РАЗРАБОТКА ТЕХНОЛОГИИ И ОБОРУДОВАНИЯ ДЛЯ РАЦИОНАЛЬНОГО ИСПОЛЬЗОВАНИЯ ТЕКСТИЛЬНЫХ ОТХОДОВ
РАЗРАБОТКА ТЕХНОЛОГИИ И ОБОРУДОВАНИЯ ДЛЯ РАЦИОНАЛЬНОГО ИСПОЛЬЗОВАНИЯ ТЕКСТИЛЬНЫХ ОТХОДОВ
Abstract
Рассматривается технологический процесс регенерации волокон из текстильных отходов вплоть до получения одиночных волокон на основе использования в технологической линии разработанного оборудования для дополнительного разрыхления, рассортировки волокон, их распределения и транспортировки. Разработанное оборудование позволяет более эффективно использовать регенерированные волокна в общем сырьевом балансе текстильной промышленности, а также расширить ассортимент текстильной продукции. Выведено дифференциальное уравнение, моделирующее процесс аэросъема волокна потоком воздуха с зуба гарнитуры вращающегося пильчатого барабана. Разработана технология изготовления композиционного материала из регенерированных одиночных волокон. Использование разработанного оборудования для регенерации волокон из текстильных отходов в технологических линиях и способа получения многослойных композиционных материалов в текстильной промышленности поможет бизнесу занять новые рыночные ниши, организовать производство новых материалов различного назначения.
1. Введение
В целях экономии натурального текстильного сырья на фоне значительного снижения его объемов разрабатываются новые малоотходные и безотходные технологии, новое оборудование и активно развиваются направления рационального использования текстильных отходов, в том числе производство из них пряжи больших линейных плотностей и нетканых материалов
, , .Пряжа больших линейных плотностей используется для производства тканей, которые используются при изготовлении специальной одежды, средств защиты рук, верха специальной обуви, укрывных палаток, пологов, рюкзаков, тентов и т.д.
Рост объемов производства нетканых и композиционных материалов обусловлен значительным ростом спроса на текстильную продукцию специального назначения.
Производство пряжи, нетканых материалов из бывших в употреблении изделий и текстильных отходов обеспечивает улучшение экологической обстановки окружающей среды, рациональное использование натурального сырья, создание дополнительных рабочих мест
, , .Выпуск качественного регенерированного волокна невозможен без четкой организации технологического процесса и использования современного оборудования. Полный технологический цикл получения регенерированных волокон из текстильных отходов состоит из следующих этапов: приемка и контроль качества сырья, рассортировка сырья по видам материалов, удаление фурнитуры и мелких деталей, получение регенерированных волокон, прессование, маркировка и упаковка, складирование и формирование партий, хранение готовой продукции.
Однако получение регенерированных волокон и использование их в производстве пряжи показывает отрицательное воздействие комплексов волокон, которые содержатся (более 30%) в волокнистой массе после регенерации, на протекание технологического процесса прядения на пневмомеханических и кольцепрядильных машинах.
Поэтому актуальной становится необходимость разработки технологического процесса получения одиночных волокон после регенерации на основе создания оборудования для максимального выделения из волокнистой массы одиночных волокон благодаря обеспечению повторного расщепления комплексов волокон.
2. Основные результаты
Цель работы заключается в повышении эффективности технологических процессов получения текстильной продукции для различных отраслей народного хозяйства с использованием регенерированных волокон из текстильных отходов на основе разработки новых технологий, способов и технологического оборудования.
Научная новизна работы заключается в развитии теории технологических процессов разрыхления, очистки и съема волокнистой массы.
Выполнены теоретические исследования процессов разрыхления и очистки волокнистой массы в зоне разрыхления разработанного оборудования для дополнительного разрыхления, рассортировки волокон, их распределения, а также процесса очистки комплексов волокон в зоне их транспортирования для повторного разрыхления.
Результатом теоретических исследований стало получение дифференциального уравнения, моделирующего процесс аэросъема волокна потоком воздуха с зуба гарнитуры вращающегося пильчатого барабана.
