РАЗРАБОТКА ПРОГРАММНОГО ОБЕСПЕЧЕНИЯ И ЭЛЕКТРОННОЙ ЧАСТИ ПРОМЫШЛЕННОГО ДЕЛЬТА-РОБОТА НА ПРИВОДАХ ABB
РАЗРАБОТКА ПРОГРАММНОГО ОБЕСПЕЧЕНИЯ И ЭЛЕКТРОННОЙ ЧАСТИ ПРОМЫШЛЕННОГО ДЕЛЬТА-РОБОТА НА ПРИВОДАХ ABB
Аннотация
В данной работе описывается процесс разработки программного обеспечения промышленного дельта-робота для выполнения специализированных операций, оснащенного приводами ABB и управляемого контроллером SIEMENS, а также модулем расширения X20 компании B&R. Основное внимание уделяется подбору компонентов, интеграции системы и программированию для достижения высокой точности и эффективности работы. Результатом разработки является робот, оптимизированный под задачи укладки продукции на пищевом производстве весом до 1кг, демонстрирующий улучшенные характеристики скорости, точности и надежности. Оригинальность работы подтверждена экспериментальными данными и сравнением с существующими аналогами, а также простотой создания из общедоступных промышленных комплектующих.
1. Введение
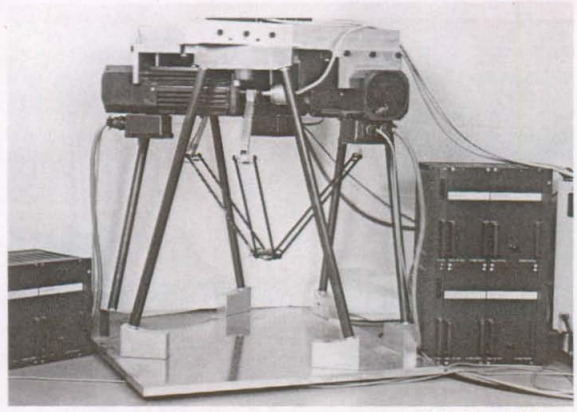
Рисунок 1 - Прототип одного из первых роботов DELTA 580
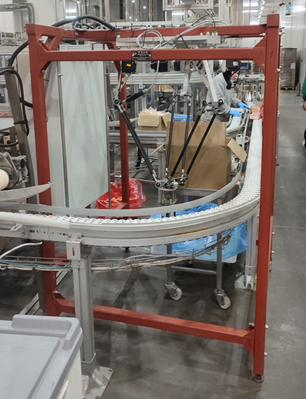
Рисунок 2 - Общий вид дельта робота
В процессе модернизации аппаратной части была произведена замена редукторов электродвигателей на имеющиеся в наличии на предприятии и использующиеся в похожем производственном оборудовании. Затем была произведена установка и настройка приводов путем подключения сигналов, и выставление задержек момента, тока, задание типа управления. Все это не составило больших затруднений, так как похожие параметры настроек часто производятся в процессе эксплуатации упаковочных машин. После этого был сделан монтаж трансформатора для питания всех узлов автоматики, так как для силовой части использовалось питание 110 В на одну фазу вместо обычно подаваемых 220 В. Затем был произведен монтаж блока питания и установка контроллера. В конце произведена установка и подключение остальных электронных управляющих компонентов, в виде кнопок, датчиков позиционирования. Далее, было произведено программирование контроллера SIEMENS и настройка связи в специализированной для данных контроллеров среде TIA Portal. После механической сборки и подключения электроники было разработано и загружено программное обеспечение для управления тягами через электродвигатели. В целом движение рабочего органа сводится к математической задаче обратной кинематики. Это требует математического преобразования координат в углы поворота валов электродвигателей.
