Влияние плазменной и лазерной резки на формирование цинкового покрытия на стали
Влияние плазменной и лазерной резки на формирование цинкового покрытия на стали
Аннотация
В работе были изучены особенности формирования цинкового покрытия на изделиях из стали Ст3сп после лазерной и плазменной резки. Обнаружено, что обработка поверхности оказывает влияние на толщину и фазовый состав цинкового покрытия. На поверхностях после механического снятия фаски и после прокатки толщина покрытия достигает 126 мкм и имеет строение, характерное для стали Ст3сп: на 80% представляет собой крупные кристаллы ζ-фазы, остальное δ-фаза. На поверхности после плазменной резки образуется тонкое покрытие около 43мкм, в котором хорошо различимы три фазовых слоя – столбчатая δ-фаза, ζ-фаза и η-фаза. Установлено, что снятие окалины не приводит к устранению этого эффекта, в то время как механическое снятие поверхностного слоя устраняет это явление. Показано, что в приповерхностной зоне реза происходит плавное изменение мартенситной структуры в ферритно-перлитную. Глубина закаленного слоя после плазменной резки составляет 117 мкм, максимальная микротвердость 260HV, а после лазерной резки глубина закаленного слоя 55 мкм, микротвердость 160 HV. Таким образом, недостаточная толщина цинкового покрытия на поверхностях после плазменной и лазерной резки обусловлена не поверхностными дефектами и присутствием окалины, а структурными изменениями в зоне термического влияния. Диффузионный процесс образования цинкового покрытия тормозится образованием на поверхности структуры мартенсита, представляющим собой пересыщенный твердый раствор углерода в α-железе. В случаях, когда снижение толщины покрытия недопустимо, необходимо механически снимать поверхностный закаленный слой.
1. Введение
В современном производстве для раскроя листовых металлических материалов широко используются источники высококонцентрированных потоков энергии: лазерные и плазменные [1], [2]. Лазерное излучение используют для резки листов толщиной до 8-10 мм. Для резки листов большей толщины необходимо применять источники плазменного излучения [3]. Механизм плазменной и лазерной резки состоит в том, что высокоэнергетическая струя взаимодействует с металлом и расплавляет его по линии воздействия. Прилегающие к линии реза микрообъемы металла также разогреваются, но до более низких температур. Градиент температуры изменяется на некотором расстоянии от кромки реза от температуры плавления до комнатной. Эта область называется зоной термического влияния (ЗТВ). Поверхность реза полностью переходит в жидкое состояние, а после прекращения нагрева затвердевает с очень большой скоростью охлаждения из-за быстрого отвода теплоты внутрь холодного объема. Фактически на поверхности реза происходит закалка с плавлением поверхности — это термическая обработка, при которой главным процессом является быстрое затвердевание поверхностного слоя с образованием метастабильной структуры. В результате в кромках металла на стадии затвердевания происходят такие фазовые и структурные изменения, которые вообще невозможны при нагреве без расплавления [4]. Большие скорости нагрева и охлаждения, присущие плазменной резке, могут приводить к образованию высокотвердых и прочных фаз, охрупчивающих сталь [5], [7], [10], [11]. Подобные качественные изменения металла в зоне термического влияния (ЗТВ) обуславливают последующие технологические и эксплуатационные свойства в этой зоне. Возникающее упрочнение поверхностных слоев при поверхностной плазменной и лазерной закалке успешно используется для деталей, работающих в условиях износа и трения [12], [13], [15], [17]. Однако существуют случаи, когда поверхностные структурные изменения приводят к дефектам и проявлению нежелательных явлений [5]. Например, обнаружено, что при горячем цинковании изделий, имеющих поверхности после плазменной и лазерной резки, наблюдается недостаточная толщина покрытия на изучаемых поверхностях. В связи с этим, целью работы было установление причин изменения формирования цинкового покрытия на поверхности металла после лазерной и плазменной резки.
2. Методы и принципы исследования
Для исследования были отобраны образцы из стали Ст3сп после плазменной и лазерной резки. Поверхность реза образцов после плазменной резки зачищали с помощью угловой шлифовальной машины до металлического блеска (снятие окалины) и до снятия поверхностного слоя. После чего образцы травили в 10% соляной кислоте 1 час. Цинкование производили на ОАО «Завод Продмаш» при температуре 4480С, время выдержки 2 мин.
