МЕТОДИКА ИССЛЕДОВАНИЯ ДОКРИТИЧЕСКОГО РОСТА ТРЕЩИН В КЛЕЕВЫХ СОЕДИНЕНИЯХ
Муру Г.Н.1, Корягин С.И.2, Буйлов С.В.3, Великанов Н.Л.4, Шарков О.В.5
1Кандидат технических наук, доцент, 2Доктор технических наук, профессор, 3Кандидат технических наук, профессор, 4Доктор технических наук, профессор, 5Доктор технических наук, профессор, Балтийский федеральный университет им. И. Канта, г. Калининград
МЕТОДИКА ИССЛЕДОВАНИЯ ДОКРИТИЧЕСКОГО РОСТА ТРЕЩИН В КЛЕЕВЫХ СОЕДИНЕНИЯХ
Аннотация
Анализ причин разрушения клеевых соединения показывает, что в большинстве случаев оно вызвано наличием конструктивных и технологических концентраторов напряжений, из-за которых в процессе эксплуатации развиваются трещины. В правильно спроектированных и качественных клееных конструкциях слабое место располагается не по клею. Исключением из этого правила является разрушение под действием окружающей среды. Долговечность представляет собой сумму периодов зарождения и подрастания трещины до некоторого предельного размера, определяемого либо условием хрупкого разрушения, либо потерей какого-то технического свойства, например герметичности. Для количественного анализа необходимы характеристики сопротивления клеевого соединения разрушению на всех этапах: образование трещины, медленный рост, переход к хрупкому разрушению.
Ключевые слова: клеевые соединения, хрупкое разрушение, рост трещины, консольные балки.
Muru G.N.1, Koryagin S.I.2, Byilov S.V.3, Velikhanov N.L.4, Sharkov O.V.5
1PhD in Engineering, Associate Professor, 2PhD in Engineering, Professor, 3PhD in Engineering, Professor, 4PhD in Engineering, Professor, 5PhD in Engineering, Professor, Immanuel Kant Baltic Federal University, Kaliningrad
RESEARCH TECHNIQUE FOR SUBCRITICAL CRACK EXTENSION IN ADHESIVE JOINTS
Abstract
Analysis of reasons of adhesive joints destruction shows that in most cases it happened because of constructive and technological stress concentrators which cause cracks when in operation. In properly designed high-quality glued structures trouble spot is not along a glue line. An exception to this rule is destruction caused by the environment. Durability is the sum of periods of crack nucleation and crack growth up to some maximum size, which is identified by a brittle fracture or loss of some technical property, for example air‑tightness. Properties of adhesive joints resistance to breakage during all stages are needed for quantitative analysis: crack formation, slow growth, followed by a brittle fracture. In this article there are methodology and results of a research of the second stage of breakage, i.e. slow growth of a crack under long-term static loading and also in liquid mediums.
Keywords: adhesive joints, brittle fracture, growth of a crack, cantilever beam.
Introduction
Durability of adhesive joints should be prognosed on the basis of destruction mechanisms. Analysis of reasons of adhesive joints destruction shows that in most cases it happened because of constructive and technological stress concentrators which cause cracks when in operation [1,2]. In properly designed high-quality glued structures trouble spot is not along a glue line. An exception to this rule is destruction caused by the environment.
In accordance with works [3, 4] durability is the sum of periods of crack nucleation and crack growth up to some maximum size, which is identified by a brittle fracture or loss of some technical property, for example air‑tightness. Properties of adhesive joints resistance to breakage during all stages are needed for quantitative analysis: crack formation, slow growth, followed by a brittle fracture. [6]
The aim of this study was to develop a testing technique allowing to get spontaneously changing as well as constant crack growth force value for a specimen.
In this article there are methodology and results of a research of the second stage of breakage, i.e. slow growth of a crack under long-term static loading and also in liquid mediums.
In order to investigate adhesive joints failure double cantilever beam specimen is widely used, beams of which are narrowed at the angle of 7, 04˚ [7, 8]. At some part of a specimen such shape of beams provides weak dependence of force during crack growth. It simplifies tests. However, as it was noted in the work [5], methods of testing of such specimen under long-term static loading are too complicated for wide use. As a result of this, the so called specimens of permanent offset are usually more preferable in subcritical destruction tests. Specimen is a double cantilever beam splitted with a wedge or screws. Crack growth force is declining rapidly during crack extension in these specimens [5, 7], they are suitable for establishing threshold values of crack growth force at which crack growth stops. However significant difficulties arise during determination of delamination speed at a given level of growth force.
Fig.1 - Double cantilever specimen: 1 – cantilever beams; 2 – adhesive layer; shape of unglued cantilever beams (hachure line)
In our research we used a specimen similar to previously described specimens. It also consists of two beams connected with glue under study. Beams have cross-section all along the length; unglued beams are bent (Fig. 1) [9].
