ОСНОВНЫЕ ПРИНЦИПЫ ПРОЕКТИРОВАНИЯ, ИЗГОТОВЛЕНИЯ И ПРИМЕНЕНИЯ МИКРОРЕАКТОРОВ
ОСНОВНЫЕ ПРИНЦИПЫ ПРОЕКТИРОВАНИЯ, ИЗГОТОВЛЕНИЯ И ПРИМЕНЕНИЯ МИКРОРЕАКТОРОВ
Аннотация
В данной обзорно-аналитической статье рассматриваются разработка, изготовление и применение малотоннажных микрореакторных систем. Технология микрореакций и микрореакторные системы направлены на повышение интенсификации и безопасности химических процессов. Технология микрореакций совершенствуется постоянно, в связи с чем обзор современных методов проектирования, изготовления, применения является важным аспектом для современного понимания развития малотоннажной химии. Микрофлюидные реактора получили широкое распространение в различных областях науки: медицина, специальная химия, биохимия, ядерная химия и многие другие. Они пользуются успехом ввиду обеспечения повышенного массо- и теплообмена, лучшей интенсификации процесса и, как следствие, высокого выхода продукта. Обсуждаются материалы, типы реакций, технологии изготовления, области применения.
1. Введение
Первые микрореакторы были изготовлены в начале 1990-х годов Центральным экспериментальным отделом Исследовательского центра Карлсруэ (Германия). Микрореакторы были побочным продуктом производства разделительных сопел для обогащения урана
. Центр занимался разработкой высокоэффективных микроструктурированных теплообменников. В связи с изменением политики Германии в области исследований ядерных технологий в 90-х годах, резкое сокращение финансирования заставило исследователей искать новое применение данной технологии. Группа исследователей изучила возможность применения микроструктурированных теплообменников для проведения высокоэкзотермических и опасных химических реакций. Новая концепция получила название «технология микрореакций» или «микротехнология». Далее в работах , , было показано, что микрореакторы с глубиной канала 100-1000 микрометров могут быть использованы для проведения сложных реакций, таких как этерификация, химическое гидрирование, окисление, нитрование, аминирование, получение азосоединений, металлорганические реакции.Цель данной работы – рассмотреть основные принципы проектирования, изготовления и применения микрореакторов за последние 30 лет.
Общепринятое определение, микрореактор – это устройство, в котором протекает химическая реакция в капиллярных каналах (диаметром менее 1 мм)
. Микрореакторы являются проточным типом реакторов. Микрореакторы имеют ряд преимуществ в сравнении с типовыми реакторами, таких как: хороший контроль температуры, эффективное перемешивание, как следствие, высокие показатели массообменных процессов, конверсии. Благодаря миниатюрным размерам микроструктур микрореакторы способствуют экономии материала при их изготовлении, а также сырья, катализатора и энергии в процессе эксплуатации. Вследствие ускорения тепло- и массопереноса производительность установок с микрореакторами в ряде случаев значительно (на 1-2 порядка) выше применяемых в промышленности классических реакторов . На рис. 1 представлена одна из простейших форм – Т-образный микрореактор.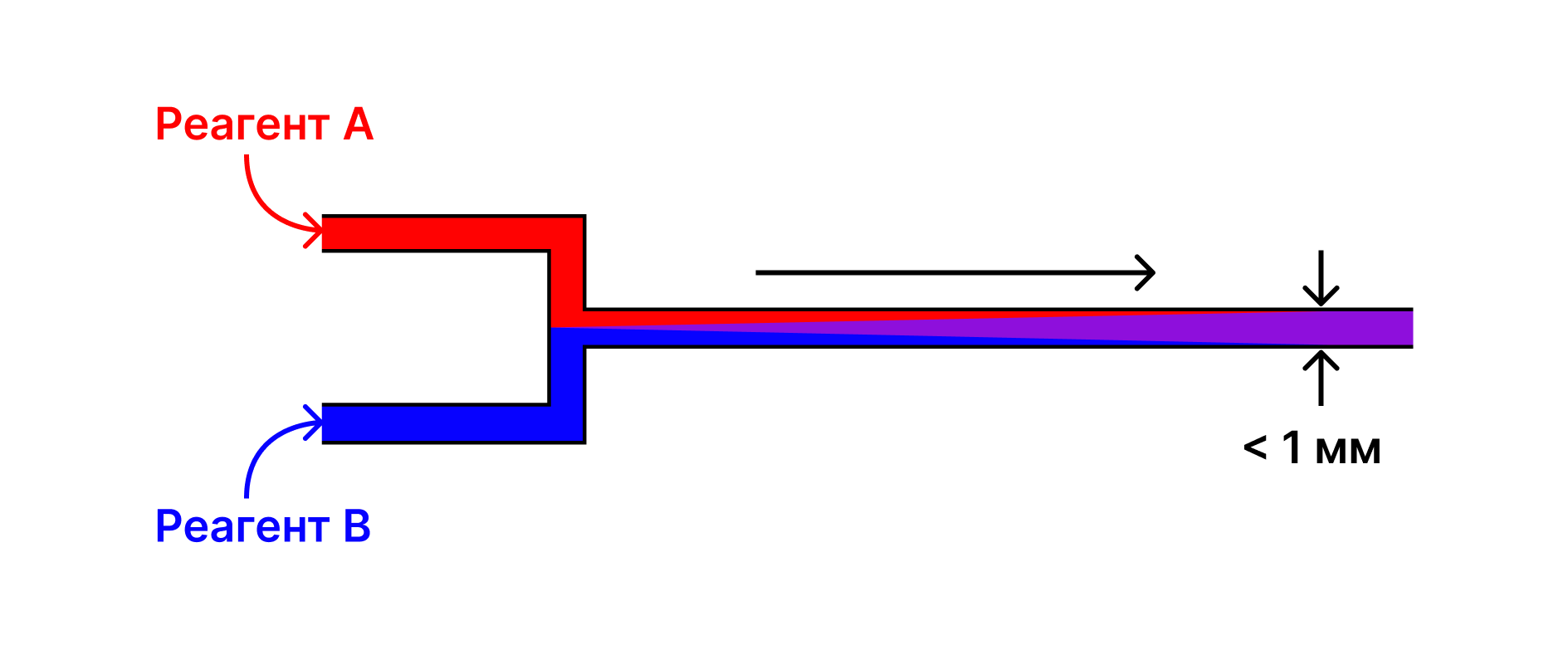
