Conditions of glass-metal composite formation
Conditions of glass-metal composite formation
Abstract
The use of glass-metal composite (GMC) as an alternative material to titanium in the construction of strong hulls of deep-sea submersibles will make it possible to create deep-sea vehicles for operation at any existing ocean depths. The article examines the interaction of liquid glass and aluminium shell surface during the fabrication of glass-metal composites. The results of research on glass compositions with different glass cooking temperatures are given. The research of conditions providing reliable connection of glass layer with metal cladding, and also research of physical and chemical properties of the connecting layer, is carried out. Comparison of the character of diffusion layers "glass-metal" in the obtained glass-metal composites has been carried out.
1. Введение
Главной проблемой при изготовлении подводных аппаратов для использования на глубинах свыше 8000 метров является наличие лишь небольшого числа (ряда) прочных и легких материалов. В основном для этих целей применяется титан и его сплавы, а также дорогостоящие углепластики. Хорошо известно, что по показателям теоретической удельной прочности и цене титан уступает обычному силикатному стеклу: приблизительно в полтора раза по удельной прочности и не менее чем в 50 раз по цене , . Высокая природная прочность практически применяемых стекол в отсутствие дефектов подтверждена экспериментально в соответствующих работах , . Установлено, что неорганическому стеклу присуща высокая природная прочность независимо от его размеров и фазового состояния (как для стекловолокна, так и для листового или массивного стекла).
Однако эксплуатационная прочность стекла составляет менее 1% от природной прочности стекла. Низкая прочность используемого стекла объясняется ослаблением его структуры из-за наличия в его структуре, и особенно на поверхности, разного рода разупрочняющих дефектов, среди которых наиболее типичными и опасными являются поверхностные микротрещины. Их устранение повышает прочность стекла в сотни раз .
2. Методы и принципы исследования
Авторами многих работ предложены различные методы защиты от микротрещин или их удаления с поверхности стекла. На рисунке 1 приведены основные методы упрочнения стекла и пределы прочности в МПа, достигнутые с их использованием.
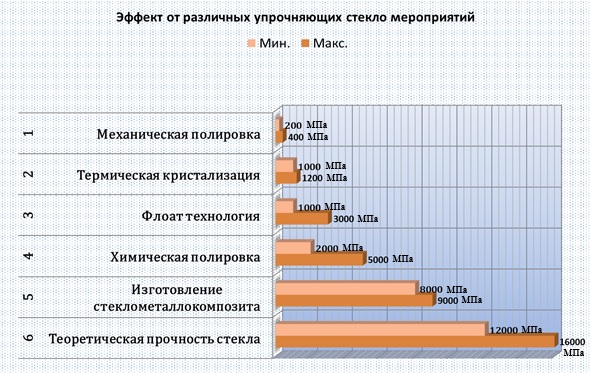
Рисунок 1 - Способы упрочнения стекла
В составе СМК стеклянные слои формируются без образования поверхностных микротрещин, а металлические обшивки защищают его от непосредственного взаимодействия с окружающей средой. Освобождение от поверхностных микротрещин придает стеклянным слоям и СМК в целом исключительно высокую прочность и ударную стойкость.
В СМК реализуются все три главных условия обеспечения бездефектной структуры силикатного стекла. Надежно соединенные со стеклянными слоями металлические прослойки и обшивки при остывании, вследствие более высокого коэффициента температурного расширения, сокращают свои размеры более интенсивно, чем стеклянные слои . Тем самым они стягивают поверхности стеклянных слоев, предотвращая появление в них деформаций растяжения и исключая появление поверхностных микротрещин . Обшивки исключают непосредственный контакт стеклянных слоев с внешней средой, изолируя их от воздействия влаги (ОН – групп) и других негативных влияний. Внутренние дефекты исключаются формированием стеклянных слоев под давлением.
Применение СМК как альтернативного материала в построении прочных корпусов глубоководных подводных аппаратов позволит создавать глубоководную технику для работы на любых существующих океанских глубинах при существенном сокращении финансовых затрат. Важной задачей получения СМК является изучение взаимодействия жидкого стекла и поверхности алюминиевой оболочки при заливке расплава в алюминиевую оболочку корпуса.