Theory and estimated dependencies
Let us consider the destruction process of such specimen. Glued specimen has potential energy [10].
(1)
where l is the specimen length; a is the crack length; M is bending moment; E is the modulus of elasticity of the cantilever beam; I is the moment of inertia of the cantilever beam cross section.
Crack growth force:
(2)
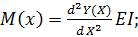

where y is bending; R is radius of curvature,
For the specimen beams of rectangular cross-section where h is the height of cross-section of the beam.
Maximum permissible value GI can be determined by linear-elastic deformation of the beams and in this case where σ either the limit of proportionality or elastic limit of the cantilever beam material can be used depending on which amount is smaller.
The technique described was used for the research of the Sprut Plus adhesive composition crack resistance. Glass reinforced coatings based on the Sprut Plus composition are used in the reinforcement of a load capacity of worn-out capacitive equipment without its decommissioning.
Preparation of specimens
Cantilever beam specimens were made of steel (Art. 3). Preliminary bending was made by rolling the beams through three roller bending machine. The radius of curvature of the beam was constant along the whole length (excluding end sections, which were used for crack initiation). The radius of curvature was determined through the value of deflection. Residual stresses in beams were eliminated by thermal processing. Beams were straightened by stretching screws and brackets before specimen adhesion.
Surface treatment consisted of cleaning it with abrasive cloth and degreasing. The quality of preparation was considered satisfactory if there was a solid water film on the surface.
Adhesion was carried out the following way. Cantilever beams surfaces were covered with glue, a layer of glass fabric was placed on one of the beams then it is being rolled unless it was saturated with glue; then cantilever beams were connected. Before testing the specimen was being held in the air for ten days. Cracks were initiated by splitting the specimen at both ends. The specimen was compressed at the beginning of working spaces with clamps. The crack tip displacement was measured with microscope MIR-2.
The results of tests in the air are shown in Fig. 2. There are significant variations of experimental data. The curves in Figures 2 and 3 were drawn in such a way that they primarily reflect the upper speed limit of a crack growth. Minimum values GI, below which there is no crack propagation were established on a time base 2×106 seconds. Points corresponding to zero speeds were marked on a horizontal axis. Test on specimens when GI <2/3GIa showed that crack growth started some time after the beginning of tests (where Gla is the crack growth force when it stops given the unstable fracture under increasing static load). There was no reliable registration of such incubation period under large values of GI. Part of specimens, tested under GI>0,8GIa, was immediately destroyed after the clamps were removed, or the crack spread along the entire working area after some slow growth. It shows that in adhesive layer there are zones with lower crack resistance. During fast crack growth along the specimen these zones of the cantilever beam accumulate kinetic energy which is then spent on its destruction. Cohesive failure occurred in all specimens which were exposed to the air during tests.
In order to assess the influence of liquids on the process of destruction, specimens after tests in air for establishing the crack extension speed were placed in distilled water and in petroleum products.
Test results in petroleum products are shown in Fig. 2. Petroleum products had little impact on the crack growth speed. The speed was slightly increasing and this increase was more noticeable at high values of GI. The impact was insignificant because there is no chemical interaction between petroleum products and adhesive and because of high molecular weight of petroleum products which hinders their diffusion into adhesive. An increase of the crack growth speed happened because of a wedging effect of a thin liquid layer, which was caused by a difference of values of thermodynamic and chemical potentials of a thin layer from their values in a bulk phase [1].
Results and discussion
Results of tests of specimens in water are shown in Fig.3. Two areas can be singled out in the diagram (solid line), the values of which are marked at 200 J/m2. Water increases the crack growth speed at values lower than the mentioned one and decreases it at larger values. The transition from cohesive to adhesive fracture was registered approximately at that value. Reverse transition from adhesive to cohesive fracture happens at 300 J/m2. During further increase of GI difference between crack growth speed in the air and in water decreases. Peculiarities of adhesive joints destruction at GI larger than 200 J/m2 qualitatively coincide with famous tests on epoxy adhesive joints [6]. Apparently it can be explained by the same reactions: destruction happens at large GI because water was delivering plasticizing power while penetrating glue. The growth of crack extension speed, the decline of the volume of diffusing water and accordingly its influence lead to adhesive-cohesive transition. When GI is less than 200 J/m2 the crack growth speed is small and polymer material at the crack tip is being influenced by water and mechanical stresses for considerably large amount of time. It is likely that such long-term influence leads to chemical changes in adhesive, which reduce its crack resistance.
Results of tests in water of specimens which were previously kept in water and in the air are shown in Fig. 3. Specimens for these tests were produced the following way. Adhesive composition with reinforcing material was placed on a straightened cantilever beam, after that the polymerization of adhesive was carried out.
