КАСКАДНЫЙ МЕТОД В ТЕХНИЧЕСКОЙ ПОДГОТОВЕ ПРОИЗВОДСТВА
КАСКАДНЫЙ МЕТОД В ТЕХНИЧЕСКОЙ ПОДГОТОВЕ ПРОИЗВОДСТВА
Научная статья
Шайхулова А.Ф.1, *, Гаврилова О.А.2
1 ORCID: 0000-0002-3340-3880;
2 ORCID: 0000-0002-9667-7977;
1, 2 Уфимский государственный авиационный технический университет, Уфа, Россия
* Корреспондирующий автор (shaihulova[at]inbox.ru)
АннотацияСтатья посвящена каскадному методу технической подготовки производства как перспективному методу управления технической системой в долгосрочный период. Этот метод широко применяется в разных отраслях, но для проблематики организации и управления производством впервые. В статье освещается сущность метода, фундаментальные закономерности, которые лежат в его основе, его актуальность в условиях четвертой промышленной революции, а также практическое применение и результаты апробации метода в реальном производстве. Статья также освещает возможности применения новых ранее неисследованных зависимостей для управления производством по координатам время-затраты. В публикации также освещается проблематика применения трехмерного имитационного моделирования для задачи верификации проектных решений.
Ключевые слова: техническая подготовка производства, инновационное проектирование, цифровое производство, каскадный метод, сигмоидальные кривые, трехмерное моделирование.
CASCADE METHOD IN PRODUCTION MANAGEMENT
Research article
Shaykhulova A.F.1, *, Gavrilova O.A.2
1 ORCID: 0000-0002-3340-3880;
2 ORCID: 0000-0002-9667-7977;
1, 2 Ufa State Aviation Technical University, Ufa, Russia
* Corresponding author (shaihulova[at]inbox.ru)
AbstractThe main theme of the article is a cascade method in production management. The supposed approach is proposed to be very efficient in long-term technical system management. This method is widely known in many different fields though for production technical preparation was used for the first time. This article highlights its essence, fundamental regularities that lay beyond it, its relevance, and results of approbation in real production. A new regularity that has never been observed earlier was highlighted as well. These regularities can be used for production management in terms of time-cost and can help to provide smart project management. Application of 3D imitation models for decision making verification in production development was observed as well.
Keywords: production management, innovation development, digital production, cascade method, s-shaped curves, 3D-models.
IntroductionIndustry 4.0 with its artificial intelligence, IoT, digital shadows and digital twins is on the hight top level of popularity today. We may say that it is one of the most popular and thus rapidly growing area of different studies and research. As it changes so quickly many definitions for digital economic and production is still proceeding and still defining [1].
Digital twin – is a flagship for Industry 4.0 [2]. Idea of digital twin was formulated by Grieves M. and Vickers J. in 2003 [3]. But since then, we have made a big progress in information technologies and industry technologies: 3D printing, composite materials etc. Very exhaustive survey in history of digital twins we can see in [4]. As we made a big progress, we got a lot of opportunities for building smart factories – ideal digital production. But the main problem we face here is that digital production requires integrative and system approach for its building. Despite of it we have a lot of research devoted to economic issues or research focused basically on CAD/CAM/CAE or ERP systems but still very few that could combine all these aspects into one approach or method. Current research is a part of a full study that aimed on building such system approach for production digitalization built on fundamental regularities.
Intuition of the Cascade methodThe modern market requires production to be flexible, always ready for changes, new technologies, and new methods. Production values can change very rapidly, technological life circle becomes shorter and shorter – all these things force us to develop new methods and new approaches especially for production management. Cascade method is one of such newbies that well-known in other fields, but never been used in the observed area. Figure 1 shows the model for stable production development.
Fig. 1 – Shaped technological systems development curves
Figure 1 shows production system development in coordinates time – production capacity. The wave-conception for describing the technical system (production) was well described by authors in [5]. This diagram (fig.1) shows big and small harmonics of production capacity changing. All of them show how it changes in time. Also, small harmonics represent small projects of technical organizational events. At the same time, big harmonics represent big projects during which sets of high and critical technologies (technological innovation kernels or production modernization) are being adopted. During research it was revealed that both kinds of s-shaped curves can be described by the Ferhulst equation:
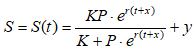
Sometimes equation (1) can degenerate with linear regression.
The application of s-shaped curves in production management firstly was described by Archibald in [11] though there was the only conception without mathematical description and practical use. So, the main achievement of current research is revealing mathematical regularity for production development in time. These curves lay in the basement of the cascade method in production management.
Cascade method in production managementThe Cascade method can be used for developing long term production strategies. It allows technical system management in all stages and levels of its lifetime circle: from the beginning till its restructuration. This requires a software application to conduct digital transformation. Figure 2 shows the general concept of the method.