Ниже приведен пример программных вычислений модели обратной кинематики:
// вспомогательная функция, расчет угла theta1 (в плоскости YZ)
int delta_calcAngleYZ(float x0, float y0, float z0, float &theta) {
float y1 = -0.5 * 0.57735 * f; // f/2 * tg 30
y0 -= 0.5 * 0.57735 * e; // сдвигаем центр к краю
// z = a + b*y
float a = (x0*x0 + y0*y0 + z0*z0 +rf*rf - re*re - y1*y1)/(2*z0);
float b = (y1-y0)/z0;
// дискриминант
float d = -(a+b*y1)*(a+b*y1)+rf*(b*b*rf+rf);
if (d < 0) return -1; // несуществующая точка
float yj = (y1 - a*b - sqrt(d))/(b*b + 1); // выбираем внешнюю точку
float zj = a + b*yj;
theta = 180.0*atan(-zj/(y1 - yj))/pi + ((yj>y1)?180.0:0.0);
return 0;
}
// обратная кинематика: (x0, y0, z0) -> (theta1, theta2, theta3)
// возвращаемый статус: 0=OK, -1=несуществующая позиция
int delta_calcInverse(float x0, float y0, float z0, float &theta1, float &theta2, float &theta3) {
theta1 = theta2 = theta3 = 0;
int status = delta_calcAngleYZ(x0, y0, z0, theta1);
if (status == 0) status = delta_calcAngleYZ(x0*cos120 + y0*sin120, y0*cos120-x0*sin120, z0, theta2); // rotate coords to +120 deg
if (status == 0) status = delta_calcAngleYZ(x0*cos120 - y0*sin120, y0*cos120+x0*sin120, z0, theta3); // rotate coords to -120 deg
return status;
}
Алгоритм работы робота сводится к позиционированию двигателей в начале запуска робота по датчикам нулевого положения двигателей и движению в точку с целевой координатой. Затем происходит сработка рабочего органа по сигналу с контроллера.
2. Выбор компонентов
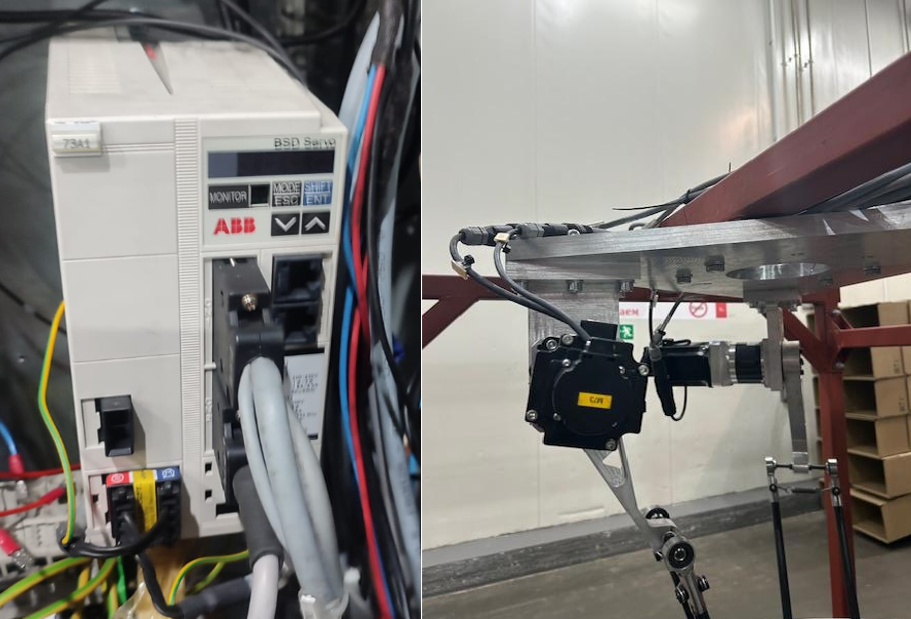
