Методика оценки изменения структурного состояния и механических свойств металлических материалов в технологических процессах ковки
Методика оценки изменения структурного состояния и механических свойств металлических материалов в технологических процессах ковки
Аннотация
Разработана методика оценки изменения структурного состояния и формирования механических свойств металлических материалов в технологических процессах ковки. Методика основана на положениях концепции поэтапного анализа изменения структуры и формирования механических свойств деформированных металлических сплавов c учетом накопленной степени деформации. Структура методики, применительно к технологическим процессам ковки, была дополнена положением о структурно-механических исследованиях материала на переходах деформирования в зависимости от показателей деформированного состояния и межоперационных подогревов. Апробация разработанной методики представлена оценкой изменения структуры и формировании механических свойств аустенитной стали 12Х18Н10Т в процессе ковки ступенчатой заготовки.
1. Введение
Ковка, как один из видов обработки давлением, имеет значительное применение в машиностроении для изготовления изделий из металлических материалов (в дальнейшем по тексту – материалов) в условиях горячей обработки. Одной из основных задач процессов ковки, кроме получения формы и размеров поковок, является получение требуемых механических свойств материала в их объеме.
Структурные изменения деформированных материалов при ковке, и связанные с ними формирование механических свойств, определяются условиями пластического деформирования, к которым относятся величина накопленной степени деформации, величина единичных обжатий, температурный интервал, число и длительность подогревов материала между переходами ковки.
В значительной степени горячей обработки подвергаются нержавеющие и жаропрочные сплавы, используемые при изготовлении ответственных объемных деталей, работающих в условиях высоких температур и коррозионной среды. Изделия изготавливаются многопереходными процессами свободной, как правило, с использованием основных операций осадки и протяжки, и промежуточных подогревов. Процессы пластического деформирования материалов характеризуются большими степенями деформации, а также пространственной неоднородностью деформированного и структурного состояния материала.
В действующей практики кузнечного производства используются положения, основанные на многолетнем технологическом опыте:
– итоговая степень деформации кузнечной обработки задается показателем уковки, который для каждого материала и ответственности, изготавливаемого из него изделия, имеет определенное значение,
– ковка основных групп поковок выполняется отработанными технологическими процессами, имеющими определенную последовательность операций и технологические параметры их выполнения: относительную подачу, степень обжатия и т.д.
В то же время получение однородности механических свойств является одной из основных характеристик кованых изделий. Поэтому решение вопросов, связанных с анализом неравномерности деформированного, и как следствие структурного состояния материала в процессе ковки является весьма актуальным.
В связи с этим целью данной работы являлась разработка методики оценки изменения структурно-механических свойств материалов в процессах ковки.
Для ее достижения были поставлены задача поэтапного анализа изменения структуры и формирования механических свойств деформированных материалов с учетом накопленной степени деформации.
2. Методы и принципы исследования
Начиная с первых работ, выполненных Ф. Киком, Э. Холленбергом, Н. Метцем . в начале прошлого столетия, неравномерность деформации в объеме формоизменяющих заготовок исследовалась многими учеными. Из отечественных ученых в области ковки следует отметить труды Я.М. Охрименко и В.А. Тюрина , И.Я. Тарновского, В.Н. Трубина и М.Г. Златкина и других ученых. В работах представлены разработанные технологические процессы изготовления основных групп поковок, дана оценка неравномерности деформации материала формоизменяющих операций, приведены применяемые технологические показатели их деформированного состояния. В экспериментальных исследованиях, в качестве основного метода, использовалось моделирование, основанное на деформации составных свинцовых образцов, припаиваемых сплавом Вуда, и имеющих в плоскостях разъема координатную сетку , по результатам замеров строились поля деформации. При всей своей показательности и возможности расчета деформированного состояния метод координатных сеток явился недостаточным для определения накопленной деформации при вариантах ковки, имеющих сочетание двух и более разнородных операций. В настоящее время в качестве оценки деформированного состояния используют характеристику В.В. Илюшина, которая определяет степень деформации любой материальной частицы тела, как арифметическую сумму интенсивностей последовательных малых деформаций, в результате которых осуществляется данное ее конечное (значительное) формоизменение . Для условия многоэтапного пластического деформирования расчет степени деформации был уточнен Г.А. Смирновым-Аляевым , согласно которому степень деформации за весь технологический процесс определяется как арифметическая сумма интенсивностей деформации отдельных операций.
