Исследование особенностей использования сернистых мазутов на энергетических предприятиях и анализ путей снижения количества выбрасываемых вредных веществ при их сжигании
Исследование особенностей использования сернистых мазутов на энергетических предприятиях и анализ путей снижения количества выбрасываемых вредных веществ при их сжигании
Аннотация
Изучен технологический процесс сжигания сернистого мазута марки М100 в котельном агрегате ДЕ-6,5/14ГМ. Установлено, что основными золообразующими агентами в мазуте являются ванадий и сера. С помощью стендовой установки, установленной в газоходе на выходе дымовых газов из конвективной части котла, определяли интенсивность образования зольных отложений на его поверхностях нагрева. Результаты измерений оценивали на предмет содержания грубой погрешности по критерию Романовского. Проведённые расчёты показали, что полученный ряд измерений с доверительной вероятностью 95% не содержит грубых промахов. Расчетным методом получены графические зависимости, описывающие процент потерь коэффициента теплопередачи. Экспериментально установлено, что с течением времени величина отложений изменяется неравномерно, что связано с величиной нагрузки котельного агрегата. При использовании в качестве топлива сернистого мазута, коэффициент полезного действия котельного агрегата снижается, а потери теплоты с уходящими газами увеличиваются. При этом снижается экономичность работы котла в следствии повышения расхода топлива на выработку пара.
1. Введение
Качество мазутов, выпускаемых отечественной промышленностью, во многом определяется свойствами исходной нефти и схемами её переработки, поэтому их эксплуатационные свойства могут изменяться в широких пределах. Известно, что более 60-70% серы в процессе переработки нефти переходит в мазут, который используется в качестве котельного топлива на энергетических предприятиях , , . При его сжигании образуются продукты сгорания, имеющие в своем составе золу, SO2, NO2, СО, а также полициклические ароматические углеводороды. В настоящее время одной из основных проблем при проектировании ТЭС стало обеспечение предельно допустимых концентраций газообразных примесей в атмосферном воздухе, установленных санитарными органами . После введения в силу ГОСТ 17.2.3.02-2014 (Правила установления допустимых выбросов загрязняющих веществ промышленными предприятиями) ужесточились нормативы предельно допустимого выброса вредных веществ в атмосферный воздух для энергетических предприятий. На значимость этой проблемы косвенно указывает то, что за последние несколько лет значительно вырос объем научных трудов, изучающих тематику снижения образования NO2 и SO2 в дымовых газах. Исследования в этой области ведутся также в США, Японии, Германии и ряде других стран .
Высокое содержание сернистых соединений в жидком котельном топливе вызывает интенсивное образование зольных отложений, сопровождающееся коррозионным износом поверхностей нагрева котельных агрегатов. Кроме этого, при сжигании такого топлива в окружающую среду выбрасывается большое количество диоксида серы и других компонентов, имеющих высокую степень токсичности. Аэрозольные твердые частицы такие, как сажа, пятиокись ванадия, бензо(а)пирен со временем накапливаются на поверхности земли, а также участвуют в приземной циркуляции атмосферы. Токсическая доза ванадия для человека составляет 0,25 мг, а летальная в зависимости от веса – 2-4 мг. По данным авторов , годовое поступление ванадия в атмосферу из антропогенных источников составляет 142 тыс. тонн в т.ч. 52 тыс. тонн за счет энергетических предприятий. Поэтому изучение особенностей использования сернистых мазутов на энергетических предприятиях и анализ путей снижения количества выбрасываемых вредных веществ послужило темой настоящего исследования , , .
2. Методы и принципы исследования
Местом проведения исследования является промышленно-отопительная котельная, расположенная в жилом массиве Советского района г. Казани, назначением которой является осуществление выработки насыщенного пара и приготовление воды на нужды отопления и горячего водоснабжения. В котельной установлены три паровых котла марки ДЕ-6,5/14ГМ Бийского котельного завода. Для рассеивания дымовых газов на предприятии используется стальная дымовая труба высотой 30 м. Котельные агрегаты снабжены горелочными устройствами ГМ-4,5 с номинальной тепловой мощностью 5,2 МВт и расходом жидкого топлива 465 кг/ч. Сернистый мазут марки М100 с содержанием общей серы 4,3% используется на предприятии в качестве резервного топлива. Физико-химические свойства мазута приведены в таблице 1.