Fig. 2 - The crack growth speed in the air (solid line) and in petroleum products (hachure line)
Fig. 3 - The crack growth speed in water of the specimen which was previously kept in the air for 10 days (solid line); in the air for 10 days and in water for 30 days (hachure line)
Half of the cantilever beam was placed in water, where it was kept for 30 days, then the other half of the cantilever beam was glued to it, then the crack was initiated and the specimen was placed in water. As it can be seen in Figure 3, the crack growth speed at large GI became lower after the specimen was kept in water (plasticizing effect of water is realized) and remained the same at low GI.
Conclusion
The testing technique described was based on the usage of residual stresses for the specimen destruction which appear during the specimen assembling, it allows to use the specimen as a double cantilever beam in order to get spontaneously changing as well as constant crack growth force value. Lack of loading system simplifies tests under conditions of active mediums influence, elevated and lowered temperatures and other similar exploitation factors.
Research results can be used in engineering practice in adhesive products design.
Список литературы / References
- Зимон А. Д. Адгезия пленок и покрытий / А. Д. Зимон // – М.: Химия, 1977. – 352 с.
- Кортен Х. Т. Механика разрушения композитов / Х. Т. Кортен // В кн.: Разрушение / Пер. с англ. Под ред. Ю. Н. Роботнова. – М.: Машиностроение, 1976. – № 7. – ч. 1. – C. 367–
- Писаренко Г. С. О механической прочности материалов и элементов конструкций / Г. С. Писаренко // Пробл. прочности, 1984. – № 1. –C. 3–
- Салганик Р. Л. Временные эффекты при хрупком разрушении / Р. Л. Салганик // Там же, 1971 – № 2. – C. 79–
- Bascom W. D. Stress corrosion of structural adhesive bonds / W. D. Bascom // Adhesive Age. – 1979. – 22 (4). – P. 28–
- Cherry B. W. The environmental fracture of adhesive joints / B. W. Cherry, K. W. Thomson // Adhesion. 1980, – P.103–112.
- Kinloch A. J. Interiacial fracture mechanical aspects of adhesive bonded joints / A. J. Kinloch //A review. – J. Adhesion – – Vol.10. – № 3. – P. 193–219.
- Mostovoy S., Ripling E. J. Fracture tonghness of an epoxy system / S. Mostovoy, E. J. Ripling // J. Appl. Polymer Sci. – – Vol. 10. – № 9. – P. 1351–1371.
- Буйлов С. В. Способ испытания клеевого соединения на прочность / С. В. Буйлов, С. И. Корягин // Авт. Св. СССР № 1529672, 1999.
- Корягин С. И. Несущая способность композиционных материалов / С. И. Корягин // ГИПП «Янтарный сказ». – Калининград, 1996, – 301 c.
Список литературы на английском языке / References in English
- Zimon A. D. Adgeziya plenok i pokryitiy [Adhesion of films and coatings] / A. D. Zimon // Moscow, Khimiya [Chemistry]. – 352 P. [in Russian]
- Korten Kh. T. Mehanika razrusheniya kompozitov [Mechanics of destruction of composite materials] / Kh. T. Korten // Razrusheniye [Destruction] / Translated from English Ed.: Robotnov Yu.N. Moscow, Mashinostroenie [Mechanical engineering]. – Vol. 7. – Part 1. – P. 367–471 [in Russian]
- Pisarenko G. S. O mehanicheskoy prochnosti materialov i elementov konstruktsiy [Mechanic strength of materials and construction elements] / G. S .Pisarenko // prochnosti – [Strength of Materials]. – 1984. – № 1. – P. 3–5 [in Russian]
- Salganik R. L. Vremennyie effekti pri khrupkom rasrushenii [Brittle fracture time effects] / R. L. Salganik // Ibid. – № 2. – P. 79–85 [in Russian]
- Bascom W. D. Stress corrosion of structural adhesive bonds / W. D. Bascom // Adhesive Age. – Vol. 22. – № 4. – P. 28–34.
- Cherry B. W. The environmental fracture of adhesive joints / B. W. Cherry, K. W. Thomson // Adhesion – Vol. 4. – P.103–112.
- Kinloch A. J. Interiacial fracture mechanical aspects of adhesive bonded joints / A. J. Kinloch // Adhesion – Vol.10. – № 3. – P. 193–219.
- Mostovoy S. Fracture tonghness of an epoxy system / S. Mostovoy, E. J. Ripling // – J. Appl. Polymer Sci. – Vol. 10. – № 9. – P. 1351–1371.
- Builov S. V. Sposob ispyitaniya kleevogo soedineniya na prochnost [Method of testing the strength of adhesive joints] / S. V. Builov, S. I. Koryagin // Patent USSR № 1529672, 1999 [in Russian]
- Koryagin S. I. Nesuschaya sposobnost kompozitsionnyih materialov [Loading capacity of composite materials] / S. I. Koryagin // State publishing and printing house Jantarnyi skaz – 1996. – 301 P. [in Russian]