В отношении исследования неоднородности структурного состояния материала и их влияния на формирование механических свойств в технологических процессах ковки следует отметить их немногочисленность и ограниченность. Практически все структурные исследования горячедеформированных материалов проводилось с использованием стандартизованных испытаний на растяжение, сжатие и кручение. При этом следует отметить, что структурные изменения горячедеформированных металлических материалов на микроструктурном уровне связаны с процессом рекристаллизации . Основными зависимостями, оценивающих процесс рекристаллизации горячедеформированных материалов, являются трехмерные диаграммы рекристаллизации, построенные в координатах «средняя величина (площадь) зерна – фактическая степень деформации – температура» . Однако данные диаграмм рекристаллизации не позволяет в полной мере дать оценку процесса рекристаллизации в много переходном процессе горячего деформирования с большими степенями деформации, в частности процессах ковки, по двум причинам. Во-первых, в диаграммах в качестве показателя фактической степени деформации используется относительная степень осаженного образца по высоте, которая не характеризует степень деформации материала в условиях сложного нагружения. Во-вторых, показатель относительной степени деформации в диаграммах имеет малые значения и не превышает 80%.
Для процессов свободной ковки, по причине отсутствия зависимостей рекристаллизации материала для условий больших степеней деформации, много переходности процесса и наличия подогревов материала между переходами, актуальной задачей является разработка методики их оценки, что и стало целью работы.
В силу выявленной несостоятельности исследований горячедеформированных материалов в условиях многопереходного деформирования с использованием стандартизованных монотонных испытаний, в данной работе предложена методика, основанная на положениях концепции поэтапного анализа изменения структуры и формирования механических свойств деформированных металлических сплавов с учетом накопленной степени деформации .