Таблица 1 - Физико-химические характеристики мазута М100
№ п/п | Показатели | Численные значения | Метод испытания |
1 | Условная вязкость, °ВУ при 80℃ | 25,3 | ГОСТ 6258 |
2 | Температура вспышки не ниже, ℃ | 125,0 | ГОСТ 4333 |
3 | Температура застывания не выше, ℃ | 25,5 | ГОСТ 20287 |
4 | Плотность при 80℃, кг/м3 | 978,0 | ГОСТ 3900 |
5 | Содержание серы, % | 4,3 | ГОСТ 3877 |
Элементный состав мазута определялся с помощью элементного анализатора CHNS/O Perkin Elmer модели 2400 Series II. Результаты анализа приведены в таблице 2. Теплоту сгорания мазута определяли по ГОСТ 21261-91.
Таблица 2 - Элементный состав мазута
Марка мазута | Ср, % | Нр, % | Ор, % | Nр, % | Sр, % | Ар, % | Wр, % | Qнр, МДж/кг |
М100 | 82,7 | 10,1 | 0,15 | 1,04 | 4,3 | 0,62 | 1,09 | 38,80 |
Как видно из таблицы 2, рабочий состав мазута практически не отличается от состава исходной нефти. Характерной особенностью высокосернистого мазута является низкое содержание углерода и водорода в рабочей массе по сравнению с малосернистыми аналогами. Уменьшение соотношения углерода к водороду способствует увеличению плотности мазута и снижению его теплоты сгорания. Содержание серы и азота в рабочей массе напротив значительно выше чем в сырой нефти, что объясняется высокой концентрацией первых в следствии углубленной переработки последней .
Как известно, при сжигании мазута большая часть отложений оседает на поверхностях нагрева котельного агрегата. Содержащиеся в сернистых мазутах золообразующие ингредиенты такие, как сера и ванадий, дают плотные отложения, которые с трудом удаляются из-за адгезионного сцепления с трубами котельного агрегата. Основным элементом, определяющим загрязнения поверхностей нагрева липкими отложениями, является пятиокись ванадия, который из-за низкой температуры плавления находится на них в размягчённом состоянии. А также при сжигании сернистых мазутов появлению липких отложений способствует образование сульфатов щелочных металлов . Следствием чего является непрерывный рост тяжёлых форм зольных отложений на конвективных поверхностях нагрева котлов, требующих незапланированных остановок для очистки их поверхностей нагрева.
Объектом исследования послужил паровой котёл ДЕ-6,5/14ГМ ст.№3 заводской №4956. Котельный агрегат полностью исправен. Режимно-наладочные испытания проводились 21.07.2021 г. Результаты испытаний приведены в таблице 3. Топочная камера котла отделена от конвективного пучка газоплотной перегородкой из плотно поставленных и сваренных между собой труб. Перегородка имеет проход для дымовых газов в пучок, образованный коридорно-расположенными вертикальными трубами, развальцованными в верхнем и нижнем барабанах котла. Газы проходят по всему сечению конвективного пучка и выходят через переднюю стенку в короб, расположенный над топочной камерой, из которого они попадают в экономайзер котла. Исследования проводили с помощью стендовой установки, сваренной и установленной в газоходе на выходе дымовых газов из конвективной части котла. Установка представляет собой станину, на которой закреплены куски пластин и труб диаметром 51х2,5 мм. Суммарное время проведения эксперимента составило 48 суток. За это время котельный агрегат ДЕ-6,5/14ГМ ст. №3, израсходовал 204 тонн мазута. Перерыв в работе составил 18 суток. В промежутках между этапами эксперимента при помощи цифрового микрометра Infors 06-11-45 осуществлялся замер отложений на пластинах и трубах установки по методике, приведенной литературе .
Таблица 3 - Параметры работы парового котла ДЕ-6,5/14ГМ ст. №3, установленные в результате режимно-наладочных испытаний
Параметр | Нагрузка | |||
25 % | 50 % | 75 % | 100 % | |
Паропроизводительность, т/ч | 1,72 | 3,64 | 4,87 | 6,13 |
Расход топлива (мазут Qнр=38,80 МДж/кг), кг/ч | 153 | 268 | 376 | 463 |
Расход дымовых газов, м3/c | 1,35 | 2,44 | 3,62 | 4,84 |
Температура уходящих газов, за котлом, °С | 227 | 249 | 302 | 325 |
КПД котлоагрегата брутто, % | 76,03 | 85,71 | 87,21 | 87,73 |
3. Основные результаты
Результаты измерений оценивали на предмет содержания грубой погрешности по критерию Романовского. Проведённые расчёты показали, что полученный ряд измерений с доверительной вероятностью 95%, не содержит грубых промахов. Осреднённые значения по всем измерениям показаны в таблице 4.
