CEMENT ASH FIBROFOAM CONCRETE OF NATURAL CURING
CEMENT ASH FIBROFOAM CONCRETE OF NATURAL CURING
Abstract
The article presents data on the effect of dispersed micro reinforcement on the properties of non-autoclaved cement ash foam concrete. The material was prepared on protein blowing agents of domestic production. Fly ash from the combustion of brown coals of Borodinsky open-cut mine of Kansko-Achinsky coal basin is used as an aggregate for the preparation of foam concrete. It is established that the use of polypropylene fibre in cement ash foam concrete of natural curing is the most expedient. The maximum firmness of foam in mortar mixture is obtained at introduction of asbestos fibre. The use of fibrous additives in the composition of foam concrete allows to increase its crack resistance by 34-75%, this indicator increases when using fibres with higher tensile strength. The use of basalt fibres in Rospena foamed concrete allows to reduce the density to D500 and provide a thermal conductivity coefficient of 0.150 W/(m°C).
1. Введение
Утилизация техногенных отходов производств, например, таких как зола-унос, в составе строительных материалов является актуальной экологической и экономической задачей , , , . Одним из перспективных направлений применения зол-уноса является производство с их использованием неавтоклавных пенобетонов. Такие изделия обладают повышенными теплоизоляционными характеристиками, невысокой стоимостью, относительно низкими энергетическими затратами при производстве. Сложность обеспечения требуемых эксплуатационных характеристик неавтоклавного пенобетона заключается в сохранении оптимальной пористой структуры до затвердевания материала. Для повышения его качества используют волокнистые добавки
. Они способствуют повышению агрегативной устойчивости пенобетонной смеси , , повышают пластическую прочность и прочность готовых изделий , а также трещиностойкость . За счет микроармирующего эффекта фибра позволяет снизить усадочные деформации , . В качестве фибры используют стеклянные и базальтовые волокна , , , полипропиленовые , применяют углеродное волокно , , целлюлозный наполнитель, полученный в результате мокрого измельчения макулатуры , и др.Целью данной работы является повышение агрегативной устойчивости и прочностных характеристик неавтоклавного цементно-зольного пенобетона с использованием волокнистых добавок.
2. Методы и принципы исследования
В работе использовались следующие материалы:
– портландцемент класса ЦЕМ I 42,5Н (ООО «Топкинский цемент», Кемерово), химический состав, мас. %: CaO – 63,02; SiO2 – 19,29; Al2O3 – 4,63; Na2O – 0,37, K2O – 0,47; MgO – 1,86; TiO2 – 0,28; Fe2O3 – 3,91; SO3 – 3,98, P2O5 – 0,07, MnO – 0,05, ППП – 2,25, истинная плотность – 3160 кг/м3, насыпная плотность – 1056 кг/м3;
– основная зола-унос от сжигания бурых углей Бородинского разреза Канско-Ачинского угольного бассейна (ТЭЦ-5, Новосибирск), химический состав, мас. %: SiO2 – 49,47; Al2O3 – 7,36; Fe2O3 – 7,51; CaO – 27,53; MgO – 4,52; Na2O – 0,23; K2O – 0,28; SO3 – 1,24; BaO – 0,38, P2O5 – 0,03, TiO2 – 0,44, ППП – 0,52, насыпная плотность – 1342 кг/м3, истинная плотность – 2489 кг/м3, удельная поверхность – 240 м2/кг, влажность – 0,4%.
Удельная активность естественных радионуклидов золы составляет 113 Бк/кг, такой материал может использоваться для строительства жилых и общественных зданий .
По данным рентгенофазового анализа в составе золы обнаруживаются кварц (3,35, 1,82, 1,54)×10-1 нм, муллит (3,35, 2,11, 2,40, 2,28, 2,12, 1,54) ×10-1 нм, мусковит (3,35, 1,98, 2,40, 2,12, 1,69, 1, 54) ×10-1 нм, ортоклаз (3,35, 1,81, 4,26, 3,5, 2,77, 2,46,2,12, 1,98) ×10-1 нм.
