ИЗМЕНЕНИЕ СОСТАВА ТВЕРДОГО РАСТВОРА Fe-Pd В ОДНОСТАДИЙНОМ МЕТОДЕ СИНТЕЗА МЕТАЛЛ-УГЛЕРОДНЫХ НАНОКОМПОЗИТОВ
ИЗМЕНЕНИЕ СОСТАВА ТВЕРДОГО РАСТВОРА Fe-Pd В ОДНОСТАДИЙНОМ МЕТОДЕ СИНТЕЗА МЕТАЛЛ-УГЛЕРОДНЫХ НАНОКОМПОЗИТОВ
Научная статья
Ефимов М.Н.1, *, Васильев А.А.2, Муратов Д.Г.3, Карпачева Г.П.4, Сидорова Е.Н.5,
Дзидзигури ЕЛ.6, Ковтун А.В.7
1 ORCID: 0000-0001-7996-474X;
1, 2, 3, 4 Институт нефтехимического синтеза имени А.В. Топчиева РАН, Москва, Россия;
2, 3, 5, 6, 7 Национальный научно-технический университет "МИСиС", Москва, Россия
* Корреспондирующий автор (efimov[at]ips.ac.ru)
АннотацияПредложена одномоментная процедура одновременной подготовки углеродной поддержки на основе полиакрилонитрила и биметаллических наночастиц Fe-Pd. Показано влияние условий синтеза на структурные характеристики металлоуглеродных нанокомпозитов. Установлено, что размер кристаллитов наночастиц металлической округлой формы, иммобилизованных в карбонизированной полимерной матрице, увеличивается с повышением температуры синтеза. Константа решетки твердого раствора на основе fcc-Pd в нанокомпозите меньше, чем характеристика объемного fcc-Pd и уменьшается с увеличением температуры синтеза.
Ключевые слова: Наночастицы Fe-Pd, ИК-пиролиз, металл-углеродный нанокомпозит, твердый раствор.
EVOLUTION OF Fe-Pd SOLID SOLUTION COMPOSITION IN ONE-STEP METAL-CARBON NANOCOMPOSITE FABRICATION METHOD
Research article
Efimov M.N.1, *, Vasilev A.A.2, Muratov D.G.3, Karpacheva G.P.4, Sidorova E.N.5, Dzidziguri E.L.6, Kovtun A.V.7
1 ORCID: 0000-0001-7996-474X;
1, 2, 3, 4 A.V. Topchiev Institute of Petrochemical Synthesis RAS, Moscow, Russia;
2, 3, 5, 6, 7 National University of Science and Technology "MISiS", Moscow, Russia
* Corresponding author (efimov[at]ips.ac.ru)
AbstractThe one-step procedure of simultaneous preparation of polyacrylonitrile-based carbon support and Fe-Pd bimetallic nanoparticles was proposed. The effect of synthesis conditions on the metal-carbon nanocomposite structural characteristics was shown. It was found that the crystallite size of the metallic rounded shape nanoparticles immobilized in the carbonized polymer matrix increases as synthesis temperature rises. The lattice constant of a solid solution based on fcc-Pd in the nanocomposite is smaller than that characteristic of bulk fcc-Pd and decreases with increasing synthesis temperature.
Keywords: Fe-Pd nanoparticles, IR pyrolysis, metal-carbon nanocomposite, solid solution.
