ЦЕМЕНТНО-ЗОЛЬНЫЙ ФИБРОПЕНОБЕТОН ЕСТЕСТВЕННОГО ТВЕРДЕНИЯ
ЦЕМЕНТНО-ЗОЛЬНЫЙ ФИБРОПЕНОБЕТОН ЕСТЕСТВЕННОГО ТВЕРДЕНИЯ
Аннотация
В статье приведены данные по влиянию дисперсного микроармирования на свойства неавтоклавного цементно-зольного пенобетона. Материал готовился на протеиновых пенообразователях отечественного производства. В качестве заполнителя для приготовления пенобетона используется зола-унос от сжигания бурых углей Бородинского разреза Канско-Ачинского угольного бассейна. Установлено, что использование полипропиленовой фибры в цементно-зольном пенобетоне естественного твердения является наиболее целесообразным. Максимальная стойкость пены в растворной смеси получена при введении асбестовой фибры. Использование в составе пенобетона волокнистых добавок позволяет увеличить его трещиностойкость на 34-75%, данный показатель увеличивается при использовании фибры с более высокими показателями прочности при растяжении. Применение базальтовых волокон в пенобетоне Rospena позволяет снизить плотность до D500 и обеспечить коэффициент теплопроводности 0,150 Вт/(м°С).
1. Введение
Утилизация техногенных отходов производств, например, таких как зола-унос, в составе строительных материалов является актуальной экологической и экономической задачей , , , . Одним из перспективных направлений применения зол-уноса является производство с их использованием неавтоклавных пенобетонов. Такие изделия обладают повышенными теплоизоляционными характеристиками, невысокой стоимостью, относительно низкими энергетическими затратами при производстве. Сложность обеспечения требуемых эксплуатационных характеристик неавтоклавного пенобетона заключается в сохранении оптимальной пористой структуры до затвердевания материала. Для повышения его качества используют волокнистые добавки
. Они способствуют повышению агрегативной устойчивости пенобетонной смеси , , повышают пластическую прочность и прочность готовых изделий , а также трещиностойкость . За счет микроармирующего эффекта фибра позволяет снизить усадочные деформации , . В качестве фибры используют стеклянные и базальтовые волокна , , , полипропиленовые , применяют углеродное волокно , , целлюлозный наполнитель, полученный в результате мокрого измельчения макулатуры , и др.Целью данной работы является повышение агрегативной устойчивости и прочностных характеристик неавтоклавного цементно-зольного пенобетона с использованием волокнистых добавок.
2. Методы и принципы исследования
В работе использовались следующие материалы:
– портландцемент класса ЦЕМ I 42,5Н (ООО «Топкинский цемент», Кемерово), химический состав, мас. %: CaO – 63,02; SiO2 – 19,29; Al2O3 – 4,63; Na2O – 0,37, K2O – 0,47; MgO – 1,86; TiO2 – 0,28; Fe2O3 – 3,91; SO3 – 3,98, P2O5 – 0,07, MnO – 0,05, ППП – 2,25, истинная плотность – 3160 кг/м3, насыпная плотность – 1056 кг/м3;
– основная зола-унос от сжигания бурых углей Бородинского разреза Канско-Ачинского угольного бассейна (ТЭЦ-5, Новосибирск), химический состав, мас. %: SiO2 – 49,47; Al2O3 – 7,36; Fe2O3 – 7,51; CaO – 27,53; MgO – 4,52; Na2O – 0,23; K2O – 0,28; SO3 – 1,24; BaO – 0,38, P2O5 – 0,03, TiO2 – 0,44, ППП – 0,52, насыпная плотность – 1342 кг/м3, истинная плотность – 2489 кг/м3, удельная поверхность – 240 м2/кг, влажность – 0,4%.
Удельная активность естественных радионуклидов золы составляет 113 Бк/кг, такой материал может использоваться для строительства жилых и общественных зданий .
По данным рентгенофазового анализа в составе золы обнаруживаются кварц (3,35, 1,82, 1,54)×10-1 нм, муллит (3,35, 2,11, 2,40, 2,28, 2,12, 1,54) ×10-1 нм, мусковит (3,35, 1,98, 2,40, 2,12, 1,69, 1, 54) ×10-1 нм, ортоклаз (3,35, 1,81, 4,26, 3,5, 2,77, 2,46,2,12, 1,98) ×10-1 нм.
