Characteristics of a New Design of Regular Packing for Heat-and-Mass Transfer Processes
Characteristics of a New Design of Regular Packing for Heat-and-Mass Transfer Processes
Abstract
The article introduces a new design for a regular packing intended for use in column apparatuses of the chemical and petrochemical industries. The packing can be applied in a wide range of chemical and technological processes, from purification or separation of mixtures to heat transfer. The packing design, characterized by low hydraulic resistance and increased resistance to surface fouling, is a promising solution for "heavy conditions" applications. In such situations, where the likelihood of contamination of contact devices is particularly high, its features can provide significant advantages. In order to evaluate the hydraulic performance of the new packing, experimental results were compared with data obtained for Raschig rings tested under similar conditions, allowing the effectiveness of the new packing design to be evaluated in comparison with conventional solutions. An air-water system was used to determine the heat-and-mass transfer characteristics. Manufacturing of the prototype of the proposed design was performed using waste from the production of plate heat exchangers, as well as using the technology of layer cladding of thermoplastic material acrylonitrile-butadiene styrene.
1. Введение
Процессы тепло-массообмена занимают центральное место в химической технологии, обеспечивая преобразование потоков веществ и энергии для получения необходимых продуктов или условий проведения технологических процессов. Для достижения требуемой эффективности процессов, осуществляемых с использованием внутреннего объема аппаратов, требуется достаточно развитая поверхность контакта взаимодействующих потоков, для чего используют различные контактные устройства – массообменные тарелки и насадки.
С 1890 года, когда Фридрих Рашиг впервые применил керамические кольца, названные впоследствии его именем, для использования в колоннах для фракционной дистилляции органических веществ, появилось большое количество как конструктивных, так и технологических решений по использованию различных видов насадок как контактных устройств, и работы эти не менее интенсивно продолжаются в настоящее время .
Широкое разнообразие существующих контактных устройств отражает потребность в решениях, адаптированных к конкретным условиям процесса и природе взаимодействующих веществ. Выбор подходящего типа или конструкции контактного устройства имеет решающее значение для оптимизации эффективности процесса; влияют на этот выбор как физические свойства взаимодействующих веществ и рабочие условия процесса, так и желаемый конечный результат.
Регулярные насадки имеют ряд преимуществ по сравнению с насадками, засыпаемыми в навал, и массообменными тарелками, включая меньший перепад давления, более высокую эффективность, большую пропускную способность и меньшую степень задержки жидкости в насадочном слое. Однако у регулярных насадок есть и недостатки, такие как более высокая стоимость и повышенная чувствительность к неравномерному распределению взаимодействующих потоков .
Например, в тяжелых условиях эксплуатации, характеризующихся высокой склонностью к коксованию поверхности контакта и засорению (уменьшению) свободного сечения аппарата, что в свою очередь может существенно затруднить осуществление процесса, ряд производителей советует использовать специальные конструкции внутренних контактных устройств, такие как PROFLUX от Koch-Glitsch и Mellagrid от Sulzer. Так, использование решётчатой насадки PROFLUX, специально предназначенной для использования в тяжёлых условиях эксплуатации, увеличило производительность на 10% при снижении гидравлического сопротивления, достигнутого благодаря использованию более подходящей процессу насадки, что напрямую ведет к уменьшению эксплуатационных расходов на транспортировку газа через слой насадки в сочетании с высокой надёжностью при использовании в условиях, подверженных образованию отложений на контактных поверхностях, что потенциально может привести к увеличению гидравлического сопротивления и закупориванию каналов движения сред (тяжёлых условиях). Конструктивные требования для тяжёлых условий эксплуатации включают в себя баланс между требованиями к эффективности при сохранении надежности и существенном увеличении выхода продукта .