Рисунок 1 - Схема микрореактора с Т-образным смесителем
Примечание: источник [7]
Таблица 1 - Основные типовые характеристики микрореакторов
№ | Характеристики: | Значение: |
1 | Количество потоков жидкости, шт. | 2 и более |
2 | Количество потоков газов, шт. | 1 и более |
3 | Время контакта, мин | 0,2-20 |
4 | Размер каналов, мм | высота 0,1-1 ширина 0,1-1 |
5 | Рабочий объем микроканалов, см3 | До 10 и более |
6 | Материал микрореакторов | нержавеющая сталь, полимерные материалы, стекло, керамика |
7 | Управление системой | Компьютер, контроллер |
8 | Рабочая температура, °С | до 500 |
9 | Рабочее давление, бар | до 25 |
10 | Удельная поверхность, м2/м3 | от 10 000 до 50 000, в то время как у традиционных реакторов достигает только 100 м2/м3. |
11 | Требования к производству | Квалификация персонала должна соответствовать требованиям производства первого и второго класса опасности. Площадка должна быть аккредитована Ростехнадзором. |
12 | Охрана окружающей среды | Отходы 2-го класса опасности |
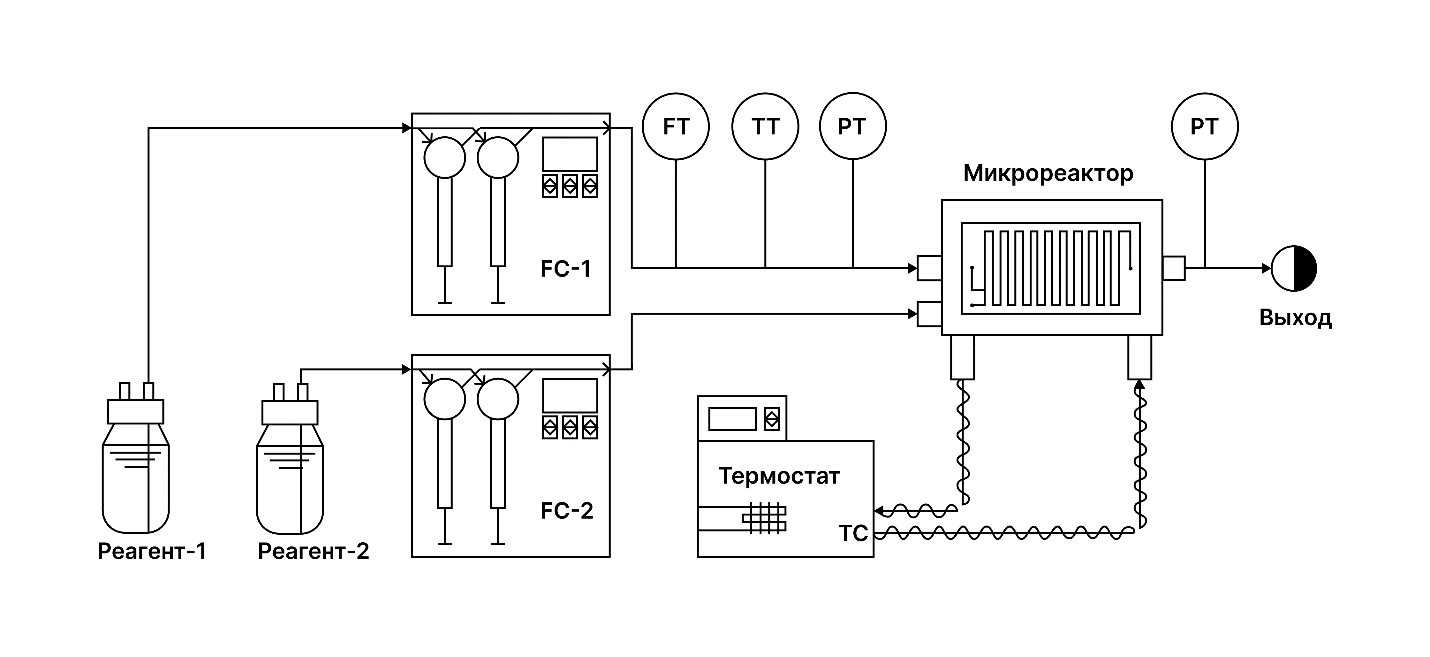
Рисунок 2 - Принципиальная технологическая схема микрореакторной установки
Примечание: FC-1, 2 – насосы высокого давления, FT – датчик расхода, TT – датчик температуры, PT – датчик давления [8]
2. Основные результаты
2.1. Изготовление микрореакторов
Малотоннажные микрореакторы могут быть выполнены в виде капиллярных реакторов или реакторов с чип-формой (рис. 3). Капиллярные реакторы проектируются, когда необходимо учитывать свойства реагентов и продуктов химической реакции, кинетики химического процесса, технологические параметры (высокие температуры и давления). Капиллярные микрореакторы изготавливают из высоколегированных марок стали, титана методами химического травления, 3D-печатью
. В отличие от них, микрореакторы с чип-формой, как правило, проектируются, когда реакция быстрая (менее 1 с) и не требуется учитывать другие параметры. Микрореакторы с чип-формой изготавливают из кремния, стекла или даже некоторых видов пластика, методами травления и литографии , , .![Капиллярный микрореактор (а) и микрореактор с чип-формой (б) [11]](/media/images/2024-06-11/5a8fa9ee-1632-4d6c-bfb2-aea4a5c6eb83.png)
Рисунок 3 - Капиллярный микрореактор (а) и микрореактор с чип-формой (б) [11]
![Общая схема материалов для изготовления микрореакторов [12]](/media/images/2024-06-11/bfbcca12-e9f8-4563-a007-473e57c1958a.png)
Рисунок 4 - Общая схема материалов для изготовления микрореакторов [12]
Микрореакторы из нержавеющей стали: изготавливаются из высокопрочной нержавеющей стали, такой как AISI 316L или AISI 304L (отечественный аналог 03Х17Н14М3 и 08Х18Н10 по ГОСТ 5632-72, соответственно), которая обладает высокой термической и химической стойкостью. Эти микрореакторы могут выдерживать высокие температуры и давления и часто применяются в катализе и гидрогенизации.