3. Основные результаты
В работе исследованы условия образования диффузионного слоя «стекло-алюминий» при получении СМК на основе стекол, имеющих различные температуры варки: тугоплавких составов 54,60SiO2-14,08Al2O3-22,63CaO-0,59MgO-3,12B2O3-3,07Na2O, 63,50SiO2-6Al2O3-6,40CaO-2,75MgO-8,37B2O3-8,37B2O3-12,95Na2O (температуры варки 1400…1600 °С), среднеплавких 40SiO2-10Al2O3-20Na2O-40B2O3 (1100…1300 °С) и легкоплавких (ниже 1000 °С).
3.1. Исследование границы раздела алюминия и стекла с высокой температурой плавки
Температура варки стекол превышает 1500 °С. Температуры, при которых осуществлялась их заливка, не опускались ниже 1400 °С.
Высокоплавкие стекла составов 54,60SiO2-14,08Al2O3-22,63CaO-0,59MgO-3,12B2O3-3,07Na2O, 63,50SiO2-6Al2O3-6,40CaO-2,75MgO-8,37B2O3-8,37B2O3-12,95Na2O заливались в алюминиевую оболочку при температурах более 1400 °С.
Условия проведения первого эксперимента:
‒ температура заливки стекломассы 1450 °С;
‒ температура алюминиевой оболочки (изложницы) 150 °С;
‒ скорость вращения центрифуги составляла 2000 об/мин.
В дальнейших экспериментах менялись температуры алюминиевых оболочек до 300, 450 °С и скорости вращения центрифуги в диапазоне 3000, 4000, 5000 об/мин.
Скорость охлаждения поддерживалась на уровне 400 °С в минуту. Тепловое равновесие устанавливалось в районе температур 500…600 °С.
Полученный образец СМК охлаждался до температуры стеклования, отжигался в течение 6 часов. После этого печь отключалась, и в течение 10 часов образец охлаждался в печи до комнатной температуры . Диффузионный слой полученных образцов исследовался различными методами.
