Компьютерное моделирование и экспериментальные исследования пластиковых регулярных конструкций полученных аддитивными технологиями
Компьютерное моделирование и экспериментальные исследования пластиковых регулярных конструкций полученных аддитивными технологиями
Аннотация
Результаты моделирования регулярных конструкций из пластмасс и изучения их разрушения могут быть эффективно использованы в качестве отправной точки для разработки технологии изготовления композиционных материалов. Численные эксперименты и полевые испытания помогли определить наиболее предпочтительные типы конструкций – сотовые конструкции на основе пластика со следующими прочностными характеристиками: модуль Юнга Θ = 342,3 МПа, прочность на сжатие σ = 20,4 МПа, удельная прочность σsp = 81 МПа см3/г. Пластиковые 3D-модели были использованы при изготовлении металлических композитов с использованием технологии, сочетающей селективное лазерное расплавление титанового каркаса из порошков и пропитку более легкоплавкими сплавами. Значения прочности при изгибе изменяются в пределах от 1440 до 1560 МПа, значения модуля Юнга – от 49500 до 54000 МПа, твердость – 400HB. Повышенные показатели прочности можно объяснить композитной структурой материала, образованной сочетанием двух взаимопроникающих каркасов.
1. Introduction
Additive technologies of 3D printing methods by fused deposition modelling (FDM) have a number of advantages over other traditional processing methods for manufacturing composites: powder metallurgy, fabric and woven prepregs, investment casting, etc. They enable obtaining complex spatial structures with unprecedented geometry and high performance in accordance with a computer model. Their use makes it possible to form so-called lattice structures formed by repeating regular geometric cells in space (stochastic and regular) – arranged by 3D printing, this architecture gives polymer, metal, or ceramic materials a unique combination of properties that cannot be achieved by traditional methods: increased values of specific strength, specific surface area, heat transfer coefficient, elastic modulus, etc. As a result, we have extended prospects for application in various fields: manufacture of geometrically-complex parts for mechanical engineering, aerospace industry, biomedicine, oil and gas industry, etc. , . A number of papers provide data on the effect of the composition and structure of the arrangement of layers on the physical and mechanical properties and suggest options for topological optimization of surfaces of the gyroid and honeycomb structures to obtain products for various purposes with properties set at the design stage. The works , , , provide examples of the practical use of the FDM method in creating contour-complex solid parts made of plastics, metals, and alloys. Despite a significant amount of studies and applied work in the field of additive technologies, the problems of topological optimization of structures obtained by 3D printing are still relevant, first of all, due to the need to adapt them to the shape, size and operating conditions of a particular product, and the modelling of parts with complex geometry requires further improvement and development. In addition, topological optimization on plastic prototypes reduces the amount of experimental tests and speeds up the procedure of subsequent transformation and adaptation in relation to structures made of metals and alloys. In the field of additive technologies, designers have also developed other methods to increase the density and strength of materials obtained by Selective laser melting (SLM). Metal compositions based on titanium and its alloys , etc. can also be produced by a combination of printing technology and application of an intermediate liquid layer of a binder between the layers of the base material. Residual porosity in materials obtained by layer-by-layer deposition can also be eliminated by infiltration, i.e. impregnation with a melt of other (more fusible) material , , . The aim of this study is to model regular structures made of plastics and the processes of their destruction as a starting method in the development of a technology for manufacturing metal composite.
2. Results of numericaland experimental studies of regular structures made of plastics
The first stage of research was to analyze the state of the problem, and promising directions and designs of regular structures for subsequent manufacture of composite materials. Preliminary numerical calculations (Cura, Prusa, and Solidworks Simulation software products) to determine the stress-strain state of various types of structures are necessary to reduce the number of field experimental studies. The images of the models, the topology of the samples, and the assessment of the stresses arising in the samples’ volumes are shown in Fig. 1. The numerical analysis of the strength of various types of structures according to the model showed that the longitudinal construction of layers is preferable to the transversal (35%), and the honeycomb structure provides strength higher than the gyroid one (75%).