Микрореакторы из никеля: никелированные микрореакторы широко используются для проведения газообразных реакций при высоких температурах и давлениях. Никель обладает хорошими термическими и химическими свойствами для работы с агрессивными реагентами.
Микрореакторы из металлов и металлических сплавов имеют ограничения в применимости, из-за шероховатой поверхности, которая образуется при металлообработке, в том числе при 3D-печати (неровности 10 микрон и выше).
Керамические микрореакторы применимы в специфическом химическом синтезе или реакциях, в которых металлические или полимерные системы не могут быть использованы, поскольку керамика обладает особыми свойствами (например, термической и химической стойкостью)
. Тем не менее использование керамических микрокомпонентов, как правило, не является распространенным из-за длительного и дорогостоящего производства элементов, соответствующих спецификациям модели. Основное ограничение – необходимость изготовления керамических элементов с точностью до микрона. Выходом может быть комбинированное производство – стереолитография с керамическим литьем под низким давлением .Микрореакторы для химических процессов, которые не требуют высоких температур и давлений, могут быть изготовлены из таких материалов, как стекло, с покрытием или нет, из графита, различных полимеров.
Стекло является хорошим материалом для изготовления микрореакторов благодаря отличному продвижению химических реагентов по каналу (наименьшее сопротивление среди всех материалов). Стеклянные материалы имеют некоторые ограничения для конструкций реакторов (невысокий нагрев и давление), тем не менее, они подходят для стандартной жидкофазной химической реакции, так как могут выдерживать невысокое давление и температуры, создавая минимальное сопротивление потоку жидкости.
Стеклянные микрореакторы с керамическими нанопокрытиями: такие реакторы обычно изготавливаются из стекла, обладающего хорошей термической и химической стойкостью. Каналы микрореакторов могут быть покрыты керамическими нанопокрытиями, такими как оксид алюминия или оксид кремния (кремнезем), для улучшения их механической прочности и устойчивости к высоким температурам и давлениям.
Микрореакторы с использованием ПДМС используются в производстве топливных элементов
. Из-за дешевизны материала микрореакторы из ПДМС в перспективе могут иметь значительное применение. Полимеры, в целом, пригодны для изготовления микрореакторов различных форм и геометрии каналов, тем не менее, у них есть ограничения: если реакция с высоким экзотермическим эффектом в канале могут развиваться значительные температуры из-за чего некоторые полимеры могут деформироваться.Кремниевые микрореакторы универсальны в отношении условий реакции; например, экзотермические газофазные реакции, как правило, хорошо протекают в них. В кремниевых микрореакторах реакция может протекать даже при относительно высоких температурах (т.е. 600-800 °C)
, а также они обладают равномерной ламинарной гидродинамической структурой потока, несмотря на плохую поверхностную обработку) . Некоторые кремниевые микрореакторы были разработаны для аналитического определения температуры с помощью термочувствительных чипов. Кремниевые микрореакторы позволяют добиваться высокой селективности и высокой конверсии продуктов в различных химических реакциях .Отдельно стоит отметить микрореакторы из пиролитического графита. Графитовые микрореакторы обладают высокой стабильностью при высоких температурах и давлениях. Они широко используются в газификации, при синтезе углеродных наноматериалов и проведении реакций с выделением газа.
В данном разделе рассмотрены основные материалы для производства микрореакторов, которые появились в публикациях за последние 10-15 лет. Выбор материала для микрореактора зависит от конкретной реакции, условий, требований безопасности и сложности метода изготовления.
2.1.2. Методы изготовления
Микрореакторы в химии могут быть получены различными способами в зависимости от конструкции и материалов, используемых для их изготовления. В данном разделе будут рассмотрены методы, которые получили широкое применение в последние 10 лет.
1. Литейный метод. Этот метод включает наполнение формы, обычно сделанной из силикона или стекла, материалом, который затем затвердевает и принимает форму микрореактора
.2. Фотолитография. Этот метод основан на использовании фоторезистов и ультрафиолетового света для создания микроструктур на поверхности чипа. Разработка этих технологий началась в Германии под названием LIGA (литография, гальваника и литье). Этот метод оказался популярным, так как его можно применять ко многим типам материалов: металлы, пластики, композиты. Метод можно разделить на три этапа: (1) перенос рисунка на фотосенсор (который обычно представляет собой материал синтетической смолы), (2) последующее гальваническое покрытие поверхности материала путем удаления некоторых структурных слоев, и (3) фотоизлучение, которое обеспечивается фоторезистом или фотосенсором
.3. Химическое осаждение. Этот метод включает химическое осаждение материала на подложку с использованием химических реакций прекурсора. Данный метод используется в первую очередь для формирования специализированного покрытия на внутренних каналах микрореактора. Также может быть использован для нанесения катализатора на подложку. Для получения микрореакторов могут использоваться такие материалы, как металлы, полимеры или керамика
.4. 3D-печать. Современный метод включает использование специализированных 3D-принтеров для создания микрореакторов заданной формы путем цифрового моделирования. Полимерные материалы или металлические порошки могут быть использованы для 3D-печати микрореакторов
.5. Методы травления. Суть метода – удаление материала с подложки. Различают мокрое и сухое травление. Мокрое травление применимо к стеклу. Стекло Pyrex отлично подходит для мокрого травления. Материалы могут травиться в разных направлениях (горизонтально или вертикально) с разной скоростью. Большое значение имеет скорость травления. Сухое травление – это воздействие на подложку лазером, жестким ультрафиолетом, плазмой. Метод является передовым, применимость осложняется тем, что он оказался дорогостоящим
.6. Метод микромеханической обработки. Наиболее часто встречающийся метод для производства микрореакторов для органического синтеза. Сверление, фрезерование, многократное шлифование. Используются специальные инструменты, такие как алмазные фрезы. В работе
предложено разогревать материал при высоких температурах перед микрообработкой, чтобы придать ему дополнительную гибкость и эластичность.Каждый из этих методов имеет свои преимущества и ограничения, и выбор способа получения микрореактора зависит от результатов проектирования с заданной производительностью и условий протекания химических реакций.
