ОСОБЕННОСТИ ИСПОЛЬЗОВАНИЯ ТЕРМОЗВУКОВОЙ МИКРОСВАРКИ ПРОВОЛОЧНЫХ ВЫВОДОВ ПРИ СБОРКЕ РАДИОФОТОННЫХ МОДУЛЕЙ
ОСОБЕННОСТИ ИСПОЛЬЗОВАНИЯ ТЕРМОЗВУКОВОЙ МИКРОСВАРКИ ПРОВОЛОЧНЫХ ВЫВОДОВ ПРИ СБОРКЕ РАДИОФОТОННЫХ МОДУЛЕЙ
Аннотация
В статье приведены результаты отработки технологического режима термозвуковой микросварки, обеспечивающего надёжные электрические соединения разнородных элементов фотонных интегральных схем при их корпусировании в виде радиофотонных модулей. Экспериментально определено, что наиболее оптимальным режимом микросварки золотым шариком к металлизированной контактной площадке и клиновидным соединением является режим со следующими параметрами: мощность ультразвукового воздействия равна 0,375 Вт, сила прижима инструмента равна 350 мН, длительность процесса сварки составляет 200 мс, длина проволоки, из которой формируется шарик, равна диаметру капилляра. При использовании данного режима микросварки проволочных соединений размеры пятна контакта составляют в среднем 60 мкм и не превышают геометрические размеры контактных площадок интегральных микросхем. Электрические соединения, выполненные в данном технологическом режиме, успешно прошли испытания тестирования на воздействие изменения температуры окружающей среды и на отрыв. Показано, что для более надежного закрепления на контактной площадке клиновидного соединения можно использовать дополнительное шариковое соединение. Электрические соединения, выполненные в данном технологическом режиме, успешно прошли тестирования на воздействие циклического изменения температуры окружающей среды (изменении внешней температуры плюс 100 ºС - минус 60 ºС в течении 5 циклов с выдержками при каждом крайнем значении температуры в течение 30 минут) и испытания на отрыв динамометром с силой отрыва 2 г.
1. Введение
Одной из важных операций при установке кристалла полупроводниковой интегральной микросхемы в корпус является электрическое соединение его контактных площадок с выводами корпуса . Наиболее часто используемым на производстве видом электрического соединения контактных площадок кристалла и выводов корпуса является микросварка выводов проволокой, а в некоторых случаях – лентой , , . Данный метод позволяет в полной мере воспользоваться автоматизацией, кроме того он обладает универсальностью по отношению к разным технологическим вариантам изготовления монолитной интегральной схемы и геометрическим параметрам корпусов .
Существует несколько видов микросварки контактных площадок интегральных схем и проволочных выводов: термозвуковая микросварка, термокомпрессионная и контактная , , . Основными преимуществами термозвуковой микросварки перед другими видами является то, что при этом процессе не происходит плавление металла, температура нагрева кристалла значительное ниже, на контактные площадки микросхемы не подается высокий ток, что особенно важно для высокочувствительных микросхем, а также обеспечивается высокая адгезия свариваемых поверхностей .
Несмотря на хорошую изученность метода термозвуковой микросварки, при корпусировании коллективом авторов фотонных интегральных схем электрооптических модуляторов и кристаллов полупроводниковых лазерных диодов возникла необходимость в отработке технологии формирования электрических соединений разнородных элементов (полупроводниковый кристалл, керамическая переходная плата, корпус изделия) методом термозвуковой микросварки с имеющимися особенностями для данных компонентов.
Целью данной работы является отработка технологии термозвуковой микросварки, которая обеспечит получение надёжных электрических соединений разнородных элементов фотонных интегральных схем при их корпусировании в виде радиофотонных модулей.
2. Методы и принципы исследования
Отработка технологии термозвуковой микросварки разнородных элементов фотонных интегральных схем осуществлялась на установке HB16 (TPT, Германия). Данная установка представлена на рисунке 1 и представляет собой полуавтоматическую установку, которая предназначена для выполнения клиновой термозвуковой сварки и термозвуковой сварки шариком. Для сварки установка позволяет использовать проволоку диаметром от 17 до 75 мкм.