2. Описание новой конструкции насадки и методики обработки экспериментальных данных
Конструкция рассматриваемого контактного устройства представляет собой многослойный блок насадки (см. рис. 1). Каждый слой выполнен в виде пакета 3, состоящего из ряда вертикальных гофрированных пластин 2, установленных параллельно друг другу с соблюдением технологического зазора между ними, посредством дистанцирующих стержней, на которых они закреплены. Малая высота пакета 3 способствует развитию поверхности плёнки стекающей жидкости за счёт увеличения числа так называемых «концевых эффектов» в сравнении с известными аналогами с тем же объёмом насадки и большей высотой пакета. Тенденция к уменьшения высоты пакетов насадки с точки зрения повышения ее эффективности наблюдается в ряде работ , , , , такая конструктивная особенность способствует повышению эффективности за счёт лучшего перемешивания, однако в проведенных ранее исследованиях , недостаточно полно использована возможность дальнейшего снижения высот слоев для расширения диапазона их допустимых значений. Установка пакетов 3 с поворотом на 90° относительно соседних по высоте пакетов способствует развитию активной поверхности контакта взаимодействующих фаз за счёт более частого разрыва и обновления плёнки стекающей жидкости, а уменьшение высоты пакета 3 позволяет увеличить число «концевых эффектов» в сравнении с тем же объёмом насадки с большей высотой пакета, т.е. участков локальной турбулизации (волнообразования) плёнки жидкости при её перетекании между соседними слоями (пакетами), характеризующихся интенсивным перестроением профиля скорости потока. Гофрированные пластины могут быть изготовлены из металла, пластика или керамики, допускающих использование насадки при работе в жестких эксплуатационных условиях. Опробовано изготовление пакетов из деловых отходов промышленного производства пластинчатых теплообменных аппаратов, материалом которых является AISI 316L, а также методом послойного наплавления акрилонитрил-бутадиенстирола.
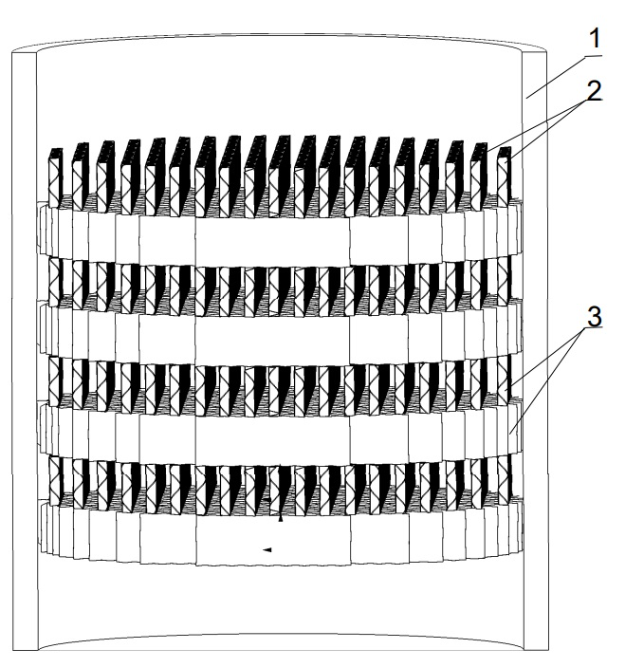
Рисунок 1 - Конструкция регулярной насадки:
1 - колонна; 2 - гофрированные пластины; 3 - пакеты
Таблица 1 - Основные геометрические характеристики рассматриваемых насадок