Микроструктуру стали и покрытия исследовали с помощью сканирующего электронного микроскопа Tescan Vega SB. Элементный анализ структурных составляющих проводили с помощью с энергодисперсионного рентгеновского анализатора INCAx-act. Микротвердость стали измеряли под нагрузкой 20 г на микротвердомере HV-1000.
3. Основные результаты и обсуждение
Исследования показали, что состояние стальной поверхности оказывает непосредственное влияние на толщину цинкового покрытия. На рисунке 1 показано поперечное сечение образца, имеющего поверхности после плазменной резки, после механического снятия фаски и после прокатки листа.
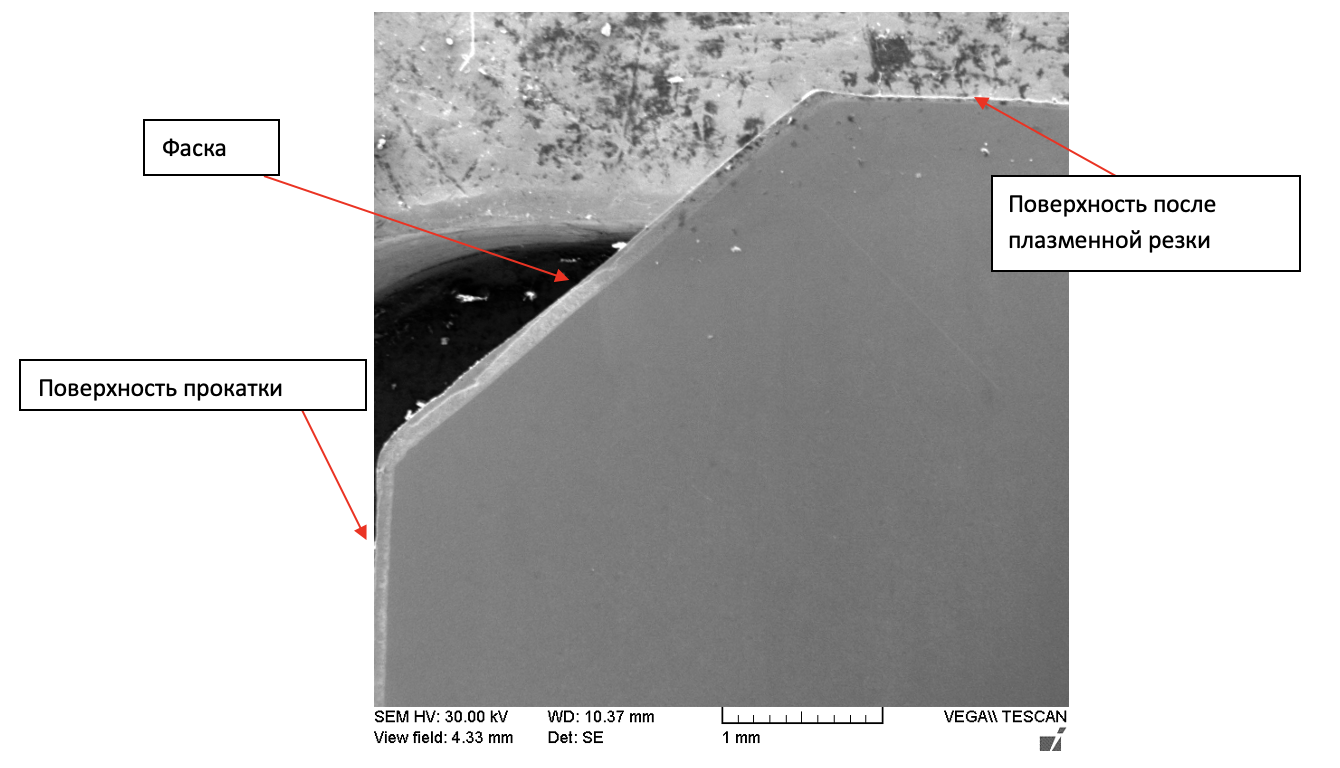
Рисунок 1 - Общий вид поперечного сечения цинкового покрытия на образце
Таблица 1 - Толщина покрытия на различных поверхностях
Вид поверхности | Толщина покрытия, мкм |
После плазменной резки | 43,4 |
После снятия фаски | 125,9 |
Исходная поверхность прокатки | 129,3 |
Строение цинкового покрытия на различных поверхностях образца отличается. На поверхности после плазменной резки в покрытии хорошо различимы три фазовых слоя – столбчатая δ-фаза, ζ-фаза и η-фаза (рис.2а). На поверхности после прокатки наблюдается покрытие, характерное для стали Ст3сп (рис.2б) [18]. Оно на 80% представляет собой крупные кристаллы ζ-фазы, остальное δ-фаза.
