ИССЛЕДОВАНИЕ ПРОЦЕССА ВОССТАНОВЛЕНИЯ СИСТЕМЫ [Ni1-x, Cox](Fe1-x, Mox)2O4+NH4ReO4 И РАЗРАБОТКА ТЕХНОЛОГИИ ПОЛУЧЕНИЯ МАРТЕНСИТНО-СТАРЕЮЩEГО СТАЛЬНОГО ПОРОШКА
ИССЛЕДОВАНИЕ ПРОЦЕССА ВОССТАНОВЛЕНИЯ СИСТЕМЫ [Ni1-x, Cox](Fe1-x, Mox)2O4+NH4ReO4 И РАЗРАБОТКА ТЕХНОЛОГИИ ПОЛУЧЕНИЯ МАРТЕНСИТНО-СТАРЕЮЩEГО СТАЛЬНОГО ПОРОШКА
Аннотация
Одним из приоритетных направлений современного материаловедения является создание материалов с высокими и функциональными свойствами. К числу таких материалов относятся мартенситно-стареющие стали, используемые в транспортной технике, машиностроении, авиастроении, судостроении, приборостроении, атомной энергетике, военной промышленности и т.д. В отличие от углеродистых сталей, мартенситно-стареющие стали более устойчивы к хрупкому разрушению, особенно при отрицательных температурах. Эти стали хорошо поддаются обработке резанием, легко деформируются и подвергаются термической обработке.
Исследованы механизм и кинетика восстановления шихты, изготовленной из сложного оксида [Ni1-x, Cox](Fe1-x, Mox)2O4, синтезированного из оксидной системы Fe2O3–NiO–CoO–MoO3, и перрената аммония (NH4ReO4). Путем совмещения процессов синтеза и восстановления сложных оксидов разработана эффективная технология производства легированных металлических порошков, которая позволяет получать высокопрочные порошки мартенситно-стареющей стали со сверхчистым химическим составом, требуемыми структурой и свойствами. Показано, что полученные стальные порошки по своим физико-технологическим свойствам не уступают стандартному стальному порошку, а в ряде случаев даже превосходят его.
1. Введение
Развитие современной техники, особенно в области военной промышленности, требует создания материалов с функциональными свойствами и, прежде всего, с высокой прочностью и пластичностью, которые будут способны работать в условиях переменных нагрузок при высоких и низких температурах, особенно отрицательных. Большое значение для этих материалов имеет ударная вязкость в качестве структурно-чувствительного свойства. При наличии комплекса указанных свойств повышаются предел текучести материала, усталостная прочность, а также способность работать при переменных нагрузках. К числу таких перспективных материалов относятся мартенситно-стареющие стали, которые используются в транспортной технике, авиастроении, судостроении, приборостроении, атомной энергетике, военной промышленности и т.д. [1], [2], [3]. В отличие от углеродистых сталей, мартенситно-стареющие стали более устойчивы к хрупкому разрушению, особенно при отрицательных температурах. Эти стали хорошо поддаются обработке резанием, легко деформируются и подвергаются термической обработке [2], [4], [6], [7].
Мартенситно-стареющие стали должны иметь высокую химическую чистоту и не содержать примесей, таких как углерод, водород, кислород, азот, сера и фосфор. По этой причине наиболее целесообразно получать указанные стали методом порошковой металлургии, синтезом сложных оксидов из оксидов компонентов [8], [9], восстановлением, прессованием полученного стального порошка, сваркой, горячей экструзией и термической обработкой [3]. В качестве исходных материалов для легирования рением следует использовать оксиды высокой чистоты и перренат аммония. Полученная по указанной технологии порошковая сталь не только отличается высокими технико-экономическими показателями, но и дает возможность получить мелкозернистую структуру, высокие физико-механические, технологические и эксплуатационные свойства. Однако ограниченность производства легированных металлических порошков не позволяет осуществлять массовое производство порошковых композиционных материалов.
