THE EFFECT OF AMPERAGE ON THE PRODUCTIVITY OF ALUMINUM ELECTROLYSERS
THE EFFECT OF AMPERAGE ON THE PRODUCTIVITY OF ALUMINUM ELECTROLYSERS
Abstract
The performance of the electrolyser depends on many parameters. Each parameter can affect both the performance and the service life of the aggregate. Therefore, all major aluminium manufacturers have a goal to achieve maximum performance per unit of production area.
The article investigates the processes of aluminum electrolysis with an increase in the current strength in electrolyzers and maintaining optimal technological parameters of electrolyzers. The presented results on the adjustment of technological parameters in electrolyzers with pre-fired anodes were obtained under the conditions of a series of electrolysis of JSC "Kazakhstan Electrolysis Plant" (Kazakhstan).
The analysis of the data with an increase in the current strength was carried out, using a mathematical model, the calculation of the optimal technological parameters was made, as well as the adjustment in accordance with the operating current strength, at which the optimal performance of the electrolysers was achieved.
1. Introduction
The main method for producing aluminum is electrolysis, which is characterized by significant consumption of electrical energy per unit of finished product.
The relevance of the issue and the task of the entire aluminum industry are to increase the service life of electrolysers and their productivity and reduce the cost of electricity per 1 ton of metal, which can be achieved by increasing the current strength, as well as reducing the loss of supplied energy.
The purpose of this study is to determine the effect of increasing the current strength on the technological parameters and performance of the electrolyser.
The stable production of primary aluminum by the electrolytic method depends on the applied technologies and the design of the baked anode (BA) cells. Interaction with the production environment should be resource-saving and characterized by modes of operation for the following indicators: productivity, current efficiency, technological efficiency, consumption of electrical energy and raw materials.
At present, the goal of large aluminum producers is to achieve maximum performance per unit of production area. In order to achieve additional productivity, there is a steady tendency to increase the current strength in the electrolysers in comparison with the design one. This is due to the economic benefits due to increased productivity or increased metal production with low capital costs for the reconstruction of supply transformers. So, for example, an increase in the current strength by 1 kA corresponds to an increase in the productivity of one electrolyser by 7.5 kilograms per day with a current output of 93.2%.
The best technical and economic indicators (TEP), namely the maximum productivity and the minimum power consumption, are achieved while ensuring the optimal energy regime of the electrolyser at the minimum permissible electrolyte temperature
. In this case, the maximum performance depends on both the current strength and the current output, which in turn depends on a large number of factors. The optimal mode is achieved by changing the main technological parameters.The current strength on the existing structures of electrolysers is established on the basis of calculations, with its subsequent correction, considering the operation. To ensure stable operation, at a certain current strength and operating conditions, the pole-to-pole distance (MPD), metal and electrolyte levels are selected, each of which must meet certain requirements
.An increase in the productivity of existing electrolysers can be achieved by reducing metal losses (increasing the cathode current efficiency), as well as by increasing the current strength in electrolysers with certain design parameters and methods of their implementation.
These are, for example, a decrease in the cryolite ratio (CR) and maintenance of the optimum temperature of the electrolyte; optimization of the shape of the working space of the bath and more. Insufficient attention is paid to the issues of intensifying electrolysis production by increasing the current strength in electrolysers.
2. Analysis of ways to improve the performance of electrolyzers
A review of the literature shows that the technological issues of electrolysis intensification are considered only from the point of view of individual parameters that provide either for the provision of a heat-power regime or for the provision of conditions for the stability of MHD.
For example, the authors of the work proposed to correct the electrolyte with corrective additives in a given interval, which makes it possible to increase the technical and economic indicators of aluminum electrolysis, but only for the use of acidic electrolytes with CR at or less than 2.3 relative units.
In work , a method is proposed for conducting electrolysis in aluminum electrolysers with burnt anodes at a current of 85-92 kA, while maintaining the electrolyte temperature of 950-960 °C, maintaining a given level of electrolyte, metal and cryolite ratio of the electrolyte. But in this case, the expediency of the work depends on certain claimed technological parameters within the specified limits and is determined by the cost of raw materials, aluminum, electricity, labor, and other factors.