Структура методики, применительно к оценке структурно-механических свойств металлических материалов в технологических процессах ковки, включила этапы:
– деформирование материалов в технологических испытаниях, моделирующих процесс ковки конкретной группы поковок, и определение степени деформации на переходах и последовательно накопленной после каждого перехода;
– исследование поэтапного изменения структурного состояния и формирования механических свойств материала на переходах деформирования в зависимости от показателей деформированного состояния и межоперационных подогревов.
Апробация разработанной методики была проведена на примере исследования деформированной стали аустенитного класса 12Х18Н10Т в технологическом испытании, моделирующем процесс ковки ступенчатой поковки. Исследование поэтапного изменения структурного состояния и формирования механических свойств проводилось на переходах деформирования, разработанных в соответствии с технологическими рекомендациями процесса ковки ступенчатых поковок .
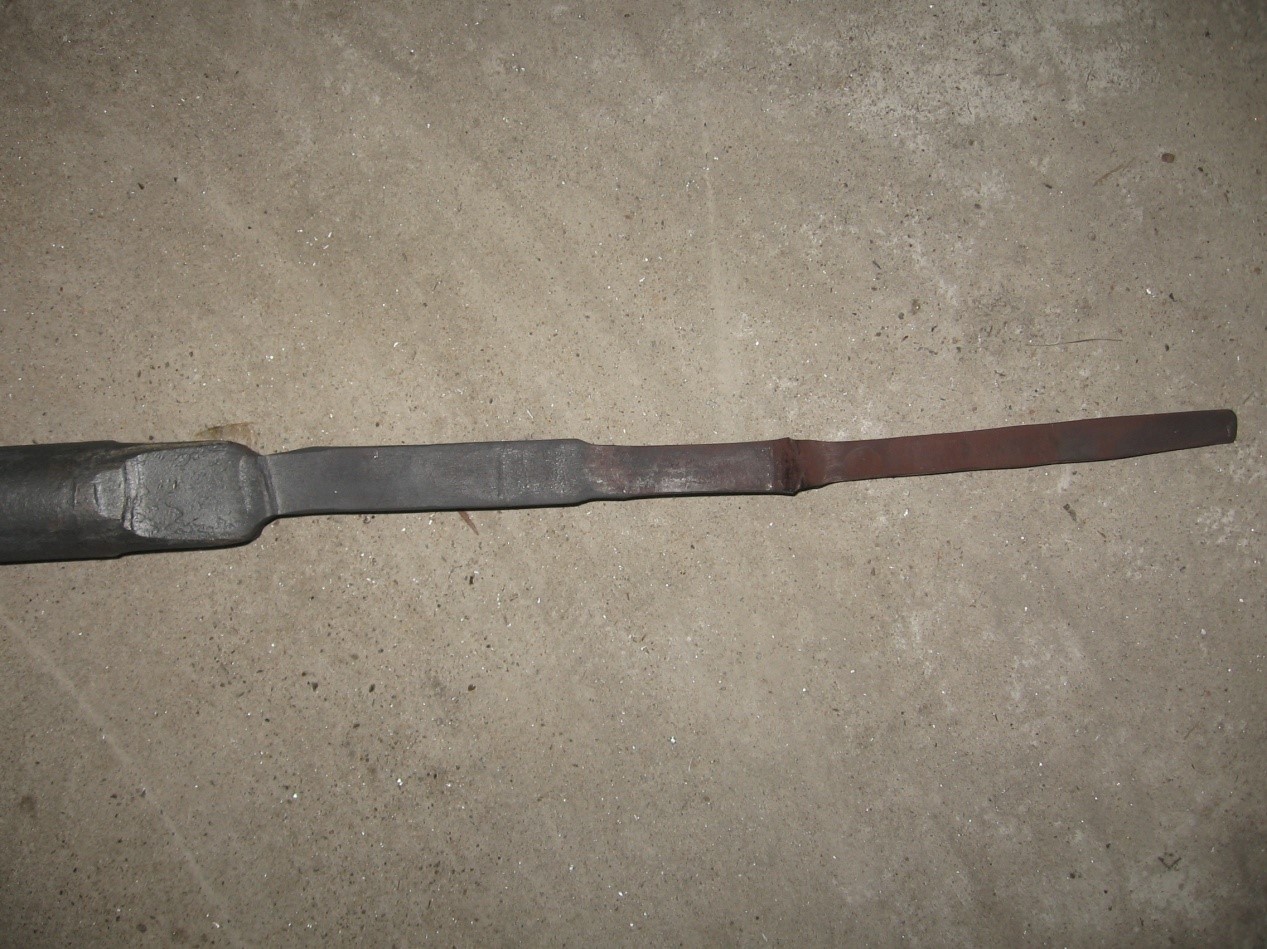
Рисунок 1 - Фотография четырехступенчатой кованой заготовки
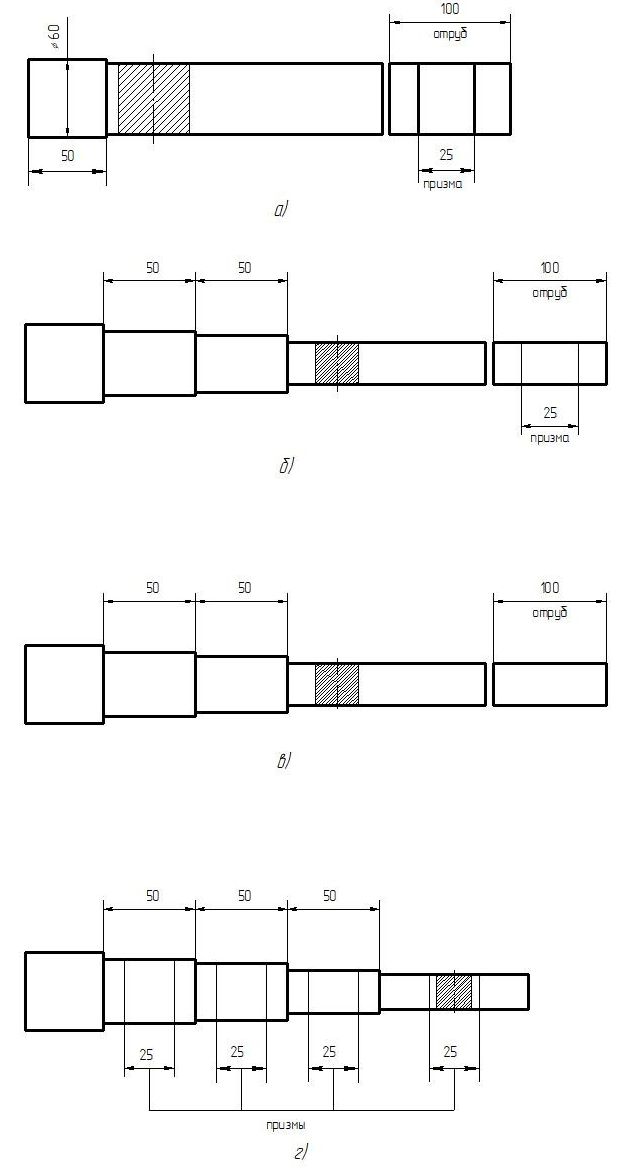
Рисунок 2 - Переходы деформирования ступенчатой заготовки
Примечание: а – 1-й переход (сечение 43×50 мм, = 1,31); б – 2-й переход (36×36 мм, = 1,66, у2общ = 2,08); в – 3-й переход (32×34 мм, = 1,19, у3общ = 2,59); г – 4-й переход (22×24 мм, = 1,12, у4общ = 5,3)
Методика работы включила деформационный анализ и структурно-механические исследования материала каждой ступени заготовки.
Деформированное состояние материала в объеме ступеней заготовки в показателе интенсивности деформации определяли методом численного моделирования физических процессов согласно ГОСТ Р 57188-2016 с использованием программного комплекса DEFORM, разработанного на основе метода конечных элементов (см. рис. 3).