По содержанию оксида кальция зола содержит более 10 %, в соответствии с ГОСТ 25818-2017 «Золы-уноса тепловых электростанций для бетонов. Технические условия» зола является основной. По требованиям стандарта для ячеистых бетонов количество CaOсвоб не нормируется. По классификации Савинкиной М. А. и Логвиненко А. Т. исследуемая зола относится к среднекальциевой с содержанием CaO 20-30%
. Содержание сернистых и сернокислых соединений не превышает 6%, количество щелочных оксидов также удовлетворяет требованиям стандарта (не более 3,5%). Потери при прокаливании составляют 0,52%, что не превышает нормируемых показателей (3%) и соответствует значениям золы сухого отбора. Зола-унос соответствует требованиям ГОСТ 25818-2017.Модуль основности для исследуемой золы составляет 0,56, коэффициент качества равен 1,04. Такие золы обладают свойством самостоятельного твердения, могут применяться для производства изделий на их основе. По требованиям межгосударственного стандарта в качестве вяжущего компонента в ячеистых бетонах можно использовать высокоосновную золу с содержанием оксида кальция не менее 40%. Т.к. исследуемая зола данному параметру не соответствует, было решено ее использовать в качестве заполнителя.
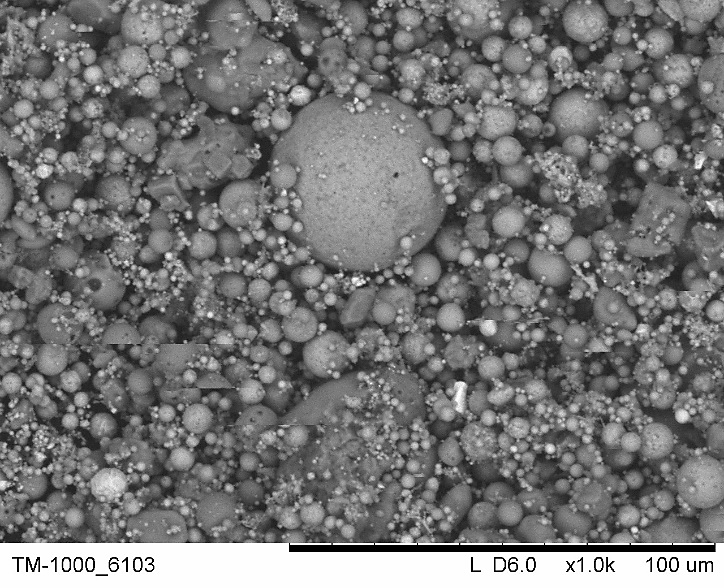
Рисунок 1 - Электронная фотография золы
Примечание: 1000-кратное увеличение
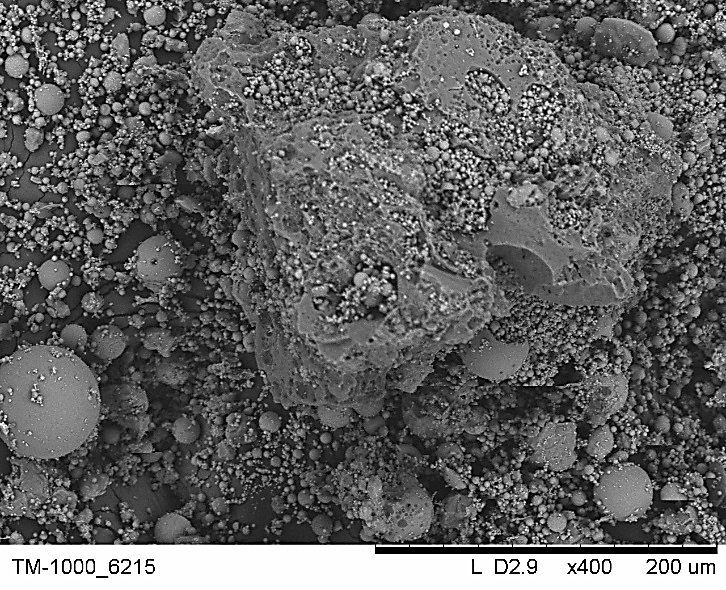
Рисунок 2 - Электронная фотография золы
Примечание: 400-кратное увеличение
Для приготовления пены использовались отечественные пенообразователи, состоящие из протеинов (белков) – биополимеров Rospena (ТУ 24.66.47.142-001-0139620869-2019) и Эталон (ТУ 2483-003-13420175-2015).