По содержанию оксида кальция зола содержит более 10 %, в соответствии с ГОСТ 25818-2017 «Золы-уноса тепловых электростанций для бетонов. Технические условия» зола является основной. По требованиям стандарта для ячеистых бетонов количество CaOсвоб не нормируется. По классификации Савинкиной М. А. и Логвиненко А. Т. исследуемая зола относится к среднекальциевой с содержанием CaO 20-30%
. Содержание сернистых и сернокислых соединений не превышает 6%, количество щелочных оксидов также удовлетворяет требованиям стандарта (не более 3,5%). Потери при прокаливании составляют 0,52%, что не превышает нормируемых показателей (3%) и соответствует значениям золы сухого отбора. Зола-унос соответствует требованиям ГОСТ 25818-2017.Модуль основности для исследуемой золы составляет 0,56, коэффициент качества равен 1,04. Такие золы обладают свойством самостоятельного твердения, могут применяться для производства изделий на их основе. По требованиям межгосударственного стандарта в качестве вяжущего компонента в ячеистых бетонах можно использовать высокоосновную золу с содержанием оксида кальция не менее 40%. Т.к. исследуемая зола данному параметру не соответствует, было решено ее использовать в качестве заполнителя.
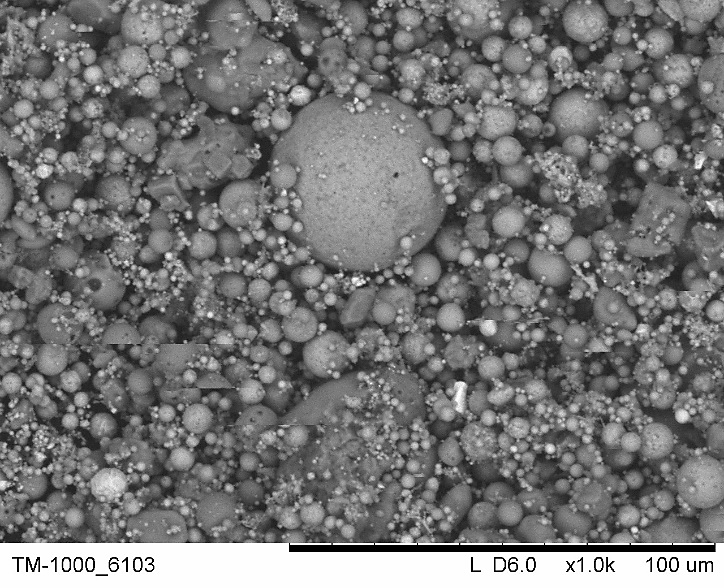
Рисунок 1 - Электронная фотография золы
Примечание: 1000-кратное увеличение
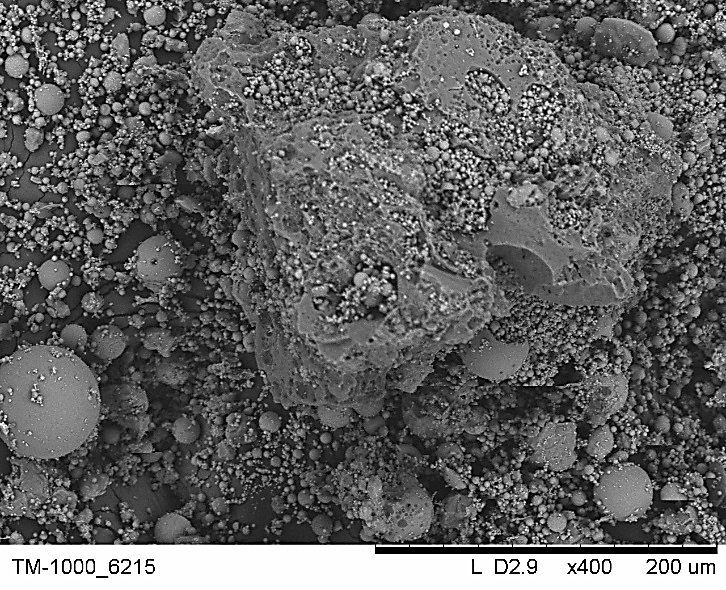
Рисунок 2 - Электронная фотография золы
Примечание: 400-кратное увеличение
Для приготовления пены использовались отечественные пенообразователи, состоящие из протеинов (белков) – биополимеров Rospena (ТУ 24.66.47.142-001-0139620869-2019) и Эталон (ТУ 2483-003-13420175-2015).