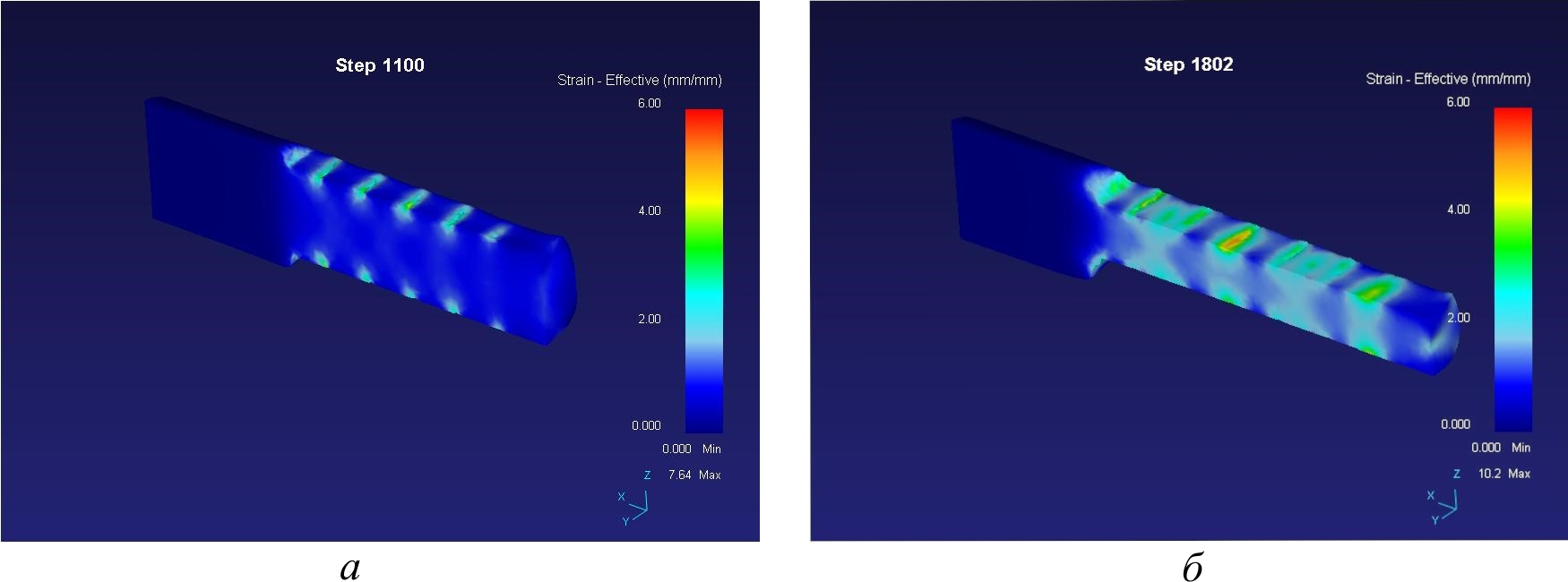
Рисунок 3 - Картины деформированного состояния стали 12Х18Н10Т 1-й ступени заготовки
Примечание: а – после первого прохода и кантовки; б – после второго прохода
Металлографический анализ микроструктур выполняли на микроскопе KEYENCE VHX-1000 на продольных шлифах образцов по направлениям 1, 2 и 3 (см. рис. 4). Для обработки цифровых фотографий микроструктур использовали разработанную для ЭВМ программу .
Твердость измеряли на поперечных шлифах образцов с шагом 2 мм по направлениям 4 и 5 (см. рис. 4).
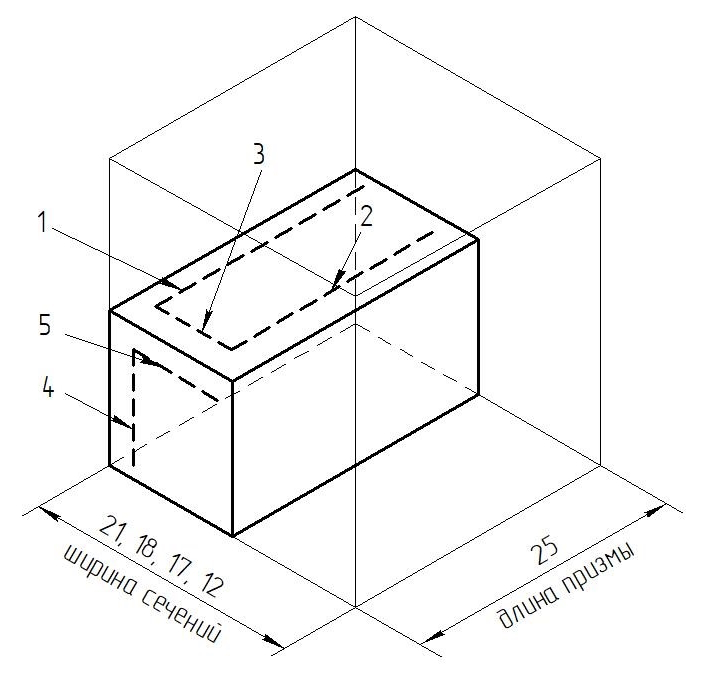
Рисунок 4 - Направления структурно-механических исследований на продольном (1, 2 и 3) и поперечном (4 и 5) шлифах образцов, вырезанных из призм
3. Основные результаты
Результаты деформационного анализа материала первых трех ступеней кованой заготовки, обозначенные на ее поперечных сечениях линиями одинаковой интенсивности деформации (см. рис. 5), свидетельствуют об изменении неравномерности деформации материала ступеней заготовки в зависимости от накопленной степени деформации.