Тип насадки | Удельная поверхность, м2/м3 | Свободный объём, м3/м3 | Эквивалентный диаметр канала, м |
Исследуемая насадка 20х10 | 270 | 0,077 | 0,0011 |
Кольца Рашига 25х25х3 | 204 | 0,7 | 0,0137 |
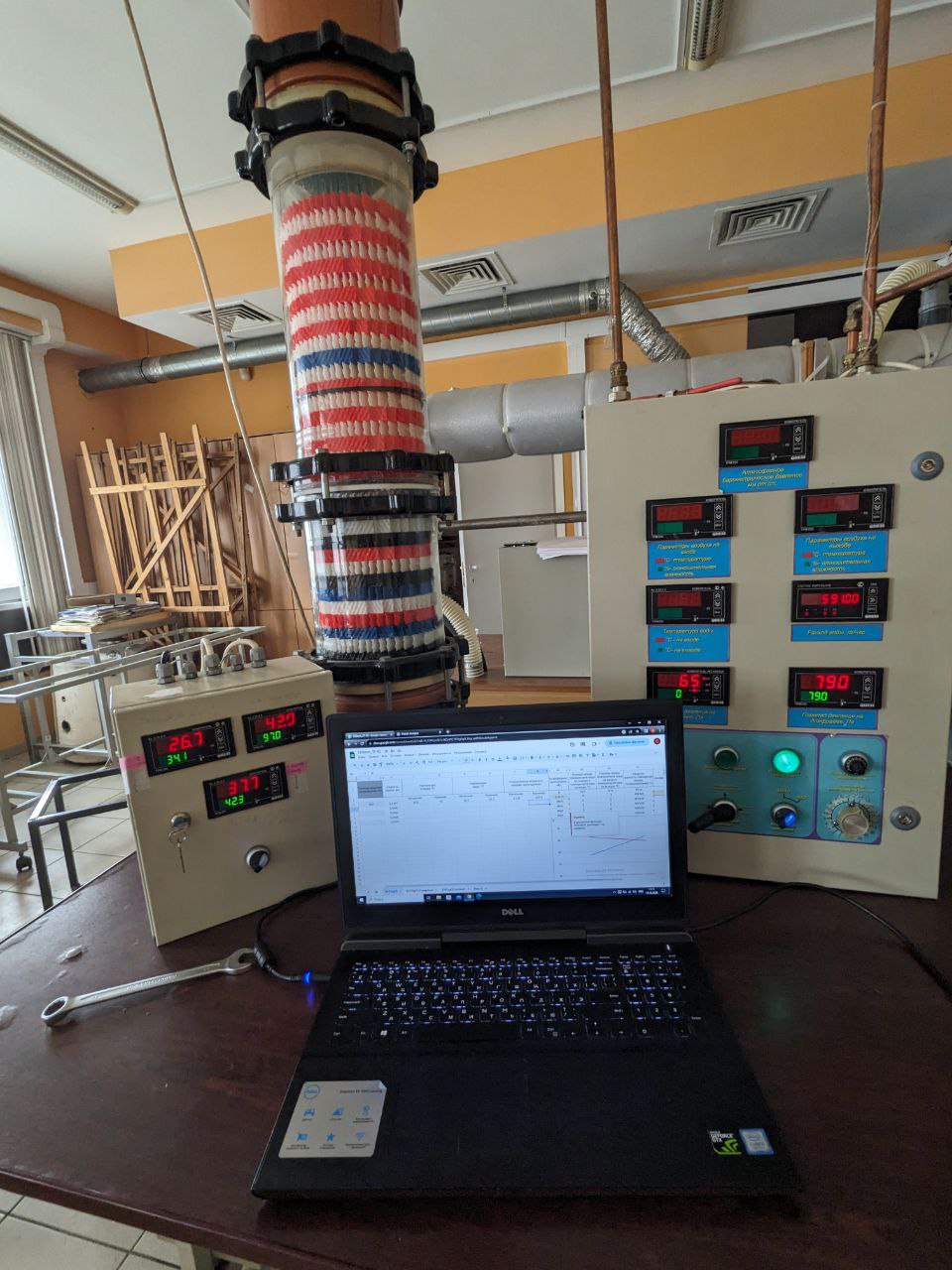
Рисунок 2 - Общий вид экспериментальной установки
Испарительное охлаждение жидкости происходит вследствие тепломассообменных процессов, происходящих при контакте жидкости и газа. Этот процесс в основном обусловлен испарением жидкости с ее поверхности и теплопередачей при контакте теплоносителей. «Движущей силой» процесса испарения является разность парциальных давлений пара у поверхности воды и в ядре воздушного потока. При теплоотдаче движущей силой является разность температур воды и воздуха. Испарение жидкости приводит к уменьшению ее объема и температуры.
В описании тепломассообменных аппаратов поток жидкой фазы принято указывать в виде плотности орошения. Это мера, которая отражает объем жидкости, проходящей через единицу площади за единицу времени. Плотность орошения важна для оценки эффективности процесса тепло- и массообмена, поскольку она влияет на распределение жидкости в насадке и, соответственно, на эффективность контакта между фазами. Поток газа принято описывать через F-фактор, который представляет собой соотношение между скоростью газа и его плотностью. Этот показатель используется для оценки режимов работы аппарата и влияния газового потока на процессы массо- и теплообмена. F-фактор является ключевым параметром в оценке работы насадочных колонн, характеризующим соотношение между скоростью газового потока и его плотностью. Он выражается через скорость газа, делённую на квадратный корень из его плотности, и играет важную роль в анализе гидравлических условий внутри колонны, включая перепады давления и риск затопления. В контексте нашего исследования, где мы вводим новую конструкцию регулярной насадки. F-фактор помогает оценить её способность обеспечивать эффективный массообмен при минимальных потерях давления и максимальном сохранении производительности системы, даже в условиях повышенного газового потока. Математически F-фактор выражается как скорость газа (м/с), деленная на квадратный корень из плотности газа (кг/м³) .