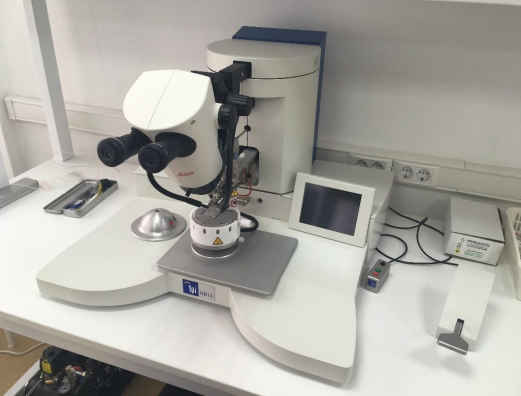
Рисунок 1 - Внешний вид установки TPT HB16
![Виды сварки: а) шариком, б) клином [3]](/media/images/2023-10-26/e73304d6-9416-4abd-9db3-0c106d3ee81a.png)
Рисунок 2 - Виды сварки: а) шариком, б) клином [3]
При сварке соединением типа «клин» две металлические поверхности соединяются между собой методом диффузии. Проволока приваривается к контактной площадке кристалла или металлическому корпусу в результате ультразвукового трения между собой нагретых свариваемых поверхностей
, , .Тестирование сформированных проволочных соединений на отрыв осуществлялось с использованием динамометра HOLEX 478900 50CN (Hoffmann GmbH Quality Tools, Германия).
Термоциклические испытания сварных соединений на экспериментальных образцах производились с использованием электрошкафа тепла СНОЛ-3,5.3,5.3,5/3,5-И5М (ТермИКС НПФ, Россия) и термокамеры ТК 005-70-80 (Россия).
3. Основные результаты и обсуждение
На первом этапе отработки технологии термозвуковой микросварки разнородных элементов фотонных интегральных схем производилась оценка диапазонов варьирования технологических параметров термозвуковой микросварки.
Для этого, была проведена оценка размера сварного соединения типа «шарик-клин». Данный этап необходим, чтобы электрическое соединение не превышало геометрических размеров контактной площадки. Отношение диаметра капилляра (Dмин) к длине ее вылета из наконечника капилляра (Lпров) возможно брать любое, однако значения отношений более единицы, для данных критических размеров нецелесообразны, так как размер сварного соединения будет превышать размер контактной площадки (рисунок 3). В данной работе использовались два соотношения длины вылета проволоки и диаметра капилляра: Lпров= 0,5·Dмин и Lпров= Dмин. Учитывая возможность заклинивания сформированного плазмой шарика в инструменте, в работе используется случай, при котором длина проволоки Lпров, из которой формируется шарик, равен диаметру капилляра Dмин.
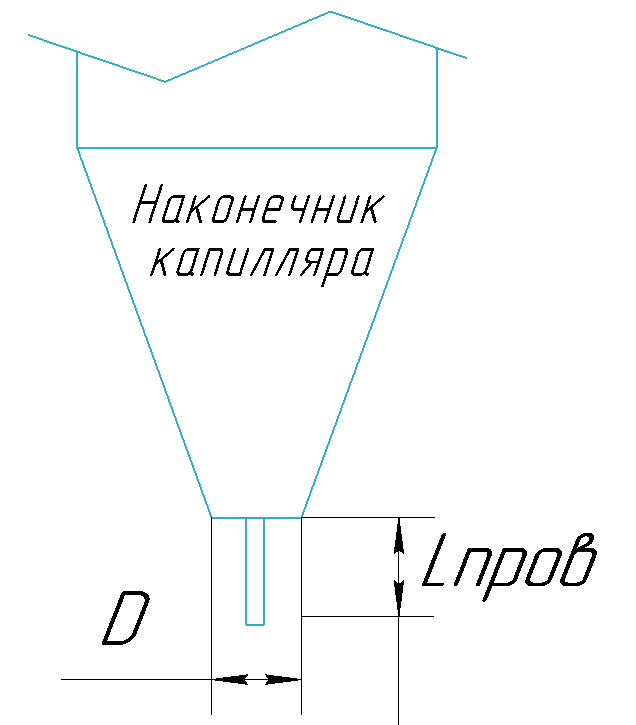
Рисунок 3 - Графическая схема определения длины проволоки
Рекомендованный производителем установки диапазон силы прижима инструмента (Fинст) составляет от 100 мН до 500 мН. При значении силы прижима капилляра менее 150 мН, подавляющим параметром, который образует соединение, является мощность ультразвукового воздействия. При этом чаще всего в последующем наблюдается отрыв соединения от контактной площадки. Таким образом, в данных исследований диапазон значений для силы прижима капилляра изменялся от 150 до 500 мН.