Исследованием физического состояния зоны спаивания стекла с алюминием с помощью сканирующего микроскопа выявлено образование диффузионного слоя «алюминий-стекло», вследствие изменения распределения атомов алюминия в поверхностной зоне стекла (рисунок 2).
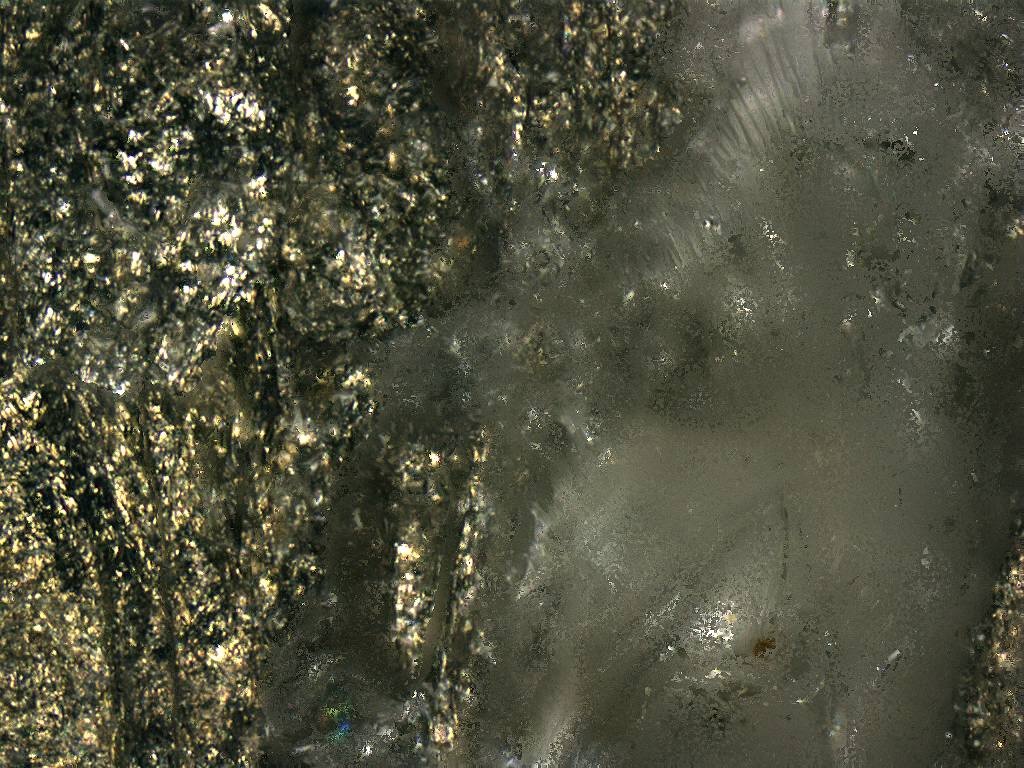
Рисунок 2 - Изображение поверхности алюминия полученного при заливке стекла 54,05SiO2-13,04Al2O3-19,80CaO-0,36MgO-7,30B2O3-2,00Li2O-0,05Na2O в алюминиевый корпус при температуре 1450 °С и скорости центрифуги 2000 об/мин
Очевидно, что столь жесткие условия получения СМК приводят к некачественному сцеплению стекло–металл. Вместо образования ровного диффузионного слоя с равномерным распределением частиц стекла и алюминия образуются участки с неравномерными напряжениями на стекло, что должно привести к его растрескиванию и резкому уменьшению прочности СМК. Использование корпусов из таких материалов не целесообразно.
Характер диффузионного слоя был исследован с помощью электронной микроскопии. В отличие от оптической микроскопии, позволяющей исследовать довольно большие участки границы раздела, электронная микроскопия проводит точечные измерения глубины диффузионного слоя.
На рисунках 3, 4 приведены типичные электронные изображения участка поверхности алюминия при заливке стекол при высоких температурах. Видно, что стекло состава 54,05SiO2-13,04Al2O3-19,80CaO-0,36MgO-7,30B2O3-2,00Li2O-0,05Na2O, залитое при температуре 1450 °С и скорости центрифуги 2000 об/мин, подплавляет поверхность алюминия и образует диффузионный слой глубиной до 100 мкм.
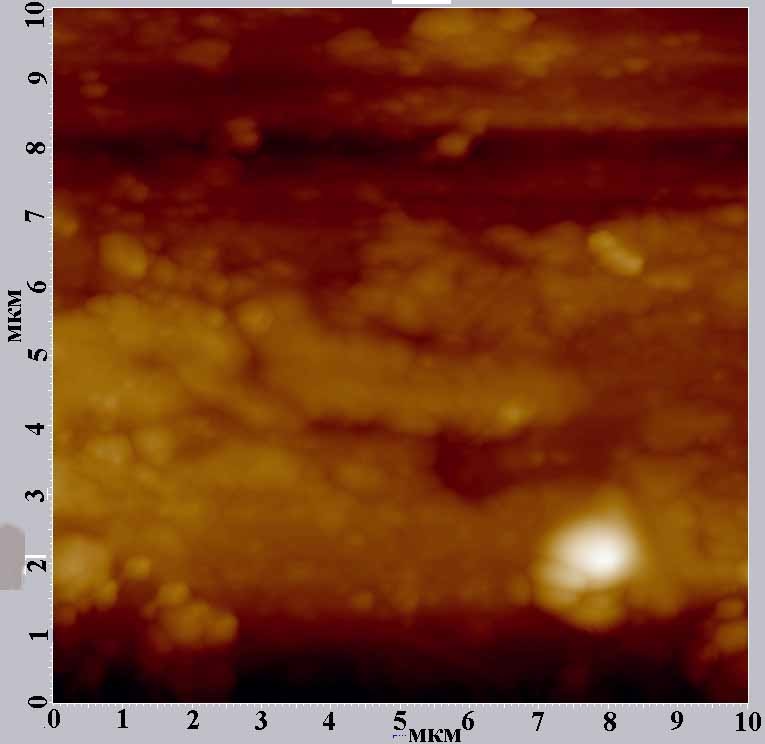
Рисунок 3 - Снимок поверхности алюминиевого корпуса на границе раздела стекло-алюминий, полученного заливкой стекла состава 54,05SiO2-13,04Al2O3-19,80CaO-0,36MgO-7,30B2O3-2,00Li2O -0,05Na2O при температуре 1450 °С