В качестве армирующих компонентов применяли минеральную и органическую фибру: базальтовую, полипропиленовую и асбестовую. Использовались базальтовые волокна (CEMMIX), содержащие SiO2, Al2O3. Длина фибры – 12 мм, диаметр – 17 мкм, обладают химической стойкостью. Прочность при растяжении – 3000 МПа. Полипропиленовое волокно (ООО ПК Альянс) с длиной волокон 6 мм, диаметром 40 мкм. Волокна обладают химической стойкостью. Прочность при растяжении – 570 МПа. Асбест хризотиловый Киембаевского месторождения марки А-6К-30 (АО «Оренбургские минералы») с длиной волокон менее 16 мм, диаметром менее 0,5 мкм. Прочность при растяжении – 3200 МПа.
Пенобетон естественного твердения готовился по двухстадийной технологии на турбулентной установке со скоростью вращения рабочего органа 940-1500 об/мин. Твердение образцов происходило в нормальных условиях, на 28-е сутки проводились их испытания.
3. Основные результаты
Для приготовления пенобетона было определено оптимальное количество порообразователя, которое составило 3% для пенообразователя Эталон, для Rospena – 7%. На пенообразователе Эталон возможно получить низкократную пену (16), а на пенообразователе Rospena – среднекратную (25). Добавки вводились в воду для их равномерного распределения в объеме материала, чтобы исключить агрегирование волокон.
В таблице 1 представлены результаты испытаний пенобетона на основе пенообразователя Эталон. Для контрольного образца плотность составляет 603 кг/м3. Базальтовые волокна значительно повышают плотность по сравнению с контрольным составом (на 30%). При введении асбестовых и полипропиленовых волокон плотность меняется незначительно по сравнению с контрольным образцом.
При сравнении ККК можно отметить, что введение асбестовых волокон снижает его на 12%, наблюдается увеличение ККК при введении полипропиленовой (23) и базальтовой фибры (89).
Таблица 1 - Свойства пенобетона Эталон
Показатель | Волокна | |||
Без добавок | Базальтовая | Полипропиленовая | Асбестовая | |
Средняя плотность, кг/м3 | 603 | 822 | 638 | 570 |
Предел прочности при сжатии, МПа | 2,12 | 5,47 | 2,76 | 1,76 |
ККК | 3,52 | 6,65 | 4,33 | 3,09 |
Предел прочности при изгибе, МПа | 1,35 | 5,25 | 2,37 | 1,97 |
Rизг/Rсж | 0,64 | 0,96 | 0,86 | 1,12 |
Механизм действия волокнистых добавок заключается в армировании материала и препятствии распространению трещин в композите. Использование в составе пенобетона фибры позволяет увеличить его трещиностойкость (Rизг/Rсж) на 34-75%. Увеличение трещиностойкости материала при введении волокон может быть связано с их характеристиками. С повышением прочности при растяжении используемой фибры наблюдается рост трещиностойкости полученного пенобетона (табл. 1).
Также волокнистые добавки повышают стойкость пены в растворной смеси на 6-15% (рис. 3). За счет своей протяженной формы волокна более эффективно удерживают воздух в пенобетонной смеси. Наиболее значительное влияние оказывает асбестовая фибра (15%), возможно это связано с наилучшим распределением волокон в объеме материала. Волокна могут закупоривать каналы Плато, что также положительно сказывается на агрегативной устойчивости пенобетонной смеси.