Исходя из вышесказанного, целью работы является исследование механизма и кинетики восстановления шихты, изготовленной из сложного оксида [Ni1-x, Cox](Fe1-x, Mox)2O4, синтезированного из оксидной системы Fe2O3–NiO–CoO–MoO3, и перрената аммония (NH4ReO4), и разработка технологии получения высокопрочных мартенситно-стареющих стальных порошков.
2. Постановка задачи и обоснование методики
Мартенситно-стареющие стали относятся к группе сверхчистых сплавов, т.е. характеризуются точным химическим составом, отсутствием полостей и определенной структурой [1], [2], [7]. С этой точки зрения, технология получения мартенситно-стареющих стальных порошков отличается от известных технологий и позволяет до восстановления сложных оксидов готовить шихту, дополнительно легируя ее рением в виде перрената аммония (NH4ReO4).
Согласно приведенной реакции
при восстановлении перрената аммония водородом получается рений высокой чистоты, который, будучи очень активным, растворяется в системе Fe-Ni-Co-Mo, образуя твердые растворы и интерметаллиды рения, повышая прочность, твердость, ударную вязкость, теплоемкость, коррозионную стойкость, хладноломкость порошковой стали. Особенность рения состоит в том, что, будучи металлом с плотной гексагональной структурой, он обладает высокой растворимостью в переходных металлах (до 65 ат.%), кристаллическая решетка которых объемно-центрированная кубическая.
Согласно исследованиям Тумарева и Чуфарова [10], [11], если процесс восстановления оксидных систем осуществляется при высоком потенциале, то он будет протекать без разделения. При обычном восстановлении, например с помощью H2, происходит деление оксидов, следовательно, имеет место селективное восстановление. Что касается оксидных систем, не содержащих трудно восстанавливаемые оксиды, то процесс восстановления в этом случае проходит без осложнений. Оксидная система «[Ni1-x, Cox](Fe1-x, Mox)2O4», разработанная в работе [9], не подвергается делению, так как термодинамические потенциалы компонентов близки друг к другу. По этой же причине она восстанавливается, производя стальной порошок, в котором металлические компоненты смешиваются в виде твердых растворов или интерметаллических соединений. Даже если происходит частичное деление, система не может влиять на процесс формирования сплава.
Эксперименты проводились на термогравиметрической установке (рис. 1), которая дает возможность постоянно контролировать изменение массы образца, поддерживая постоянной требуемую температуру. Водород с точкой росы от -30 до -400Сиз баллона 1 через редуктор 2, реометр 3 и манометр 4 поступает в батарею с абсорбционными сосудами, которые наполнены активированным углем 5, хлоридом кальция 6, силикагелем 7, концентрированной серной кислотой 8 и гидроксидомнатрия 9. Осушенный водород через вентиль 11 поступает в реактор 12, куда заранее с помощью корзины 13 помещается образец(шихта), подготовленный для восстановления. Продукты реакции удаляются через трубку 14. Изменение (потеря) массы навески (образца) фиксируется на аналитических весах 15типа АДБ-200М. В качестве инертного газа для продувки реактора используется азот 10, который осушается по той же схеме, что и водород.