Fig. 2 – Cascade method in production management
The first box in figure 2 – analysis of current production capacity and estimation required production values in the future. The results go to the second box input, where production strategy and road maps should be developed, this step requires s-shaped curves (1) for calculating dates and production capacity values. The third box: correcting road map from the previous step. The fourth box performs a method based on neuro networks for revealing the optimal production organizational structure. The final fifth box is a verification step. To verify all decisions that were taken we should build an imitation model that will show us how production will work in real-time. For this step, new software was developed [12]. Long-term production management is conducted by the feedback that goes from 5 step to the 1 to check production capacity value and if it is necessary to reconstruct production. So, from the first step to the last we continuously audit production capacity, build strategies using S-shaped curves, organize production developing optimal technological lines and production departments, verifying how it will work in real-time. Let us briefly consider all these boxes.
A. Production analysisDuring the time normal production should expand and eventually it will be stuck on production capacity deficit as well as with the need to renew equipment and involve new technologies. Such projects cost a lot so its planning should be ahead of time. To conduct it let us perform the following scheme (figure 3).
Fig. 3 – Scheme for analyzing and estimation financial costs on equipment in production technical preparation projects
This picture shows production capacity M(t) and production value (t) changing in time. We can see that even if we do not buy new equipment M(t) grows because of technology adaptation, it’s a natural process. But it’s still not enough to cover V(t) and V* (the value we are planning to produce in the nearest feature). So, we should answer two questions:
- When should we start technological reinforcement to cover V*?
- What is required production capacity C for values V*?
To answer these questions let’s use the following equation cascade (figure 4).
Fig. 4 – Cascade mathematical model of production development
The first and second equations define a start and end dates (tmin, tmax). The third equation defines the value of capital investments at the expense of the enterprise's funds, which can be used to develop production using its technical re-equipment. The fourth equation calculates C – production capacity growing.
At the same time, from the point of view of using the curves of technology development in Fig. 3, one can distinguish the following areas:
- (a1; b1) - transitional process S-shaped curve for the implementation of the technical re-equipment project at the expense of borrowed funds (credit).
- (a2; b2) - transitional process S-shaped curve for the implementation of the technical re-equipment project at the expense of the enterprise's funds (profit).
Within this interval, combined project management schemes from various funding sources are possible.
Figure 3 shows the existing production capacity and production volumes. In the tmax area, production will move from the surplus zone to the production capacity deficit zone. At the same time, updating the production base to tmin is illiquid due to incomplete depreciation of the equipment. Thus, the calculation of the timing of the technical re-equipment of production must be made based on the conditions for the sufficiency of production capacity and the terms of equipment depreciation [13], [14].
It should be noted that the analysis of the diagram in Figure 4 makes it possible to estimate only the general deficit of production capacity. In serial production, local "bottlenecks" often arise, the identification of which can be carried out exclusively through simulation, for example [12]. Debottlenecking can be accomplished by (a) introducing additional equipment groups; (b) changes in the technological process (modernization); (c) changing the order in which products are put into processing.
The general deficit in production capacity can be eliminated by an exceptional renewal of production using the means of the production reinforcement. The cascade of equations 4 just allows you to calculate the control data for the initialization of such a project for the preparation and re-equipment of production.
B. Cascade method in production managementAfter the stage of analysis of production capacity (block 1 of Fig. 2) and deciding on the initialization of the reinforcement project, it is necessary to develop a phased schedule for this project (block 2). Figure: 5 shows the general concept of project management of technical re-equipment of production in terms of time-cost coordinates.
Fig. 5 – Scheme for Project management using the cascade method based on S-shaped curves
The mathematical model for figure 5 can be described by (1) [11], [13].
C. Production structure optimizationTo reduce the costs and increase the efficiency of their use, the drawings of technological layouts must be optimized according to the criteria of cargo turnover and area (block 4). The optimization method using neural networks is discussed in detail in [11, 12, 14]. Their main idea is the primary clustering of the flow of parts and assembly units using self-organizing Kohonen maps and then identifying representative products for which a group or modular technological process will be designed. The problem of optimizing the actual drawing of the technological layout (equipment location) belongs to the classical problems of system analysis (the problem of the traveling salesman, the optimal cut, etc.) and can be solved using genetic algorithms and cascade neural networks, as well as using the Pareto method, where competing for the criteria will be the area of the workshop and the turnover of goods.