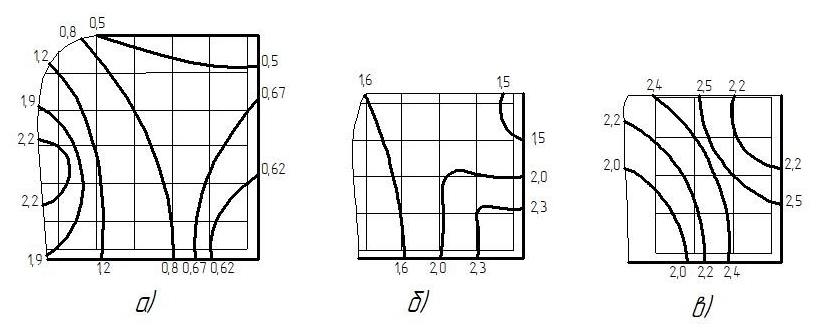
Рисунок 5 - Линии одинаковой интенсивности деформации (цифры) в поперечных сечениях первой (а), второй (б) и третьей (в) ступеней заготовки
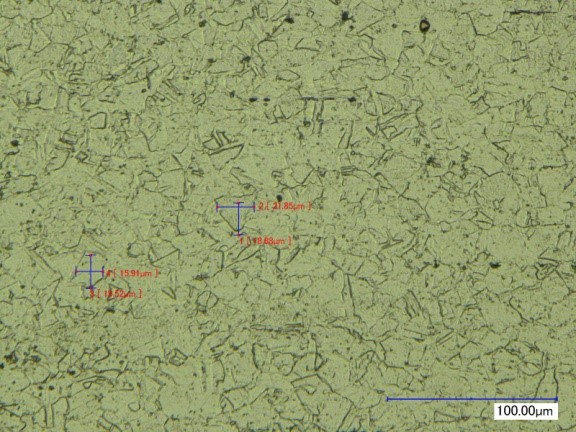
Рисунок 6 - Микроструктура аустенитной стали 12Х18Н10Т в исходной поставке горячекатаного проката
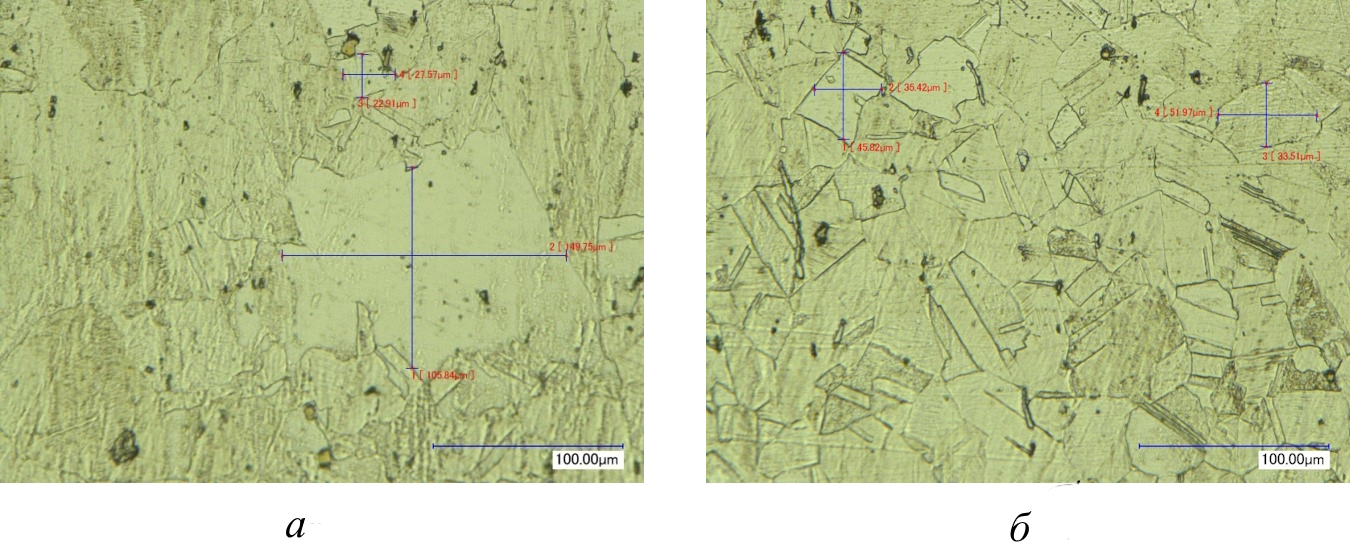
Рисунок 7 - Микроструктуры стали 12Х18Н10Т первой ступени после деформирования
Примечание: а – периферийная зона; б – центральная зона
В микроструктуре материала второй ступени заготовки после деформирования в периферийной зоне (см. рис. 8 а) наблюдается увеличение числа больших зерен. В центральной зоне (см. рис. 8 б) микроструктура, по сравнению с первой ступеней, характеризуется дроблением зерна.