The paper presents a method of operation of electrolysers for the production of aluminum, which includes current control and regulation of the thermal regime of electrolysers. This method confirms that the maximum performance and the lowest power consumption on aluminum electrolysers are achieved when the most important technological parameters of the current strength, the interpolar distance (i.d.), the electrolyte temperature (TE), the shape of the working space (s.w.s.) are maintained in optimal ranges.
The intensification of the electrolysis process in the current series is the most important means of increasing production efficiency. The maximum values of current strength, current output and, accordingly, performance are achieved in relatively narrow ranges of electrolyte temperature and the inter-pole gap .
The temperature of the electrolyte shall be, on the one hand, sufficiently low to ensure a high current output and normal thickness of the on-board headstock and sufficiently high, on the other hand, to exclude formation on the bottom of the crust, long floorboards and large accumulations of sludge insoluble alumina.
A prerequisite for achieving high values of current strength, current output and low power consumption is to work in an optimal, narrow range of changes in the inter-pole gap, controlled by the magnitude of the voltage drop in the inter-pole gap .
Maintaining the thermal equilibrium of the aluminum bath at the optimum electrolyte temperature and the shape of the working space can be ensured at a constant current strength
.It is known that about 50% of the input power is irretrievably lost in each electrolyser in the form of heat losses. This value also increases slightly with increasing current strength. Therefore, with an increase in the current strength, it is also necessary to ensure the removal of excess input power (caused by an increase in the current strength) while maintaining the stable operation of the electrolyser and a stable FWS (Form of working space) (according to
, the minimum thickness of the casing should be within 10-15 cm).The initial data for calculating the balance are: geometric characteristics of the electrolyser, thermal and electrical conductivity of the materials used, technological parameters (current strength, processing frequency, etc.) . The operating voltage and electrolysis temperature are calculated when solving the heat-electric transfer system and are transmitted to the module for calculating the balance. The authors calculated the remaining values necessary for drawing up the balance using analytical formulas
, .Based on the given initial data for the operating electrolyser, on the basis of the programs, the temperatures inside and on the surface of the bath, the profile of the casing, the electrical balance and the operating voltage are calculated. The calculated temperatures make it possible to calculate the heat losses from the structural elements of the bath. The uneven distribution of temperatures along the height of the bath in the longitudinal and transverse sections is considered by the correction factor.
3. Methods and principles of research
At the Kazakhstan Electrolysis Plant, electrolysers of two types, GAMI-320 and NEUI-330, are installed and are in operation. The main differences between the electrolysers are the busbar and cathode casing designs. Due to the better configuration of the magnetic field from the busbar and the casing with improved aeration, NEUI-330 electrolysers have a higher design amperage and, therefore, are more prone to electrolysis intensification in all baths of the plant. The operated electrolysers have the same geometrical dimensions, similar to the anode current density. The electrolysers are equipped with a five-point automatic alumina supply system, one fluoride salt supply point is installed for GAMI-320 electrolysers, and two fluoride salt supply points are installed for NEUI-330 electrolysers. Both types of cells are equipped with a two-piece anode lifting mechanism for 40 anodes.
With an increase in the current strength, the technological regime, parameters and basic technical and economic indicators of electrolysis unambiguously change.
The optimal current strength with its increase can be understood as several of its values, namely:
- economic, at which the minimum cost of electrolytic aluminum will be obtained, which mainly depends on the price of sold aluminum, the cost of electricity consumed and the prices and quality of raw materials;
- technological, at which the highest basic technical and economic indicators are achieved – current efficiency and specific power consumption.
In the period from 2018 to 2020, studies were carried out for electrolysers with baked anodes GAMI-320 (design current 320 kA) and NEUI-330 (design current 330 kA), on the basis of JSC "Kazakhstan Electrolysis Plant" operated at increased amperage. During the period of normal operation, with an increase in the current strength, after an increase in the current strength by 15 kA, and 6 months after the increase in the current strength, experimental measurements of various technological, thermal and energy parameters (current strength, operating voltage, metal and electrolyte levels, temperatures electrolyte and outer surfaces of the casing, voltage drops in the cathode and busbar, and others).
