AN EXPERIMENT AND CALCULATIVE EVALUATION OF DEFORMATION CHARACTERISTICS OF A SPECIAL LABORATORY SPECIMEN FOR MECHANICAL TESTS
AN EXPERIMENT AND CALCULATIVE EVALUATION OF DEFORMATION CHARACTERISTICS OF A SPECIAL LABORATORY SPECIMEN FOR MECHANICAL TESTS
Abstract
The article describes experimental studies of the stress-strain state (SSS) characteristics of a laboratory prismatic specimen used to evaluate the structural strength of a material. This specimen allows to model in its working zone biaxial tension of material with different ratio of values of principal stresses, and at the same time its loading is carried out on standard testing equipment with one power drive. The displacements and deformations of the specimens are studied at the stage of their elastic deformation on the basis of the digital image correlation method. Quantitative analysis of comparison of the results obtained by MCIA with the results of physical experiment modelling based on the finite element method is performed. According to the totality of the presented data, the obtained experimental and calculated displacements and deformations have a discrepancy not exceeding 14%.
1. Введение
Исследования прочности деталей машин и конструкций в зависимости от вида возникающего в них напряженно-деформированного состояния (НДС) проводятся, как правило, на основе испытания специальных лабораторных образцов, способных создавать в своей рабочей зоне НДС с требуемыми параметрами