IntroductionAt present, the development of new and improvement of existing production methods of nanomaterials with specified properties is one of the priority scientific and industrial tasks. The study of nanosystems features, their structural characteristics and functional properties, depending on the conditions of preparation, makes it possible to tune the parameters of the material during its synthesis and form the final product with specified properties. In general, the nanocomposites may be described as materials consisting of two parts: support and filler [1]. In the case of the metal-carbon nanocomposite, a support can be obtained from many types of carbonaceous precursors such as coal, natural and synthetic polymers, etc., whereas metal nanoparticles play the role of a filler. The features of these systems are determined by the nature and properties of carbon and metal. For example, various types and forms of carbon can define different properties of the carbon support: a porosity, an ability to hold and distribute metal nanoparticles, electrochemical and thermal properties, etc. The functional properties of nanocomposites are provided by the properties of metal nanoparticles which can have catalytic, medical and antibacterial, ferromagnetic and other various properties. Therefore, carbon-based nanocomposites with metal nanoparticles have a very wide range of their applications [2-4]. In order to improve functional properties or expand the scope of possible applications, the preparation alloy or bimetallic nanoparticles is suggested [5], [6], [7]. In addition to the mentioned changes, in some cases the use of alloys or bimetallic nanoparticles can be considered as a route to reduce the cost of production of metal-carbon nanocomposites. Thus, noble metals are widely known as effective catalysts for industrial processes [2], [7], [8]. However, catalysts based on noble metal nanoparticles are expensive. In order to cost-minimize, the strategy of the alloy or bimetallic ‘core-shell’ structured nanoparticles fabrication was proposed [9], [10]. The catalysts based on monometallic Pd and its alloys nanoparticles show their efficiency in important industrial and promising processes such as Fischer-Tropsch synthesis [11], [12], steam reforming of alcohol [13], [14], hydrogenation reactions, etc [9], [15]. Besides, Pd forming hydrids has hydrogen storage properties [16]. Earlier, we reported on the study of the simultaneous palladium nanoparticles formation and polyacrylonitrile carbonization [17]. Hydrogen released as a result of dehydrogenation of the backbone polymer chain dissolved in the metal leading to a change in the lattice period of nanoscale palladium.
Fe nanoparticles have also catalytic activity in petrochemical reactions. In addition, the attention of researchers focused on mono- and bimetallic Fe nanoparticles due to their excellent ferromagnetic properties [18]. On the other hand, Fe-Pd alloys were reported as ferromagnetic shape-memory materials [19].
To date, the most general metal-carbon nanocomposite fabrication method employs wet synthetic chemistry, which involves the reduction of metal precursors in a solvent and impregnation of the carbon support with it. This strategy needs preparation of the carbon support at first and at the second stage an introducing metal nanoparticles is carried out followed by heating for several hours or applying chemical metal reduction. This route seems more complicated, considering how long it takes for convectional heating to form a carbon support and reduce a metal. Polymers employed as carbon precursors for a support and IR radiation heating provide a tremendous reduction in the time of metal-carbon nanocomposites synthesis. Since this method is scalable, cost-efficient and provides tuning of structural characteristics during the material synthesis, it can be proposed as a very promising route for the industrial fabrication of metal-carbon nanocomposites with desired properties.
In our work, the one-step procedure of metal-carbon nanocomposite preparation based on IR pyrolyzed polyacrylonitrile and Fe-Pd nanoparticles was proposed. We studied the evolution of Fe-Pd solid solution depended on synthesis temperature and suggest the model of alloy nanoparticles formation.
Materials and methods
Metal-carbon nanocomposite preparation
Metal-carbon nanocomposite based on Fe-Pd nanoparticles supported on polyacrylonitrile-based carbon were fabricated via pyrolysis of the joint solution of polyacrylonitrile and metal salts under infra-red heating in the temperature range of 100-900 ºC. The heat treatment was performed in the laboratory device of incoherent IR annealing [20] providing heating temperature up to 900 °C in nitrogen atmosphere. The halogen lamps KG-220 (total power of 24 kW) were applied as a radiation source, which had maximum emission wavelength in the region of 0.9–1.2 µm. Samples were placed in a graphite case. The intensity of the IR radiation controlled by the temperature of heating of the sample, measured by a chromel-alumel thermocouple. The accuracy of temperature control was 0.25 ºC.
PAN was prepared according to the described procedure [20]. The joint solution of PAN, Fe(С5Н7О2)3 (Acros Organics) and PdCl2 (Acros Organics) in DMF was dried in Petri dish at 80 ºC. The metals were taken at the atomic ratio of 60:40 (Fe:Pd) and the total amount of metals was 20 wt%. The obtained precursor film was chopped and pre-carbonized at 200 °C for 20 min in air followed by the main annealing stage at the desired temperature from the range of 300-900 °C in nitrogen atmosphere. In the case of lower temperatures (100 and 200 °C) the preliminary annealing was not conducted.
Sample characterization
Powder XRD analysis was performed using a diffractometer “Difray” 401 with Bragg–Brentano focusing, using Cr-Kα radiation in the continuous mode (wavelength 0.229 nm) at room temperature. The average coherent scattering regions (CSR) size was calculated by the approximation method of the broadening of the diffraction peaks.