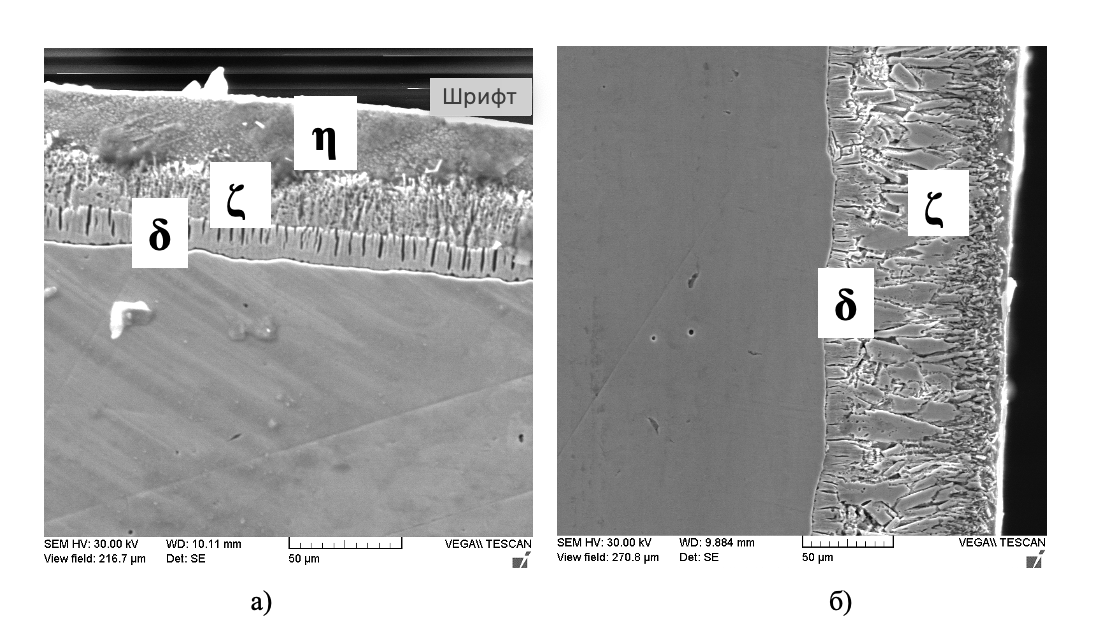
Рисунок 2 - Цинковое покрытия на различных поверхностях образца:
а – поверхность после плазменной резки; б – поверхность проката
Исследования поверхности металла после плазменной и лазерной резки показали, что на поверхности присутствует характерный рельеф, вызванный течением металла под воздействием высокоэнергетического пучка. Поверхность стали покрыта окалиной (рис. 3а,б).