Рисунок 3 - Приводы и двигатели от компании ABB
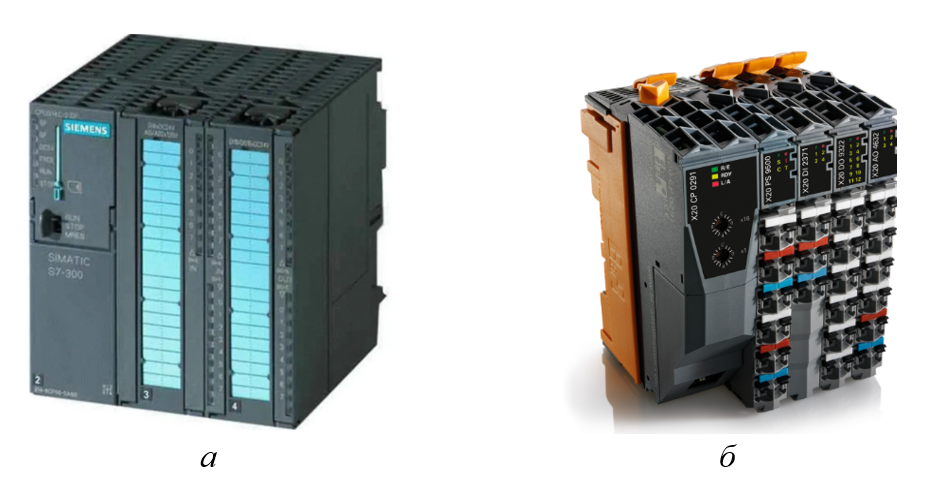
Рисунок 4 - Контроллер Siemens s7-300 (а) и модуль X20 B&R (б)
3. Разработка программного обеспечения
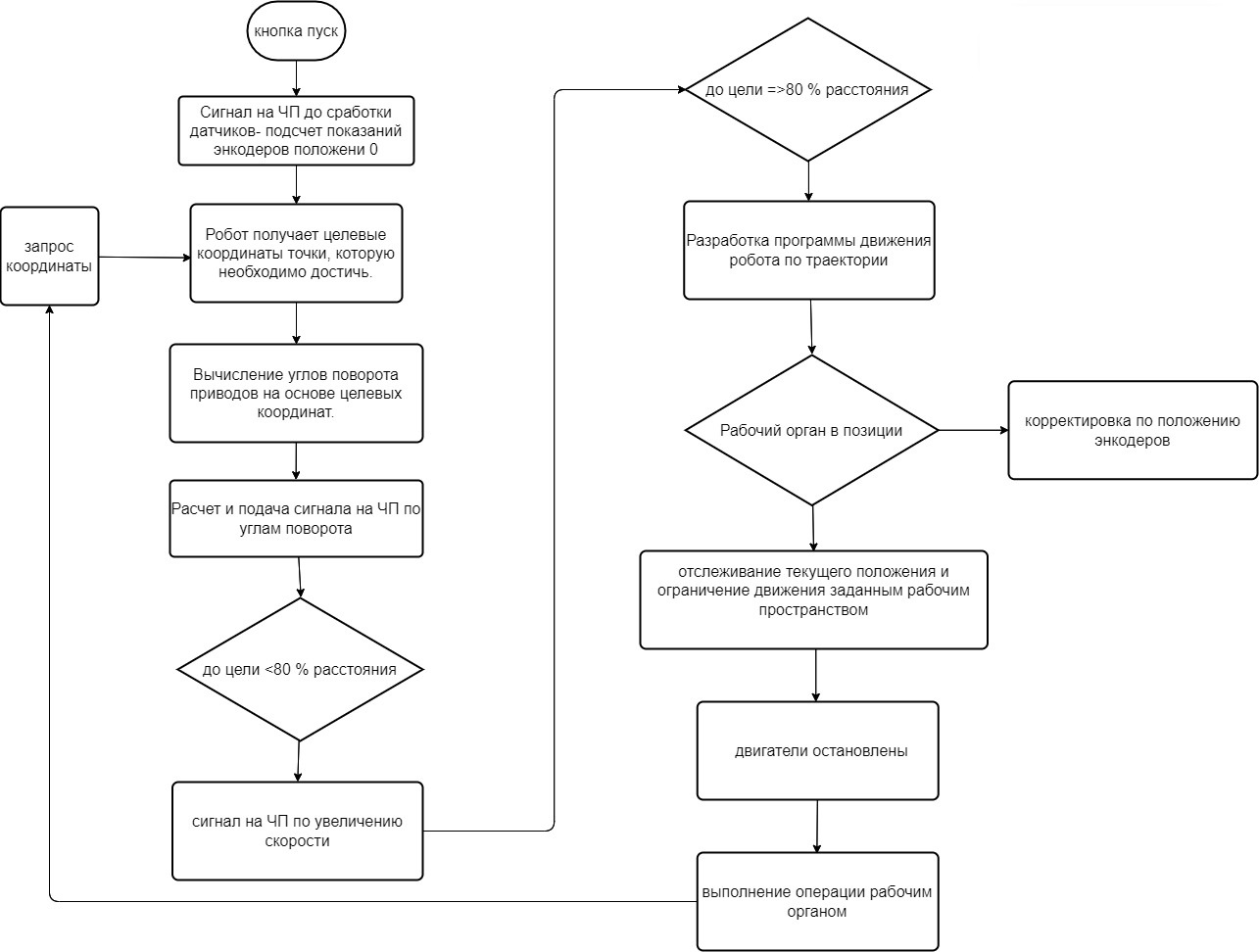
Рисунок 5 - Алгоритм перемещения рабочего органа в целевую координату
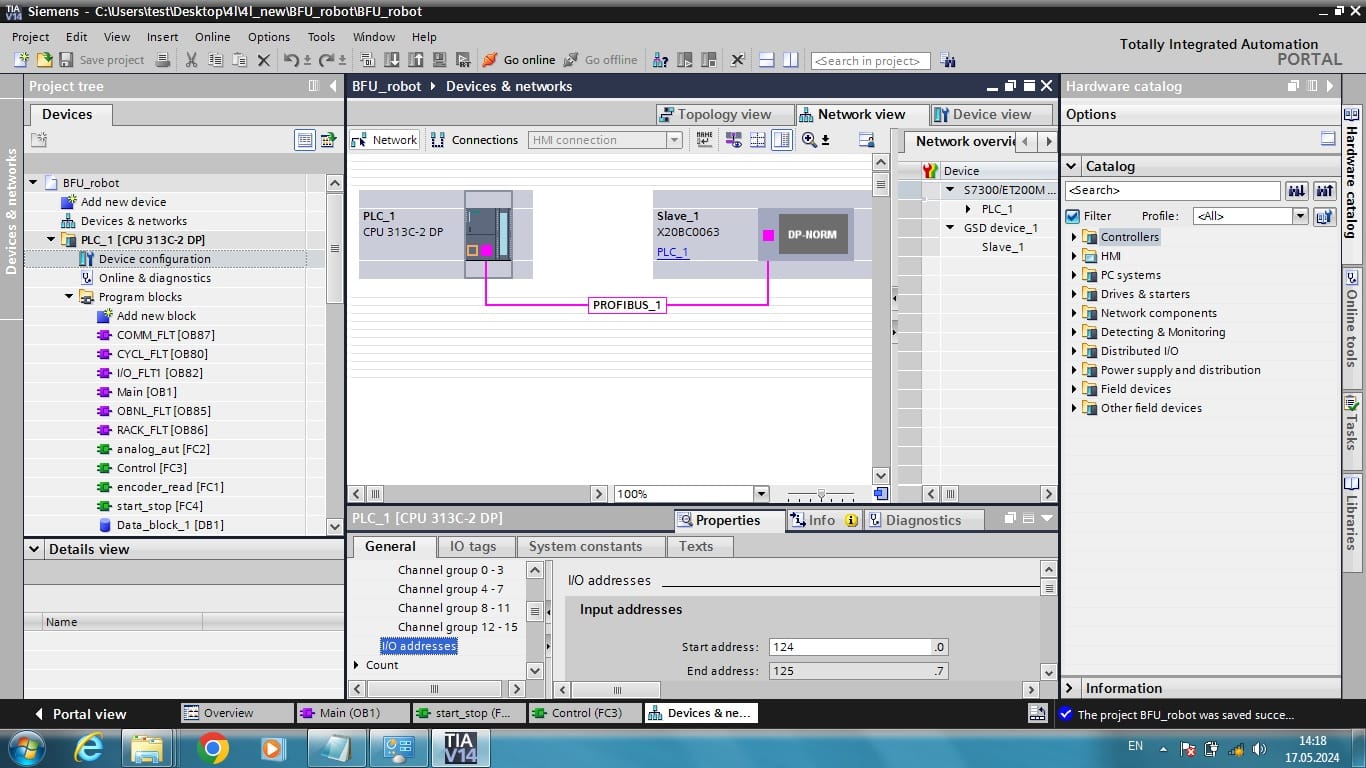
Рисунок 6 - Конфигурирование контроллера и модуля расширения в среде TIA Portal
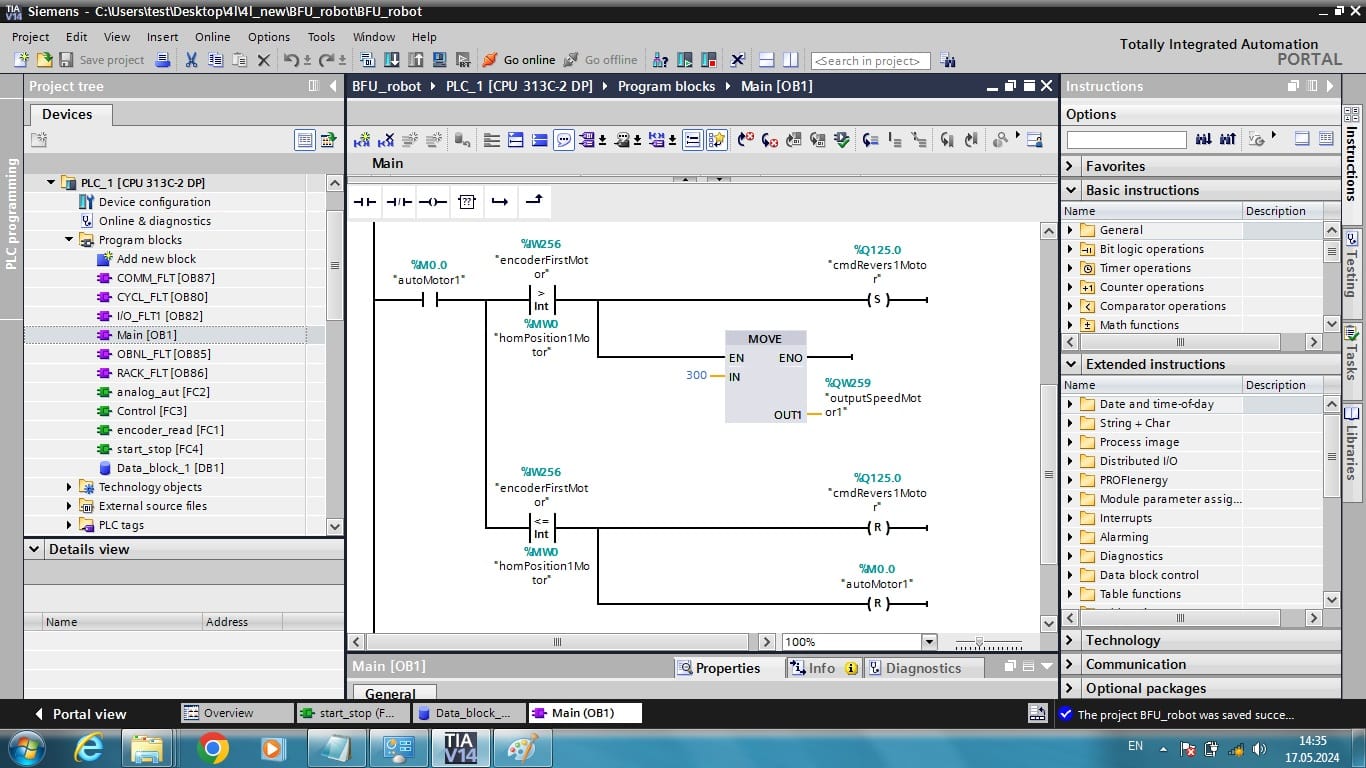
Рисунок 7 - Пример главной ветки программы
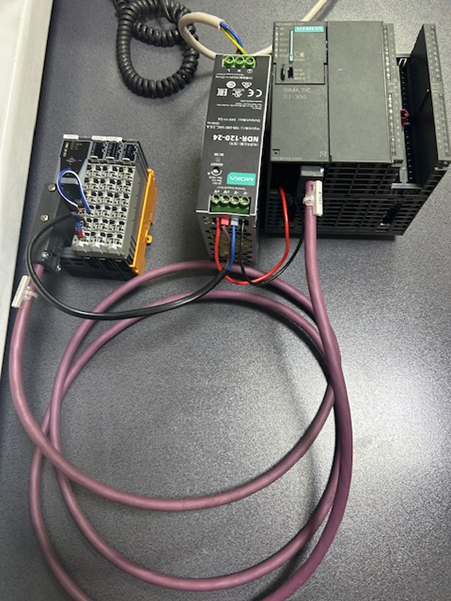
Рисунок 8 - Коммутация котроллера, блока питания и модуля расширения
Примечание: справа налево
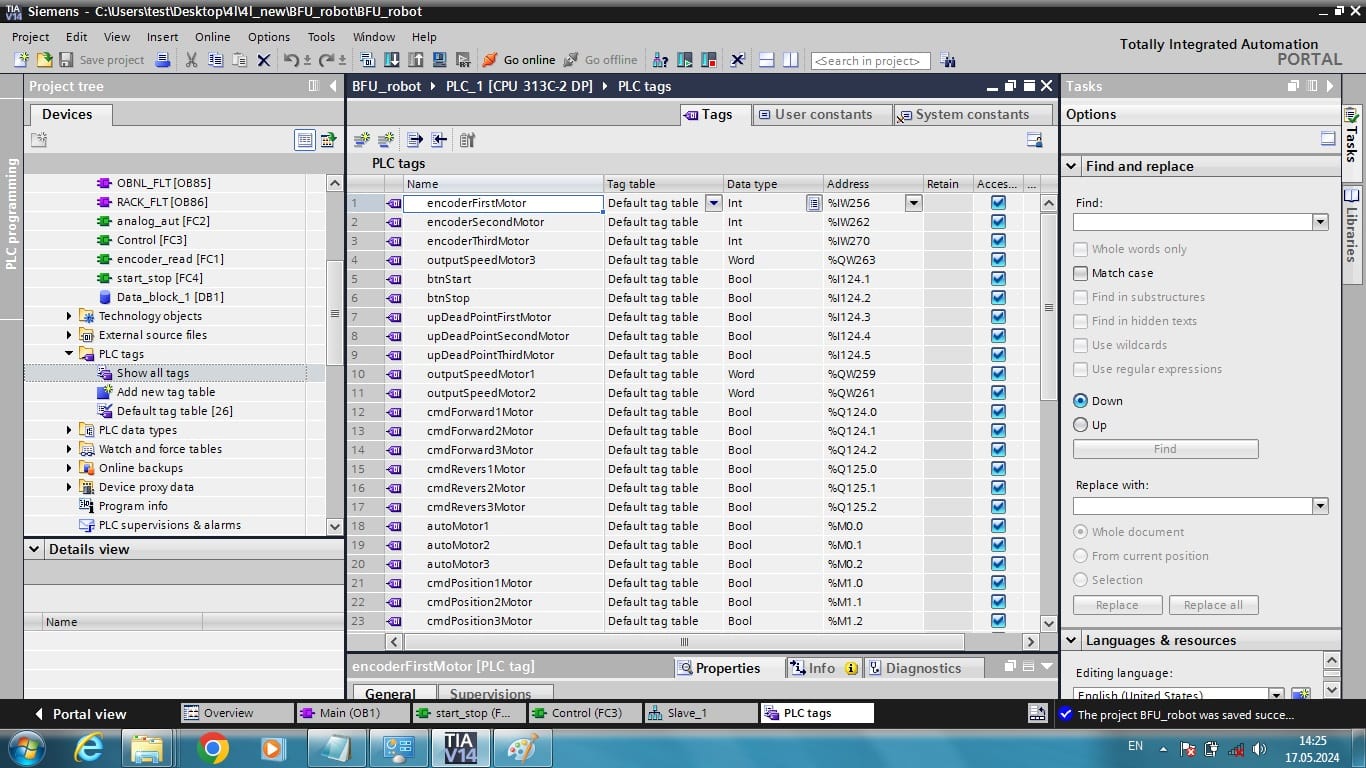
Рисунок 9 - Программные переменные в среде TIA Portal
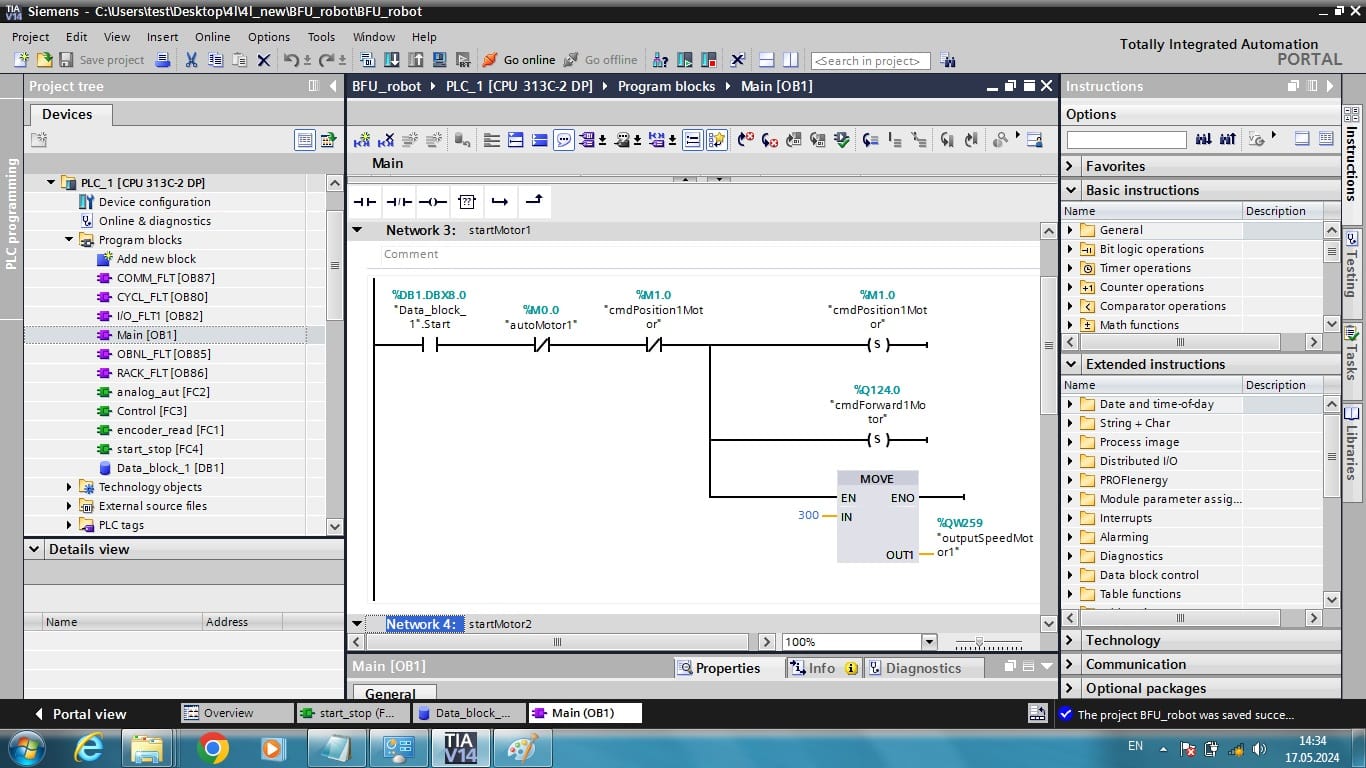