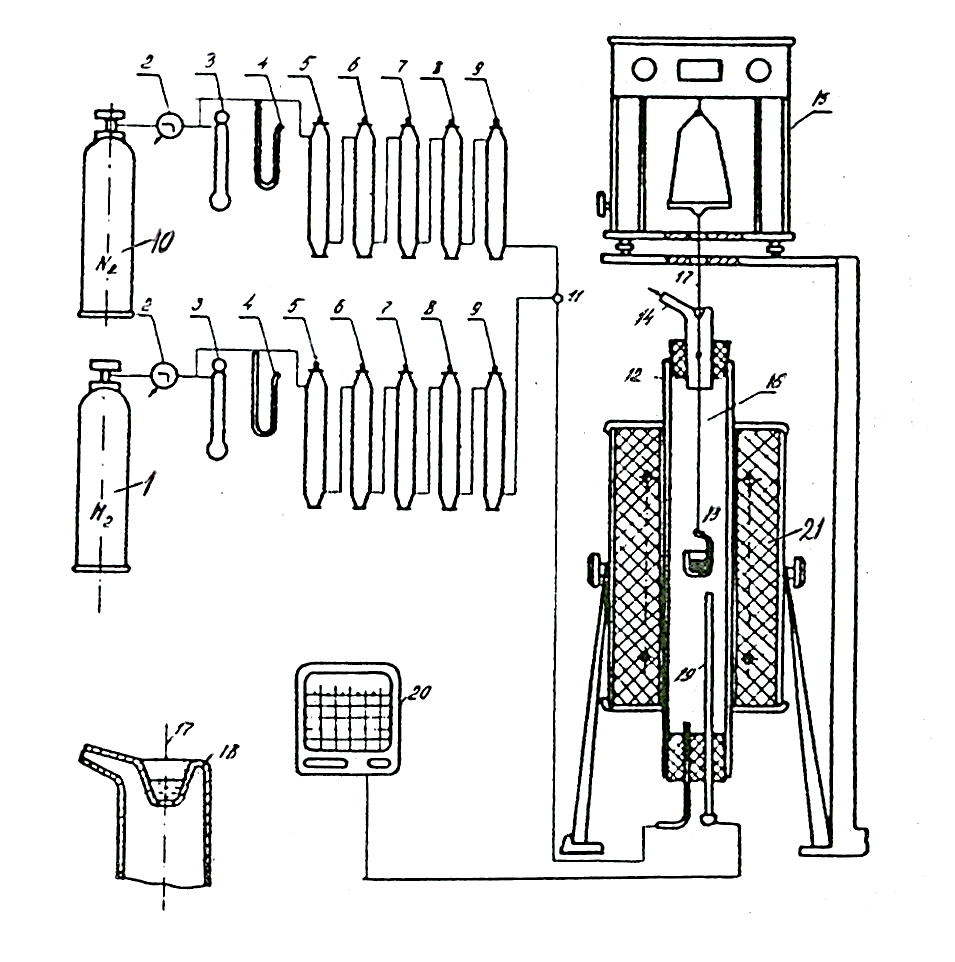
Рисунок 1 - Схема термогравиметрического прибора:
1 – баллон с водородом, 2 – редуктор, 3 – реометр, 4 – манометр, 5 – сосуд с активированным углем, 6 – сосуд с хлоридом кальция, 7 – сосуд с силикагелем, 8 – сосуд с концентрированной серной кислотой, 9 – сосуд с гидроксидом натрия, 10 – баллон с азотом, 11 – клапан, 12 – реактор, 13 – кварцевая корзина, 14 – выход продуктов реакции, 15 – аналитические весы, 16 – нихромовая проволока, 17 – капроновая проволока, 18 – капиллярная трубка, 19 – термопара, 20 – потенциометр, 21 – печь
Реактор представляет собой трубу из нержавеющей и тугоплавкой стали (П136 мм), которая помещена в электропечь типа Т-40/600. После сборки и выпуска устройства реактор продувают азотом, затем подают водород и определяют потерю массы образца за определенный период времени. Расход водорода – 1 л/мин. Отклонение, вызванное контактом капроновой проволоки с капиллярной жидкостью, находится в пределах чувствительности весов и не влияет на точность эксперимента. Степень восстановления (λ, %) рассчитывают по потере массы и скорости восстановления (по скорости изменения массы в единицу времени (V, мг/мин)).
3. Результаты исследования
Для получения мартенситно-стареющего стального порошка состава 18%Ni+10%Co+5%Mo+0,7%Re+Feмн на термогравиметрической установке была восстановлена шихта состава 99%[Ni1-x, Cox](Fe1-x,Mox)2O4+1%NH4ReO4, приготовленная механическим перемешиванием в течение 1,5...2,0 ч,. Результаты исследования, полученные в виде интегральных и дифференциальных кривых, представлены на рис. 2 и 3. Как видно из рисунков, кинетические кривые претерпевают самокаталитический процесс восстановления. Вначале наблюдается быстрая потеря массы с незаметным индукционным периодом.