2.2. Проектирование микрореакторов
Современный подход в проектировании микрореакторов состоит в разработке математической модели протекающего химического процесса
. Задачу проектирования микрореактора заданной производительности можно разделить на основные подзадачи:1) задача микросмешения реагирующих компонентов, исходя из физико-химических свойств поступающих реагентов, геометрии и длины канала;
2) расчет необходимой длины канала, исходя из кинетики химического процесса (по сути, расчет времени пребывания с учетом гидродинамики и массообмена) (рис. 5). Фундаментальные и основные математические уравнения для данных задач были подробно описаны в работе
.![Проектирование микрореактора: зона смешения, длина реактора [5]](/media/images/2024-06-11/3689e8e2-12dd-4290-81c0-b165a5a95d65.png)
Рисунок 5 - Проектирование микрореактора: зона смешения, длина реактора [5]
В микрореакторах происходит два типа перемешивания: пассивное перемешивание (диффузия) и активное перемешивание (создание искусственной конвекции). Ламинарный гидродинамический профиль микросмешения (Re < 100) необходим для снижения потери давления в микроканалах
. На данный момент не упоминаются химические насосы, которые способны компенсировать потерю давления в микроканалах (диаметр менее 1 мм) при Re > 10 000. Создание искусственной конвекции за счет изменения геометрии пространства дополнительно увеличивает площадь для диффузионного массообмена. Диффузионный массообмен является основным фактором смешения поступающих реагентов. Общие свойства поступающих реагентов, такие как агрегатное состояние (выделяют основные фазы жидкость-жидкость (L-L) и жидкость-газ (L-G)), плотность, вязкость и скорость потока определяют скорость диффузии в микроканале. Стоит отметить, что даже для фаз, которые имеют нулевую несмешиваемость, необходимо рассчитывать длину и геометрию канала, так как диффузия в микроканалах не происходит мгновенно. Жидкие системы создают межповерхностное натяжение (особенно если речь идет о несмешивающихся жидкостях). При проведении экспериментов в двухфазном потоке жидкость-жидкость при различных расходах и соотношениях расходов с использованием системы вода–циклогексан наблюдались три типичных различных режимах течения: четко выраженный пробковый поток, ламинарный поток и деформированный поток на границе раздела фаз .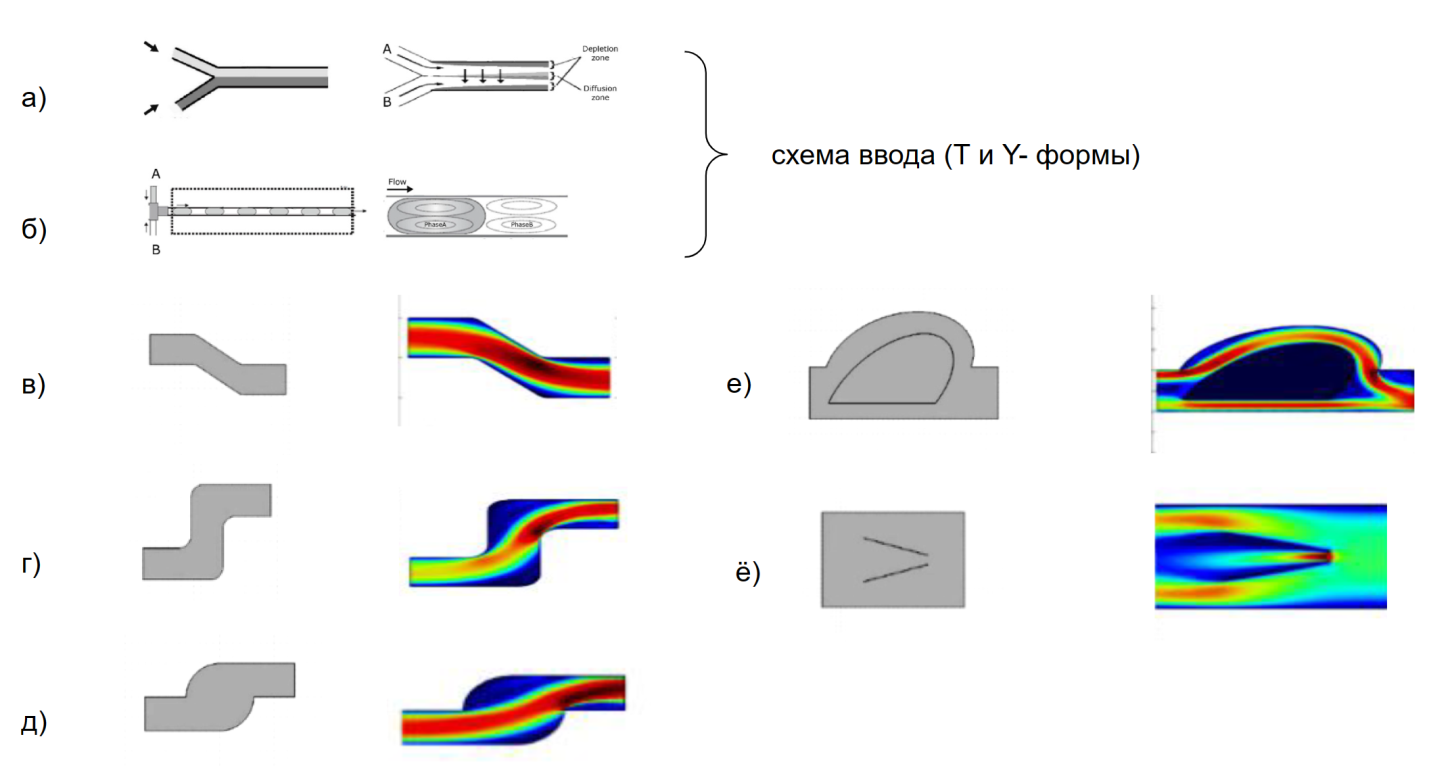
Рисунок 6 - Задача микросмешения:
a) Y-образное смешение; б) T-образное смешение; в – г) варианты Z-образного смешения; д) «Улитка»; е) «Петля»; ж) «Жиклёр»
Примечание: источник [30]
Подробное исследование микросмешения приведено в работе
, в которой проводился численный расчет основных геометрических форм смешения и была предложена оригинальная геометрическая форма, нашедшая свое отражение в патенте . Также есть работы, в которых оригинальная геометрическая форма предложена на основе природных фракталов (рис. 7) . В этой работе предложены различные геометрические формы смешения для платы 40х40 мм на основе природных фракталов (рис. 7), а также проведено сравнение эффективности микросмешения в %.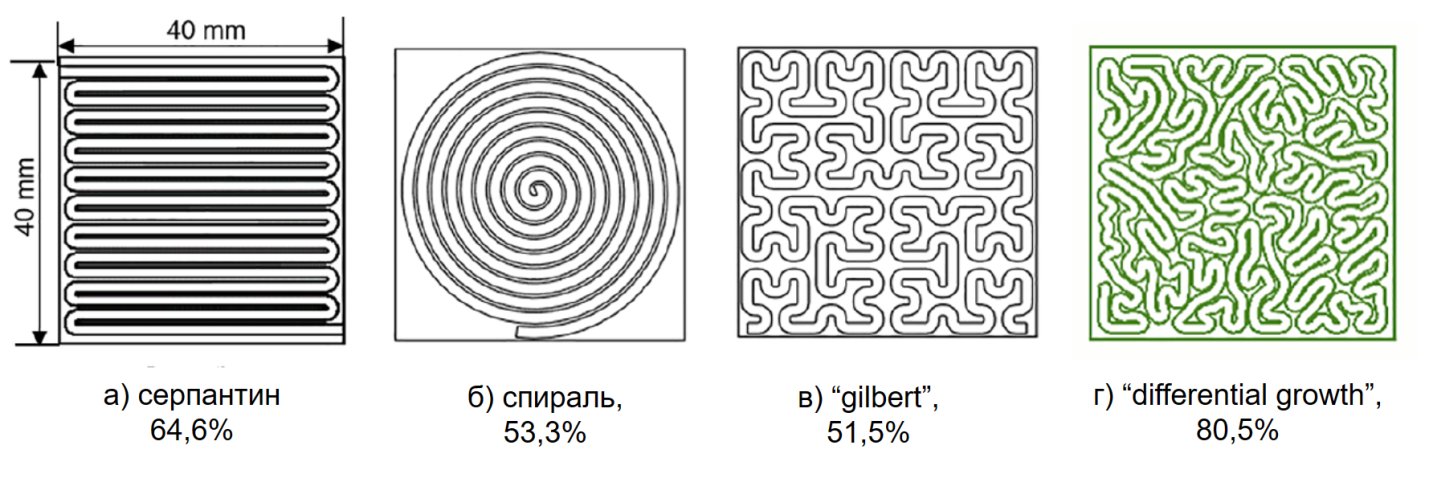