, , . В свою очередь, наибольшую трудоемкость на лабораторных образцах вызывает моделирование НДС, характеризуемое различным соотношением величин главных напряжений и их знаков .В работе описываются экспериментально-расчетные исследования НДС (далее – деформационных характеристик) лабораторного призматического образца, способного моделировать в своей рабочей зоне двухосное растяжение материала с различным соотношением величин главных напряжений с целью оценки достоверности этого НДС, полученного в результате расчетных исследований методом конечных элементов (МКЭ). Испытание такого образца осуществляется на стандартном оборудовании с одним силовым приводом
. Как показали результаты этих исследований , варьирование геометрических параметров указанного образца позволяет воспроизводить требуемое двухосное НДС, аналогичного тому НДС, которое возникает в исследуемой конструкции, прочность которой оценивается.2. Методы и принципы исследования
Для оценки достоверности деформационных характеристик предложенных образцов, полученных в результате исследований по МКЭ, проводились экспериментальные исследования перемещений и деформаций этих образцов. В исследовании использовался метод корреляции цифровых изображений (МКЦИ)
, реализованный в цифровой оптической системе Vic-3D , . Данная система представлена на рис. 1. Суть метода МКЦИ сводится к отслеживанию смещений одних и тех же физических точек на поверхности тела до и после его деформирования. Свидетелями этому являются