При формировании второго соединения «клин» с помощью подреза проволоки капилляром, важными параметрами являются форма и размер клинового следа, а также мощность ультразвукового воздействия. Для того чтобы второе соединение, как и шарик, размещались на поверхности контактной площадки и не превышали критические размеры, необходимо чтобы клиновой след был или немного меньше, или соразмерен шарику. При таком виде соединения основным параметром, определяющим качество микросварки, является мощность УЗ воздействия.
Частота излучения в используемой установке составляет 63,3 кГц. При значении мощности УЗ воздействия 0,75 Вт для маленьких размеров проволоки и соединений из тонкой проволоки наблюдается чрезмерная деформация контактной площадки и ее оплавление, а также, что немаловажно, деформация и частичное оплавление капилляра. Исходя из вышесказанного, значение мощности ультразвукового воздействия выше 0,625 Вт нецелесообразно использовать для используемой на установке паре капилляр – проволока. На рисунке 4 представлена микрофотография прожога контактной площадки при мощности ультразвукового воздействия 0,75 Вт, длины проволоки равной диаметру капилляра, и при значениях Fинст = 150 мН, время сварки 200 мс.
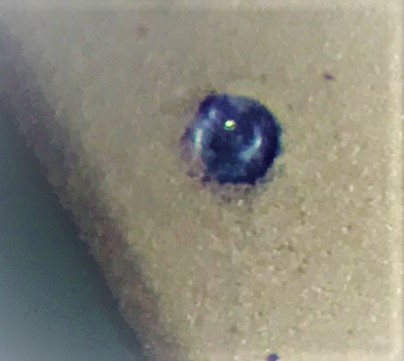
Рисунок 4 - Микрофотография прожога Руз = 0,75 Вт
Для выбора оптимального режима микросварки проволочных выводов на тестовые платы приваривались проволочные соединения при шаговых изменениях мощности ультразвукового воздействия и силы прижима инструмента (рисунок 5).
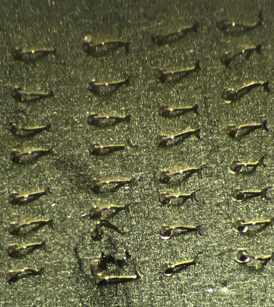
Рисунок 5 - Визуализация эксперимента по отбраковке неподходящих режимов термозвуковой микросварки, вид сверху
Таблица 1 - Результаты тестовых исследований режимов микросварки
Сила прижима инструмента, Fинст, мН | Мощность ультразвукового воздействия, Pуз, Вт | |||
0,25 | 0,375 | 0,5 | 0,625 | |
150 | – | – | – | – |
200 | – | – | – | – |
250 | – | + | + | + |
300 | – | + | + | + |
350 | – | + | + | + |
400 | – | + | + | + |
450 | – | + | + | + |
500 | – | + | + | + |
Анализ полученных результатов показывает, что среди опробованных 32 режимов микросварки проволочных выводов пригодными для создания соединений оказались лишь 18 режимов.
Для дальнейшей отбраковки отобранных режимов экспериментальные образцы подвергались тестированию на воздействие изменения температуры окружающей среды (термоциклирование). Данный метод испытаний необходим, чтобы выявить скрытые дефекты соединения.
Используемые параметры процесса термоциклирования следующие:
1) температура в камере тепла: + 100 ºС;
2) температура в камере холода: – 60 ºС;
3) время выдержки в камере тепла: 30 минут;
4) время выдержки в камере холода: 30 минут;
5) время переноса из камеры в камеру: не более 2 минут;
6) количество циклов: 5.