В соответствии со вторым законом Ньютона движение волокна моделируется следующей системой обыкновенных дифференциальных уравнений :
где Mv – масса волокна;
N – сила нормального давления;
β – угол наклона передней грани зуба;
ω – угловая скорость барабана;
RB – радиус барабана;
Fа – аэродинамическая сила;
g – ускорение свободного падения;

Рисунок 1 - Схема сил, действующих на волокно при аэросъеме
Обозначим через k коэффициент трения волокна о сталь. Так как Fт=kN, то
Очевидно, что решение уравнения (3) следует получить при следующих начальных условиях:
1) при t = 0 центр масс волокна находится в точке y = 0;
2) при t = 0 скорость центра масс волокна равна нулю .
Далее условия для решения (3) выбираем из следующих соображений. Обозначим дугу аэросъема через ε, а время аэросъема – Δt. За время Δ𝑡 пильчатый барабан повернется на угол 𝜀, а волокно переместится по рабочей грани зуба от основания зуба до его кончика, то есть на расстояние 𝑙𝑝.
где hz – высота зуба.
Следовательно, задача численного моделирования заключается в том, что, задаваясь необходимым значением величины дуги аэросъема ε, подобрать такое значение расхода воздуха в канале аэросъема и такое его сужение, чтобы за время Δt = ε/ω центр масс волокна преодолел расстояние, равное lp.
В настоящее время в Ивановской области появилось несколько новых предприятий, которые занимаются переработкой текстильных отходов с целью получения регенерированных волокон.
На рисунке 2 представлен вид текстильных отходов. Процесс рассортировки сырья по видам материалов, является важным этапом технологического процесса получения регенерированных волокон, так как от качества выполнения рассортировки сырья зависит качество регенерированных волокон.
Для резки текстильных отходов на предприятиях установлены ротационные резальные машины модели АС40 и модели АС 39 фирмы «Befama» (Польша).
Ротационная резальная машина модели АС 39 предназначена для разрезания текстильных отходов на определенную длину. После резки текстильных отходов на определенную длину они попадают на выводной транспортер с последующей подачей к выпускным валам. Затем нарезанные отходы попадают в многобарабанную щипальную машину, которая предназначена для разволокнения текстильных отходов любого вида и волокнистого состава на отдельные волокна и комплексы волокон.
Подача текстильных нарезанных отходов к многобарабанной щипальной машине может осуществляться с помощью питающих устройств. Разрыхленный волокнистый материал выводится из щипальной машины либо вентилятором, либо с помощью обеспыливающего отводящего устройства. Обеспыливающее устройство содержит два перфорированных барабана, из внутреннего пространства которых отсасывается воздух, пару выпускных валиков и отводящий транспортер.
В процессе расщипывания и очистки волокнистой массы необходимо обеспечить щадящий режим работы оборудования, предохраняющий волокна от механического повреждения.

Рисунок 2 - Сырье - текстильные отходы
В таблице 1 представлена характеристика выхода волокнистой смеси после регенерации волокон из текстильных отходов.
Таблица 1 - Характеристика состава волокнистой смеси после регенерации волокон из текстильных отходов
Наименование составных частей волокнистой смеси после регенерации | Характеристика волокнистой смеси после регенерации |
Выход одиночного волокна, % | 51,0 |
Выход комплексов волокон, % | 38,0 |
Короткие одиночные волокна и комплекс волокна, % | 8,0 |
Нескладируемые отходы, % | 3,0 |
Как вытекает из таблицы 1, волокнистая смесь после регенерации содержит не только одиночные волокна, но и комплексы волокон.
Следует отметить, что на предприятиях по переработке текстильных отходов, процентное соотношение составляющих примерно одинаковое
.Полученная смесь, состоящая из одиночных и комплексов волокон, в основном используется для изготовления нетканых материалов.
На одном из предприятий по переработке текстильных отходов организовано производство по изготовлению нетканых материалов вязально-прошивным способом. Такие нетканые материалы обычно используются в тех случаях, когда нет особых требований к их качеству. Так, нетканые материалы, полученные вязально-прошивным способом, продают в виде ветоши.
Для обеспечения более эффективного использования регенерированных волокон в общем сырьевом балансе текстильной промышленности и расширения ассортимента текстильной продукции из них необходимо осуществлять максимальное и более качественное расщепление комплексов волокон до получения одиночных волокон.
В связи с этим нами разработана технологическая линия для регенерации волокон из текстильных отходов, обеспечивающая максимальный выход одиночных волокон.