The main parameters for the period of operation of electrolysers after increasing the current strength are given below:
- during the period of operation of the electrolysers, there was a decrease in the KO of the electrolyte from 2.22-2.16. A decrease in KO, as evidenced by various researchers, contributes to an increase in current efficiency;
- with stable operation of electrolysers, the optimum electrolyte temperature was ensured, equal to 949-955 °C, and the operating voltage was 4.21-4.03 V.
The analysis of the experiments carried out with an increase in the current strength in the electrolysers shows that the change in all parameters is linear. An increase in the current in the electrolyser causes the greatest effect on the thickness of the casing, the temperature of the cathode side lining, while the effect on the cathode base is practically negligible. The change in the temperature of the side of the cathode base is in the range of 2 - 3 °C, and the bottom does not exceed 1 °C. Figures 1, 2, 3 show graphs of energy parameters calculated using a mathematical model based on the results of increasing the current strength to 330 kA, in order to determine measures to further increase the current load.
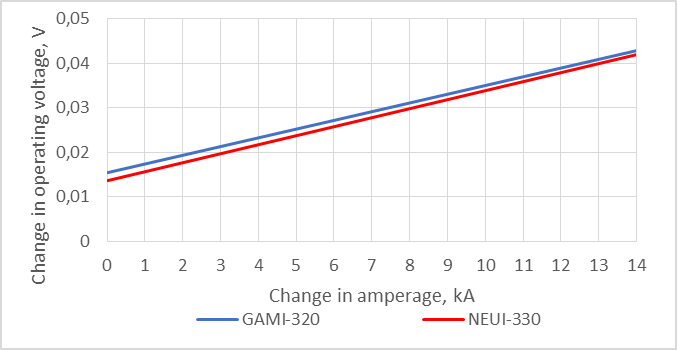
Figure 1 - Change in operating voltage with increasing current strength
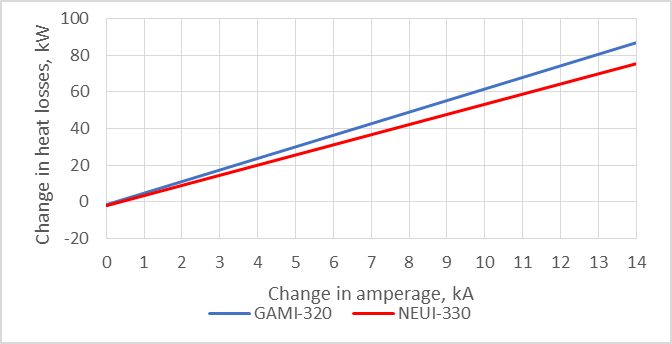
Figure 2 - Change in operating heat losses with increasing current strength
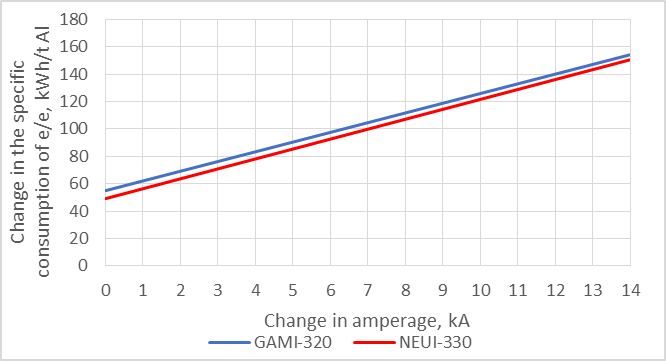
Figure 3 - Change in operating specific power consumption with increasing current strength
It is also possible to use cathode blocks of 50 % or 70 % graphitization, the use of cast-iron casting for fixing blooms, the use of less heat-conducting side lining of the cathode shell, the use of energy balance control systems of the electrolyser.
Figure 4 shows the increase in the process temperature with increasing current strength, obtained by calculation on a mathematical model.