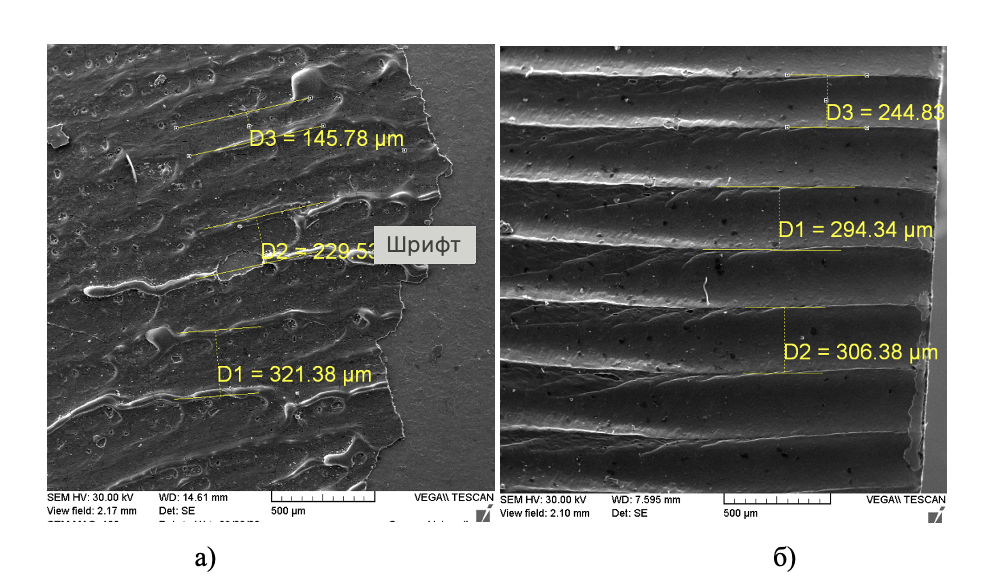
Рисунок 3 - Окалина на поверхности образца:
а - после плазменной резки; б - после лазерной резки
Анализ данных по средней толщине цинкового покрытия показал, что на поверхности после плазменной резки образуется покрытие меньшей толщины, чем на других поверхностях. При средних значениях толщины покрытия на поверхности после плазменной резки 64,5 мкм, в некоторых местах покрытие достигает минимальных значений, не допустимых ГОСТ 9.307-89 около 40мкм. Механическое снятие окалины не приводит к устранению этого эффекта и увеличению толщины покрытия. В то время как снятие поверхностного слоя устраняет этот эффект, толщина покрытия увеличивается до 98,5 мкм (табл.2).
Таблица 2 - Толщина цинкового покрытия в зависимости от обработки поверхности
Обработка поверхности | Толщина покрытия, мкм |
Плазменная резка | 64,5 |
Механическое снятие окалины | 64,7 |
Механическое снятие поверхностного слоя | 98,5 |
Исследования микроструктуры стали в зоне плазменной резки показали, что ферритно-перлитная структура стальной основы (рис. 4б) переходит в закаленную игольчатую структуру в приповерхностной зоне (рис.4в). Глубина закаленного слоя около 12 мкм, ширина зоны термического влияния около 380 мкм (рис. 4а)
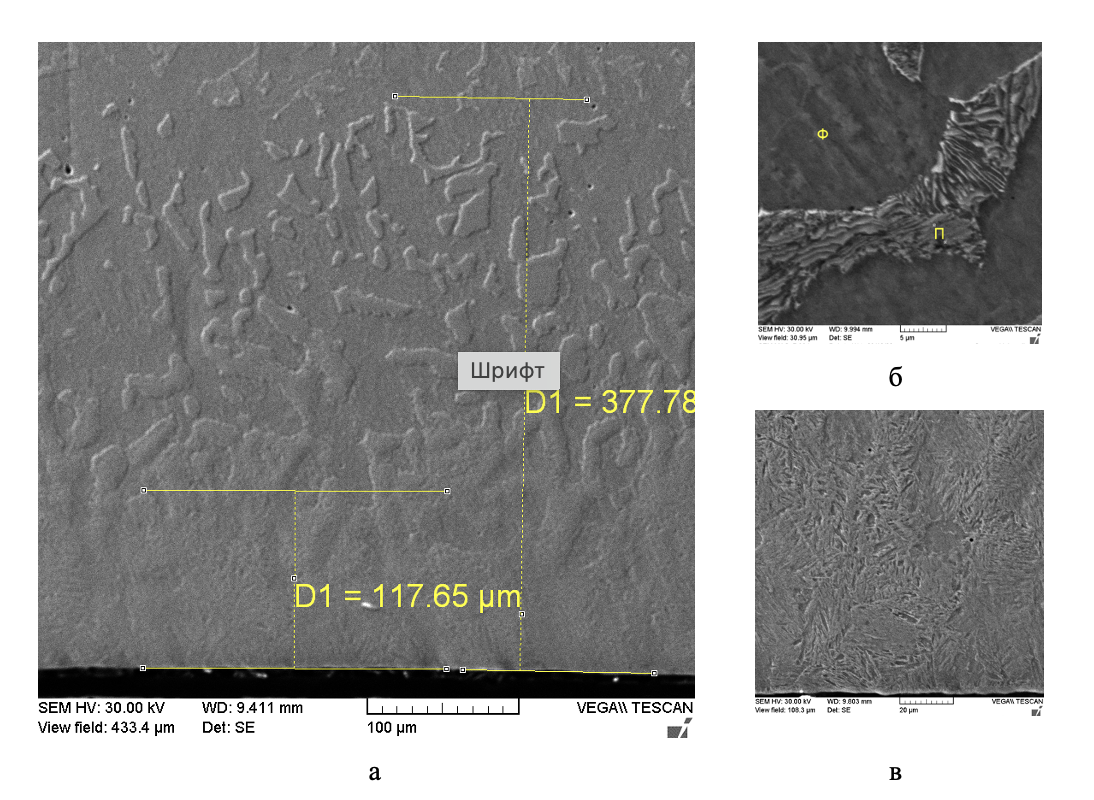
Рисунок 4 - Микроструктура зоны термического влияния после плазменной резки:
а – общий вид, х500; б – основа, х7000; в – приповерхностная зона, х2000
После лазерной резки в структуре стали также наблюдается переход от феррито-перлитной структуры (рис.5б) к закаленной игольчатой (рис.5в). Однако глубина ЗТВ меньше, чем после плазменной резки – 140 мкм, а глубина закаленной зоны – 55 мкм (рис.5а).