смещения элементов системы хаотически распределенных по поверхности объекта и неразрывно связанных с ним малоразмерных меток-пятен – спекл-структуры . Для анализа полей перемещений и деформаций необходимы, как минимум, два изображения поверхности испытуемого объекта со спекл-структурой. Одно из этих изображений, как правило, регистрируется в исходном состоянии объекта, а второе – при заданной нагрузке. В ходе обработки полученных изображений вся поверхность объекта разбивается на фрагменты и анализируется перемещение спекл-структуры в пределах каждого элементарного окна , .Наиболее важным параметром, определяющим точность получаемых экспериментальных данных на основе использования системы Vic–3D, является уровень дискретности спекл-структуры, связанной с поверхностью объекта. Для обеспечения метрологически необходимой спекл-структуры на поверхности образца и оценки достоверности получаемых деформационных характеристик проведены тестовые испытания на растяжение плоских образцов, имеющих центральные круглые отверстия
, . В соответствии с измерительная погрешность МКЦИ при определении всех компонент деформаций около центрального отверстия не превысила 8%.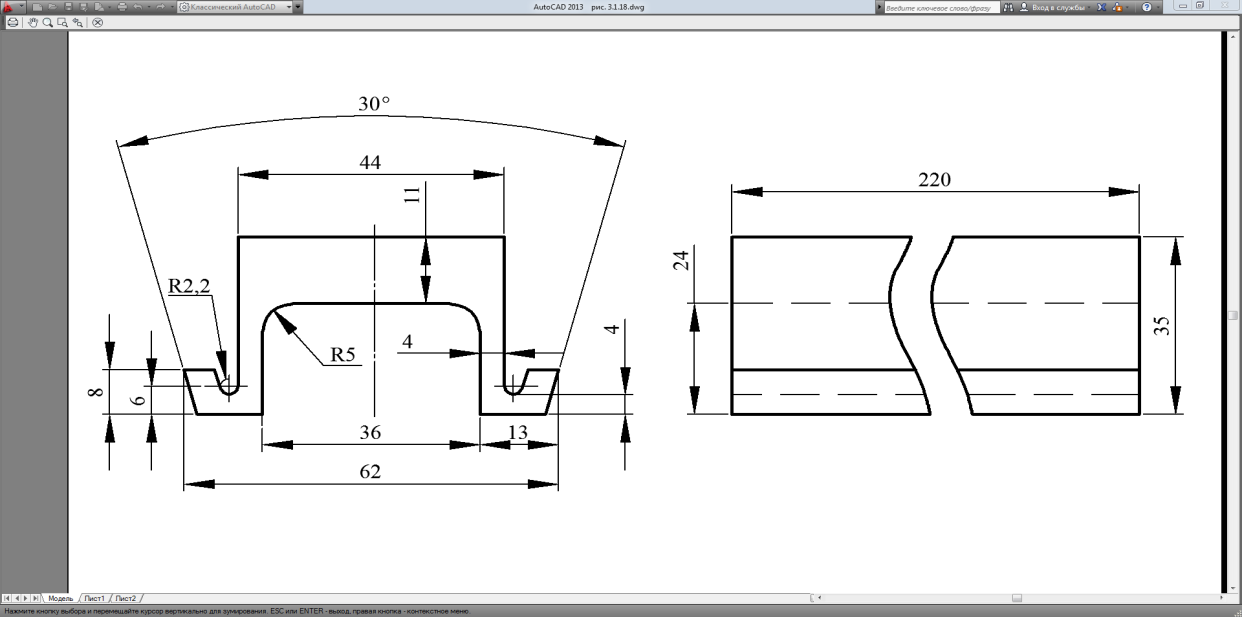
Рисунок 1 - Геометрические размеры призматического образца