The lattice constants of the metal-containing phase were determined by XRD data analysis. In order to determine the composition of the solid solution in the metallic phase, the technique [17] based on comparing the periods of the solvent lattice in bulk and nanosized states was applied:
anano – abulk = ±∆a | (1) |
where anano, nm is the lattice constant of the nanosize solvent, abulk, nm is the lattice constant of the solvent in bulk state. The graph of the dependence of the dissolved element content in the nanosized solvent on its lattice constant was plotted via shifting by ±Δa value.
The morphology of nanopowders was studied with LEO912 AB OMEGA transmission electron microscope. Elemental composition and elemental mapping were carried out by X-ray fluorescence analysis using a X-ray analytical microscope-microprobe PAM-30μ.
Results and discussion
The preparation of metal-carbon nanocomposites IR-PAN/Fe-Pd was carried out under the conditions of IR heating. The procedure of the formation of similar metal-carbon nanocomposites was described in [17], [21]. It is worth noting that IR annealing is a more efficient route to carbonize the polymer. IR radiation provides a decrease of carbonization and metallic nanoparticles formation time. It takes only a few minutes for the process instead of several hours for conventional heat treatment.
Thus, PAN is carbonized and structured simultaneously and interdependently with the formation of ordered carbon structures and the reduction of metals in the presence of hydrogen released during the polymer chain dehydrogenation under IR heating.
As shown by the TEM images (Fig. 1), mostly metallic nanoparticles (dark areas on microphotographs) have a rounded shape, close to spherical, and immobilized in a carbon matrix (gray area). However, shapes similar to triangle, square, hexagon are observed and may lead to a change of the material functionalities [22].
In addition, large dark formations can be found on microphotographs. These species can be either large polymeric layers or large particles of the metallic phase. During the preparation of the nanocomposite, various reactions and structural transformations take place. The type and sequence of these reactions change as the pyrolysis temperature increases. Therefore, in some areas the conditions for the coagulation of nanoparticles may arise. As can be seen from Fig. 1 at higher temperatures above mentioned areas and particles are observed more often. Furthermore, the obtained micrographs show that the polymer matrix has a layered structure, and at temperatures above 700 °C, structured carbon tubes are formed.
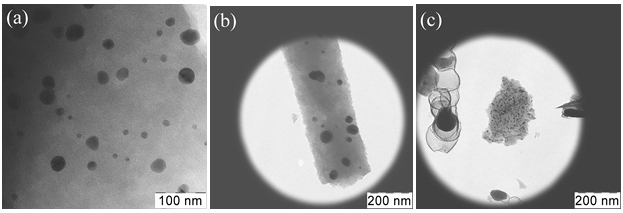
Fig. 1 – TEM images of the IR-PAN/Fe-Pd samples obtained at 500 (a), 600 (b), and 700 °C (c)
The generation and growth of various carbon forms in the structure of the composite depend both on the nature of the metal, which is the catalyst of the process, and on the source of the formation of the carbon phase [23], [24]. The average linear diameters of CSR of metal-containing nanoparticles are calculated and shown in Table 1.
The obtained results show that the size of palladium phase CSR is a few nanometers at the synthesis temperature range of 200-400 °C. The preparation of the metal-carbon nanocomposites at 500 °C provides the increase of CSR size up to 28 nm. As the fabrication temperature rises, the diameter of the CSR does not change much, however, a general tendency for nanoparticle size increase is observed. Most probably, such results of the metallic phase dispersity study are related to the reduction temperatures of palladium and iron in the system, which are about 150 and 500 °C, respectively.
Table 1 – The average linear diameters of CSR of metal-containing nanoparticles
Synthesis temperature, °C | CSR average size, nm |
200 | 8 |
250 | 5 |
300 | 4 |
400 | 8 |
500 | 28 |
600 | 34 |
700 | 23 |
800 | 30 |
900 | 41 |
Palladium and iron display unlimited solubility in the liquid phase. As the temperature decreases, the alloys crystallize to form a continuous series of austenitic solid solutions [25], [26]. Table 2 shows the results of the elemental analysis of the metallic phase.