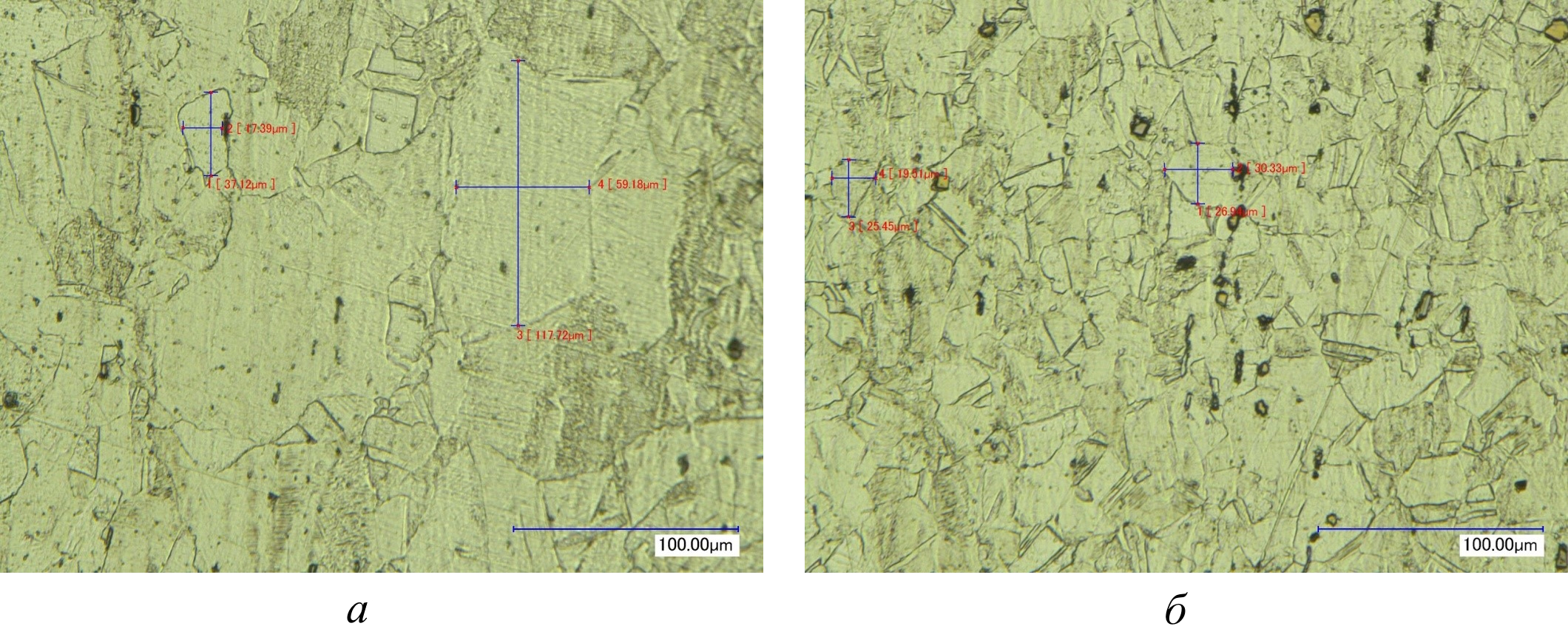
Рисунок 8 - Микроструктуры стали 12Х18Н10Т второй ступени после деформирования
Примечание: а – периферийная зона; б – центральная зона
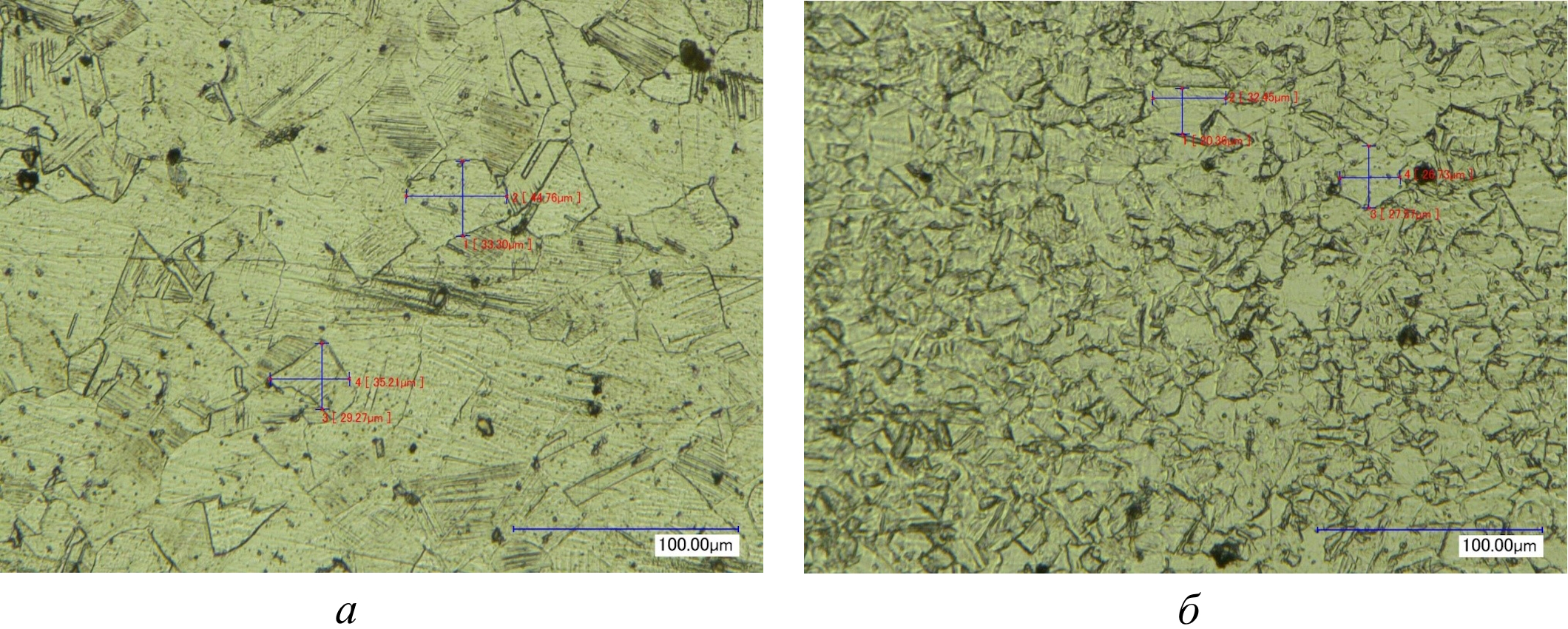
Рисунок 9 - Микроструктуры стали 12Х18Н10Т третьей ступени после деформирования
Примечание: а – периферийная зона; б – центральная зона

Рисунок 10 - Микроструктура стали 12Х18Н10Т четвертой ступени
после деформирования
4. Обсуждение
Полученные результаты позволили сделать следующий вывод о влиянии накопленной степени деформации на структурные изменения в материале при горячей дробной деформации. Для достижения равномерной мелкозернистой структуры по сечению ступенчатой заготовки ее ковку следует проводить с выполнением