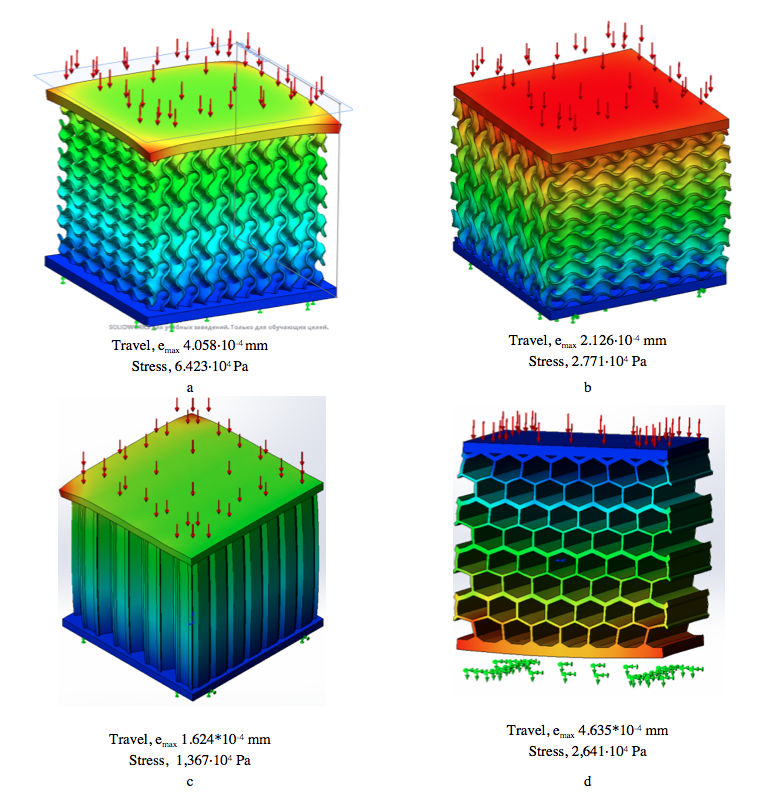
Figure 1 - Types of structures:
a – gyroid, transversal along the normal to the construction axis; b – gyroid, longitudinal along the construction axis; c – honeycomb, longitudinal along the axis of construction; d – honeycomb, transversal along the normal of the axis of construction
The compression tests of the samples were carried out in accordance with ISO 604:2002 on a Tinius Olsen 100ST universal testing machine, which enables to measure deformations with a video extensometer (Fig. 2a). The specific strength was calculated taking into account the fact that the density of the samples when filled with plastic material for 20% of the total volume is 0,25 g/cm3 for the honeycomb, and 0,21 g/cm3 for the gyroid.
The Tinius Olsen H25KT universal testing machine was used to determine the bending strength (Fig. 2b). The VT6 titanium samples with an aluminium or bronze binder had dimensions and shape in accordance with ISO 3325:1996: length: 50 mm; width: 10,0 ± 0,1 mm; height: 5,0 ± 0,10 mm. Rockwell hardness was measured on a TP50-14 on a C scale with a load of 1500 N subject to ISO 6508-86. Determination of the density and calculation of the porosity of the samples was carried out according to the standard method of hydrostatic weighing on an EX205 analytical balance by Mettler Toledo with a hydrostatic weighing kit. The study of the morphology of the initial powders, microstructure and elemental composition of the obtained samples was carried out by the methods of secondary electrons and energy dispersive microanalysis using a JEOL JSM-7001F scanning electron microscope equipped with an INCA Penta FETx3 X-ray spectrometer by Oxford Instruments. The microstructure of the samples was studied on polished surfaces using a JEOL JSM-7500FA scanning electron microscope.