Рисунок 7 - Геометрические формы смешения на основе природных фракталов:
а) серпантин; б) спираль; в) «gilbert»; г) «differential growth»
Примечание: источник [31]
После того, как произведен расчет и подбор элементов микросмешения, необходимо рассчитать длину канала, чтобы обеспечить полное протекание химической реакции. Расчет необходимой длины канала проводят на основе установленной кинетики химического процесса с учетом гидродинамики и массообмена. Также необходимо учитывать последовательность синтеза. На рис. 8 представлены основные схемы проведения химического синтеза в микрореакторых
.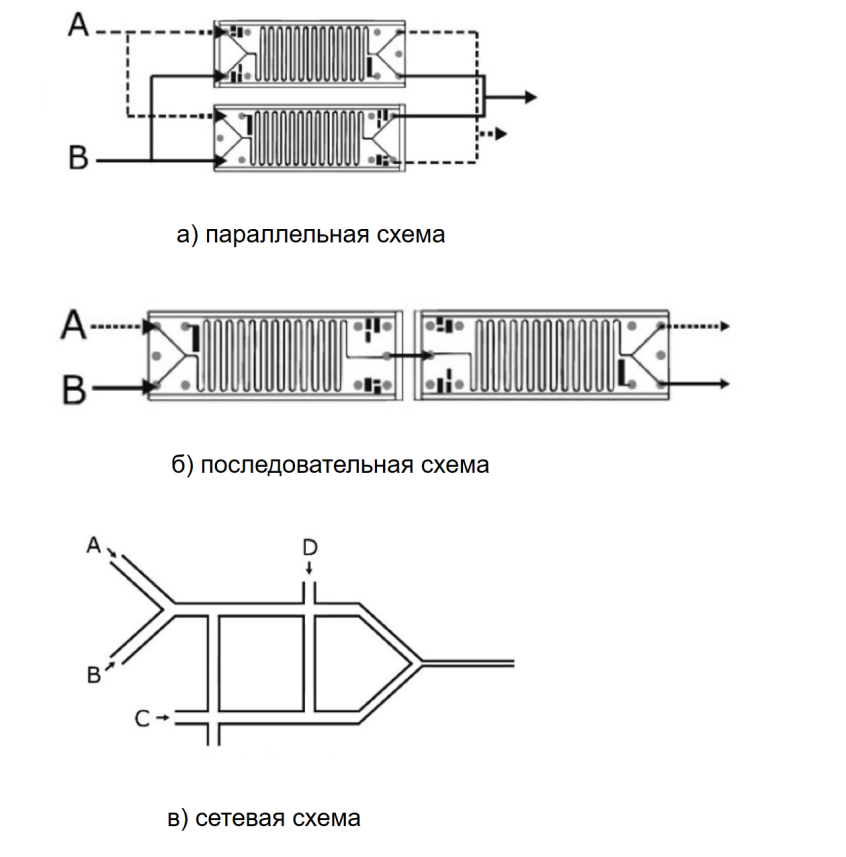
Рисунок 8 - Основные схемы проведения химического синтеза в микрореакторах:
а) параллельная схема; б) последовательная схема; в) сетевая схема
Примечание: источник [8]
При моделировании химических процессов в аппаратах необходимо записывать три основных уравнения балансов: массового, теплового и импульса
. Для типовых химических аппаратов разработан математический аппарат для их расчета (РИВ, РИС, диффузионно-ячеечная модель и др.). Их вывод основан на материальном и тепловом балансе с допущениями по гидродинамическому профилю, по стационарности, усреднению по координате. Если необходимо учесть влияние диффузии, она включается в материальный баланс, отдельно баланс импульса не записывается. модель смешения реагентов также не учитывается при расчетах типовых реакторов.Для химических процессов, протекающих в микроканалах (смешение или смешение + химическая реакция), математические модели для расчета типовых реакторов не подходят, так как данные уравнения не позволяют учесть ряд важных факторов:
- необходимо учитывать связь между скоростью движения реагентов и абсолютным давлением. Профиль скоростей позволяет увидеть наличие застойных зон, которые для микроканалов приобретают основной фактор (поток протекает мимо застойной зоны, не взаимодействуя с ней). Профиль развиваемых давлений позволяет учитывать потери давления в микроканалах, что также является критически важным параметром, так как у современных химических насосов для компенсации потери давления предел 50-200 атм.
- основной гидродинамический поток ламинарный (низкие значения числа Рейнольдса, Re<100) в виде пленочного течения, пробкового или смешанного.
- необходимо учитывать поверхностные силы (силы внутреннего трения), которые более значительны в сравнении с инерционными силами (импульс).
- и, пожалуй, самый важный фактор для расчета процессов в микроканалах – это необходимость получения профилей скоростей, концентраций, температур, давлений в трехмерном (t, x, y) и четырехмерном пространстве (t, x, y, z). Для периодического РИС – это одномерное пространство t (время), для РИВ t, x (время и длина реактора) - двумерное.