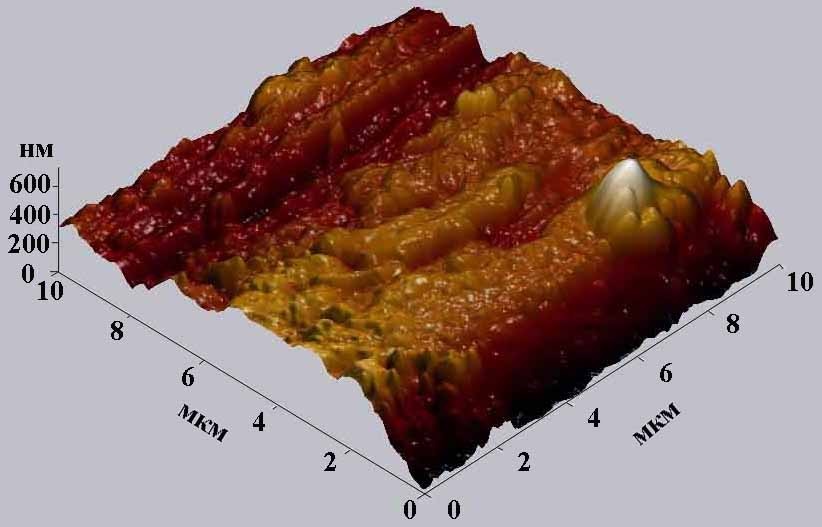
Рисунок 4 - 3D-изображение поверхности алюминия, полученное при обработке снимка
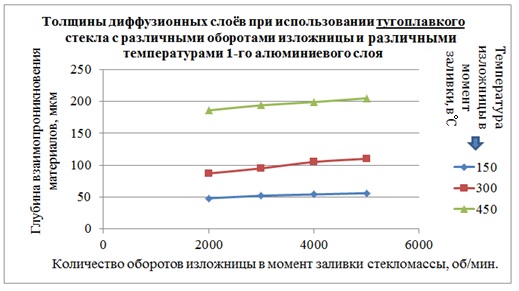
Рисунок 5 - Зависимость толщины диффузионного слоя от скорости вращения и температуры изложницы в момент заливки стекломассы
В качестве стекла со средней температурой варки (до 1300 °С) и температурой заливки около 1000 °С использовались боратные стекла состава 40SiO2-10Al2O3-20Na2O-40B2O3. Эти стекла выплавлялись в платиновых тиглях при температурах 1200…1250 °С и заливались в кожух корпуса, вращающего со скоростями до 5000 об/мин.
Тепловое равновесие в этих случаях наступает при температурах их стеклования 450…500 °С. Глубина диффузионного слоя, получаемого при этом, варьирует до 150 мкм. Граница «алюминий-среднетемпературное стекло» ровная, и, в отличие от границы «алюминий–высокотемпературное стекло», остается качественной при скоростях вращения 5000 об/мин.
На рисунке 6 приведены результаты исследования толщины слоев среднеплавких стекол от условий их получения.
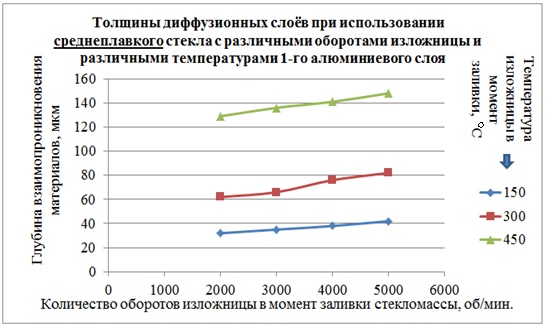
Рисунок 6 - Зависимость толщины диффузионного слоя среднеплавких стекол от условий изготовления образцов СМК
Проведено исследование условий образования диффузионных слоев «алюминий–низкоплавкое стекло» фторсодержащих алюмоборатных стекол общей формулой xMgB204-yAl203-zMgF2-hLiF, температура плавки которых ниже 1000 °С.
Высокая стойкость к кристаллизации низкоплавких стекол позволяет проводить ступенчатый подъем и снижение температур, исключающих возникновение опасных напряжений в диффузионном слое «алюминий-низкоплавкое стекло».