Figure 2 - Testing equipment:
a – for compression tests; b – for bending strength

Figure 3 - Stages of destruction of the walls of the honeycomb under loading
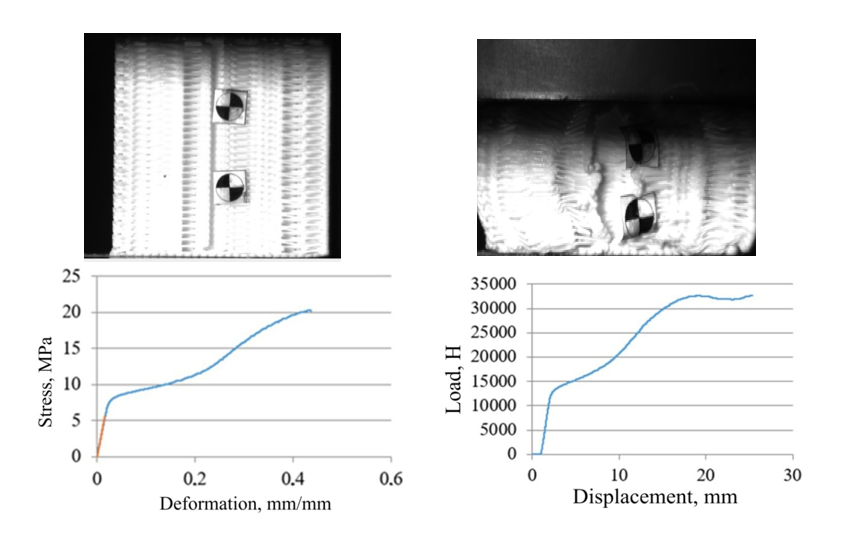
Figure 4 - Measurement results of sample 3
Note: PLA2 honeycomb, longitudinal along the growth axis
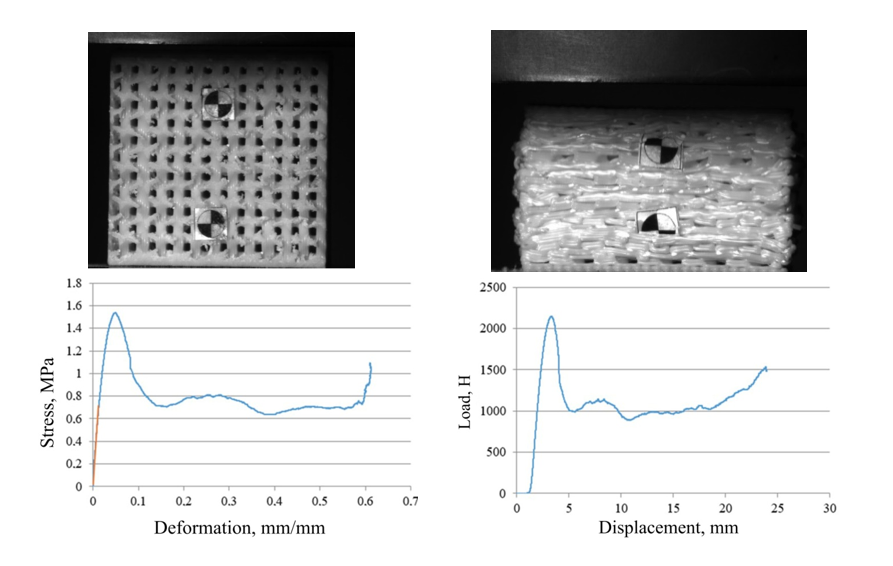
Figure 5 - Sample 8 – ABS4 gyroid, longitudinal along the growth axis
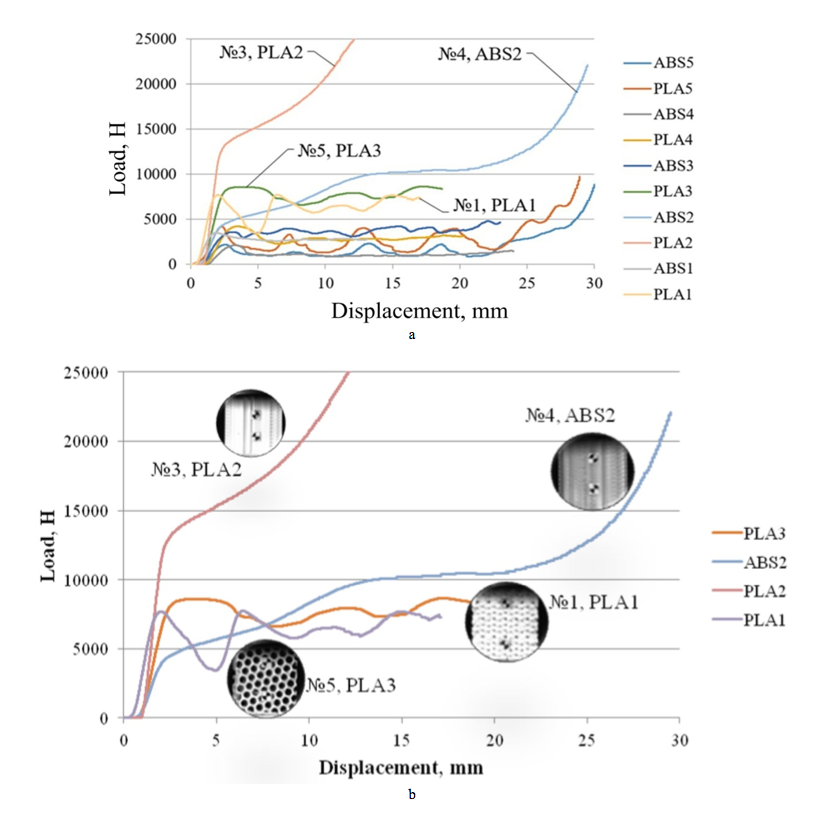
Figure 6 - Deformation patterns during compression:
a – for all samples; b – for samples with the best strength values
Table 1 - Physical and mechanical properties of the obtained samples
3. Results of experimental studies of metal composites produced by SLM-method
That is why, we used computer models of particularly these porous regular structures with the best strength indicators to manufacture TI6AL4V titanium alloy samples by additive technologies (SLM) and then infiltrate them with a melt of a more fusible aluminium bronze as a binder. The results of studies of the microstructure of Ti6Al4V+aluminium bronze composite materials are given in Fig. 7. Application of the phase contrast method revealed the presence of two main phases: Ti6Al4V (Fig. 7c) – spectrum 2; and aluminium bronze (Fig. 7c) – spectrum 1. The results of scanning electron microscopy of the microstructure of the regular honeycomb samples impregnated with an aluminium bronze melt (composite material), and determination of relative density (98% of the theoretical density) indicate a fairly high efficiency of filling the honeycomb voids and the elimination of residual porosity (Fig. 7b). Images of the microstructure and chemical analysis of phase components indicate a fairly high uniformity of the structure and efficiency of infiltration (Fig. 7d) – spectrum 1-3); density and residual porosity (less than 1%) confirm this fact. A very interesting effect, which was found during the study of the microstructure of the low-temperature-melting phase, is the formation of an acicular structure with marked elongated crystallized grains – “whiskers” with a cross-sectional size of 0,1 μm (Fig. 6d). The appearance of this reinforced fragmentary-nanostructured phase