Тестирование прочности соединения на отрыв было проведено с использованием динамометра HOLEX для двух подготовленных партий подготовленных экспериментальных образцов: подвергавшихся (плата 1) и не подвергавшихся (плата 2) процессу термоциклирования. Осмотр по результатам тестирования на воздействия изменения температуры окружающей среды проводился на оптическом микроскопе Альтами СМ0745-Т (Альтами, Россия). Результат проведения тестирования прочности соединения на отрыв приведен в таблице 2. Прочерками в таблице отмечены испытываемые образцы, не прошедшие испытания на отрыв (отрыв которых наступил при силе отрыва менее 1 г).
Таблица 2 - Анализ результатов тестирования образцов на отрыв
Параметры микросварки | Плата 1 | Плата 2 | |
Fинст, мН | PУЗ, Вт | Fотрыва, г | Fотрыва, г |
250 | 0,375 | – | 1 |
0,5 | – | 1 | |
0,625 | – | – | |
300 | 0,375 | – | 2,5 |
0,5 | – | – | |
250 | – | 1 | |
350 | 0,375 | 3,5 | 4 |
0,5 | 2 | 1 | |
0,625 | – | – |
Пригодным режимом по результатам тестирования проволочных соединений на отрыв считаются образцы, сила отрыва которых на всех платах больше 2 г.
Таким образом, с учетом прошедшего тестирования на отрыв и на воздействие изменения температуры окружающей среды было определено, что предъявляемым требованиям соответствуют образцы, полученные при силе прижима инструмента 350 мН и мощности ультразвукового воздействия 0,375 Вт.
Тестирование на отрыв соединений типа шарик – клин показало, что при механическом воздействии от тестовой платы прежде всего отходит соединение типа клин. Для более надежного закрепления было решено использовать на контактной площадке клиновидного соединения дополнительное шариковое соединение. Данное соединение применяется в случаях, когда необходимо получить повышенную прочность электрического соединения к контактной площадке. Важно отметить, что второе шариковое соединение после обрезки соединительной проволоки не должно иметь остаточный проволочный выступ. В высокочастотных устройствах данный дефект может привести к искажению частотных характеристик. Наиболее простым способом устранения образуемой «антенны» является ее прижим к сформированному соединению с помощью специальной насадки на рабочую часть установки.