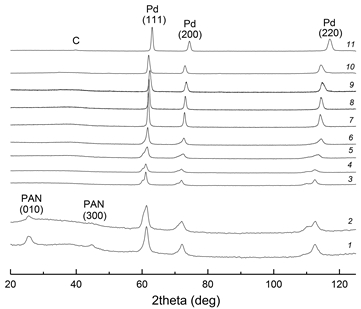
Fig. 2 – XRD patterns of IR-PAN/Fe-Pd nanocomposite, synthesized at 100 (1), 150 (2), 200 (3), 250 (4), 300 (5), 400 (6), 500 (7), 600 (8), 700 (9), 800 (10) and 900 °C (11). The polymer crystal structure is still observed at XRD patterns of samples obtained at 100 (1) and 150 °C (2) in air. The preparation of the nanocomposites at temperatures above 200 °C was conducted in inert atmosphere
Quantitative analysis showed that the content of metal components is very close to the initial composition of Pd and Fe.
The phase analysis presented in Fig. 2 shows the presence of two reflection peaks of the crystal structure of PAN in the samples synthesized at 100 and 150 °C.
An amorphous halo corresponding to the amorphous component of the polymer is also observed at angles 2θ = 20-50°. As the annealing temperature increases, the crystalline and amorphous phases of PAN are reduced and disappear, and a carbon phase is simultaneously formed. The phases of palladium and amorphous carbon are observed on the XRD patterns of the samples obtained at temperatures 200-900 °C. The phase of metallic iron is not found due to the formation of a solid solution of iron in palladium.
Table 2 – The results of element analysis of metal-carbon nanocomposites prepared at different temperatures
Synthesis temperature, °С | Element | Content, wt% | Content, at% |
100 | Pd | 58.5 | 42.6 |
Fe | 41.5 | 57.4 | |
150 | Pd | 59 | 43.1 |
Fe | 41 | 56.9 | |
200 | Pd | 60 | 44.1 |
Fe | 40 | 55.9 | |
250 | Pd | 59 | 43.1 |
Fe | 41 | 56.9 | |
300 | Pd | 59.3 | 43.4 |
Fe | 40.7 | 56.6 | |
400 | Pd | 58 | 42.1 |
Fe | 42 | 57.9 | |
500 | Pd | 62 | 46.2 |
Fe | 38 | 53.8 | |
600 | Pd | 58.2 | 42.3 |
Fe | 41.8 | 57.7 | |
700 | Pd | 56.5 | 40.6 |
Fe | 43.5 | 59.4 | |
800 | Pd | 55 | 39.1 |
Fe | 45 | 60.9 | |
900 | Pd | 56 | 40.1 |
Fe | 44 | 59.9 |
Despite the fact that reflexes of the iron-containing phase are not observed on the diffractograms, it can be assumed that iron acetylacetonate starts to decompose to Fe2O3 at a given temperature.
At the diffraction maxima (111) of the samples obtained at 200, 250 and 300 °C, a shoulder is observed from the side of smaller angles (Fig. 3). The peaks are shifted toward smaller angles compared to higher temperatures and are located between PdH hydride and pure Pd dashed lines. According to most researchers, palladium and hydrogen form two limited solid solutions: an α-solid solution containing approximately 30 volumes of hydrogen per volume of palladium at room temperature; β-solid, containing at room temperature 1023 - 1300 volumes of hydrogen per 1 volume of palladium [27].
Fig. 3 – Small-angle region of XRD patterns of IR-PAN/Fe-Pd nanocomposite. The left vertical line is corresponding to PdH, right line - pure Pd
As hydrogen dissolves in palladium, the lattice parameters continuously increase from 0.3889 to 0.3895 nm. When the atomic ratio of H:Pd reaches about 0.02 (the maximum for a solid solution), a β phase appears, which has a lattice constant of approximately 0.4025 nm.
Both phases exist up to a ratio of H/Pd = 0.58, at which the structure of the α-solid solution completely disappears. A further increase in the hydrogen content causes the expansion of the β-phase lattice parameters. At a ratio of H/Pd = 0.70 and a temperature of 25 °C, the parameters of the β-phase lattice reach 0.4040 nm.
With increasing temperature, the maximum ratio of H/Pd at which there is an α-solid solution increases, whereas the minimum ratio at which the β-phase exists is reduced. At temperatures above 300 °C there is only one solid solution. The hydrogen-saturated palladium decreases its specific gravity, the electrical conductivity, the strength and elongation decrease as compared to pure palladium.