В качестве армирующих компонентов применяли минеральную и органическую фибру: базальтовую, полипропиленовую и асбестовую. Использовались базальтовые волокна (CEMMIX), содержащие SiO2, Al2O3. Длина фибры – 12 мм, диаметр – 17 мкм, обладают химической стойкостью. Прочность при растяжении – 3000 МПа. Полипропиленовое волокно (ООО ПК Альянс) с длиной волокон 6 мм, диаметром 40 мкм. Волокна обладают химической стойкостью. Прочность при растяжении – 570 МПа. Асбест хризотиловый Киембаевского месторождения марки А-6К-30 (АО «Оренбургские минералы») с длиной волокон менее 16 мм, диаметром менее 0,5 мкм. Прочность при растяжении – 3200 МПа.
Пенобетон естественного твердения готовился по двухстадийной технологии на турбулентной установке со скоростью вращения рабочего органа 940-1500 об/мин. Твердение образцов происходило в нормальных условиях, на 28-е сутки проводились их испытания.
3. Основные результаты
Для приготовления пенобетона было определено оптимальное количество порообразователя, которое составило 3% для пенообразователя Эталон, для Rospena – 7%. На пенообразователе Эталон возможно получить низкократную пену (16), а на пенообразователе Rospena – среднекратную (25). Добавки вводились в воду для их равномерного распределения в объеме материала, чтобы исключить агрегирование волокон.
В таблице 1 представлены результаты испытаний пенобетона на основе пенообразователя Эталон. Для контрольного образца плотность составляет 603 кг/м3. Базальтовые волокна значительно повышают плотность по сравнению с контрольным составом (на 30%). При введении асбестовых и полипропиленовых волокон плотность меняется незначительно по сравнению с контрольным образцом.
При сравнении ККК можно отметить, что введение асбестовых волокон снижает его на 12%, наблюдается увеличение ККК при введении полипропиленовой (23) и базальтовой фибры (89).
Таблица 1 - Свойства пенобетона Эталон
Показатель | Волокна | |||
Без добавок | Базальтовая | Полипропиленовая | Асбестовая | |
Средняя плотность, кг/м3 | 603 | 822 | 638 | 570 |
Предел прочности при сжатии, МПа | 2,12 | 5,47 | 2,76 | 1,76 |
ККК | 3,52 | 6,65 | 4,33 | 3,09 |
Предел прочности при изгибе, МПа | 1,35 | 5,25 | 2,37 | 1,97 |
Rизг/Rсж | 0,64 | 0,96 | 0,86 | 1,12 |
Механизм действия волокнистых добавок заключается в армировании материала и препятствии распространению трещин в композите. Использование в составе пенобетона фибры позволяет увеличить его трещиностойкость (Rизг/Rсж) на 34-75%. Увеличение трещиностойкости материала при введении волокон может быть связано с их характеристиками. С повышением прочности при растяжении используемой фибры наблюдается рост трещиностойкости полученного пенобетона (табл. 1).
Также волокнистые добавки повышают стойкость пены в растворной смеси на 6-15% (рис. 3). За счет своей протяженной формы волокна более эффективно удерживают воздух в пенобетонной смеси. Наиболее значительное влияние оказывает асбестовая фибра (15%), возможно это связано с наилучшим распределением волокон в объеме материала. Волокна могут закупоривать каналы Плато, что также положительно сказывается на агрегативной устойчивости пенобетонной смеси.