Измерение перемещений и деформаций выполнялось для боковой поверхности призматического образца, доступной для фотофиксации цифровыми камерами с помощью МКЦИ. Нагружение призматического образца выполнялось при постоянной скорости нагружения 2 мм/мин. Таким образом, полученные экспериментальные поля компонент перемещений и деформаций позволят далее сравнить их с результатами соответствующих расчетными данными по МКЭ
.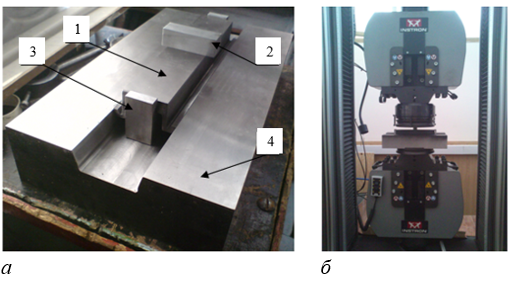
Рисунок 2 - Лабораторная установка для испытания призматических образцов
Примечание: а – базирование образца в опорах (1 – образец, 2 – усилие, создаваемое толкателем испытательной машины, 3 – концевые опоры, 4 – призматическая опора), б – базирование призматической опоры с образцом на рабочем столе испытательной машины
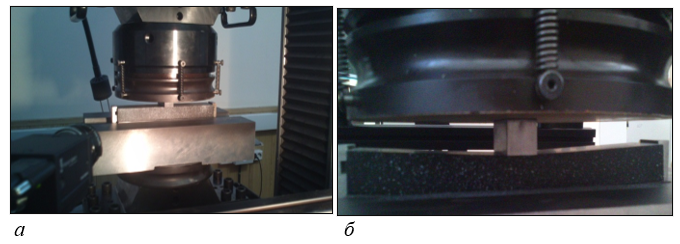
Рисунок 3 - Деформированное состояние призматического образца
Примечание: а – начальное состояние, б – конечное состояние
3. Результаты экспериментальных и расчетных исследований
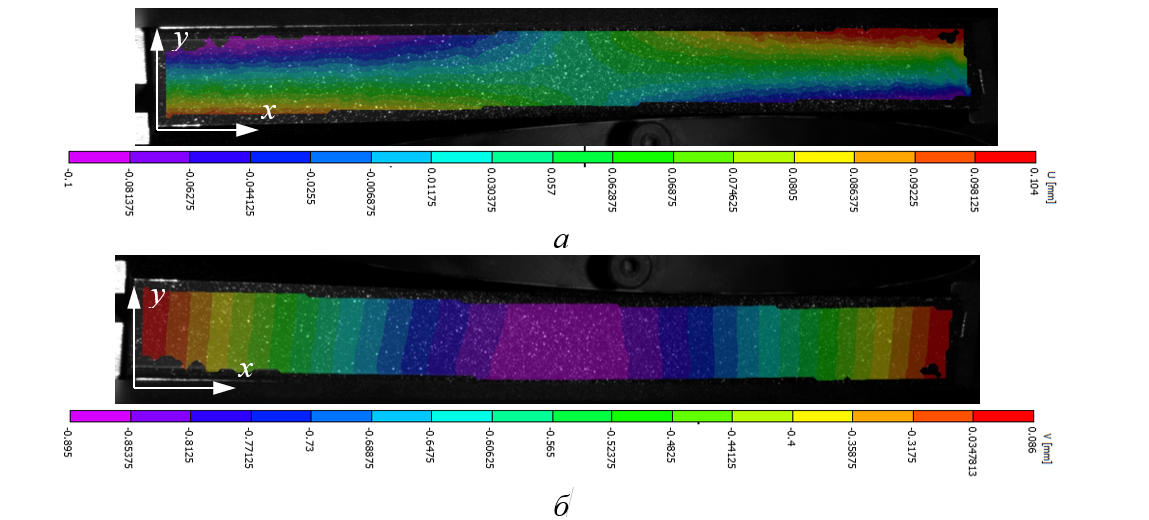
Рисунок 4 - Распределение экспериментального поля продольных Δlxx (а) и осевых Δlyy(б) перемещений
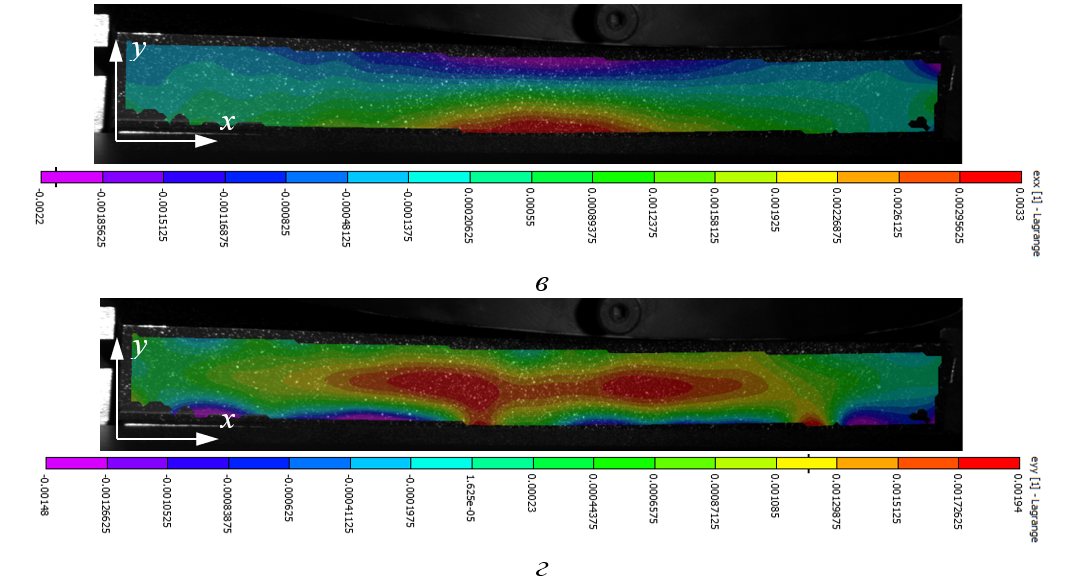
Рисунок 5 - Распределение экспериментального поля продольных εxx (в) и осевых εyy (г) деформаций
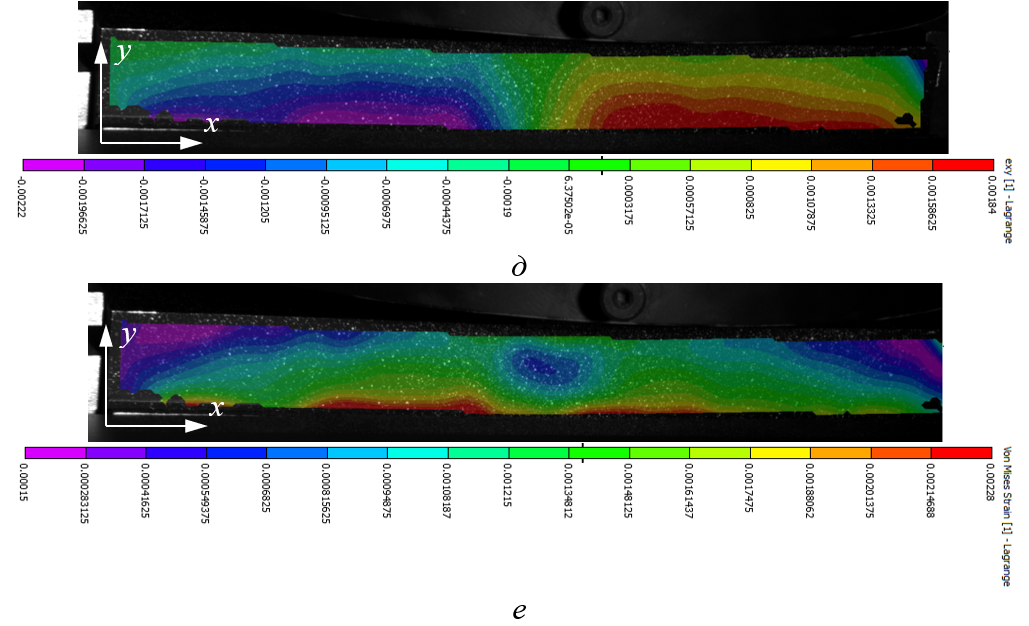
Рисунок 6 - Распределение экспериментального поля сдвиговой εxy (д) деформации и интенсивности εi (е) деформаций в результате обработки системой Vic-3D
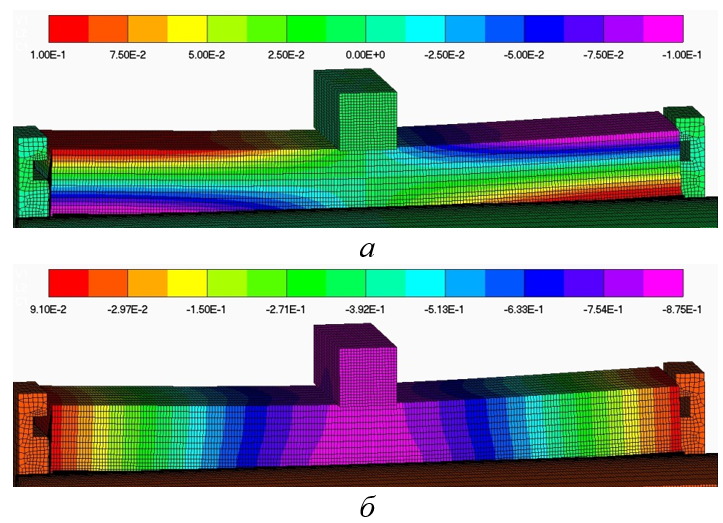
Рисунок 7 - Распределение расчетного поля продольных Δlxx (а) и осевых Δlyy(б) перемещений
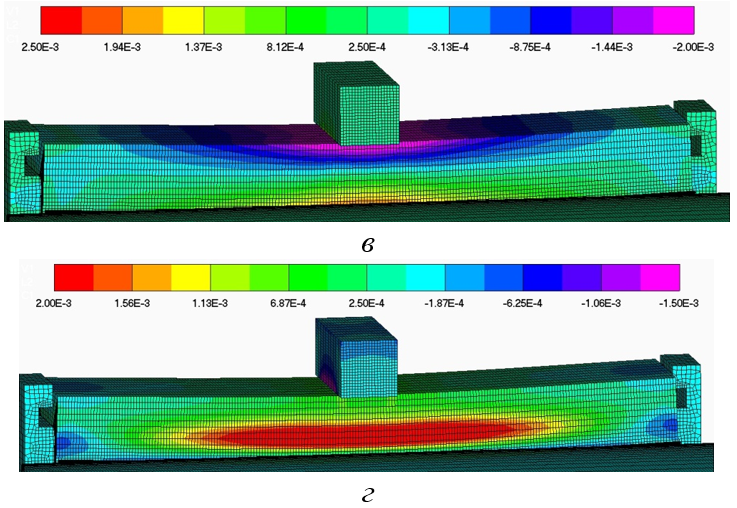