Таблица 4 - Величина отложений на этапах эксперимента
№ п/п | Этап эксперимента | Расход топлива, т | Среднее значение замера отложений, мм | |
на пластинах | на трубах | |||
1 | 1 (01.09.2022-10.09.2022) | 58,5 | 0,04 | 0,03 |
2 | 1 (17.09.2022-26.09.2022) | 66,2 | 0,09 | 0,11 |
3 | 1 (03.10.2022-12.10.2022) | 79,3 | 0,16 | 0,23 |
Из данных таблицы 4 видно, что с увеличением времени проведения эксперимента величина отложений изменяется неравномерно, что вероятно связано с величиной нагрузки котельного агрегата, которая также отслеживалась по расходу топлива.
Как известно, загрязнения конвективных поверхностей нагрева золой и твёрдыми отложениями снижают эффективность теплопередачи. Поэтому дальнейшее исследования проводились с целью выяснить это значение. Результаты расчётов зависимости коэффициента теплопередачи от толщины отложений приведены в таблице 5.
Таблица 5 - Результаты расчёта коэффициента теплопередачи в зависимости от толщины золовых отложений
№ п/п | Поверхность нагрева | Значение коэффициента теплопередачи от толщины отложений, Вт/(м2 ·℃) | |||
нет | 0,04 мм | 0,09 мм | 0,16 мм | ||
1 | Экранные трубы | 209,7 | 198,6 | 186,2 | 171,4 |
2 | Конвективный пучок | 145,0 | 139,6 | 133,4 | 125,6 |
3 | Экономайзер | 96,9 | 94,5 | 91,6 | 87,9 |
Как видно из данных, представленных в таблице 5, при величине слоя отложений на поверхностях нагрева котла толщиной 0,04 мм, 0,09 мм и 0,16 мм коэффициент теплопередачи для экранных труб снижается соответственно на 2,5%, 5,5% и 9,4% соответственно. Для труб конвективного пучка эти значения составят 3,7%, 8,0% и 13,4%, а для труб экономайзера 5,3%, 11,2% и 18,3%.
Таким образом, становится отчётливо ясно, что при более низких температурах теплоносителя процент потерь в следствии недогрева значительно возрастает. Данная зависимость проиллюстрирована на рисунке 1.
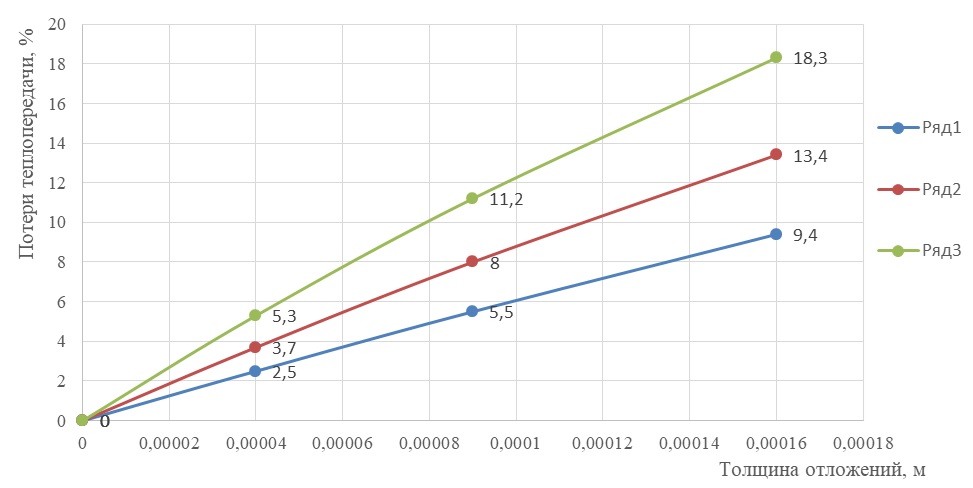
Рисунок 1 - Влияние толщины отложений золы на величину тепловых потерь
Таблица 6 - Изменение температуры уходящих газов на этапах эксперимента
№ п/п | Дата регистрации показаний | Температура уходящих газов, ℃ | Потери теплоты с уходящими газами, % | |
до экономайзера | после экономайзера | |||
1 | 01.09.2022 | 325 | 175 | н.д. |
2 | 10.09.2022 | 329 | 181 | 4,5 |
3 | 26.09.2022 | 334 | 188 | 5,2 |
4 | 12.10.2022 | 341 | 197 | 6,7 |
Из данных таблицы 6 видно, что повышение температуры уходящих газов на первом этапе с 325℃ до 328℃ и 175℃ до 181℃ способствует увеличению потерь теплоты в газовом тракте до 4,5%. С увеличением толщины слоя отложений потери возрастают до 5,2% на втором, и 6,7 % на третьем этапе соответственно. Эти потери в значительной мере способствуют снижению коэффициента полезного действия котельного агрегата, так как из-за отложений, прежде всего, возрастает термическое сопротивление стенок труб экономайзера, тем самым снижая температуру питательной воды на входе в котёл на 1,5-4,0 ℃ в зависимости от заданного режима горения. Результаты повторных режимно-наладочных испытаний котлоагрегата ст.№3, проведенных в конце третьего этапа эксперимента показаны в таблице 7.