Схема разработанной технологической линии переработки текстильных отходов и получения регенерированных волокон представлена на рисунке 3.
Как следует из рисунка 3, в технологическую линию для переработки текстильных отходов и получения регенерированных волокон включено оборудование для дополнительного разрыхления, рассортировки волокон, их распределения и транспортировки
.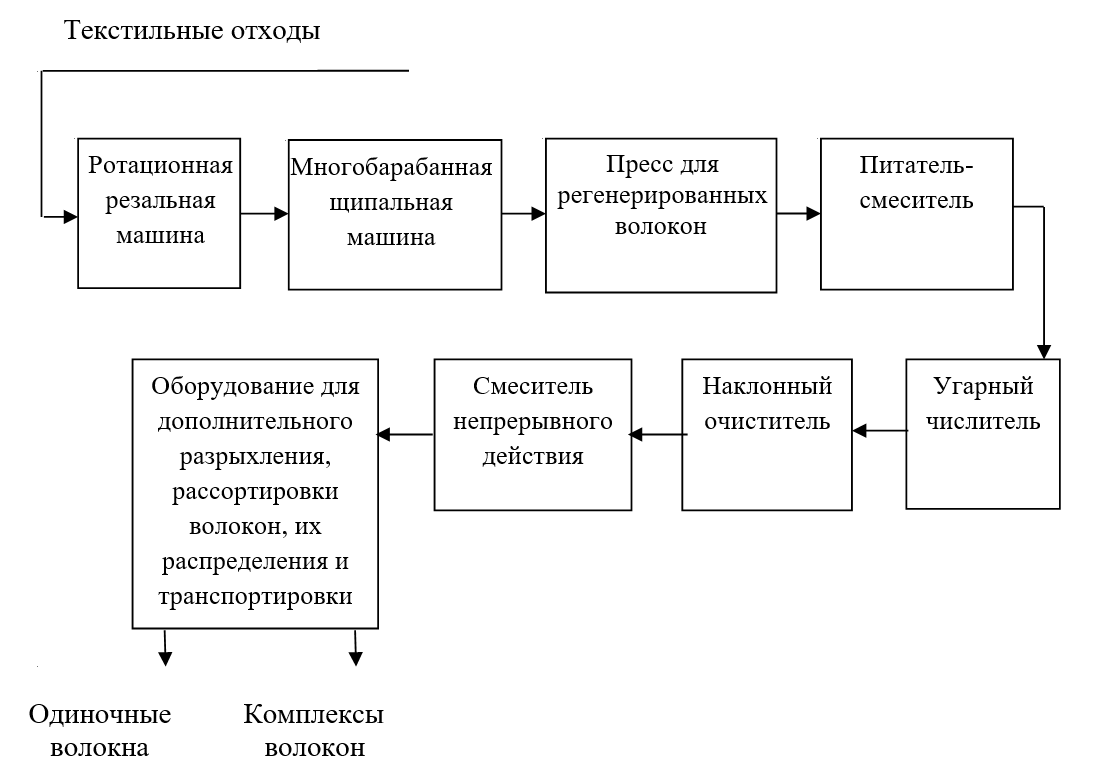
Рисунок 3 - Схема разработанной технологической линии переработки текстильных отходов и получения регенерированных волокон
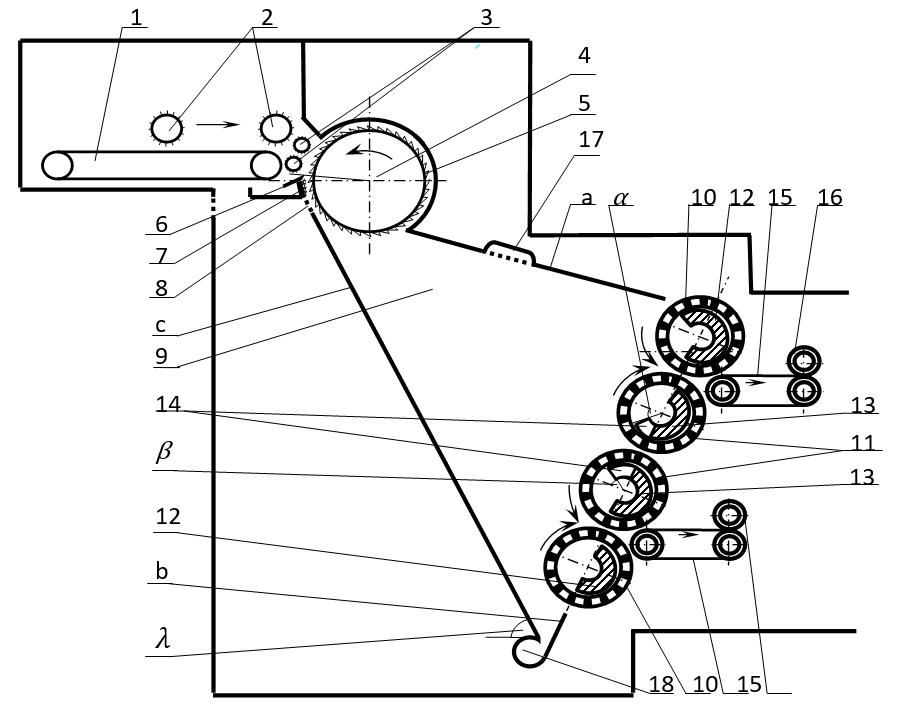
Рисунок 4 - Технологическая схема оборудования для дополнительного разрыхления, рассортировки волокон, их распределения и транспортировки:
1 - транспортер; 2 - прижимные валики; 3 - питающие валики; 4 - пильчатый рабочий барабан; 5 - пильчатая гарнитура; 6 - сороотбойный нож; 7 - неподвижный чешущий сегмент; 8 - щель для поступления воздушного потока; 9 - распределяющая камера; 10, 11 - попарно сетчатые барабаны; 12, 13 - неподвижные сегменты с пневмоотсосом; 14 - подвижные заслонки; 15 - транспортеры; 16 - самогрузочные контролирующие валики; 17 - верхняя контролирующая зона обеспыливания; 18 - узел сороудаления; а, b, с - стороны сечения распределяющей камеры; α, β - углы раскрытия зоны пневмоотсоса
Были проведены производственные исследования по оценке эффективности работы установленного в технологической линии разработанного оборудования для дополнительного разрыхления, рассортировки волокон, их распределения и транспортировки.
Для этого были исследованы длины волокон, взятые на многобарабанной щипальной машине и на входе в камеру оборудования для дополнительного разрыхления, рассортировки волокон, их распределения и транспортировки.