D. VerificationTo verify the design and technological solutions at the previous stages, it is recommended to use three-dimensional modelling systems (block 5) (Fig. 6). This need arises because often when designing complex production systems, two-dimensional layouts may not reflect the inconsistency of the transport and logistics interchanges of the workshop, or errors in the design of lightweight partitions. In addition to all this, even with painstaking analysis of the production load, a real production system can show either an incomplete load or, on the contrary, an overload - all this can be a consequence of the emergence of local "bottlenecks" that can only be identified empirically or through dynamic modelling. To identify such local bottlenecks, it is recommended to perform 3D simulation modelling in appropriate environments, such as Open CIM. During the research, new software was developed (fig.6). It allows not only visualizing the work of shops/sections / technological lines to identify processing queues, uneven equipment loading but also contextually solve these problems.
Fig. 6 – Factory 3D imitation modeling using original software system
ResultsThe cascade method for managing projects for technical re-equipment of production was tested for enterprises of the aviation industry. It showed good results: within 2 years, completely new products were supplied and mastered. The experience of using the method at an instrument-making enterprise made it possible to master about 80 new unique products within 5 years; at the same time, the efficiency of using production capacity has doubled.
However current research is on the go. The main current goals are improving 3D system for production simulation – implementing into one software system all methods and approaches that were observed in article to conduct user-friendly environment for using the cascade method.
Conclusion
Let's formulate the main results of the research:
- Was formulated and formalized the problem of project management of technical re-equipment of production according to the criteria of time-cost.
- To solve this problem, a cascade method of managing projects for technical re-equipment of production was developed. This method involves the use of mathematical, 3D, and simulation modeling.
- The cascade method for production management has already been successfully tested and has proven itself well for enterprises in the aviation and instrument-making industry.
Конфликт интересов Не указан. | Conflict of Interest None declared. |
Список литературы / References
- Белоусов Ю. В. Методология определения цифровой экономики / Ю. В. Белоусов, О. И. Тимофеева// Мир новой экономики. 2019;13(3):79-89. DOI: 10.26794/2220-6469-2019-13-4-79-89
- Kurganova N. Digital twins’ introduction as one of the major directions of industrial digitalization / N. Kurganova, М. Filin, D. Cherniaev et al. // International Journal of Open Information Technologies ISSN: 2307-8162 vol. 7, no.5, 2019.
- Grieves M. Digital twin: manufacturing excellence through virtual factory replication / M. Grieves // White paper. 2014. V. 1. P. 1–7
- Шведенко В.Н. Применение концепции цифровых двойников на этапах жизненного цикла производственных систем / В.Н. Шведенко, А.Е. Мозохин // Научно-технический вестник информационных технологий, механики и оптики. 2020. Т. 20. № 6. С. 815–827. DOI: 10.17586/2226-1494-2020-20-6-815-827
- Евгенев Г.Б. Российские технологии создания систем класса «Индустрия 4.0». Часть 2 / Г.Б. Евгенев // Известия высших учебных заведений. Машиностроение, 2018, № 9, с. 18–27, DOI: 10.18698/0536-1044-2018-9-18-27.
- Боровков А.И. Цифровые двойники: определение, подходы и методы разработки / А.И. Боровков, Ю.А. Рябов // Цифровая трансформация экономики и промышленности: сб. тр. конф. ИНПРОМ-2019 / под. ред. А.В. Бабкина. СПб.: СПбПУ, 2019. С. 234–245.
- Боровков А.И. Цифровые двойники в высокотехнологичной промышленности. Краткий доклад / А.И. Боровков и др. СПб.: ПОЛИТЕХ-ПРЕСС, 2019. 62 с.
- Kovacic I. Building life cycle optimization tools for early design phases / I. Kovacic, V. Zoller // Energy. 2015. No. 92. P. 409–419. DOI: 10.1016/j.energy.2015.03.027
- Selivanov S. Regularities of high technologies involvement in production / S. Selivanov, A. Shayhulova, S. Poezjalova // Proc. of 17th International Workshop on Computer Science and Information Technologies (CSIT’2015) vol.2 p.66 – 69
- Kutin A.A. Future Development of Digital Manufacturing in Russia / A.A. Kutin, N.N. Zakshevskaya, S.G. Selivanov et al. // Proc. Of the 3rd International Conference on Manufacturing Engineering and Technology for Manufacturing Growth (METMG 2015) pp. 31 – 35
- Selivanov S. Usage of new technologies involvement regularities during project management in production technologic preparation / S. Selivanov, A. Shayhulova // Proc. of the 16th International Workshop on Computer Science and Information Technologies (CSIT’2014). vol 2 pp 74-78
- Селиванов С. Г. Законы и закономерности Инноватики / С. Г. Селиванов, А.Ф. Шайхулова, С.Н. Поезжалова // Международный научный журнал «Инновации в жизнь». № 1 (20) март 2017 – с.13-16
- Selivanov S. Methods of innovative development in technic reconctruction / S. Selivanov, A. Shayhulova, G. Kamalova // LAP LAMBERT Academic Publishing is a trademark of: AV Akademikerverlag GmbH & Co. KG, Saarbrucken, Germany. 316 p.