Palladium is well known for dissolving hydrogen very readily [16], [17], [27]. At temperatures of 200-300 °C, the amount of hydrogen in the metal reaches 655 volumes. In this case, the solid solution of introduction is formed leading to an increase of the solvent lattice period. Therefore, the shift of the diffraction maximum toward smaller angles and its bifurcation occurs due to the formation of a hydrogen solution in palladium of two dominant concentrations.
The current study of the structure of the obtained materials shows that as the IR annealing temperature increases, the peak corresponding to palladium shifts toward larger angles and becomes more intense, narrow and symmetrical (Fig. 3). The changes in the crystal lattice of palladium can be caused by the following reasons: dissolution of hydrogen, dissolution of iron and, so-called, size factor. The lattice period is increased by the dissolution of hydrogen and is decreased by the dissolution of iron. In most cases [28], the nanoparticle size reduction leads to the decrease of the crystal structure parameters.
Table 3 – Values of lattice constants of palladium phase in PAN/Fe-Pd nanocomposites
Synthesis temperature, °C | Lattice constant a, nm |
100 | 0.3889 |
150 | 0.3848 |
200 | 0.3867 |
250 | 0.3887 |
300 | 0.3885 |
400 | 0.3863 |
500 | 0.3855 |
600 | 0.3845 |
700 | 0.3833 |
800 | 0.3809 |
900 | 0.3791 |
bulk | 0.3890 |
Ultradispersed nanodiamond-supported Pd [17] | 0.3881 |
XRD analysis has shown (Table 3) that most part IR-PAN/Fe-Pd nanocomposites have a smaller lattice constant of fcc Pd phase than the value corresponding to bulk palladium [29] due to either iron dissolution or size factor, or both these reasons.

Fig. 4 – The dependence of the lattice constant of palladium on the amount of iron in bulk (1) and nanosize (2) solid solution
The estimated dependence of the change of the lattice constant of nanoscale palladium on the amount of iron dissolved (Fig. 4) is determined applying the lattice constant value of ultradispersed nanodiamond-supported palladium, according to which the composition of the resulting metallic phase is quantitatively evaluated. The results of the calculation are given in Table 4 and show that the iron content in the solid solution increases with the pyrolysis temperature and at 800-900 °C is equal to the elemental composition of the samples (Table 2).
Table 4 – The estimation of the solid solution composition of iron in palladium as a function of the IR pyrolysis temperature
Synthesis temperature, °C | Solid solution composition Fe:Pd, at% |
300 | - |
400 | 13 : 87 |
500 | 17 : 83 |
600 | 24 : 76 |
700 | 32 : 68 |
800 | 42 : 58 |
900 | 47 : 53 |
It can be suggested that at the synthesis temperature of 300-700 °C a solid solution of iron in palladium has a composition close to elemental. The difference between the compositions is caused by the dissolution of hydrogen in palladium, which increases the lattice period, thereby compensating for its decrease due to the dissolution of iron. The solid solution formation scheme based on the results of the study can be proposed (Fig. 5).
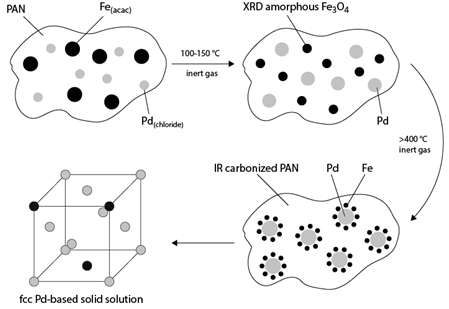
Fig. 5 – The scheme of the formation of the solid solution of iron in palladium
The pyrolysis of polyacrylonitrile at 100-150 °C leads to a release of hydrogen from the backbone polymer chain. Therefore, palladium chloride reduction starts immediately since the thermodynamic equilibrium temperature of this reaction is below 0 °C. The metallic iron appears in the samples at temperatures above 400 °C. In this case, it is advantageous to employ palladium nanoparticles as a substrate for the iron phase nuclei. Since palladium and iron form a continuous series of solid solutions, Fe atoms dissolve in Pd forming a nanosized solid solution.