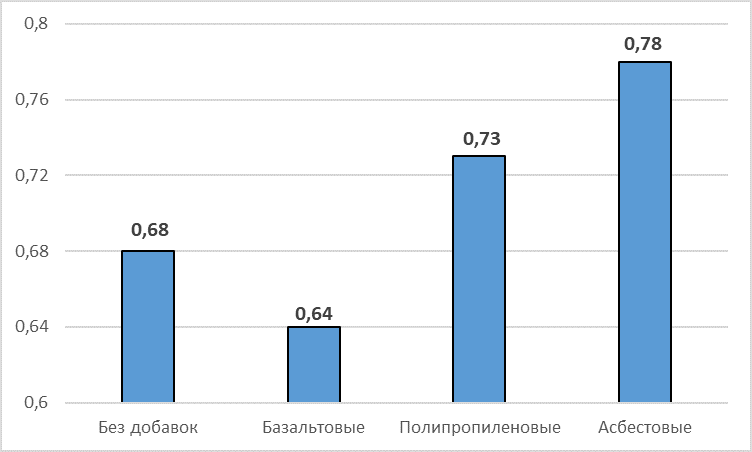
Рисунок 3 - Стойкость пены Эталон в растворной смеси
Таблица 2 - Свойства пенобетона Rospena
Показатели | Волокна | |||
без добавок | базальтовые | полипропиленовые | хризотил-асбестовые | |
Средняя плотность, кг/м3 | 575 | 494 | 589 | 310 |
Предел прочности при сжатии, МПа | 2,3 | 1,57 | 2,76 | 0,46 |
ККК | 3,99 | 3,29 | 4,57 | 1,48 |
Предел прочности при изгибе, МПа | 1,5 | 1,38 | 2,16 | 0,75 |
Rизг/Rсж | 0,65 | 0,88 | 0,78 | 1,63 |
При введении хризотил-асбестовых волокон плотность пенобетона снижается до 310 кг/м3, но при этом падает и прочность (табл. 2), ККК уменьшается практически в 2,5 раза. ККК несколько снижается при использовании базальтовых волокон, трещиностойкость при этом увеличивается на 35%. Коэффициент теплопроводности пенобетона с базальтовой фиброй составляет 0,150 Вт/(м°С) при определении методом теплового зонда , что позволяет использовать данный материал как теплоизоляционный.
Для пенобетона Rospena стойкость пены в растворной смеси увеличивается на 4-8% (рис. 4). За счет своей протяженной формы частицы повышают вязкость смеси, а также позволяют эффективно проводить воздухововлечение в смесь. Наибольшее повышение стойкости пены Rospena также наблюдается для пенобетонной смеси с хризотил-асбестовыми волокнами.
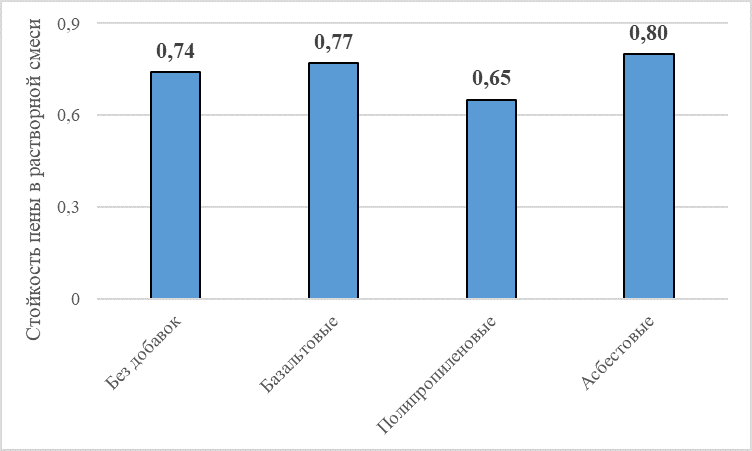
Рисунок 4 - Стойкость пены Rospena в растворной смеси
Предполагается
, , что повышение прочности цементного камня с микроармирующими волокнами может быть обусловлено увеличением степени гидратации цемента.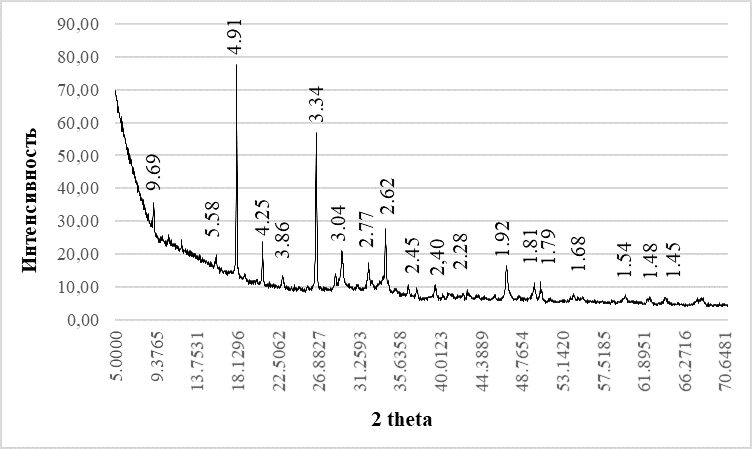
Рисунок 5 - Рентгенограмма пенобетона Rospena
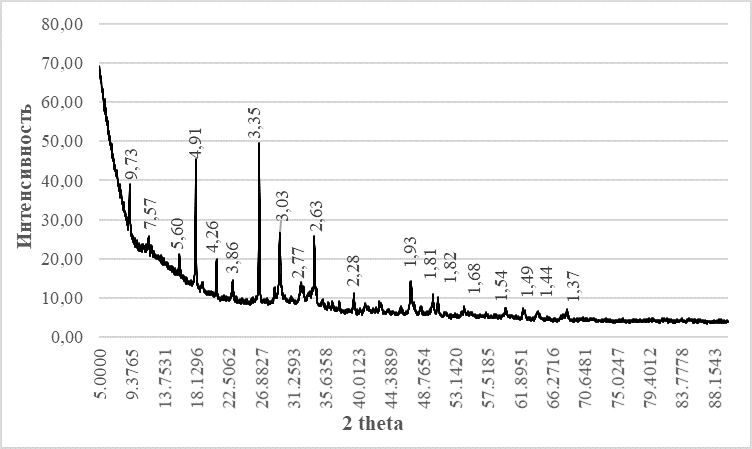
Рисунок 6 - Рентгенограмма пенобетона Эталон
При сравнении рентгенограмм пенобетона с волокнистыми добавками наблюдаются различия в интенсивностях линии, соответствующих Са(OH)2. Наибольшая интенсивность относится к пенобетону Rospena с полипропиленовой фиброй и снижается при введении базальтовой, наименьшая соответствует пенобетону с асбестовыми волокнами. Таким образом, можно предположить, что волокна выполняют роль подложки для новообразований, увеличивают