Рисунок 8 - Распределение расчетного поля продольных εxx (в) и осевых εyy (г) деформаций
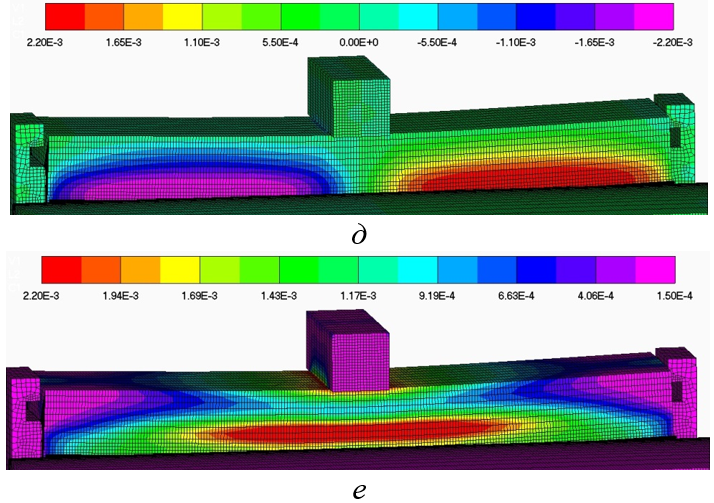
Рисунок 9 - Распределение расчетного поля сдвиговой εxy (д) деформации и интенсивности εi (е) деформаций в результате вычислительного эксперимента по МКЭ
В качестве меры относительной погрешности расхождения результатов физического эксперимента при использовании системы Vic-3D с данными численного моделирования рассматривалось отношение
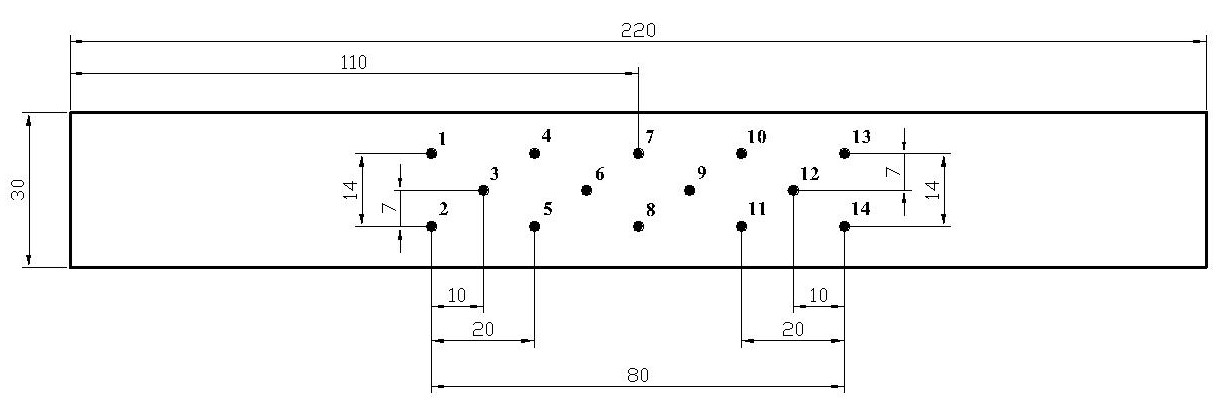
Рисунок 10 - Расположение контрольных точек на боковой поверхности образца
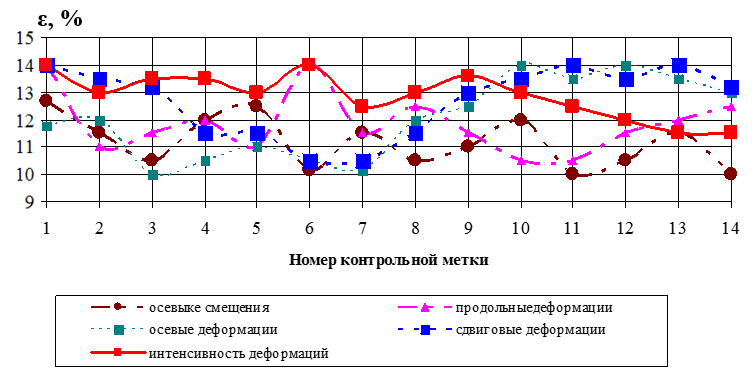
Рисунок 11 - Погрешность расхождения сравниваемых перемещений и деформаций в контрольных точках исследуемой поверхности образца
4. Заключение
По совокупности представленных экспериментальных данных можно заключить, что численная модель деформирования образцов призматического типа позволяет определять их НДС с относительной погрешностью, не превышающей 14%. Это обстоятельство подтверждает адекватность принятых расчетных схем и дискретных моделей, разработанных на основе трехмерных уравнений теории упругости.
Полученный в работе анализ деформационных характеристик призматических образцов позволяет в дальнейшем использовать эти образцы для оценки конструкционной прочности различных материалов и реализовать предложенную в
расчётно-экспериментальную методику расчёта деталей машин и конструкций на статическую прочность с целью уточнения прочностных параметров материала.