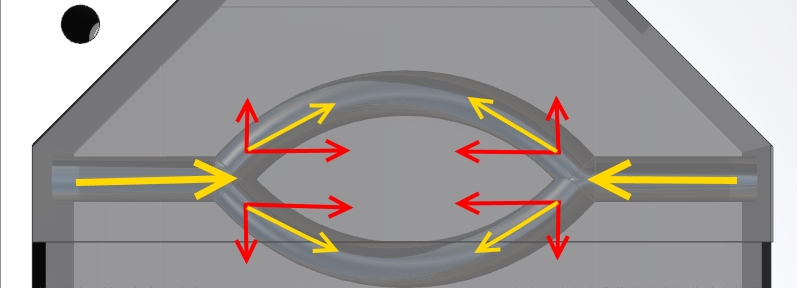
Рисунок 9 - Силы сжатия и их составляющие, постоянно действующие в армирующем элементе станины
Сам по себе синтегран по своим демпфирующим свойствам значительно превосходит чугун и тем более сталь . Для наглядности, с помощью всё той же математической модели, были приложены не равные возмущающие силы к станкам на основе разработанной синтеграновой станины и чугунной станины с армирующими элементами (см. рисунок 10). Различные силы приложены с целью вызвать одинаковую начальную амплитуду в обеих станинах, так как в противном случае не удастся оценить демпфирующие способности, ввиду того, что колебания в случае использования разработанной синтеграновой станины затухнут раньше из-за их меньшей начальной амплитуды.
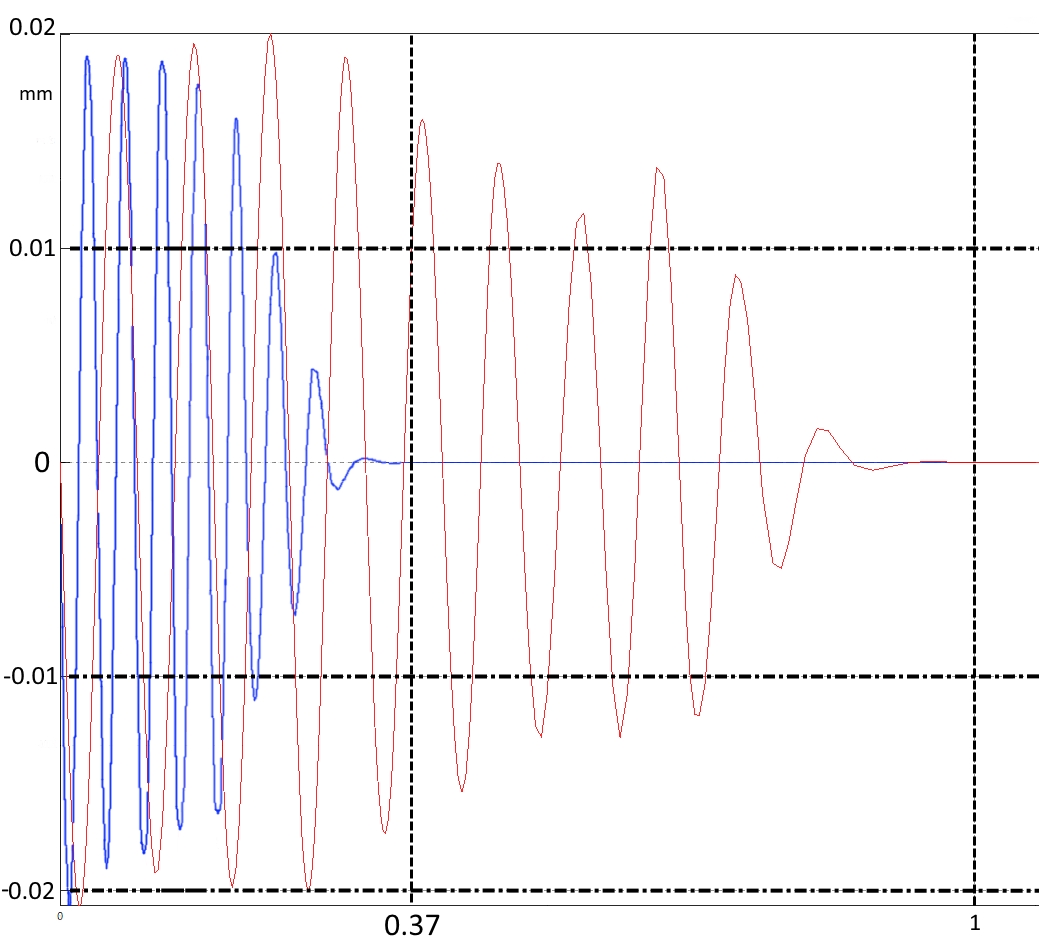
Рисунок 10 - Графики зависимости перемещений от времени в системе настольного фрезерного станка:
синий - используется предложенная нами станина; красный – чугунная станина с армирующими элементами
Ещё одной, важной к рассмотрению с точки зрения эксплуатации характеристикой, является виброустойчивость станка. Применение синтеграна в конструкции несущих элементов станка в общем случае приводит к повышению виброустойчивости в несколько раз . Посредствам математической модели настольного станка нами были проанализированы свойства виброустойчивости, а также влияние на них применения разработанной станины.