Таблица 7 - Параметры работы парового котла ДЕ-6,5/14ГМ ст. №3, установленные в результате режимно-наладочных испытаний на заключительном этапе эксперимента
Параметр | Нагрузка | |||
25 % | 50 % | 75 % | 100 % | |
Паропроизводительность, т/ч | 1,65 | 3,52 | 4,82 | 6,05 |
Расход топлива (мазут Qнр=38,80 МДж/кг), кг/ч | 156 | 271 | 383 | 469 |
Расход дымовых газов, м3/c | 1,38 | 2,58 | 3,78 | 4,96 |
Температура уходящих газов, за котлом, °С | 248 | 268 | 319 | 341 |
КПД котлоагрегата брутто, % | 74,05 | 83,91 | 85,54 | 86,17 |
4. Обсуждение
Из результатов проделанной работы видно, что на режимах при 25%-й и 50%-й нагрузке температура уходящих газов возрастает по сравнению с первоначальными данными (таблица 3) с 227 °С до 248 °С и с 249 °С до 268 °С соответственно. При дальнейшем увеличении нагрузки до 75% на заключительном этапе эксперимента разница температур уходящих газов составила 17 °С, вследствие чего коэффициент полезного действия котла снизился на 1,67%. При 100%-й нагрузке значение этого показателя составило 1,56%.
Экспериментальные исследования, описанные в литературе , связанные с обессериванием топочных мазутов при помощи электродугового метода, позволяют удалить из последних высококонденсированные циклические соединения серы, негативно влияющие на их эксплуатационные свойства. Предлагаемая авторами технология хороша тем, что без существенных затрат может встраиваться непосредственно в систему топливоподготовки любой котельной, использующей мазут в качестве топлива , .
Для предупреждения наружной коррозии и загрязнения поверхностей нагрева энергетических котлов широкое применение нашли также противокоррозионные присадки, в состав которых входят азотистые вещества и пирофорные соединения железа. Присадки взаимодействуют с асфальто-смолистой частью жидкого топлива и образуют новые низкомолекулярные прочные соединения, что стабилизирует мазут, снижает интенсивность процессов конденсации и полимеризации. Кроме того, компоненты многофункциональных присадок стабилизируют процесс горения, и подавляют каталитическую активность золовой части топлива. Эти мероприятия способствуют снижению наружной коррозии и загрязнения поверхностей нагрева. При этом повышается коэффициент использования оборудования и надежность работы котла, увеличивается КПД и срок службы котельного агрегата , , . На сегодняшний день известно, что при переходе котельной с сернистого мазута на малосернистый мазут с содержанием серы до 0,5 %, средняя паропроизводительность котельного агрегата возрастает до 7-9% при одинаковом потреблении топлива. Сжигание малосернистых мазутов позволяет сократить количество внеплановых остановов котлоагрегатов для чистки поверхностей нагрева, улучшает тонкость распыливания форсунками горелочных устройств и повышает степень сгорания мазута, а также способствует снижению выбросов оксидов серы в окружающую среду , , .
5. Заключение
На основе проведенного эксперимента были сделаны следующие выводы:
1. В результате теоретических и экспериментальных исследований установлено, что высокое содержание сернистых соединений в жидком котельном топливе при его сжигании в котельных агрегатах является источником образования диоксида серы, имеющего высокую степень токсичности.
2. Выявлено, что содержащиеся в сернистых мазутах сера и ванадий образуют плотные зольные отложения на поверхностях нагрева котлоагрегатов, увеличивая их термическое сопротивление.
3. Экспериментально установлено, что с течением времени величина отложений изменяется неравномерно, что связано с величиной нагрузки котельного агрегата. За время проведения эксперимента максимальная толщина зольных отложений на трубах котельного агрегата составила 0,23 мм.
4. Установлено, что при использовании в качестве топлива сернистого мазута, коэффициент полезного действия котельного агрегата снижается, а потери теплоты с уходящими газами увеличиваются. При этом снижается экономичность работы котла в следствии повышения расхода топлива на выработку пара.
5. Сравнительный анализ технико-экономических показателей энергетических установок в зависимости от качества топлива показал, что при использовании малосернистого мазута средняя паропроизводительность одного и того же котельного агрегата возрастает до 7-9% при одинаковом расходе топлива.