Основным уравнением, которое позволяет учесть факторы, приведенные выше, является уравнение Навье - Стокса (1) (выведенное на основе баланса импульса)
. Уравнение Навье - Стокса позволяет связать скорость (w) и абсолютное давление (p), с учетом вязкости (μ), плотности среды (ρ), нестационарности, что позволяет рассчитывать параметры модели в 3-х и 4-х мерном пространстве.В ряде случаев для упрощения решения можно задавать условие неразрывности (2), которое не всегда выполняется в действительности (пленочное течение может переходить в пробковое и наоборот).
Учет кинетики процесса , диффузии
и конвекции
происходит в уравнении (3) переноса массы с химической реакцией.
где cj – концентрация вещества, D – коэффициент диффузии, w – линейная скорость потока, ∇ – оператор набла, ∇2 – оператор Лапласа, νij – коэффициент j-го вещества в i реакции, ri – скорость химической реакции на стадии i.
Перенос тепла с учетом тепловых эффектов реакции – уравнение (4)
где cj – концентрация вещества,
Cpj – теплоемкость вещества j,
a – коэффициент теплоповодности,
w – линейная скорость потока,
∇ – оператор набла,
ri – скорость химической реакции на стадии i,
-∆Hi – тепловой эффект стадии i.
Численно систему уравнений (1-4) решают в специализированных математических программных продуктах: Flowvision, Comsol Multiphysics, Fluent и др
. Так, например, в Comsol Multiphysics есть возможность задавать геометрию пространства, разбивать его методом конечных элементов (МКЭ, также есть методы конечных объемов – МКО), строить сетку решения, подключать специализированные библиотеки Laminar Flow, Transport of Diluted Species (математические уравнения, моделирующие ламинарный поток, массообмен), при необходимости задавать собственные математические уравнения, задавать начальные и граничные условия, получать решения, проводить многопараметрическую оптимизацию. Техническая сложность в реализации решений уравнений (1-4) заключается в том, что численно задача уравнения Навье – Стокса (1) с условием неразрывности (2) решается с хорошей сходимостью по сетке, но при добавлении кинетики, тепло- и массообмена, сходимость резко падает и решение необходимо оптимизировать по сетке, в связи с чем итоговый результат не всегда удовлетворительный.Критериальные уравнения также необходимо учитывать для процессов, протекающих в микроканалах. Обычно различают кинетические, диффузионные, тепловые и гидродинамические критерии подобия.
Кинетические критерии: критерий Дамклера (третье число), характеризует отношение скорости химической реакции к изменению концентрации основного исходного вещества по (высоте) длине канала реакции – уравнение (5).
где L – характеристическая длина, D – коэффициент диффузии, k – константа скорости, n – порядок реакции, C0 – концентрация реагента.