Интенсивное взаимодействие легкоплавкого стекла с алюминием происходит при температурах от 800 °С до 900 °С.
Взаимодействие при смачивании алюминия расплавом стекла не приводит к образованию новых кристаллических фаз в диффузионных слоях «алюминий-низкоплавкое стекло».
С помощью сканирующего микроскопа выявлено образование диффузионных слоев с толщинами до 90 мкм.
Механизм адгезии и смачивания расплавом стекла алюминия происходит аналогично химическому взаимодействию, которое проявляется в виде «порога смачивания» на зависимости угла смачивания от температуры . Уменьшение угла смачивания наступает в области температур 680…700 °С, в которой угол смачивания изменяется от 70° до 35°.
Введение в состав стекол небольших добавок PbO, PbF2, Bi203, отличающихся высокой коррозионной активностью к алюминию и снижающих как поверхностное натяжение, так и вязкость расплава стекла, заметно улучшают способность фторсодержащих стеклообразующих расплавов смачивать алюминий.
Повышение прочности соединения достигается после 35…40 минутной выдержки при температуре стеклования стекла.
Введение в состав боратного стекла фторидов до 10 мол. % (MgF2, PbF2, CdF2) снижает кристаллизационную способность расплава стекла, увеличивает температурный интервал размягчения, улучшает способность фторсодержащих расплавов смачивать алюминий, и снижает температуру спаивания при высоких значениях микротвердости стекла.
Для получения надежного спая, лишенного внутренних напряжений, за счет образования переходного слоя и исключения вторичного спекания алюминия, термообработку следует вести в течение не менее 6 часов.
На рисунке 7 представлены результаты исследований зависимости толщины диффузионных слоев от условий получения СМК.
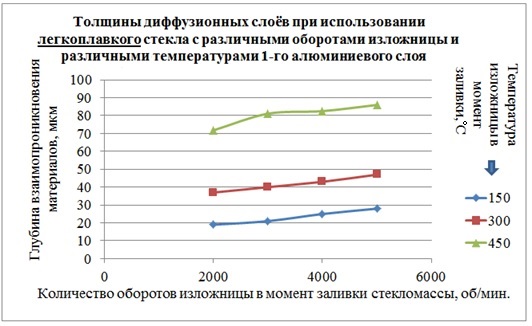
Рисунок 7 - Зависимость толщины диффузионного слоя легкоплавких стекол от условий изготовления образцов СМК
4. Заключение
В результате исследования диффузионных слоев «алюминий-стекло» выяснилась устойчивая зависимость ширины и прочности диффузионного слоя от состава стеклянного слоя. Именно состав стекла, а также нюансы технологического процесса определяют все технологические условия изготовления стеклометаллокомпозита. Ширины диффузионных слоев тугоплавких стекол лежат в пределах от 50 до 200 мкм, для среднеплавких стекол пределы ширины линий ограничиваются размерами от 30 до 150 мкм, для легкоплавких стекол – от 20 до 90 мкм.
Зависимость ширины диффузионных слоев от температуры изложниц в момент заливки стекла также сильно выражена. Для тугоплавкого стекла при температуре изложницы ≈ +150 °С, ширина диффузионного слоя составляет 50 мкм, а при температуре изложницы ≈ +450 °С значение ширины диффузионного слоя в четыре раза больше. При этом размеры ширины диффузионных слоев «алюминий–стекло» могут иметь практически равные значения для тугоплавких, среднеплавких и легкоплавких стекол при определенных условиях заливки. Например, диффузионный слой с шириной 80 мкм получается для легкоплавких стекол при температуре изложницы ≈ +450°С, а для тугоплавких и среднеплавких стекол при температуре ≈ +300 °С.
Толщины диффузионного слоя мало зависят от скорости вращения центрифуги, изменяясь в пределах 10…20 мкм при изменении скорости от 2000 до 5000 об/мин для всех составов стекол. Однако качество этого слоя резко ухудшается при увеличении скорости вращения до 5000 об/мин, и при этой скорости вращения приводит к резкому уменьшению прочности СМК, в связи с чем использование корпусов из таких материалов не целесообразно.