определенного технологического показателя: суммарный уков при изготовлении ступенчатой заготовки с применением операции протяжка из аустенитной стали 12Х18Н10Т должен иметь значение не менее 5,3.
Структурные изменения материала ступеней кованой заготовки кроме накопленной степени деформации определяются числом и длительностью подогревов. Наибольшие изменения произошли в материале периферийной зоны первой и второй ступени заготовки.
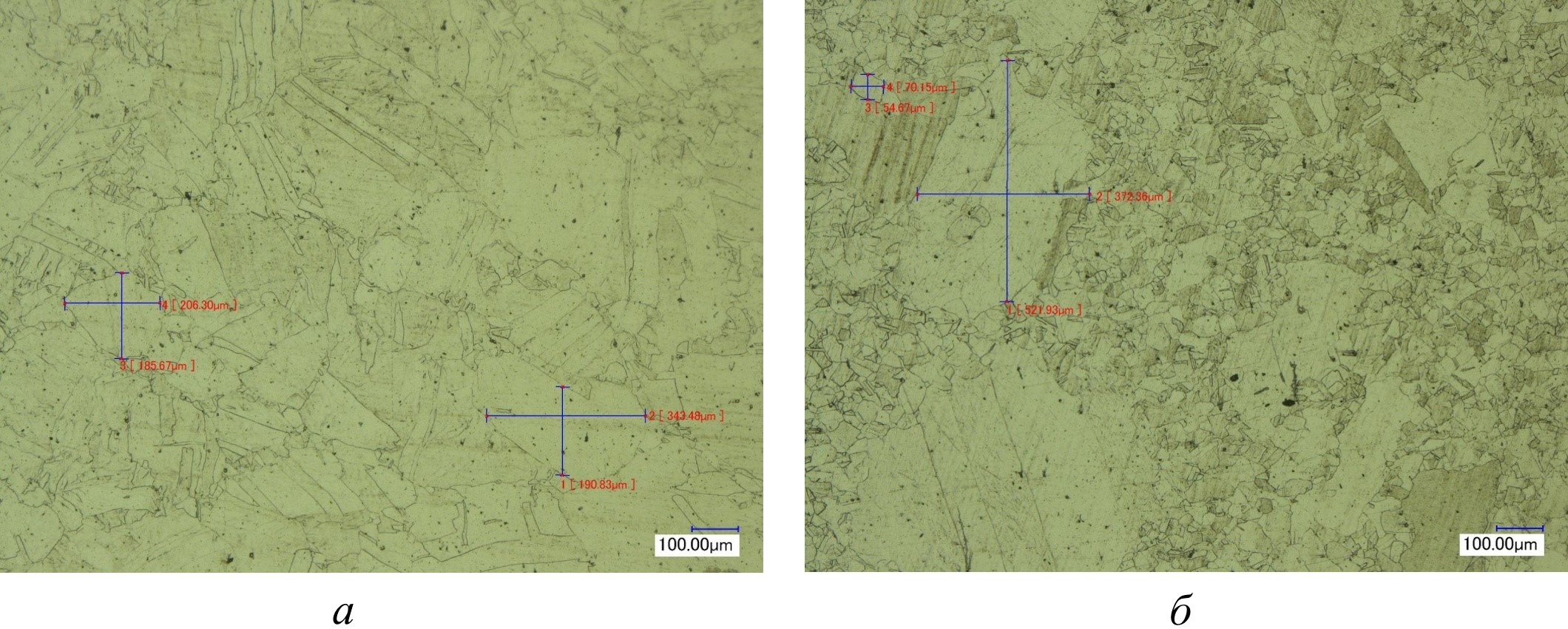
Рисунок 11 - Микроструктуры стали 12Х18Н10Т периферийной зоны заготовки
Примечание: а – первой ступени; б – второй ступени
В микроструктуре материала третьей ступени заготовки после одного подогрева (см. рис. 12) значительного роста зерна не наблюдалось.