Критерий Маргулиса характеризует отношение константы скорости реакции (k) к скорости реакционного потока (w)– уравнение (6):
Кинетическим критерием, который учитывает влияние температуры (T) на скорость химической реакции, является критерий Аррениуса – уравнение (7):
Диффузионные критерии: диффузионный критерий Пекле, характеризующий отношение скорости потока (w) к приведённой скорости молекулярной диффузии, записывают как уравнение (8)
где – характерный линейный размер (например, высота или радиус реактора);
диффузионный критерий Прандтля уравнение (9)
характеризует отношение вязкостных свойств (μ) и диффузионной способности (D);
критерий Нуссельта характеризует меру отношения константы скорости процесса (k) к приведённой скорости молекулярной диффузии (D), записывают как уравнение (10)
Гидродинамические критерии подобия: Рейнольдса , Фруда
Эйлера
, а также тепловые Нуссельта
, Прандтля
.
Для масштабирования химического процесса используются критериальные уравнения, а также первичный подбор параметров для схожих процессов (например, для типовых процессов – гидрирование, нитрование, окисление, ацилирования и др., см. Таблицу 2).
2.3. Типы химических реакций
Согласно отчету Еврокомиссии за август 2006 года по производству средне- и малотоннажной химии
, количество используемых процессов (unit processes) и операций (unit operations) в малотоннажной химии (fine chemicals) остается относительно небольшим.Основные процессы и операции перечислены в таблице 2, которая не является исчерпывающей.
Таблица 2 - Типовые процессы и операции в малотоннажной химии
№ | Типовой процесс | Типовая операция |
1 | Ацилирование | Загрузка реагентов и растворителей |
2 | Алкилирование | Инертизация |
3 | Карбоксилирование | Синтез в реакторе |
4 | Карбоксиметилирование | Выгрузка реакционной массы |
5 | Конденсация | Кристаллизация |
6 | Диазотизация и модификация диазогруппы | Фильтрация |
7 | Этерификация | Промывка |
8 | Галогенирование | Сушка |
9 | Нитрование | Экстракция |
10 | Окисление | Диализ |
11 | Перегруппировки | Абсорбция |
12 | Восстановление | Фазовое разделение |
13 | Сульфирование | Адсорбция |
14 | Сульфонирование | Дистилляция |
15 | Аминирование | Колонное разделение |
16 | - | Очистка оборудования |
17 | - | Регенерация растворителей |
Все процессы и операции, приведенные в таблице 2, определяют экономику конечного продукта. Не во всех типовых процессах необходимо использовать технологию микрореакций.
Когда мы используем технологию микрореакций:
· быстрая кинетика реакции < 10 мин,
· реакции, чувствительные к смешению,
· длительное время дозирования или контролируемое дозирование,
· селективность зависит от интенсивности пермешивания,
· реакция чувствительна к температуре,
· селективность падает при масштабировании в больших сосудах (теплопередача),
· сильно экзотермическая реакция,
· автокаталитическая реакция,
· скорость реакции зависит от концентрации продукта,
· высокая активность реагента, катализатора или растворителя.
· образование нежелательного побочного продукта.
Общепринятая классификация реакций в малотоннажной химии по скорости химической реакции :
1) Реакции типа А:
• Очень быстро (< 1 с),
• Контролируется процессом смешения,
• Выход увеличивается за счет лучшего перемешивания / теплообмена.
2) Реакции типа B:
• Быстрая реакция (от нескольких секунд до 10 минут),
• Преимущественно управляется кинетическими факторами,
• Для увеличения выхода необходимо избегать перегрева.
3) Реакции типа С:
• Медленная реакция (> 10 мин),
• Периодические процессы с термической опасностью,
• Повышенные требования к безопасности,
• Нужна интенсификация.
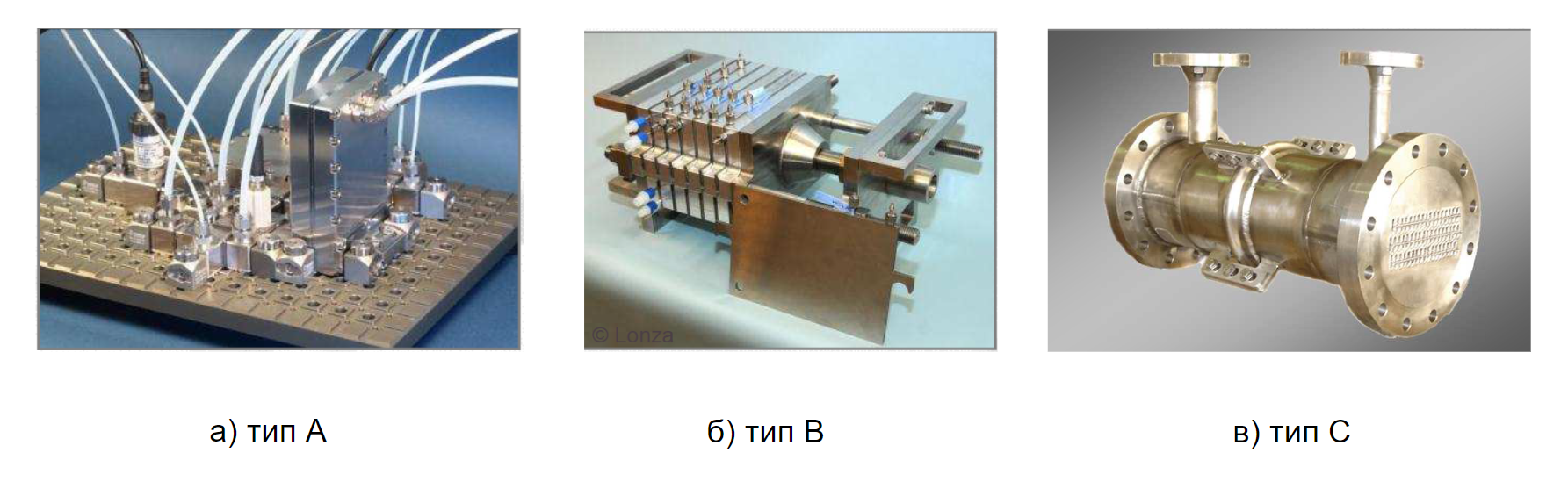
Рисунок 9 - Микрореакторы для разных типов реакций:
а) тип A – очень быстрые реакции (<1 c); б) тип B – быстрые реакции (от нескольких секунд до 10 минут); в) тип C - медленная реакция (> 10 мин)
Примечание: источник [1]
· «Смотрим» на химию (определяем тип реакции, кинетику процесса),
· Проводим реакцию при малых скоростях потока в микроканалах,
· Тестируем различные геометрии каналов,
· Оптимизация.