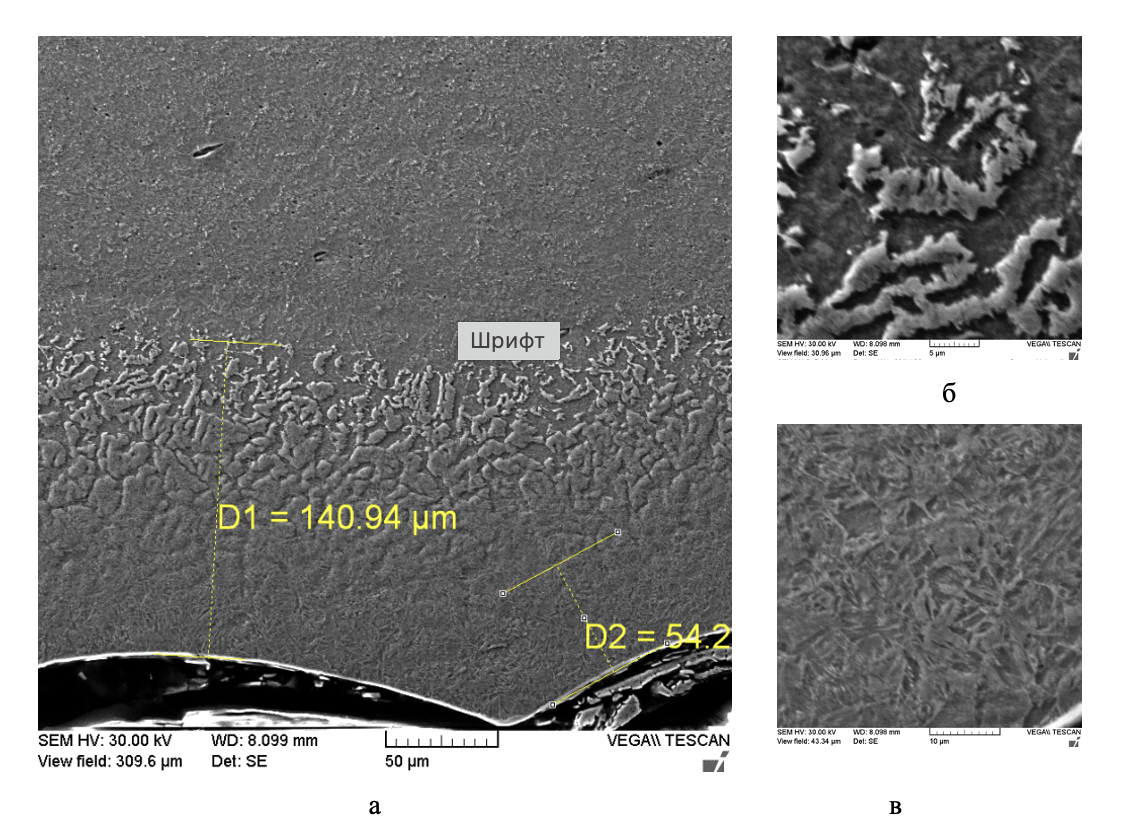
Рисунок 5 - Микроструктура зоны термического влияния после лазерной резки:
а – общий вид, х700; б – основа, х7000; в – приповерхностная зона, х5000
Установленные особенности микроструктуры металла, приобретаемые в результате плазменной и лазерной резки, вызваны сильным разогревом зоны реза и приповерхностных слоев с последующим быстрым охлаждением. Это приводит к поверхностной закалке стали в зоне реза. Глубина закаленного слоя зависит от глубины прогрева, т.е. от интенсивности энергетического пучка, поэтому после плазменной резки она больше.