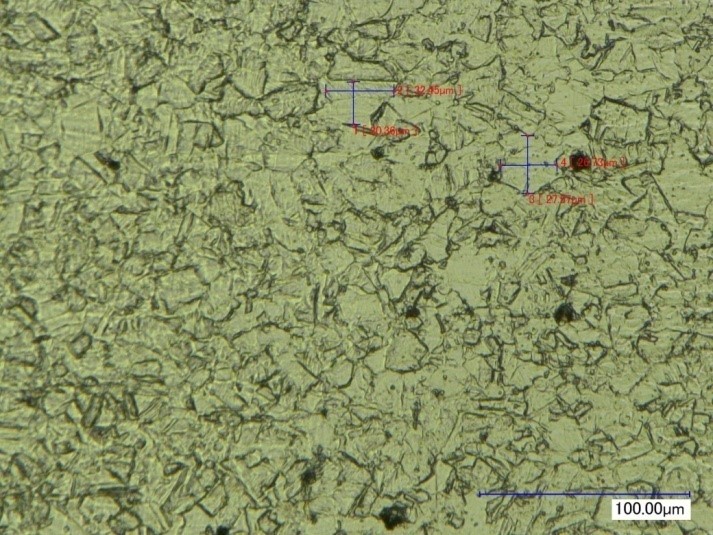
Рисунок 12 - Микроструктуры стали 12Х18Н10Т третьей ступени после одного подогрева
При деформировании четвертой ступени заготовки по всему сечению сформировалась микроструктура (см. рис.10) с равноосными однородными зернами ≈ 20 мкм, средняя площадь которых a ≈ 375 мкм2, что соответствует размеру исходного недеформированного зерна горячекатаного проката.
Полученные результаты свидетельствуют о влиянии последующих нагревов на ступени кованой заготовки в зависимости от накопленной степени деформации, при этом получение равномерной мелкозернистой структуры по сечению ступенчатой заготовки достигается при выполнении технологического показателя-суммарного укова величиной не менее 5,3.
Оценка упрочнение материала проводилась измерениям его твердости на ступенях заготовки. Твердость первых двух ступеней заготовки в периферийной зоне уменьшалась с 61 до 49 HRА, по центру – с 63 до 48 HRА. На третьей ступени, обжатой до укова у3общ = 2,59, твердость материала повысилась и по всему сечению достигла значения 54 HRА, а на четвертой, при укове у4общ = 5,3 достигла твердости 61÷63 HRА недеформированного материала. Полученные результаты показали незначительное влияние размера зерна на повышение прочности, подтверждающее положение, что основной вклад в деформационное упрочнение вносит повышение плотности дислокаций, а не уменьшение размера зерна при пластической деформации.
5. Заключение
Полученные впервые экспериментальные данные влияния накопленной степени деформации на структурные изменения в материале при горячей дробной деформации стали аустенитного класса 12Х18Н10Т, подтвердили состоятельность разработанной методики оценки изменения структурного состояния и формирования механических свойств металлических материалов в технологических процессах ковки.
Разработанная методика основана на положениях концепции поэтапного анализа изменения структуры и формирования механических свойств деформированных металлических сплавов c учетом накопленной степени деформации, как основного влияющего фактора.
Структура методики, применительно к технологическим процессам ковки, дополнена положением о структурно-механических исследований материала на переходах деформирования в зависимости от показателей деформированного состояния и межоперационных подогревов.
Для процессов ковки основных групп поковок разработанная методика позволяет разработать технологические приложения, содержащие данные деформационного анализа и структурно-механических свойств деформируемого материала.