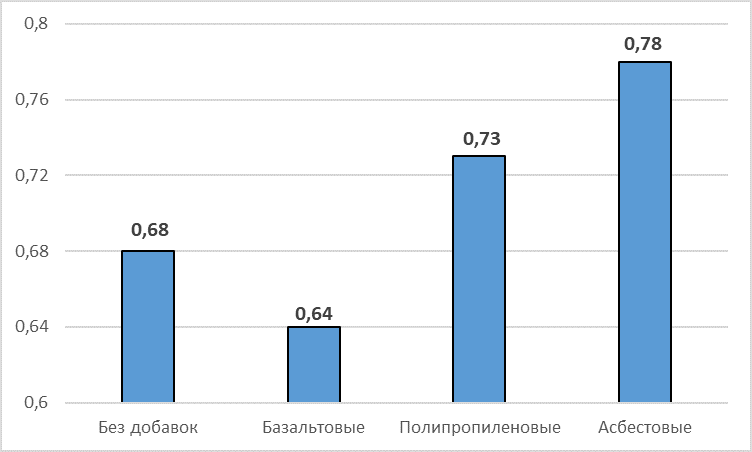
Рисунок 3 - Стойкость пены Эталон в растворной смеси
Таблица 2 - Свойства пенобетона Rospena
Показатели | Волокна | |||
без добавок | базальтовые | полипропиленовые | хризотил-асбестовые | |
Средняя плотность, кг/м3 | 575 | 494 | 589 | 310 |
Предел прочности при сжатии, МПа | 2,3 | 1,57 | 2,76 | 0,46 |
ККК | 3,99 | 3,29 | 4,57 | 1,48 |
Предел прочности при изгибе, МПа | 1,5 | 1,38 | 2,16 | 0,75 |
Rизг/Rсж | 0,65 | 0,88 | 0,78 | 1,63 |
При введении хризотил-асбестовых волокон плотность пенобетона снижается до 310 кг/м3, но при этом падает и прочность (табл. 2), ККК уменьшается практически в 2,5 раза. ККК несколько снижается при использовании базальтовых волокон, трещиностойкость при этом увеличивается на 35%. Коэффициент теплопроводности пенобетона с базальтовой фиброй составляет 0,150 Вт/(м°С) при определении методом теплового зонда , что позволяет использовать данный материал как теплоизоляционный.
Для пенобетона Rospena стойкость пены в растворной смеси увеличивается на 4-8% (рис. 4). За счет своей протяженной формы частицы повышают вязкость смеси, а также позволяют эффективно проводить воздухововлечение в смесь. Наибольшее повышение стойкости пены Rospena также наблюдается для пенобетонной смеси с хризотил-асбестовыми волокнами.
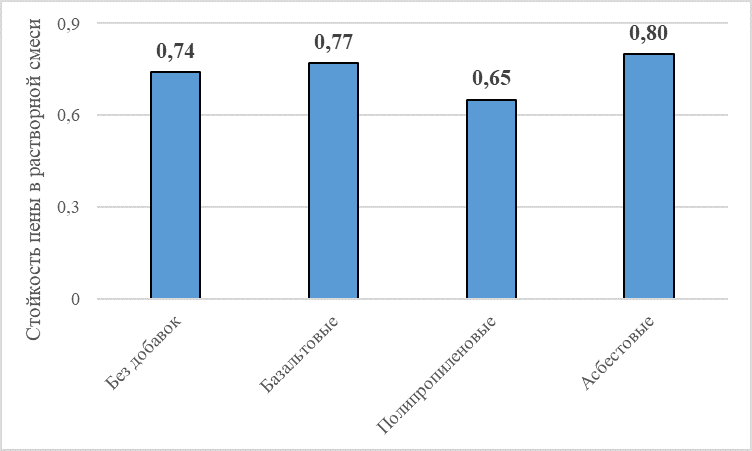
Рисунок 4 - Стойкость пены Rospena в растворной смеси
Предполагается
, , что повышение прочности цементного камня с микроармирующими волокнами может быть обусловлено увеличением степени гидратации цемента.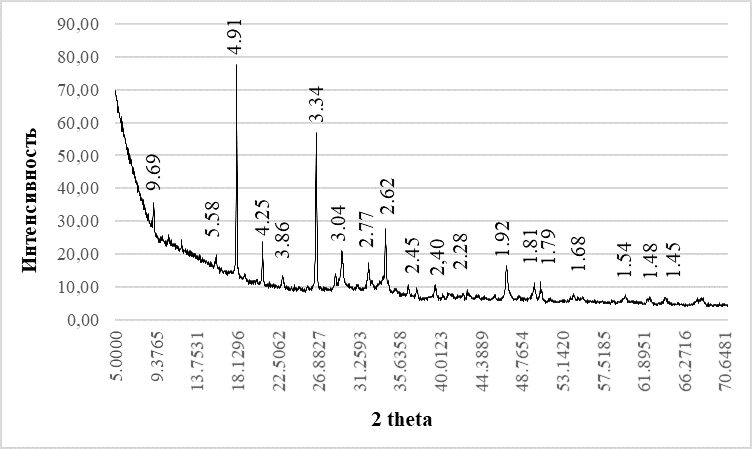
Рисунок 5 - Рентгенограмма пенобетона Rospena
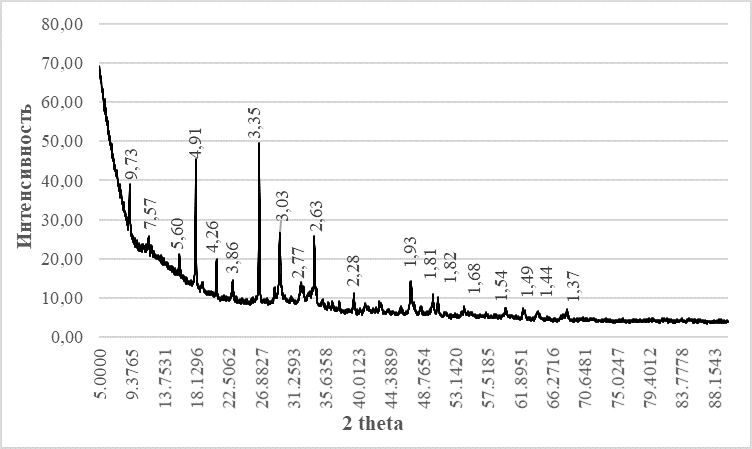
Рисунок 6 - Рентгенограмма пенобетона Эталон
При сравнении рентгенограмм пенобетона с волокнистыми добавками наблюдаются различия в интенсивностях линии, соответствующих Са(OH)2. Наибольшая интенсивность относится к пенобетону Rospena с полипропиленовой фиброй и снижается при введении базальтовой, наименьшая соответствует пенобетону с асбестовыми волокнами. Таким образом, можно предположить, что волокна выполняют роль подложки для новообразований, увеличивают