В таблице 2 представлена характеристика выхода состава волокнистой смеси после регенерации текстильных отходов по двум вариантам: первый – с включением в технологическую линию оборудования для дополнительного разрыхления, рассортировки волокон, их распределения и транспортировки и второй – без включения в технологическую линию оборудования для дополнительного разрыхления, рассортировки волокон, их распределения и транспортировки.
Таблица 2 - Характеристика выхода состава волокнистой смеси после регенерации текстильных отходов
Наименование составных частей волокнистой смеси после регенерации | С включением оборудования для дополнительного разрыхления, рассортировки волокон, их распределения и транспортировки | Без включения оборудования для дополнительного разрыхления, рассортировки волокон, их распределения и транспортировки |
Выход одиночного волокна, % | 65,3 | 50,5 |
Выход комплексов волокон, % | 21,7 | 37,7 |
Угары в зоне сороудаления, % | 6,5 | 5,9 |
Угары в верхней зоне обеспыливания, % | 1,0 | 1,0 |
Угары в верхнем и нижнем сетчатых барабанах, % | 5,5 | 4,9 |
Процент выхода угаров в зонах сороудаления и в верхней и нижней зонах сетчатых барабанов можно регулировать в зависимости от требований к качеству одиночных регенерированных волокон и соответственно к качеству композиционных материалов.
Целью проведения выше указанных исследований явилась экспертная оценка эффективности технологических режимов разволокнения текстильных отходов на различных участках линии регенерации волокон для выработки рекомендаций производственникам.
Для этого были выбраны следующие зоны исследования на технологической линии разволокнения:
- после третьего щипального барабана;
- после шестого щипального барабана;
- на входе в камеру оборудования для дополнительного разрыхления, рассортировки волокон, их распределения и транспортировки.