Conclusion
Thus, the method of IR pyrolysis of the precursor based on a polymer and metal salts led to significant reduction of synthesis time was proposed. The polyacrylonitrile-based metal-carbon nanocomposite C-Fe-Pd was obtained via IR-annealing. The effect of synthesis conditions on the metal-carbon nanocomposite structural characteristics was shown. It was found that the crystallite size of the metallic rounded shape nanoparticles immobilized in the carbonized polymer matrix increases as synthesis temperature rises. Furthermore, it has been determined that in this system a solid solution of iron in palladium is formed at all annealing temperatures studied. The lattice constant of a solid solution based on fcc-Pd in an IR-PAN/Fe-Pd nanocomposite is smaller than that characteristic of bulk fcc-Pd and decreases with increasing synthesis temperature.
Благодарности Работа выполнена при поддержке Прграммы фундаментальных исследований Президиума РАН №13 «Основы высоких технологий с Использованием особенностей наноструктур в науках о природе» | Acknowledgement This work was supported by the Program for Basic Research of the Presidium of the Russian Academy of Sciences No.13 "Fundamentals of High Technologies Using Nanostructures in Nature Sciences". |
Конфликт интересов Не указан. | Conflict of Interest None declared. |
Список литературы / References
- Guo Z. Multifunctional Nanocomposites for Energy and Environmental Applications / Guo Z., Chen Y., Lu N. L. / Z. Guo. – Wiley-VCH, Weinheim, 2018.
- Kulikova M. V. Fischer-Tropsch synthesis in the presence of cobalt-containing composite materials based on carbon / Kulikova M. V., Zemtsov L. M., Sagitov S. A. and others // Solid. Fuel. Chem. – 2014. – V. 48. – P. 105–111. doi:10.3103/s0361521914020074
- Ali F. Bactericidal and catalytic performance of green nanocomposite based on chitosan/carbon black fiber supported monometallic and bimetallic nanoparticles / Ali F., Khan S. B., Kamal T. and others // Chemosphere. – 2017. – V. 188. – P. 588–598.
- Galaburda M. V. Adsorption/desorption of explosives on Ni-, Co-, and NiCo-carbon composites: Application in solid phase extraction / Galaburda M. V., Bogatyrov V. M., Tomaszewski W. and others // Colloids Surfaces A Physicochem Eng Asp. – 2017. – V. 529. – P. 950–958.
- Yu H. Design of Cu-based intermetallic nanocrystals for enhancing hydrogenation selectivity / Yu H., Tang W., Li K. and others // Chem. Eng. Sci. – 2019. – V. 196. – P. 402–413.
- Sharma G. Novel development of nanoparticles to bimetallic nanoparticles and their composites: A review / Sharma G., Kumar A., Sharma S. and others // J. King Saud Univ - Sci. – 2017. V. 31. – P. 257–269.
- Chen M. Preparation of Au–Ag bimetallic nanoparticles for enhanced solar photothermal conversion / Chen M., He Y., Zhu J. and others // Int. J. Heat Mass. Transf. –2017. – V. 114. – P. 1098–1104.
- Laursen A. B. Availability of elements for heterogeneous catalysis: Predicting the industrial viability of novel catalysts / Laursen A. B., Sehested J., Chorkendorff I. and others // Chinese J. Catal. – 2018. – V. 39. – P. 16–26.
- Alvi M. A. An effective and low cost PdCe bimetallic decorated carbon nanofibers as electro-catalyst for direct methanol fuel cells applications / Alvi M. A., Akhtar M. S. // J. Alloys Compd. – 2016. – V. 684. – P. 524–529.
- Saha S. Graphene supported bimetallic G–Co–Pt nanohybrid catalyst for enhanced and cost effective hydrogen generation / Saha S., Basak V., Dasgupta A. and others // Int. J. Hydrogen Energy. – 2014. –V. 39. – P. 11566–11577.
- Luo M. Effect of Palladium on Iron Fischer–Tropsch Synthesis Catalysts / Luo M., O’Brien R., Davis B.H. // Catal. Letters. – 2004. V. 98. – P. 17–22.
- Minnermann M. Role of Palladium in Iron Based Fischer−Tropsch Catalysts Prepared by Flame Spray Pyrolysis / Minnermann M., Pokhrel S., Thiel K. and others // J. Phys. Chem. C. – 2011. –V. 115. – P. 1302–1310.