Перепад давления насадочной колонны отражает гидравлическое сопротивление, преодолеваемое взаимодействующими потоками. Использование внутренних устройств, создающих низкое сопротивление позволяет снизить гидравлические потери на аппарате, а следовательно нагрузку на компрессор.
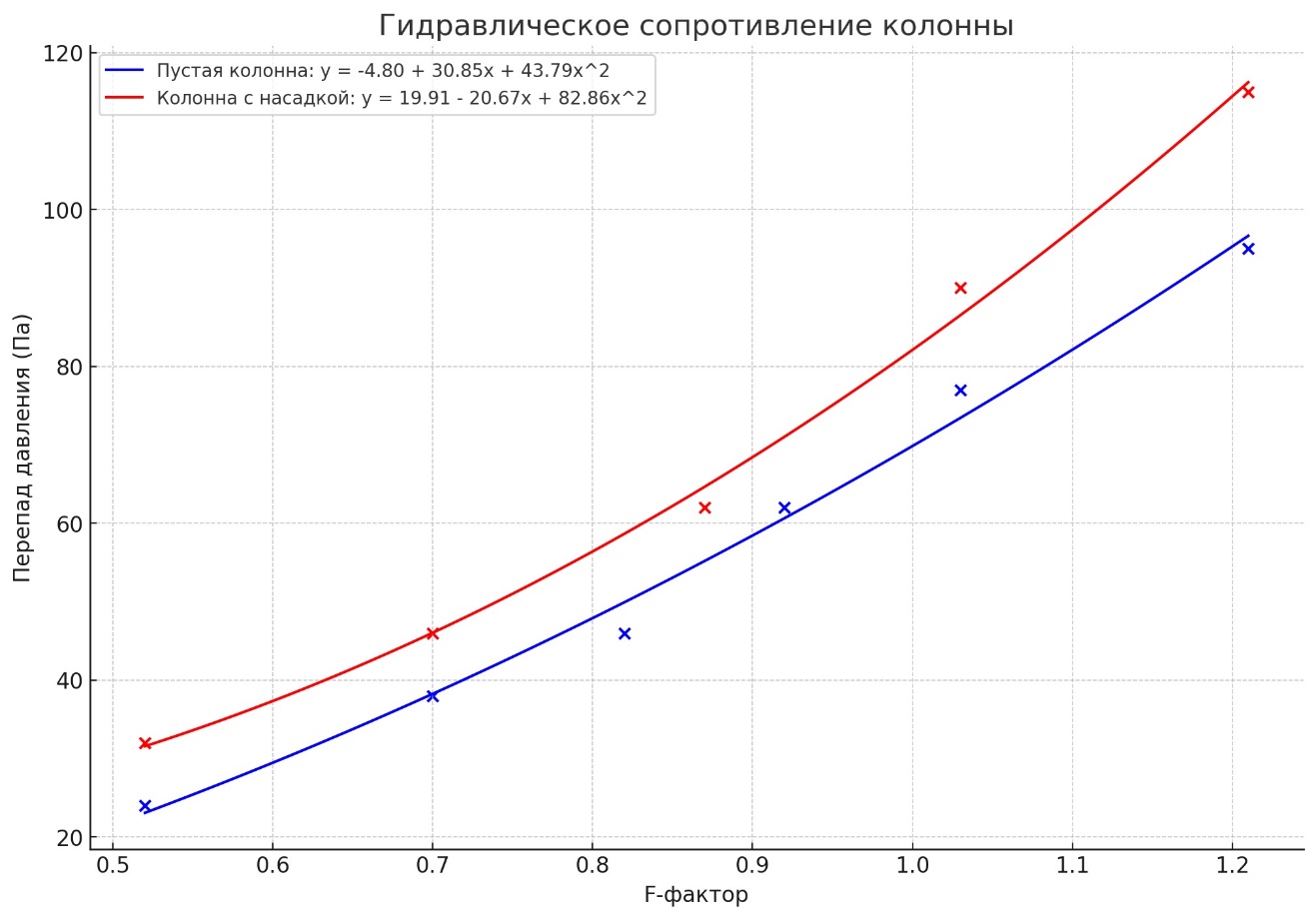
Рисунок 3 - Гидравлическое сопротивление колонны
Эти данные будут использоваться в дальнейшем для верификации результатов, полученных с помощью программ вычислительной гидродинамики (CFD). Использование методов вычислительной гидродинамики позволяет проводить численные эксперименты, моделирующие поведение жидкостей в различных условиях, включая сложные гидравлические системы, такие как колонны с насадкой. Сравнение данных из реальных испытаний с результатами, полученными при помощи CFD-пакетов, обеспечит дополнительную проверку и понимание эффективности насадки, а также поможет в дальнейшем улучшении рассматриваемой конструкции насадочных устройств.