Для всех образцов по указанным зонам определялись следующие показатели:
- выход одиночных волокон;
- количество комплексов волокон;
- наличие сора;
- характеристика длины волокна.
Оценка образцов волокнистой массы проводились при влажности 65% и температуры 24°С, после их выдержки в течение 48 часов. Оценка засоренности волокна проводились по методике ручного разбора.
Испытания по определению характеристики длины одиночных регенерированных волокон проведены на приборе Жукова.
Состав волокнистой массы по вышеуказанным зонам:
а) после третьего щипального барабана:
- волокно, % 30,1;
- комплексы волокон, % 67,4;
б) после шестого щипального барабана:
- волокно, % 51,2;
- комплексы волокон, % 38,6;
в) на входе в камеру оборудования для дополнительного разрыхления, рассортировки волокон, их распределения и транспортировки:
- волокно, % 65,3;
- комплексы волокон, % 21,7;
- Угары в зоне сороудаления 6,5.
Средняя длина волокна по вышеуказанным зонам:
а) после третьего щипального барабана:
- средняя длина волокна, мм 21,1;
б) после шестого щипального барабана:
- средняя длина волокна, мм 19,4;
в) на входе в камеру оборудования для дополнительного разрыхления, рассортировки волокон, их распределения и транспортировки:
- средняя длина волокна, мм 18,8.
Технологический процесс получения одиночных волокон осуществляется следующим образом.
Регенерированные волокна в виде кип подаются к угароочищающему агрегату УО-1, содержащему питатель-смеситель ПС-1, угарный числитель ЧУ-2, наклонный очиститель ОН-6-2, смеситель непрерывного действия СН-3У. Накопленные в смесителе непрерывного действия СН-3У регенерированные волокна подаются на разработанное оборудование для дополнительного разрыхления, рассортировки волокон, их распределения и транспортировки (рис. 3).
Таким образом, благодаря использованию в технологической линии разработанного оборудования для дополнительного разрыхления, рассортировки волокон, их распределения и транспортировки обеспечивается поступление на чесальную машину только одиночных волокон. Полученный на чесальной машине прочес, состоящий из одиночных волокон, можно использовать для получения новых видов более качественных текстильных материалов , .
Полученные регенерированные волокна были использованы для изготовления многокомпонентного композиционного материала вязально-прошивным способом.
Технологический процесс получения волокнистого холста для многокомпонентного композиционного материала вязально-прошивным способом осуществляется следующим образом.
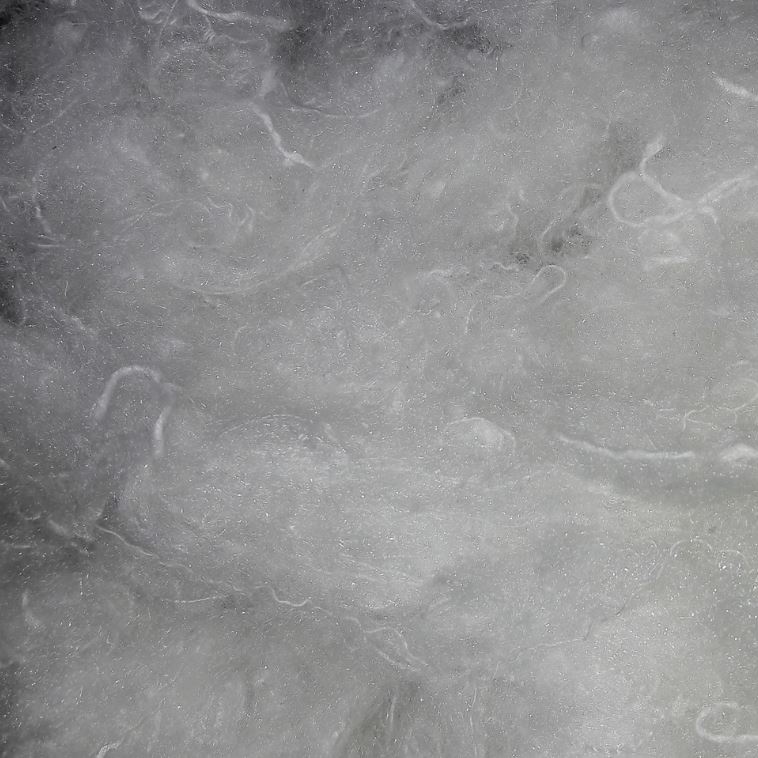
Рисунок 5 - Регенерированные волокна
На малогабаритной чесальной машине ЧММ-14Н происходит переработка волокнистой массы и получение прочеса. Она установлена в чесально-вязальном агрегате АЧВ-3 для получения нетканого материала.