Последние два этапа проводят, численно моделируя процесс в специализированных программах.
2.4. Области применения микрореакторов
Развития технологии микрореакций началось с высоко экзотермических и опасных химических процессов (specialty chemistry, специальная химия). Далее, уже подходили к типовым процессам малотоннажного синтеза (fine chemicals, малотоннажная химия).
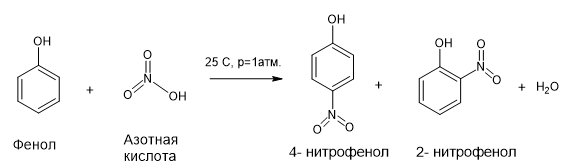
Рисунок 10 - Схема синтеза нитрования фенола
Примечание: источник [35]
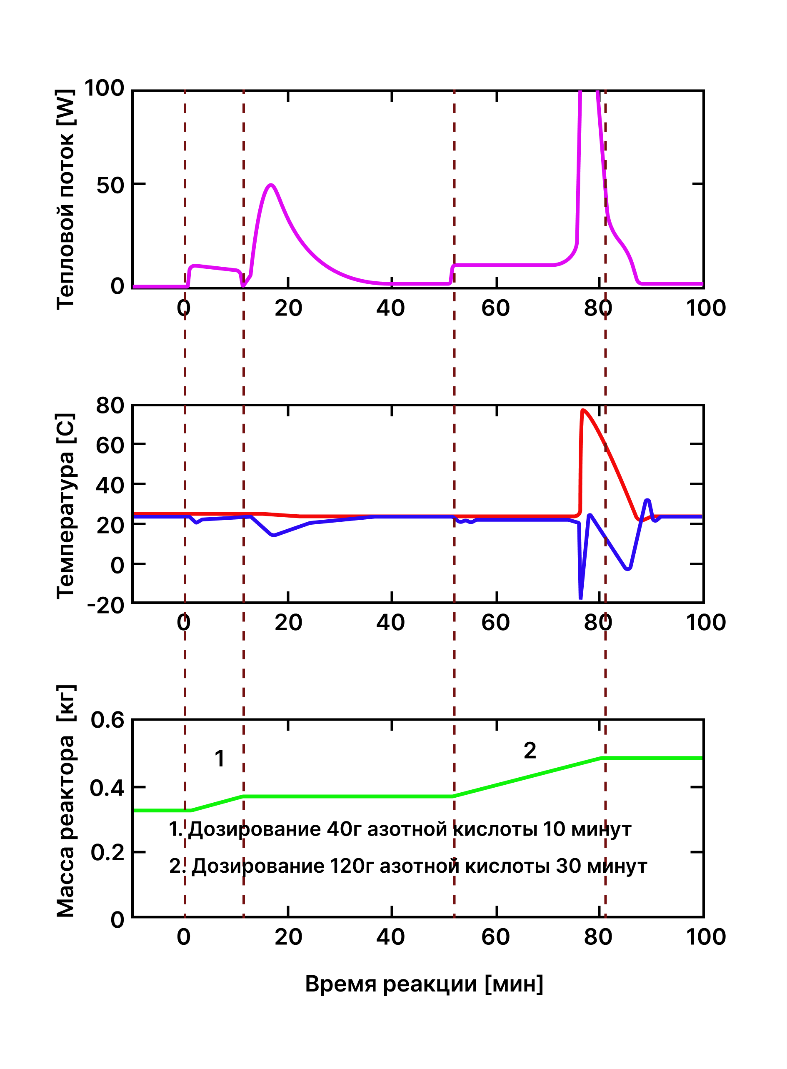
Рисунок 11 - Реакция нитрования фенола в микрореакторе: рост температуры не превышает 60 °С
Примечание: источник [35]
3. Заключение
В работе рассмотрены основные принципы проектирования, изготовления и применения микрореакторов. За последние 30 лет технология микрореакций прошла путь от применения для высокоэкзотермических и высокотоксичных (специальная химия) до типовых реакций в малотоннажной химии. На текущий момент мировой рынок микрореакторных технологий оценивается в 15-20 млрд. $. В работе дано определение микрореактора как устройства, в котором протекает химическая реакция в капиллярных каналах (менее 1 мм). Даны основные требования к производству микрореакторов (таблица 1). Микрореакторы по исполнению делят на капиллярные и с чип-формой (рис. 3). Для капиллярных микрореакторов основной материал изготовления – нержавеющая сталь с добавками никеля (более 7%), для чип-формы – стекло, керамика, кремний. Для капиллярных каналов основной метод изготовления – микромеханическая обработка (фрезерование, сверление, многократное шлифование) с использованием специальных инструментов, такие как алмазные фрезы. Также популярность завоевывает 3D-печать металлическим порошком. Технология 3D-печати металлических микрореакторов имеет ряд технических сложностей таких, как спекаемость порошка, подбор состава порошка, сложности с мехобработкой, образованием закрытых пор. Для микрореакторов с чип-формой основной метод изготовления – мокрое и сухое травление подложки, а также фотолитография. Оба метода являются технически сложными и дорогими в исполнении. Также за последние 10 лет разработаны математические модели процессов, протекающих в микрореакторах, которые позволяют решать 2 основные задачи: микросмешения и химической реакции с диффузией. Представлены основные типы смесителей (рис. 6), их комбинация, основные последовательно-параллельные схемы синтеза (рис. 8). Отражена возможность проведения основных типовых реакций с помощью технологии микрореакций на примере реакции нитрования фенола. В ближайшие 10 лет в малотоннажной химии технология микрореакций будет определяющей.