- Love P.E.D. The ‘how’ of benefits management for digital technology: From engineering to asset management / P.E.D. Love, J. Matthews // Automation in Construction. 2019. No. 107. DOI: 10.1016/j.autcon.2019.102930.
Список литературы на английском языке / References in English
- Belousov Yu.V. Metodologija opredelenija cifrovoj jekonomiki [Methodology for defining the digital economy] / Ju. V. Belousov, O. I. Timofeeva // Mir novoj jekonomiki [World of the New Economy]. 2019;13(4):79-89. DOI: 10.26794/2220-6469-2019-13-4-79-89.
- Kurganova N. Digital twins’ introduction as one of the major directions of industrial digitalization / N. Kurganova, М. Filin, D. Cherniaev et al. // International Journal of Open Information Technologies ISSN: 2307-8162 vol. 7, no.5, 2019.
- Grieves M. Digital twin: manufacturing excellence through virtual factory replication / M. Grieves // White paper. 2014. V. 1. P. 1–7
- Shvedenko V.N. Primenenie koncepcii cifrovyh dvojnikov na jetapah zhiznennogo cikla proizvodstvennyh sistem [Concept of digital twins at life cycle stages of production systems] / V.N. Shvedenko, A.E. Mozohin // Nauchno-tehnicheskij vestnik informacionnyh tehnologij, mehaniki i optiki. [Scientific and Technical Journal of Information Technologies, Mechanics and Optics], 2020, vol. 20, no. 6, pp. 815–827. DOI: 10.17586/2226-1494-2020-20-6-815-827.
- Evgenev G.B. Rossijskie tehnologii sozdanija sistem klassa «Industrija 4.0». Chast' 2 [Russian Technologies for Creation of Industry 4.0 Systems. Part 2] / G.B. Evgenev // Izvestija vysshih uchebnyh zavedenij. Mashinostroenie. [Proceedings of Higher Educational Institutions. Маchine Building], 2018, no. 9, pp. 18–27, DOI: 10.18698/0536-1044-2018-9-18-27.
- Borovkov A.I. Cifrovye dvojniki: opredelenie, podhody i metody razrabotki [Digital doubles: definition, approaches and methods of development] / A.I. Borovkov, Ju.A. Rjabov // Cifrovaja transformacija jekonomiki i promyshlennosti: sb. tr. konf. INPROM-2019 [Digital transformation of economy and industry: collection of tr.conf. INPROM-2019] / ed. A.V. Babkina. SPb.: SPbPU, 2019. P. 234–245.
- Borovkov A.I. Cifrovye dvojniki v vysokotehnologichnoj promyshlennosti. Kratkij doklad [Digital doubles in high-tech industry. Brief report] / A.I. Borovkov et al. SPb.: POLITEH-PRESS, 2019. 62 p.
- Kovacic I. Building life cycle optimization tools for early design phases / Kovacic, V. Zoller // Energy. 2015. No. 92. P. 409–419. DOI: 10.1016/j.energy.2015.03.027
- Selivanov S. Regularities of high technologies involvement in production / S. Selivanov, A. Shayhulova, S. Poezjalova // Proc. of 17th International Workshop on Computer Science and Information Technologies (CSIT’2015) vol.2 p.66 – 69
- Kutin A.A. Future Development of Digital Manufacturing in Russia / A.A. Kutin, N.N. Zakshevskaya, S.G. Selivanov et al. // Proc. Of the 3rd International Conference on Manufacturing Engineering and Technology for Manufacturing Growth (METMG 2015) pp. 31 – 35
- Selivanov S. Usage of new technologies involvement regularities during project management in production technologic preparation / S. Selivanov, A. Shayhulova // Proc. of the 16th International Workshop on Computer Science and Information Technologies (CSIT’2014). vol 2 pp 74-78
- Selivanov S. Zakony i zakonomernosti Innovatiki [Principles and Regularities of Innovatics] / S. G. Selivanov, A.F. Shajhulova, S.N. Poezzhalova // Mezhdunarodnyj nauchnyj zhurnal «Innovacii v zhizn'» [International Journal "Innovations in life"] № 1 (20) march 2017 pp.13-16
- Selivanov S. Methods of innovative development in technic reconctruction / S. Selivanov, A. Shayhulova, G. Kamalova // LAP LAMBERT Academic Publishing is a trademark of: AV Akademikerverlag GmbH & Co. KG, Saarbrucken, Germany. 316 p.
- Love P.E.D. The ‘how’ of benefits management for digital technology: From engineering to asset management / P.E.D. Love, J. Matthews // Automation in Construction. 2019. No. 107. DOI: 10.1016/j.autcon.2019.102930.