- Goula M. A. Hydrogen production by ethanol steam reforming over a commercial Pd/γ-Al2O3 catalyst / Goula M. A., Kontou S. K., Tsiakaras P. E. // Appl. Catal. B Environ. – 2004. V. 49. – P. 135–144.
- Abrokwah R. Y. Comparative performance of M-MCM-41 (M: Cu, Co, Ni, Pd, Zn and Sn) catalysts for steam reforming of methanol / Abrokwah R. Y., Deshmane V. G., Kuila D. // J. Mol. Catal. A Chem. – 2016. V. 425. – P. 10–20.
- Lo Vecchio C. Carbon-supported Pd and Pd-Co cathode catalysts for direct methanol fuel cells (DMFCs) operating with high methanol concentration / Lo Vecchio C., Sebastián D., Alegre C. // J. Electroanal. Chem. – 2018. – V. 808. – P. 464–473.
- Campesi R. Hydrogen storage properties of Pd nanoparticle/carbon template composites / Campesi R., Cuevas F., Gadiou R. andothers // Carbon N. Y. – 2008. – V. 46. – P. 206–214.
- Efimov M. N. Structural variation in palladium nanoparticles of the C-Pd system when dissolving hydrogen in them / Efimov M. N., Nekrasova A. A., Dzidziguri E. L. and others // Crystallogr. Reports. – 2012. V. 57. – P. 569–573.
- Chokprasombat K. Morphological alteration and exceptional magnetic properties of air-stable FeCo nanocubes prepared by a chemical reduction method / Chokprasombat K., Harding P., Pinitsoontorn S. and others // J. Magn. Magn. Mater. – 2014. – V. 369. – P. 228–233.
- Yasuda H. Y. Microstructure control for developing Fe-Pd ferromagnetic shape memory alloys / Yasuda H. Y., Komoto N., Ueda M. and others // Sci. Technol. Adv. Mater. – 2002. – V. 3. P. 165–169.
- Zemtsov L. M. Carbon nanostructures based on IR-pyrolyzed polyacrylonitrile / Zemtsov L. M., Karpacheva G. P., Efimov M. N. and others // Polym. Sci. - Ser. A. – 2006. – V. 48. – P. 633–637.
- Vasilev A. A. Metal-carbon nanosystem IR-PVA/Fe-Co for catalysis in the Fischer-Tropsch synthesis / Vasilev A. A., Dzidziguri E. L., Ivantsov M. I. and others // J. Phys. – 2016. – V. 741. – 12186.
- Fan T. E. Structure and stability of Fe-Pt bimetallic nanoparticles: Initial structure, composition and shape effects / Fan T. E., Liu T. D., Zheng J. W. and others // J. Alloys Compd. – 2016. – V. 685. – P. 1008–1015.
- Kuznetsov V. L. Mechanism of Coking on Metal Catalyst Surfaces: I. Thermodynamic Analysis of Nucleation / Kuznetsov V. L., Usol’tseva A. N., Butenko Y. V. // Kinet. Catal. – 2003. – V. 44. – P. 726–734.
- Esconjauregui S. The reasons why metals catalyze the nucleation and growth of carbon nanotubes and other carbon nanomorphologies / Esconjauregui S., Whelan C. M., Maex K. // Carbon N. Y. – 2009. – V. 47. – P. 659–669.
- Hansen M. Constitution of Binary Alloys / M. Hansen. – McGraw-Hill, New York, 1958.
- Kubaschewski von Goldbeck O. Iron—Binary Phase Diagrams / O. Kubaschewski von Goldbeck O. – Springer-Verlag Berlin Heidelberg, 1982.
- Johansson M. Hydrogen adsorption on palladium and palladium hydride at 1 bar / Johansson M., Skúlason E., Nielsen G. and others // Surf. Sci. – 2010. – V. 604. – P. 718–729.
- Petrunin V. F. Structural characterization of ultra dispersed (nano-) materials as intermediate between amorphous and crystalline states / V.F. Petrunin // Nanostructured Mater. – 1999. – V. 12. – P. 1153–1156.
- Pearson W. B. A Handbook of Lattice Spacings and Structures of Metals & Alloys / W.B. Pearson. – London: Pergamon Press, 1958.