2O4 + 1% NH4ReO4 от срока выдержки](/media/images/2022-10-21/70c2afdc-77f2-40e8-9073-7b1f2362af63.png)
Рисунок 2 - Зависимость степени восстановления (λ) шихты состава 99% [Ni1-x, Cox](Fe1-x, Mox)2O4 + 1% NH4ReO4 от срока выдержки
Примечание: кривая 1 - 8500C, кривая 2 - 6500C
2O4+ 1% NH4ReO4](/media/images/2022-10-21/4229b08c-32f9-4770-a8d1-201e3378f594.png)
Рисунок 3 - Дифференциальная кривая восстановления шихты состава 99% [Ni1-x, Cox](Fe1-x, Mox)2O4+ 1% NH4ReO4
Равновесное давление кислорода и состав твердого раствора зависят от состава Me' и Me''. Механизм восстановления оксида Me'cMe''(1-c)Fe23+O4 (или MeMe3+(2-x)FexO4) можно представить следующим образом. До степени восстановления λ=33 % происходит быстрый переход Me2+ из шпинельной фазы в закисную фазу. Одновременно Fe3+ восстанавливается до Fe2+, большая часть которого замещает удаленный из шпинельной фазы Me2+, а избыток Fe2+ также переходит в закисную фазу. В результате количество MeFe2O4 в шпинельной фазе уменьшается. Образуется новый компонент Fe3O4 шпинельного раствора, концентрация которого достигает ~70% при λ=20%. Закисная фаза обедняется FeO. При >33% имеется только фаза переменной сложности – закисный твердый раствор, который при восстановлении полностью обедняется кислородом до чистого металла, т.е. образуется металлический сплав. Для оптимизации режимов восстановления (Т, τ) были испытаны образцы массой до 1 кг, где толщина слоя составляла 25 мм. Результаты экспериментов представлены на рис. 4. Как видно из рисунка, при Т=950°С и продолжительности τ=3 ч (кривая 2) происходит полное восстановление (100%), а при 850°С восстановление недостаточно и составляет 80%.
2O4 + 1% NH4ReO4 при температурах: 1 - 8500C; кривая 2 - 9500C](/media/images/2022-10-21/cfd0ca92-184d-4a52-9db0-f0446d6f8749.png)
Рисунок 4 - Кинетика восстановления шихты состава 99% [Ni1-x, Cox](Fe1-x, Mox)2O4 + 1% NH4ReO4 при температурах:
1 - 8500C; кривая 2 - 9500C
Форму зерна определяли с помощью оптического микроскопа, а гранулометрический состав - по ГОСТ18318-73 с помощью ситового анализа. Пикнометрическую плотность определяли с помощью пикнометра по ГОСТ 18898-73. Насыпную плотность определяли по ГОСТ 19440-74 с помощью волюмометра. За насыпную плотность принимали среднее из трех результатов измерений, разница которых не превышала +1,5 %. Сыпучесть металлических порошков определяли по ГОСТ 20899-75 и рассчитывали по формуле , где К - коэффициент соответствия, а τ – время течения металлического порошка (с). Плотность и формуемость металлических порошков определяли по ГОСТ 25280-82, причем оба свойства объединяли в одно понятие, которое называют прессуемостью. Уплотнение оценивали по кривой прессования металлических порошков, построенной в системе координат «пористость-давление», т.е. θ=f(P). Формование металлических порошков характеризовалось определенным диапазоном пористости (θ=20...25%), при котором на поверхности прессовок после снятия с прессформы не появляются трещины.
В табл. 1-3 приведены основные свойства мартенситно-стареющего стального порошка типа ПС-Н18К10М5Rе, полученного по разработанным оптимальным технологическим режимам (путем синтеза сложных оксидов и восстановления водородом).
