ВЛИЯНИЕ ДИНАМИЧЕСКИХ ХАРАКТЕРИСТИК СТАНКА НА КАЧЕСТВО ОБРАБАТЫВАЕМОЙ ПОВЕРХНОСТИ
Каймин В.Г.1, Сабиров Ф.С.2
Магистрант, д.т.н., профессор. Федеральное государственное бюджетное образовательное учреждение высшего профессионального образования Московский государственный технологический университет «СТАНКИН» кафедра «Станков»
ВЛИЯНИЕ ДИНАМИЧЕСКИХ ХАРАКТЕРИСТИК СТАНКА НА КАЧЕСТВО ОБРАБАТЫВАЕМОЙ ПОВЕРХНОСТИ
Аннотация
Данная научно-исследовательская работа рассматривает возможность получения высоких показателей шероховатости (Ra 0,20) путем резания лезвийным инструментом конической поверхности сложной детали. Деталь имеет ряд особенностей: коническая поверхность расположена во внутренней полости, допуск радиального биения составляет 0,03 мм, малые габариты (11х18 мм), а также сложность подвода режущего инструмента. Ранее высокие показатели шероховатости внутренней конической поверхности детали обеспечивались ручной доводкой после токарной обработки путем притирки. Такой способ доводки весьма трудоемкий и давал большой процент брака. Объектом исследований являются колебания и вибрации металлорежущего станка.
Ключевые слова: металлообработка, диагностика станков, вибрационный контроль, вибродиагностика.
Kaymin V.G.1, Sabirov F.S.2
Master student, PhD, professor. Federal State budget educational institution of Higher Professional Education, Moscow State Technical University “STANKIN” “Machine-tools” department
EFFECT OF DYNAMIC MACHINE-TOOL FEATURES FOR QUALITY OF MACHINING SURFACE
Abstract
This research scientific work examines the opportunity of receiving high roughness values (Ra 0, 20) by cutting tapered surface of one of the detail with a help of edge tool. The detail has a number of specific features: the tapered surface is located in the inner chamber, radial runout tolerance is 0,03mm, small size (11х18 мм), and complexity of cutting tool approaching. Formerly, high roughness values of inner tapered surface of a detail were achieved by bench finishing (grinding) after the lathe machining. This way is quite laborious and it gives a large amount of throw-out. The object of research is fluctuations and vibration of the machine tool.
Keywords: Machine-tools, Diagnostics of machine-tools, vibration control, vibration diagnostics.
This research scientific work examines the opportunity of receiving high roughness values (Ra 0,20) by cutting tapered surface of one of the details (Fig.1) with a help of edge tool. The detail has a number of specific features: the tapered surface is located in the inner chamber, radial runout tolerance is 0,03mm, small size (11х18 мм), and complexity of cutting tool approaching.
Formerly, high roughness values of inner tapered surface of a detail were achieved by bench finishing (grinding) after the lathe machining. This way is quite laborious and it gives a large amount of throw-out.
The problem arise how to process the tapered surface on the machine-tool together with processing of inner surfaces, avoiding finishing operations. Machined material – stainless steel. Recommended cutting speed – 90mm \min
During the process of details geometry generation the roughness appears on their surfaces- a range of interchanged baffles and holes which have comparatively small size. Sometimes roughness is a track of cutter or another cutting instrument, it may also appear due to vibrations during the cutting process, or due to the force vibrations of a machine-tool. Surface roughness is one of the basic geometric characteristics of details surface quantity, it influences on operational characteristics of the machine. [1]
Fig. 1
It is impossible to process tapered surface on the lathe machines we have now due to the limited spindle rotational speed( lathe machine has rotational speed of 4000 rpm and the speed of 8000 rpm is needed) The idea of tapered surface processing on the milling machine with CNC model MDV 50811appeared , the subproduct is fixed on mainspindle and the boring tool is fixed on the table. Machine-tool has well balanced spindle and frequency range of 0-15000rpmThe evaluation of roughness values was made according to the profilographs of processed details surface which is done with a help of roughness check station Hommel Tester T8000 (Fig 2)The station is made for determination of most roughness parameters and surface contours according to the nowadays standards. One of the received profilographs is shown on the Fig 3.
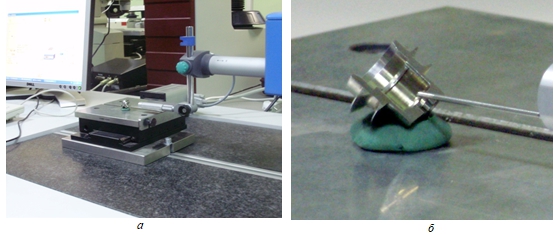
Fig.2 - General view of roughness check station( a) and detail in check (b)
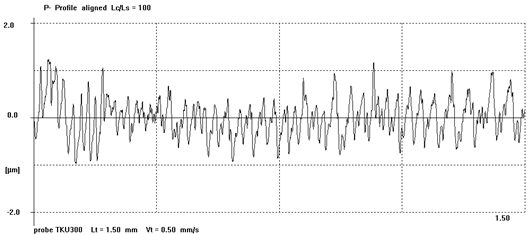
Fig. 3 - Profilograph of pattern conic surface which was processed on milling machine with CNC without coolant cutting fluid
Cyclic errors of profile are seen distinctly on the profilograph, they are connected with elastic system elements oscillation which happens during processing. Frequency characteristic of elastic system, vibration spectrum, envelope vibration spectrum by the procedure with a help of program analysis which is shown on fig 3 are used for distinguishing of vibration sources. Vibration spectrum which is shown on Fig 4 indicates cutter oscillations with frequency 8,6 khz. Measures for avoiding cutter oscillations allowed conducting further processing without vibrations.
Fig. 4 - Vibrations spectrum (vibrational acceleration of cutter during cone cutting)
Taper turning with constant cutting speed i.e., with variable spindle speed rotation gives worse results than cutting with constant speed which is equivalent to the mean diameter of the taper .
During cutting with constant cutting speed ( stepless frequency variation speed with diameter changing) the following results were received: : Ra=0.29 um, Rz=1.71 um, Rmax=2.00 um.
Cutting with constant speed equivalent to 90 m\min with mean diameter of tapered surface gives the following results: Ra=0.13 um, Rz=0.83um, Rmax=1.28 um.
The data received from this research allows to set processing modes which provide given roughness during edge cutting machining of tapered surface of details without any additional processing.
References
- Editing Bushuyeva V.V. Metallorezhushchiye stanki {Metal-cutting machines}. 2011. 608 p.
- Kudinov V.A. Dinamika Stankov { Machine-tools Dynamics }. Moscow : Mashinostroyeniye , 1967. 398 p. (rus)
- Kozochkin M.P. , Maslov A.R. , Sabirov F.S. Ispytaniya i diagnostika tekhnologicheskogo oborudovaniya {Testing and Diagnostics of Manufacturing Machinery}. Study guide. Moscow: R C MSTU “Stankin” 2012. 250 p (rus)