Рисунок 10 - Пример обработки значений энкодера в среде TIA Portal
4. Тестирование
В процессе тестирования и отладки были проведены испытания для проверки движения в начале калибровки нуля по датчикам положения нулевой точки энкодера, затем выход на позицию . Во время отладки программного обеспечения были применены корректировки конвертации углов поворотов энкодеров путем задания коэффициента-делителя в координаты рабочего органа робота.
Подход к разработке и интеграции промышленного дельта-робота потребовал взаимодействия между специалистами разных специализаций. К решению задач были привлечены механики, инженеры-электроники, программист АСУТП.
5. Перспективы улучшений
На базе полученного опыта и собранных данных планируется дальнейшая оптимизация работы дельта-робота, в частности разработка дополнительных модулей компьютерного зрения для расширения функционала робота, а также новые типы конечных эффекторов для работы с различными видами пищевой продукции.
Оптимизация работы дельта-робота путем внедрения компьютерного зрения является важным шагом для улучшения его функциональности, точности и эффективности. Этапами внедрения компьютерного зрения может быть установка и калибровка камеры, разработка алгоритмов обработки изображений для анализа визуальных данных, выделения объектов, распознавания образов и позиционирования в рабочем пространстве, интеграция с системой управления для принятия решений на основе полученных визуальных данных. Для более сложных задач компьютерного зрения можно использовать программирование и обучение нейронных сетей для распознавания образов, классификации объектов и принятия решений.
Использование компьютерного зрения позволило бы значительно расширить возможности и функциональность дельта-робота, сделать его более адаптивным к изменяющимся условиям и задачам, а также повысить производительность и точность его работы.
6. Заключение
В заключении разработки и интеграции специализированного промышленного дельта-робота на основе приводов ABB, контроллера Siemens и модуля X20 от B&R можно подчеркнуть несколько ключевых аспектов, которые стали основой для успешной реализации проекта . Выбор высококачественных компонентов от ведущих производителей, таких как ABB для сервоприводов и B&R, Siemens для контроллера, обеспечил не только высокую эффективность работы робота, но и его долговечность . Такие решения способствуют минимизации простоев и снижению эксплуатационных затрат. В статью не включена часть по разработке программного обеспечения панели оператора робота, так как размер статьи не позволяет представить необходимые пояснения. Описание решения этой части может быть изложена в следующей публикации.
В итоге данный проект подчеркивает значимость междисциплинарной работы и инновационного мышления в разработке современных промышленных решений. Он показывает успешное сочетание теоретических знаний и практического опыта, направленных на решение сложных инженерных задач.
Надеемся, что этот материал инициирует сотрудников различных предприятий на деятельность в сфере разработки производственного оборудования.