степень гидратации цемента, при этом повышается прочность при сжатии и ККК пенобетона (табл. 2). Для пенобетона Эталон интенсивность линий уменьшается в следующем порядке: при введении базальтовой фибры, полипропиленовой, асбестовой. Что также согласуется с уменьшением прочности и ККК фибропенобетона (табл. 1). Наименьшее влияние на прочность и ККК для обоих пенообразователей оказывает асбестовая фибра.
4. Заключение
По результатам работы можно сделать следующие выводы:
1. Исследуемая зола относится к среднекальциевой, может быть использована в качестве заполнителя для получения неавтоклавного пенобетона.
2. Для пенообразователя Эталон характерна низкократная пена, для Rospena – среднекратная. Стойкость пены Rospena в цементно-зольной смеси выше на 9% по сравнению с пеной Эталон. Более полная гидратация цемента происходит при использовании пенообразователя Rospena, также такой пенобетон имеет более высокий ККК.
3. Использование в составе цементно-зольного пенобетона волокнистых добавок позволяет увеличить его трещиностойкость на 34-75%, данный показатель возрастает при использовании фибры с более высокой прочностью при растяжении.
4. Стойкость пены в растворной смеси увеличивается на 4-17%, за счет дополнительного воздухововлечения снижается средняя плотность материала. Наибольшее воздухововлечение обеспечивает хризотил-асбестовая фибра.
5. Полипропиленовые волокна увеличивают ККК, средняя плотность меняется незначительно, трещиностойкость повышается на 20-34% в зависимости от пенообразователя.
6. Введение базальтовой фибры позволяет снизить среднюю плотность пенобетона Rospena до D500, ККК при этом составляет 3,29, коэффициент теплопроводности 0,150 Вт/(м°С), что позволяет использовать материал как теплоизоляционный.
Средняя плотность пенобетона Эталон значительно возрастает при использовании базальтовых волокон, ККК повышается. Что может быть связано с трудностью равномерного распределения данного вида фибры.
7. Наибольшая прочность и ККК пенобетона с фиброй соответствует образцам с более полной гидратацией цемента. Наименьшие значения определены для пенобетона с асбестовыми волокнами.