На приведённом изображении (см. рисунок 11) показана амплитудно-фазочастотная характеристика, обозначения вещественной и мнимой осей которой были заменены характеристиками, отражающими их физический смысл . Из АФЧХ видно, что при использовании синетграновой станины существенно уменьшается амплитуда отклонений головки станка при его работе. Таким образом, применение предложенной станины в настольном горизонтально-фрезерном станке имеет смысл, в том числе и с точки зрения виброустойчивости.
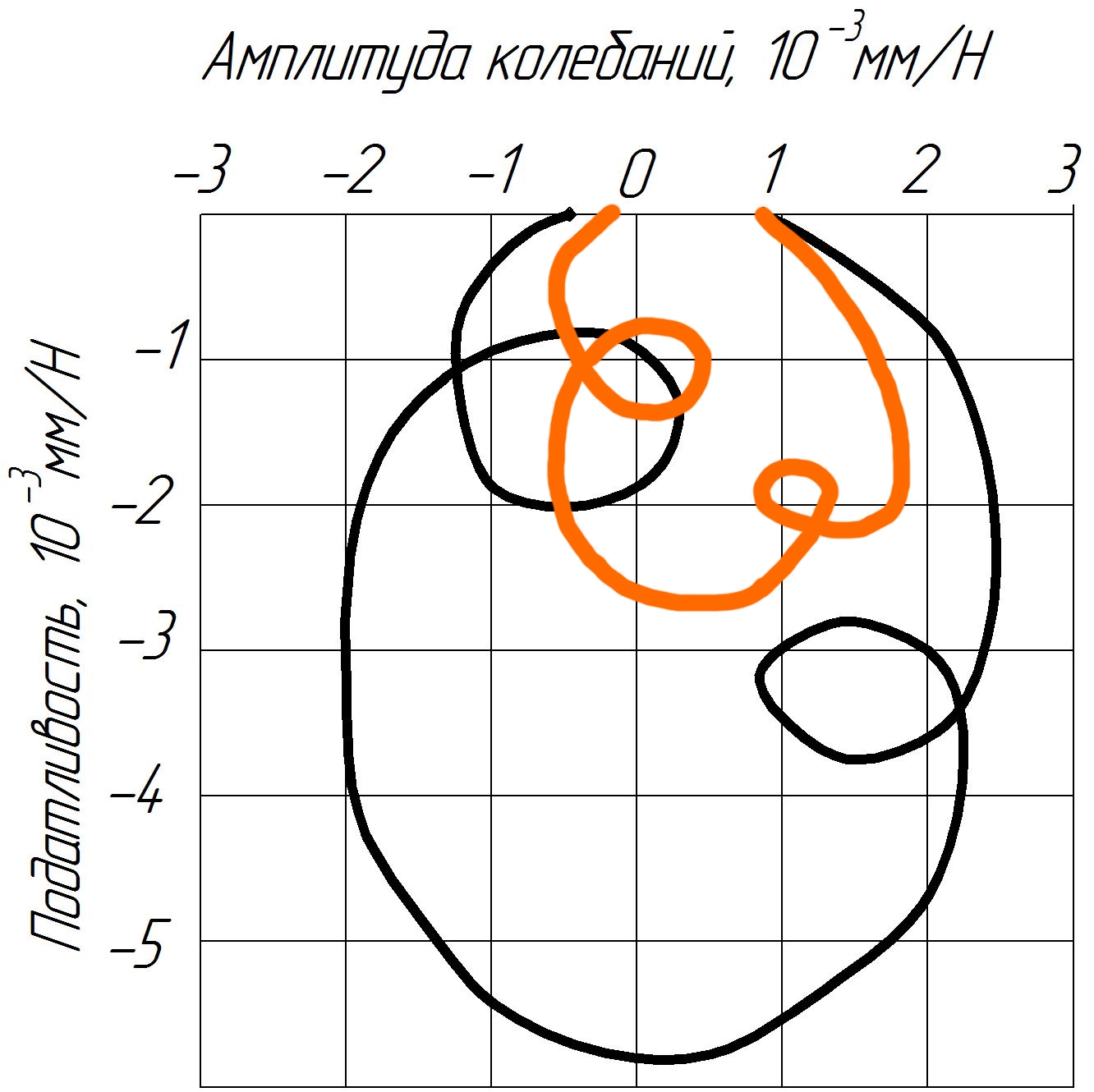
Рисунок 11 - АФЧХ настольного горизонтально-фрезерного станка:
оранжевая кривая – станок с предложенной синтеграновой станиной; черный – станок с чугунной станиной при тех же габаритах
3. Заключение
Подводя итог, можно утверждать, что предложенная конструкция синтеграновой станины с предварительно натянутыми армирующими элементами особой формы имеет в себе уникальное сочетание свойств жёсткости, виброустойчивости и демпфирования и обладает преимуществами по этим свойствам. А преимущество в точности обработки на станке с такой станиной зависит не только от физических свойств литого материала станины, но также и от соотношения между созданной силой сжатия в армирующих элементах и действующей силой резания.