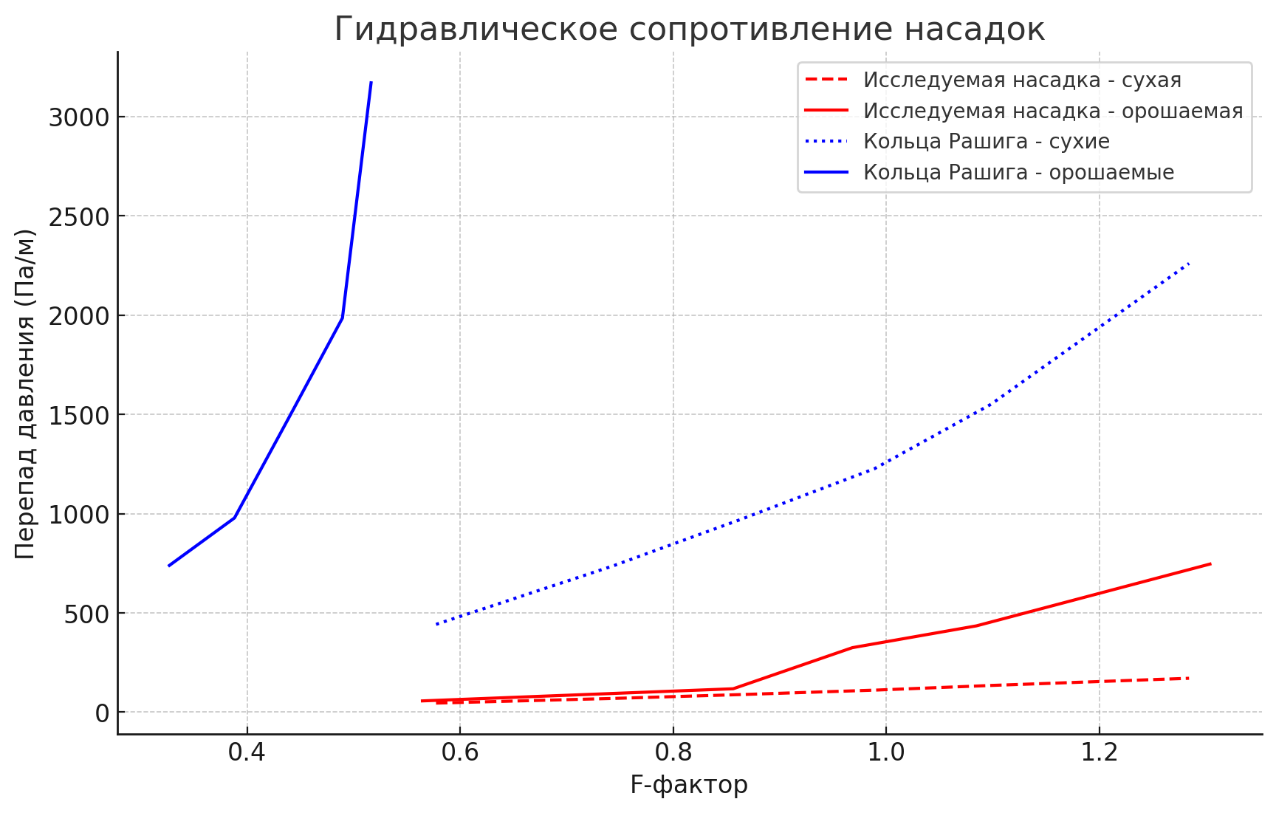
Рисунок 4 - Гидравлическое сопротивление насадок
Передача энергии в рассматриваемой системе «воздух-вода» происходит помимо механизма теплоотдачи ещё и за счёт испарения воды с её поверхности. Основное сопротивление процессу теплообмена сосредоточено в газовой фазе, так как коэффициент теплоотдачи в жидкой фазе примерно в 15 раз больше, чем коэффициент теплоотдачи в газовой фазе, следовательно, можно считать, что коэффициент теплопередачи приблизительно равен коэффициенту теплоотдачи в газовой фазе.