in a composite material gives cause to assume the possibility of dispersion strengthening of aluminium bronze and, as a result, of the composite as a whole. The fracture surface of the samples after bending tests has a quasi-plastic pattern, which can be explained by the dominant influence of the properties of the infiltrated material (aluminium bronze). Similar structures are formed during ordinary sintering of hard alloy composites obtained from bimodal powder mixtures of WC-Co-Al(Al2O3) and copper-based pseudoalloys . The density, porosity, the patterns of the phase components distribution, strength, microhardness, and Brinell hardness were studied on samples in conformity with the standard methods.

Figure 7 - Microstructure of Ti6Al4V+aluminium bronze composite materials:
a – scheme of infiltration; b – surface of the composite material infiltrated with aluminium alloy; c – images of the microstructure with selected areas of chemical analysis and their composition; d – acicular structure by volume of the binder with selected areas of chemical analysis and their composition
Note: c — x500; d — x3500
Table 2 - Strength properties of TI6AL4V composites
4. Conclusion
In the process of complex numerical and experimental studies, our team found the patterns of deformation processes and destruction of various types of regular structures 3D-printed of plastics in accordance with the computer model and the most preferred materials and honeycomb structures from the point of view of strength properties. The results of preliminary tests on plastic prototypes were used in the development of compositions and manufacturing technologies for metal composite materials based on Ti6Al4V titanium alloy powders. The study of the strength properties of Ti6Al4V structures obtained by 3D printing in combination with infiltration with aluminium bronze confirmed the effectiveness of the adopted design and technological solutions – an increase in bending strength by 20-25% compared to the base Ti6Al4V, and up to 1,5 times increase in the hardness values. Electron microscopy confirmed the homogeneity of the phase distribution in the composite structure, and the absence of residual porosity.