Для анализа механических свойств приповерхностного слоя измеряли микротвердость. Полученные результаты представлены на графике (рис.6).
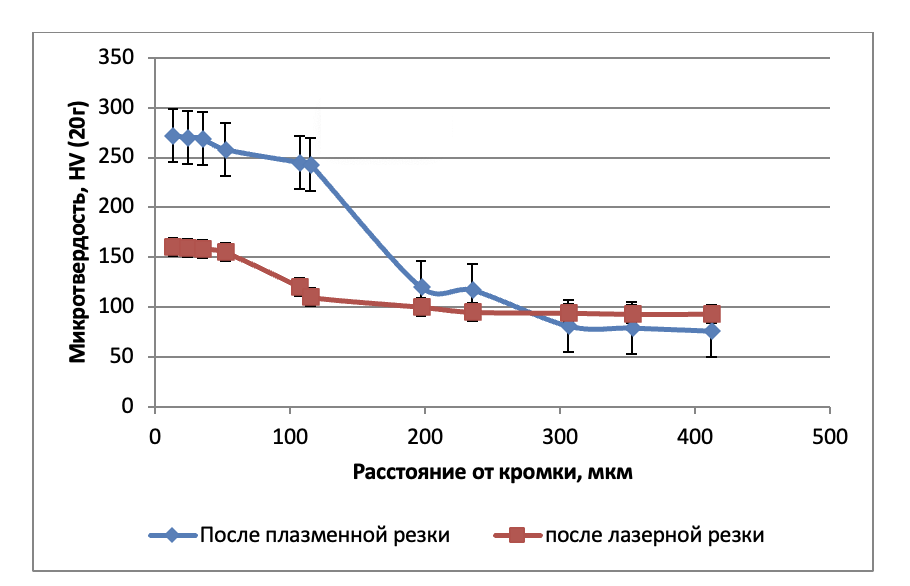
Рисунок 6 - Изменение микротвердости приповерхностного слоя после плазменной и лазерной резки
Исследования показали, что после плазменной резки микротвердость закаленной зоны составляет около 260HV (255HB), что соответствует твердости мартенсита низкоуглеродистой стали с содержанием углерода 0,2% [4]. Микротвердость закаленной зоны после лазерной резки составляет около 160HV (152HB). Это вызвано различной интенсивностью и глубиной зоны разогрева ЗТВ и соответственно разной скоростью охлаждения приповерхностного слоя. Большая твердость указывает на более значительные структурные искажения.
Мартенсит представляет собой пересыщенный твердый раствор углерода в железе, с сильными искажениями кристаллической решетки, с отсутствием границ зерен и вакансий. Таким образом, структура мартенсита может тормозить взаимную диффузию железа и цинка при образовании покрытия.
4. Заключение
Обнаружено, что предварительная обработка поверхности стали после плазменной и лазерной резки влияет на толщину цинкового покрытия, получаемого горячим цинкованием. На обработанных поверхностях толщина покрытия значительно меньше, чем на остальных поверхностях, что не допускается требованиями ГОСТ 9.307-89.
Установлено, что снятие окалины не приводит к устранению этого эффекта в то время как механическое снятие поверхностного слоя устраняет этот эффект.
Показано, что в приповерхностной зоне реза происходит плавное изменение мартенситной структуры в ферритно-перлитную. Глубина закаленного слоя после плазменной резки составляет 117 мкм, максимальная микротвердость 260HV, а после лазерной резки глубина закаленного слоя 55 мкм, микротвердость 160 HV.
Таким образом, недостаточная толщина цинкового покрытия на поверхностях после плазменной и лазерной резки обусловлена не поверхностными дефектами и присутствием окалины, а структурными изменениями в ЗТВ. Диффузионный процесс образования цинкового покрытия тормозится образованием на поверхности структуры мартенсита, представляющим собой пересыщенный твердый раствор углерода в α-железе.
В случаях, когда снижение толщины покрытия недопустимо, необходимо механически снимать поверхностный закаленный слой.