Кроме того, в состав чесально-вязального агрегата АЧВ-3 входит преобразователь прочеса ПП-180 и вязально-прошивная машина ВП-3.
На преобразователе прочеса ПП-180 происходит получение волокнистого холста необходимой толщины и ширины посредством многократного сложения элементарной ватки-прочеса, снимаемой со съемного барабана чесальной машины.
Полученный на преобразователе прочеса холст с определенными поверхностной плотностью и шириной направляется на транспортер для сложения с текстильными материалами (ткань, трикотаж, спанбонд) и образования многослойного материала, состоящего из двух слоев материала для армирования и холста. Текстильные материалы для армирования располагаются с нижней и верхней стороны холста.
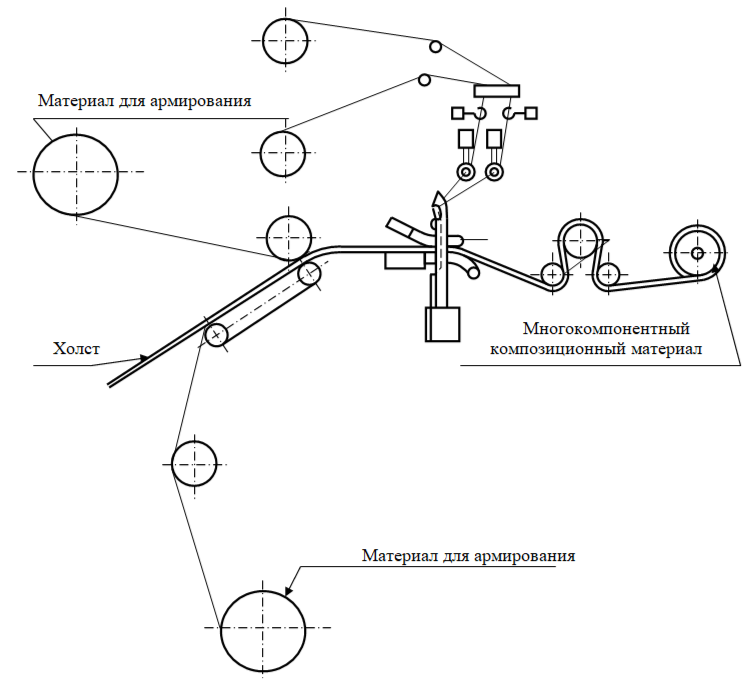
Рисунок 6 - Схема технологического процесса изготовления многокомпонентного композиционного материала после модернизации
Схема технологического процесса получения многокомпонентного композиционного материала из текстильных отходов после модернизации представлена на рисунке 6.
Готовый многокомпонентный композиционный материал, полученный на вязально-прошивной машине, наматывается в рулон.
Полученный по разработанной технологии многослойный композиционный материал был использован в мебельном производстве, в строительстве, при изготовлении рабочей одежды и т.д.
3. Заключение
Разработанное оборудование для дополнительного разрыхления, рассортировки волокон, их распределения и транспортировки обеспечивает максимальное и более качественное расщепление комплексов волокон до получения одиночных волокон, что позволяет более эффективно использовать их в общем сырьевом балансе текстильной промышленности и расширить ассортимент текстильной продукции.
Была разработана технология изготовления композиционного материала из регенерированных одиночных волокон на основе модернизации зоны питания вязально-прошивной машины.
Расчет экономической эффективности технологического процесса изготовления композиционного материала по разработанной технологии, а также ее сравнение с экономической эффективностью производства нетканого материала (ветоши), выпускаемого на предприятии показал, что годовая прибыль от реализации композиционного материала по разработанной технологии составила 7023,88 тыс. руб., а годовая прибыль от реализации нетканого материала (ветоши) – 3582,66 тыс. руб.
Таким образом, использование наших разработок в текстильной промышленности поможет бизнесу занять новые рыночные ниши, организовать производство новых материалов различного назначения.