Таблица 1 - Химический состав мартенситно-стареющего стального порошка типа ПС-H18K10M5R
Марка стали | Химический состав, % | ||||||||
основные элементы | примеси, не более | ||||||||
Fe | Ni | Mo | Co | Rе | C | Si | S | P | |
ПС-Н18К10М5Rе | ост. | 17,8... 18,3 | 4,8... 5,2 | 9,8... 10,2 | 0,6... 0,7 | 0,001 | 0,002 | 0,003 | 0,002 |
Н18К10М5 (стандарт) | ост. | 17,7... 19,0 | 4,6... 5,5 | 9,5... 10,5 | - | 0,03 | 0,200 | 0,020 | 0,020 |
Таблица 2 - Гранулометрический состав мартенситно-стареющего стального порошка типа ПС-H18K10M5Rе
Гранулометрический состав, % по массе | ||||
-0,160…+0,125 мм | -0,125…+0,100 мм | -0,100…+0,080 мм | -0,080…+0,040 мм | -0,040 мм |
8,7 | 9,5 | 12,1 | 18,2 | 51,5 |
Таблица 3 - Физические и технологические свойства мартенситно-стареющего стального порошка типа ПС-H18K10M5Rе
Пикнометрическая плотность, г/см3 | Насыпная плотность, г/см3 | Сыпучесть, с/50г | Уплотняемость при P=700 МПа, г/см3 | Прессуемость, г/см3 (нижний предел) |
8,15 | 2,6 | 38,0 | 6,7 | 4,5 |
Сравнение со стандартной сталью типа Н18К10М5 показывает, что мартенситно-стареющий стальной порошок типа ПС-H18К10М5Rе чище по количеству сплавов, чем литая сталь того же типа, что и ожидалось. Проблема заключается в том, что при ферритизации смеси, находящиеся в исходных оксидах (Fe2O3, NiO, CoO, MoO3), легко хлорируются и испаряются, что обусловлено их высокой упругостью пара. Температура испарения SiCl2 - 570С, AlCl5 - 1350С, TiCl4 - 3300С и т.д. Удаление смеси, в том числе из щелочных металлов и из перрената аммония (NH4ReO4), также легко осуществляется при восстановлении шихты. Эта технология имеет одно преимущество, согласно которому исключается азотирование металлического порошка (NH4Cl→NH3+HCl), при этом как исходные, так и синтезированные оксиды и перренат аммония не азотируются. Это объясняется тем, что процесс ферритообразования происходит при высоком кислородном потенциале, что значительно выше потенциала азота. Об этом свидетельствуют результаты химического анализа, согласно которым не обнаружено даже следов нитридов.
Таким образом, сложная оксидная технология получения легированных металлических порошков отличается от технологии термодиффузионного обогащения, разработанной в работе [13]. Металлические порошки, полученные методом термодиффузии, могут содержать большое количество азота, что обусловлено отходами диссоциации хлорида аммония в шихты, а также диссоциированным аммиаком, который часто используют в качестве защитной среды при диффузионном обогащении [14]. Например, стальной порошок П40Х содержит 0,009% N2, П70Х5 - 0,012% N2, П100Х12 - 0,014% N2, ПХ18Н12 - 0,2% N2. Содержание азота в некоторых металлических порошках достигает 0,54...0,75%. При этом загрязнение мартенситно-стареющих стальных порошков теми или иными сплавами не допускается.
Что касается физико-технологических свойств полученного стального порошка, то он находится в пределах нормы. Особенно он характеризуется хорошей плотностью и прессуемостью (рис. 3), что видно на диаграмме прессуемости (рис. 5). Металлический порошок губчатый (рис. 6), что характерно для порошков, полученных методом восстановления оксидов [14]. Индекс соосности зерен колеблется от 2,5 до 3,0. Диаграмма прессуемости - θ=f(P) и форма металлического порошка показаны на рис. 5 и 6.