степень гидратации цемента, при этом повышается прочность при сжатии и ККК пенобетона (табл. 2). Для пенобетона Эталон интенсивность линий уменьшается в следующем порядке: при введении базальтовой фибры, полипропиленовой, асбестовой. Что также согласуется с уменьшением прочности и ККК фибропенобетона (табл. 1). Наименьшее влияние на прочность и ККК для обоих пенообразователей оказывает асбестовая фибра.
4. Заключение
По результатам работы можно сделать следующие выводы:
1. Исследуемая зола относится к среднекальциевой, может быть использована в качестве заполнителя для получения неавтоклавного пенобетона.
2. Для пенообразователя Эталон характерна низкократная пена, для Rospena – среднекратная. Стойкость пены Rospena в цементно-зольной смеси выше на 9% по сравнению с пеной Эталон. Более полная гидратация цемента происходит при использовании пенообразователя Rospena, также такой пенобетон имеет более высокий ККК.
3. Использование в составе цементно-зольного пенобетона волокнистых добавок позволяет увеличить его трещиностойкость на 34-75%, данный показатель возрастает при использовании фибры с более высокой прочностью при растяжении.
4. Стойкость пены в растворной смеси увеличивается на 4-17%, за счет дополнительного воздухововлечения снижается средняя плотность материала. Наибольшее воздухововлечение обеспечивает хризотил-асбестовая фибра.
5. Полипропиленовые волокна увеличивают ККК, средняя плотность меняется незначительно, трещиностойкость повышается на 20-34% в зависимости от пенообразователя.
6. Введение базальтовой фибры позволяет снизить среднюю плотность пенобетона Rospena до D500, ККК при этом составляет 3,29, коэффициент теплопроводности 0,150 Вт/(м°С), что позволяет использовать материал как теплоизоляционный.
Средняя плотность пенобетона Эталон значительно возрастает при использовании базальтовых волокон, ККК повышается. Что может быть связано с трудностью равномерного распределения данного вида фибры.
7. Наибольшая прочность и ККК пенобетона с фиброй соответствует образцам с более полной гидратацией цемента. Наименьшие значения определены для пенобетона с асбестовыми волокнами.