При использовании дополнительного шарикового соединения необходимо удостовериться и наглядно показать, что определённый в ходе работы режим укладывается в геометрические размеры контактной площадки. На рисунке 6 представлена микрофотография разваренного в отработанном технологическом режиме соединения на контактной площадке кристалла интегральной GaAs схемы питания и согласования для СВЧ фотодиода.
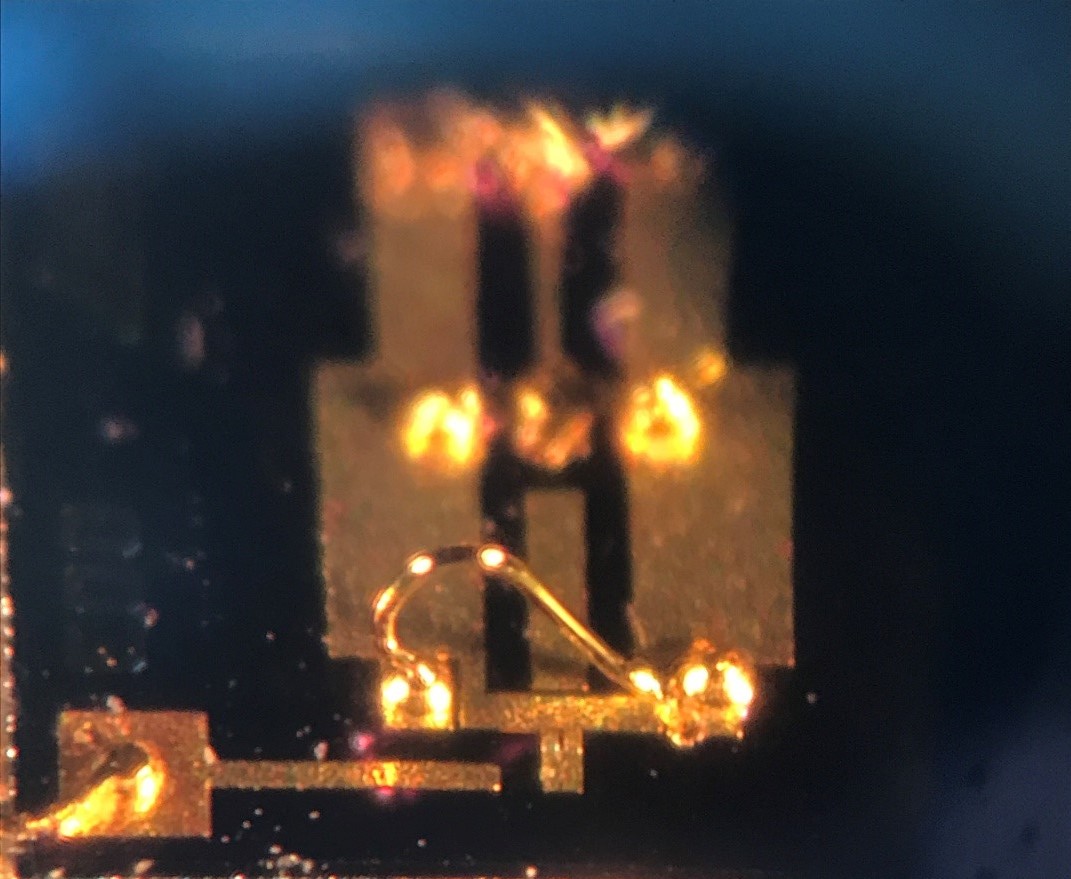
Рисунок 6 - Микрофотография разваренного соединения типа «шарик - клин» с дополнительным шариковым соединением на контактной площадке кристалла
С использованием отработанного технологического режима термозвуковой микросварки были изготовлены экспериментальные микросборки сверхширокополосного оптического модулятора с интегрированным источником излучения (рисунок 7).
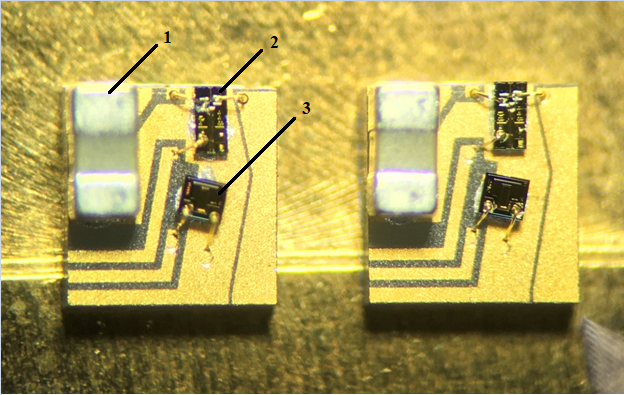
Рисунок 7 - Фотография экспериментальных микросборок сверхширокополосного оптического модулятора с интегрированным источником излучения
Примечание: 1 – конденсатор, 2 – фотонная интегральная микросхема модулятора с интегрированным лазером, 3 – мониторный фотодиод
4. Заключение
В ходе данной работы изготовлены экспериментальные образцы. Проанализировано влияние технологических параметров термозвуковой микросварки на параметры получаемых соединений. Также выполнено тестирование на контроль качества сварного соединения на отрыв и проведено испытание на воздействие изменения температуры окружающей среды.
Экспериментально определено, что наиболее оптимальным режимом микросварки золотым шариком к металлизированной контактной площадке является режим со следующими параметрами: мощность ультразвукового воздействия равна 0,375 Вт, сила прижима инструмента равна 350 мН, длительность процесса сварки составляет 200 мс, длина проволоки, из которой формируется шарик, равна диаметру капилляра. При использовании данного режима микросварки проволочных соединений размеры пятна контакта составляют в среднем 60 мкм и не превышают геометрические размеры контактных площадок интегральных микросхем. Для более надежного закрепления было решено использовать на контактной площадке клиновидного соединения дополнительное шариковое соединение. Данное соединение применяется в случаях, когда необходимо получить повышенную прочность электрического соединения к контактной площадке. Важно отметить, что второе шариковое соединение после обрезки соединительной проволоки не должно иметь остаточный проволочный выступ. В высокочастотных устройствах данный дефект может привести к искажению частотных характеристик.