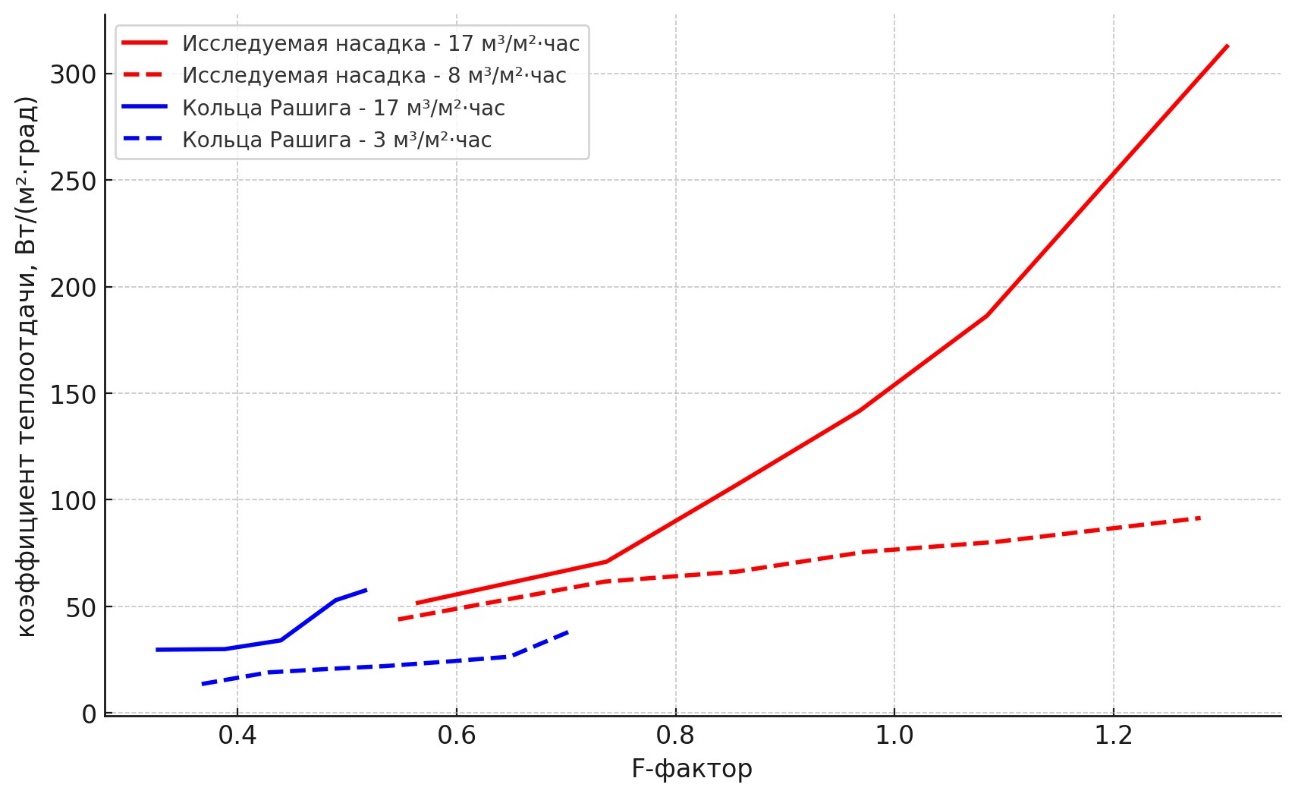
Рисунок 5 - Теплообменная характеристика насадки
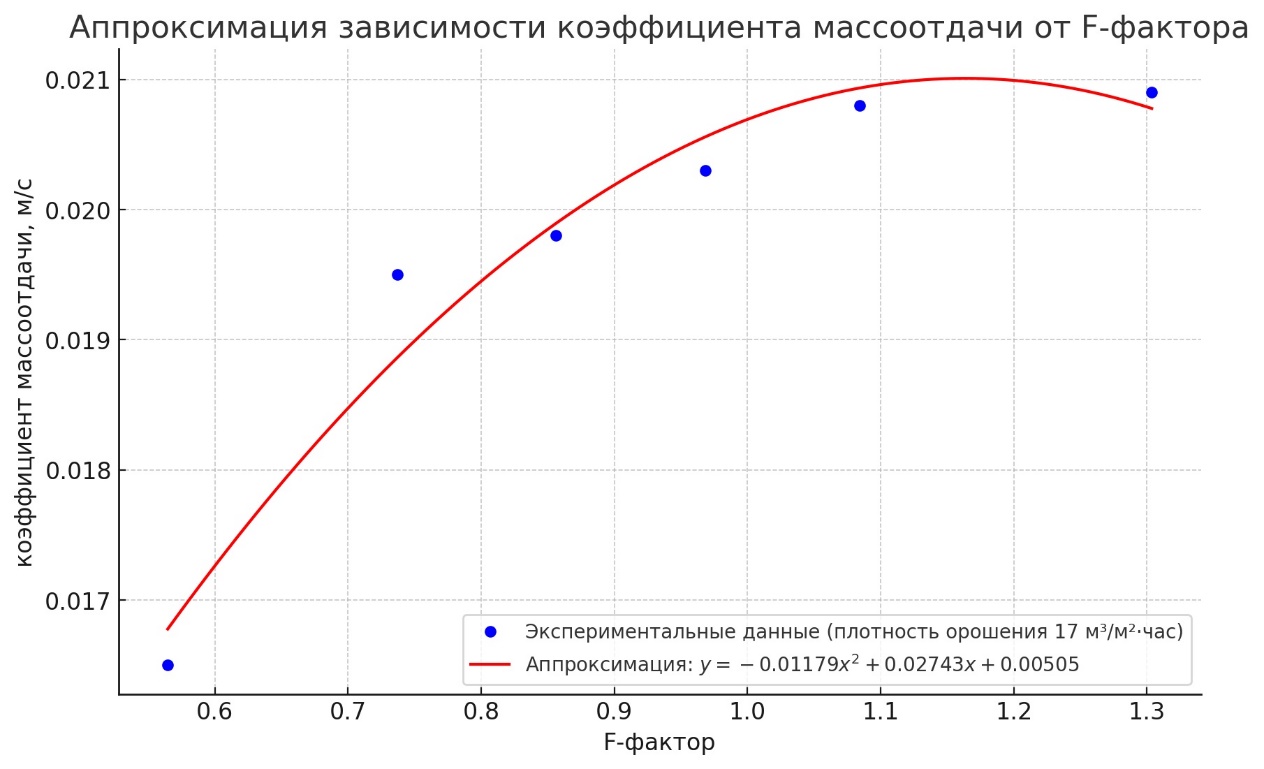
Рисунок 6 - Массообменная характеристика насадки
3. Заключение
Проведённые испытания продемонстрировали преимущества рассматриваемой конструкции. Новая насадка отличается низким гидравлическим сопротивлением при развитии достаточной поверхности контакта, что при сохранении эффективности осуществляемого процесса позволит снизить энергопотребление для его проведения.
Рассмотренная конструкция демонстрирует потенциал для различных применений в химической технологии, особенно в «тяжёлых условиях» эксплуатации и в вакуумных колоннах, где низкое гидравлическое сопротивление имеет решающее значение. Потенциал к снижению образования загрязнений на поверхности приводит к снижению потребности в обслуживании и увеличению срока службы, что делает ее ценным активом в «тяжелых» условиях процессов химической технологии.