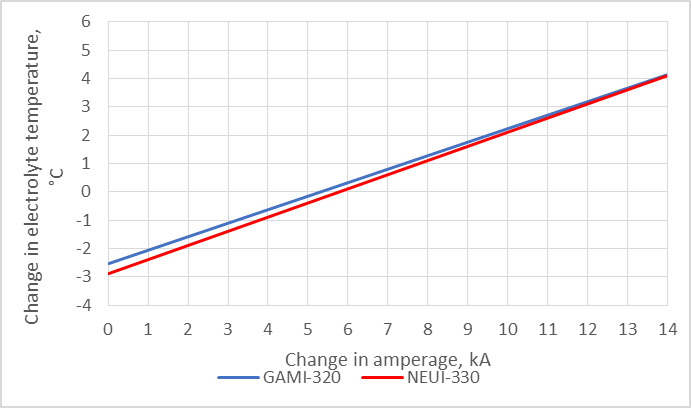
Figure 4 - Change in the temperature of the electrolyte with increasing current
Figure 5 shows the trend of decreasing the thickness of the electrolyser casing.
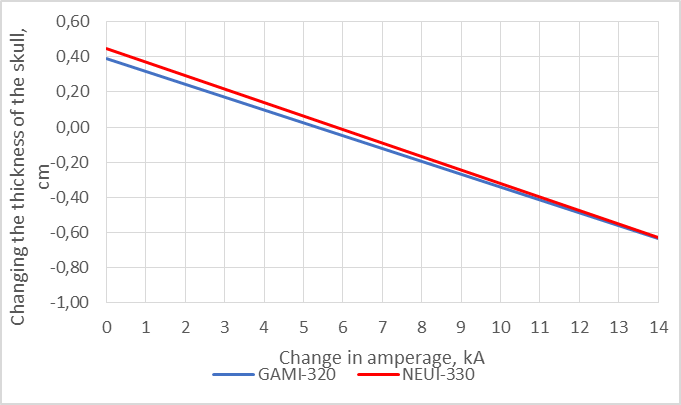
Figure 5 - Change in the thickness of the casing with increasing current strength
According to the results of the study, the dependence of the operating voltage on the KO of the electrolyte has been experimentally established: a decrease in KO leads to an increase in Up. However, a decrease in CO, despite an increase in the specific power consumption due to an increase in Up, turns out to be beneficial from the point of view of metal production.
In experimental electrolysers, the experimentally measured temperature of the bottom surfaces is lower, and the side and end walls are somewhat overheated in comparison with the period before the current increase.
It was experimentally determined that the voltage drop in the anode is comparable, and the voltage drop in the cathode is slightly higher, which is explained by the increased current in the electrolysers.
4. Conclusion
For the first time, the generalization of experimental data resulted in an empirical formula establishing the relationship between the energy efficiency and technological parameters of the electrolysis process and the structural characteristics of the electrolyser.
The results of the conducted studies showed that the promising directions for reducing the heat input are the voltage reduction and, accordingly, the MPR, however, with a decrease in the MPR, an increase in the MHD instability is observed, which can affect the decrease in the current efficiency.
In the course of the study, it was experimentally obtained that, in comparison with the design current strength (320 kA), an increase in the current strength by 1 kA leads to an increase in the productivity of the electrolyser by 0.66% (while maintaining the same current output).
With an increase in the current strength, it was possible to maintain an optimal ratio of energy parameters with a normal technological regime, mainly due to a decrease in voltage, a decrease in the cryolite ratio and the use of slot anodes. The introduction of hearth blocks with a graphite content of 70-80%, which contribute to reducing the thermal load of the electrolyser, can be considered promising for increasing the current strength. Their use is most effective when the anode current density is more than 0.78-0.8 A/cm2.
Thus, the use of modern methods of processing and analysis of data on technological parameters of the electrolyser, as well as the selection and optimization of parameters affecting the stabilization of the electrolysis process, in this article substantiates the feasibility of increasing the current strength, which makes it possible to increase productivity and increase the profitability of the applied technical solutions.