![Диаграмма прессуемости мартенситно-стареющего стального порошка марки ПС-H18K10M5Rе - θ=f(P), полученного: 1 - синтезом и восстановлением оксидов; 2 - методом термодиффузии [13]](/media/images/2022-10-21/c82d1c24-464b-4c61-b8c4-423583756963.png)
Рисунок 5 - Диаграмма прессуемости мартенситно-стареющего стального порошка марки ПС-H18K10M5Rе - θ=f(P), полученного:
1 - синтезом и восстановлением оксидов; 2 - методом термодиффузии [13]
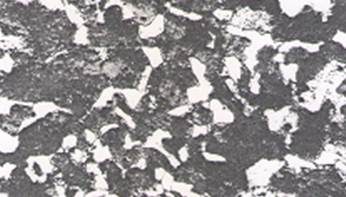
Рисунок 6 - Форма зерна мартенситно-стареющего стального порошка марки ПС-H18K10M5Rе
Примечание: x100
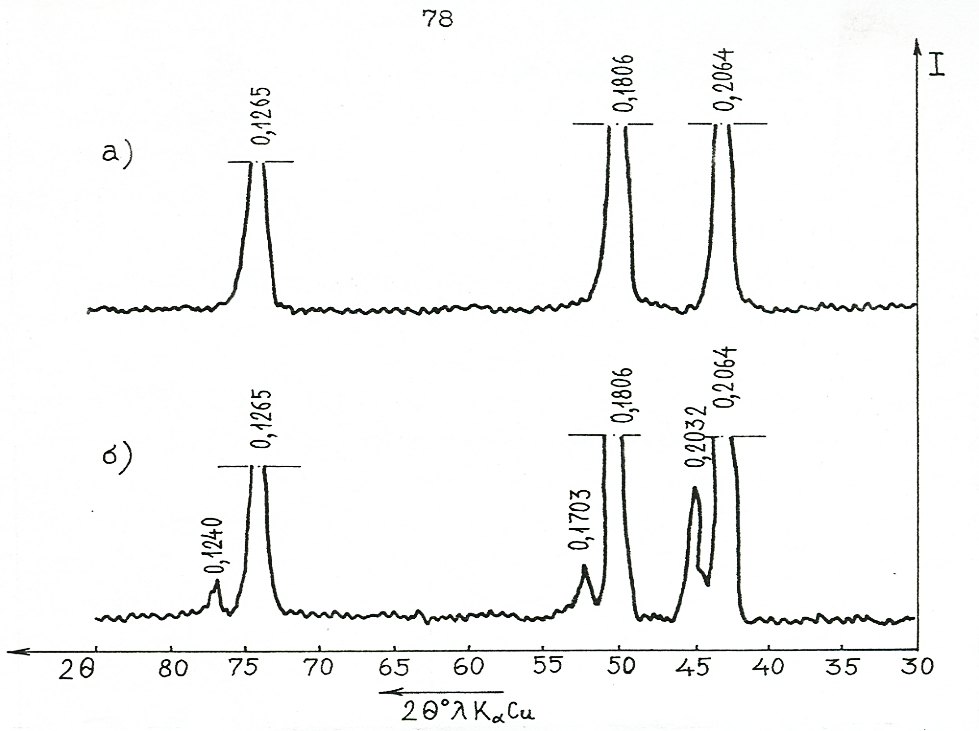
Рисунок 7 - Результаты рентгенофазового анализа стали типа H18K10M5 (а) и металлического порошка типа ПС-H18K10M5Rе (б)
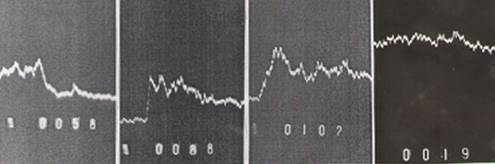
Рисунок 8 - Результаты рентгеноспектрального микрозондового анализа стального порошка типа ПС-H18K10M5Rе:
а – Ni; б – Co; в – Mo; г - Re
4. Заключение
Выявлены механизм и кинетика восстановления шихты, полученной из сложного оксида [Ni1-x, Cox](Fe1-x, Mox)2O4, синтезированного из оксидной системы Fe2O3–NiO–CoO–MoO3, и перрената аммония (NH4ReO4). Показано, что мартенситно-стареющий стальной порошок марки ПС-Х18К10М5Rе чище по количеству смесей, чем литая сталь той же марки. Выявлено, что рений, будучи очень активным, растворяется в системе Fe-Ni-Co-Mo, образуя твердые растворы и интерметаллические соединения рения, повышая прочность, твердость, ударную вязкость, теплоемкость, коррозионную стойкость и хладноломкость порошковой стали. Разработана технология получения высокопрочных мартенситно-стареющих стальных порошков.